Table of Contents:
- Introduction
- Die Casting Process
- Advantages and Disadvantages of Die Casting
- Materials Used for Die Casting
- Quality Control in Die Casting
- Design Considerations for Die Casting
- Environmental Impact of Die Casting
- Conclusion
-
1.Introduction
Die casting is a manufacturing process that involves injecting molten metal into a mold or die to produce complex and precisely shaped metal parts. This process has been around for a long time, with the first documented use dating back to the mid-1800s. Since then, die casting has evolved significantly and has become an integral part of modern manufacturing.
Die casting is used in various industries for the production of parts with high precision, intricate geometries, and excellent mechanical properties. Some of the industries that utilize die casting include the automotive, aerospace, construction, commercial, and telecommunications industries. Die casting has gained increased popularity in these industries because of its versatility, accuracy, and repeatability.
-
2. Die Casting Process
The die casting process comprises of several critical stages that include mold preparation, melting, injection, solidification, ejection, and finishing. In the mold preparation phase, the mold is rigorously cleaned to remove any debris or contaminants that may interfere with the molding process. Afterward, the mold gets coated with lubricants to enhance mold release and prevent the molten metal from adhering to the mold’s surface.
The next stage is melting, where the metal is heated to its melting point in a furnace. With the metal melted, it’s injected into the mold under high pressure with a precision plunger system. Afterward, the metal is allowed to cool and solidify into the desired shape. The ejection stage then follows, where the finished part is carefully removed from the mold.
The final phase of the process comprises trimming, finishing, and quality assurance steps. The finishing stage involves removing excess materials from the casting by trimming and polishing to achieve the final product’s desired finish. Afterward, the finished product gets inspected for conformity to requirements such as dimensional tolerances, strength, and hardness.
-
3.Advantages and Disadvantages of Die Casting
Die casting has several advantages over other manufacturing processes, including:
- Precision: Die casting offers high dimensional accuracy and consistency of parts, with tolerances within a few thousandths of an inch.
- Efficiency: Die casting is a highly efficient process that allows for high-volume production with minimal waste or need for secondary machining.
- Cost-effectiveness: The process allows for the production of large quantities of identical parts, resulting in lower unit costs over time.
- Design flexibility: Die casting can create complex geometries that are difficult or impossible to achieve with other casting methods.
- Strength: Die cast parts are known for their high strength and durability, able to withstand high temperatures and pressures.
Disadvantages of Die Casting:
Despite the numerous advantages of die casting, the process has some limitations and disadvantages that need to be considered, including:
- Limited to specific shapes: Die casting is limited to producing parts with simple or complex shapes that can be easily ejected from the mold.
- High initial cost: Die casting tooling can be expensive, making it a less attractive option for small production runs.
- Material limitations: Die casting is not suitable for all materials, and the alloys and metals that can be used are limited by factors such as melting point and reactivity.
- Porosity and defects: Die casting can be prone to defects such as porosity, shrinkage, and cracking, which must be carefully monitored and controlled.
-
4.Materials Used for Die Casting
Die casting can use a wide range of metals and alloys that include:
- Aluminum: Aluminum is the most common metal used for die casting, offering high strength, good thermal properties, and light weight.
- Zinc: Zinc is another popular metal used for die casting, offering excellent corrosion resistance, ease of casting, and high dimensional accuracy.
- Magnesium: Magnesium is the lightest metal that can be die-cast, providing high-strength-to-weight ratios and good thermal properties.
- Copper: Copper alloys are often used for electrical components due to their excellent electrical conductivity.
- Lead and Tin: Lead and tin alloys are used for specific applications requiring low melting points, such as plumbing fixtures and cast nets.
.
Characteristics of Materials Used for Die Casting:
The materials used in die casting must have specific characteristics to ensure that the final product meets the required tolerances and specifications. Some of the key characteristics of materials used in die casting include:
- Fluidity: The metal must have sufficient fluidity to flow through the mold cavity and fill out the intricate part geometries.
- Heat resistance: The metal must be resistant to high temperatures, which is required to prevent deformation of the part during the casting process.
- Strength: The metal must have sufficient strength to maintain its shape and function under load.
- Machinability: The metal must be easily machinable to remove any excess material or surface abnormalities.
- Corrosion resistance: The metal must be resistant to corrosion and tarnishing to ensure the final product’s longevity.
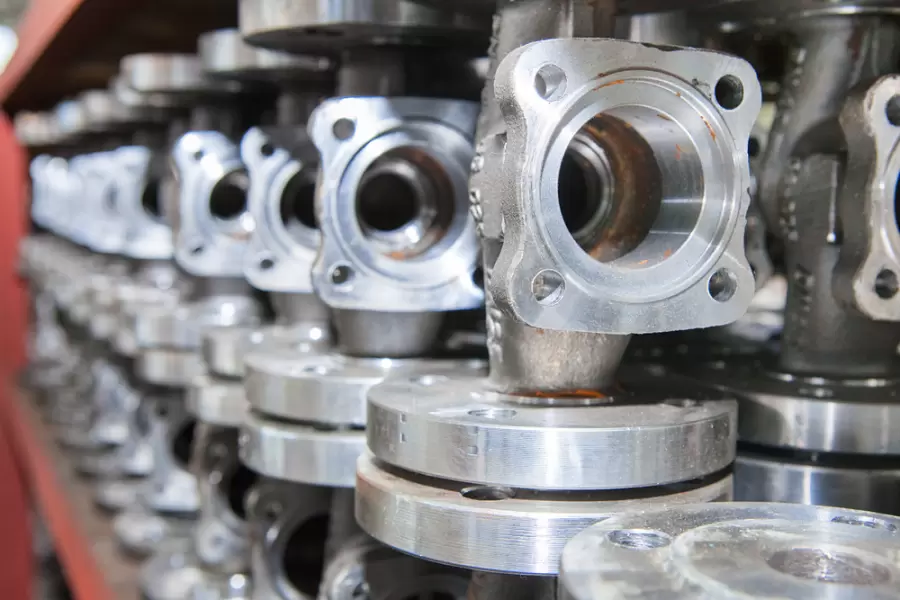
-
5.Quality Control in Die Casting
Quality control is critical in the die casting process to ensure that the final parts produced meet specified tolerances, function as intended, and are free from defects. The importance of quality control in die casting cannot be overstated as it establishes the product’s reliability and safety and helps to avoid costly mistakes or warranty claims. Quality control in die casting begins with the design stage and continues throughout the production process until the final product is delivered.
