Table of Contents:
- Introduction: What is a Plastic Injection Machine?
- Types of Plastic Injection Machines
- Parts of Injection Machine
- How Plastic Injection Machine Works
- Advantages of Using Injection Machines
- Factors to Consider When Choosing an Injection Machine
- Maintenance and Troubleshooting
- Future Trends in Plastic Injection Machine Technology
- Conclusion: Is a Plastic Injection Machine the Right Choice for Your Business?
-
1.Introduction: What is a Plastic Injection Machine?
Plastic injection machines are devices that are used to produce plastic products on a large scale. They operate by injecting molten plastic material into a mold cavity, which then cools and solidifies into a specific shape. These machines have been in use since the 1930s and have undergone numerous technological advancements to improve efficiency, speed, and precision. Today, plastic injection machines are widely used in different sectors such as automotive, medical, consumer products, and packaging. In this comprehensive guide, we will explore the different types of plastic injection machines, their parts, working process, advantages, and how to maintain and troubleshoot them.
-
2.Types of Plastic Injection Machines
- Hydraulic Injection Machines:Hydraulic injection machines are the oldest type of plastic injection machines and operate by using a hydraulic pump. The machine’s hydraulic system provides the necessary pressure to engage the mold, keeping the plastic in the mold until it cools and solidifies. Hydraulic injection machines are known for their reliable performance, robustness, and ability to produce high-quality plastic products with accuracy and precision. They operate at lower temperatures, which is ideal for heat-sensitive materials. However, these machines require more maintenance because of their hydraulic systems, and they consume more power than electric machines.
- Electric Injection Machines:Electric injection machines use electric motors to operate, and they are more energy-efficient than hydraulic machines. They are known for their high precision, fast cycle times, and low maintenance. These machines are perfect for high volume production and have faster cycle times, which increase productivity. Electric machines are more reliable than hydraulic machines, with fewer breakages and leaks. The downside to electric machines is their higher upfront cost compared with hydraulic machines.
- Hybrid Injection Machines:Hybrid injection machines, also known as servo-hydraulic machines, are a combination of hydraulic and electric machines. They use a hydraulic pump to engage the mold, just like the hydraulic machine, and an electric motor is used to drive the hydraulic pumps. Hybrid machines have a faster cycle time than hydraulic machines and consume less power than electric machines. They provide high precision, accuracy, and consistency in the production of plastic products. Hybrid injection machines are expensive compared to hydraulic machines, but they are more budget-friendly than electric machines.
It is essential to consider your production needs and budget when selecting a plastic injection machine. For small operations or low-volume production, hydraulic machines can be a cost-effective option. For high-volume production, electric or hybrid injection machines are ideal for their speed, precision, and cost-savings over time.
-
3.Parts of Injection Machine
- Barrel and Screw:The barrel and screw are the critical parts of a plastic injection machine responsible for melting and mixing plastic pellets or granules. The barrel provides a chamber for the molten material, while the screw, which rotates within the barrel, forces the molten material towards the mold. The barrel comprises three sections: the feed zone, the compression zone, and the metering zone. Each section has unique characteristics to facilitate the melting, mixing, and feeding of the plastic material.
- Clamping Unit:The clamping unit is another essential part of the plastic injection machine responsible for holding the mold in place during the injection process. It consists of clamping plates, which use hydraulic or electric pressure to exert a force that holds the mold closed during injection. The clamping mechanism tightens the mold to prevent any plastic from leaking out during injection. It is fitted with a safety feature that will stop the machine if it detects any errors or abnormalities.
- Injection Unit:The injection unit comprises the nozzle, the feed hopper, and the screw that delivers the molten material into the mold. Once the plastic material is melted and mixed in the barrel, it is fed through the nozzle into the mold. The injection unit is responsible for maintaining the temperature and pressure of the molten plastic material as it is delivered into the mold.