Inspection and Testing Methods for Die Casting Parts:
There are several inspection and testing methods used for die casting parts to ensure that they meet the required specifications. Some of the commonly used methods include:
- Visual Inspection: Visual inspection is the most basic form of quality control used in die casting, and it involves examining the parts visually for defects or abnormalities.
- Pressure Testing: Pressure testing involves subjecting the cast parts to specific pressures to confirm the casting’s integrity and evaluate the overall function’s efficiency.
- Dimensional Testing: The dimensional testing of parts involves measuring the parts’ dimensions and comparing them against the design specifications to determine whether they are accurate.
- X-Ray Inspection: X-ray inspection is used to detect internal defects, such as porosity, in the casted parts.
- Tensile Testing: Tensile testing is used to test the casting material’s strength by subjecting it to controlled amounts of tensile force.
- Spectroscopic Testing: Spectroscopic testing is used to analyze the metal’s chemical properties to ensure it meets the specified composition for the specific casting.
- Ultrasonic Testing: Ultrasonic testing is used to detect any internal defects or faults in the die casting parts by using high-frequency sound waves.
-
6.Design Considerations for Die Casting
Designing die casting parts correctly is critical to the success of the process. Engineers must follow best practices for die casting part design and take into account the unique manufacturing processes involved.
Best Practices for Die Casting Part Design:
- Keep designs simple: Simple designs are easier to cast, reduce the complexity of the die, and improve production efficiency.
- Maintain uniform wall thickness: Uniform wall thickness in the part design is critical for producing high-quality die cast parts.
- Allow adequate draft: Draft is the taper on the walls of the die cavity that helps in the ejection of the parts after casting.
- Avoid undercuts: Undercuts or negative drafts make it challenging to eject the part from the mold, can cause warping, and limit production efficiency.
- Avoid sharp corners: Sharp corners in a part design can lead to casting defects such as porosity, incomplete filling, and cracking that can affect the integrity of the part.
Design for Manufacturability in Die Casting:
Considerations for manufacturability in die casting include:
- Wall thickness: Proper wall thickness dimensions are critical to ensure consistency, minimize shrinkage, and avoid mold defects.
- Draft angle: The draft angle ensures that the part can be easily ejected from the mold without causing any quality issues.
- Tolerances: Manufacturers should specify reasonable tolerances in the part design, taking into account machine capabilities, the complexity of the part, and the material used.
- Material selection: Engineers should select the best material for the part’s application, considering factors such as strength, hardness, durability, and corrosion resistance.
- Tooling design: Appropriate tool design can improve the repeatability, accuracy, and efficiency of the die casting process.
-
7.Environmental Impact of Die Casting
Die casting has a significant impact on the environment due to the energy consumption and emissions resulting from the process. While die casting is essential for many industries, there are specific measures that manufacturers can take to reduce its environmental impact.
Energy Consumption and Emissions in Die Casting:
The energy consumption in the die casting process comes mainly from the melting of the metals and alloys used in production. Metal melting requires significant energy consumption, resulting in greenhouse gas emissions from the energy production.
In addition, the die casting process can result in emissions of pollutants such as particulate matter, sulfur dioxide, nitrous oxides, and carbon monoxide, which can negatively affect the air quality.
.
Sustainable Die Casting Practices:
Manufacturers can implement sustainable die casting practices to lessen the environmental impact of their operations. Some of the ways to achieve sustainability include:
- Recycle scrap materials: Recycling scrap metals and alloys can significantly reduce energy consumption and emissions, conserving natural resources and minimizing waste.
- Use renewable energy sources: Manufacturers can install on-site renewable energy sources, such as solar panels, biomass, or wind turbines, to reduce the energy demand required for metal melting.
- Improve energy efficiency: Manufacturers can improve energy efficiency by optimizing equipment settings and implementing best practices for energy management.
- Reduce emissions: The use of pollution control technologies such as wet scrubbers, bag filters, and electrostatic precipitators can mitigate dust and gas emissions from the die casting process.
- Choose sustainable materials: Selecting metals with a lower carbon footprint, such as aluminum or magnesium, can minimize the environmental impact of die casting.
-
8.Conclusion
The die casting process has been an essential manufacturing process for decades, offering high precision, efficiency, and cost-effectiveness. The future trends and developments in the die casting industry include the use of lightweight materials, additive manufacturing, automation, sustainable manufacturing, and advances in metallurgy. By keeping pace with these trends and adopting new technology and sustainable practices, manufacturers in the die casting industry can achieve greater efficiency, reduce their environmental impact, and meet the growing demands of their customers.
If you need about Metal Die Casting Services,You can click on the V1 Prototype website to find it.