- Control Panel:The control panel of a plastic injection machine functions as the brain of the machine. It controls and regulates all aspects of the injection process, including temperature, pressure, timing, and speed. The control panel is user-friendly and displays all necessary data for the operator to ensure that the injection process goes smoothly. The control panel’s interface will depend on the machine’s type, but it usually displays digital controls for temperature, pressure, cycle time, and speed.
Understanding the different parts of a plastic injection machine and how they function is essential to maintain the machine’s efficiency and durability. Proper maintenance and inspection of the machine’s parts will extend its lifespan and reduce the risk of equipment failure. Regular checks on the barrel’s condition, screw wear, and hydraulic system’s integrity will ensure the machine’s reliability and high-quality production.
-
4.How Plastic Injection Machine Works
The plastic injection machine relies on the following significant stages to produce a plastic product: injection, clamping, cooling, and ejection phases.
- Injection Phase:The injection phase is where the plastic material is fed into the machine’s barrel and melted, mixed, and delivered into the mold cavity. The screw rotates within the barrel, pushing the molten material towards the mold. The nozzle sprays the molten material under high pressure into the mold cavity, where it fills and takes the shape of the mold.
- Clamping Phase:Once the mold cavity is filled, the clamping phase follows. The machine’s clamping unit will apply the required pressure to keep the mold closed until the plastic material cools and solidifies. The machine’s hydraulic or electric pressure will keep the mold shut during the cooling phase to ensure that the product takes on the desired shape.
- Cooling Phase:The plastic material now begins to cool down and takes the shape of the mold. The cooling phase varies based on the size and thickness of the product being molded. The injection machine’s cooling system helps cool the mold faster, lowering the time required to produce a quality plastic product.
- Ejection Phase:Once the plastic material has cooled down, it is removed from the mold in the ejection stage. The clamping unit will release the mold, and the ejector pins will push out the finished product. The product then drops onto the conveyor belt, where it goes through the quality control process.
Plastic injection machines’ efficiency and productivity are related to the injection speed, pressure, temperature, and cycle time. Therefore, it is essential to set up and adjust the machine’s parameters, such as the barrel temperature, injection speed, and pressure, to ensure the machine produces high-quality products consistently. Regular maintenance and cleaning of the machine will ensure that it operates effectively and that all machine parts are in good working condition.
-
5.Advantages of Using Injection Machines
There are numerous advantages to using plastic injection machines to produce plastic products, some of which include:
- High Efficiency: The plastic injection machines can produce high-quality plastic products in large quantities quickly and efficiently. This makes them ideal for large volume production and also helps to reduce production costs.
- Precision and Accuracy: Injection machines offer high precision and accuracy in the production of plastic products. They can make products with intricate designs and tight tolerances that would be difficult to achieve with other manufacturing processes.
- Versatility: Plastic injection machines can produce a wide range of products, from simple to complex shapes and sizes. They can produce products for various industries such as automotive, medical, consumer products, and packaging.
- Cost-Effective: Injection machines are cost-effective because they can produce products in large quantities without a significant increase in production costs. They also require little labor, which helps reduce production costs.
- Sustainability: Injection machines can use recycled plastic material, making them an environmentally friendly option. They also produce fewer waste materials compared to other manufacturing processes.
- Consistency: The injection process is highly controlled, which guarantees consistent product quality. The machine’s variables such as temperature, pressure, and speed are closely monitored, ensuring that each product meets the desired specifications.
Overall, plastic injection machines efficiently produce high-quality products, are cost-effective, and versatile in their application, making them an ideal option for many industries.
-
6.Factors to Consider When Choosing an Injection Machine
When selecting a plastic injection machine, there are several factors you need to consider. These include:
- Material:The type of material you intend to use on the injection machine will determine the type of machine you need. Some materials may require high temperatures or pressures, while others may be heat sensitive. It is essential to choose a machine that can handle the type of material you intend to use, and it’s ideal to select a machine that can also process multiple types of materials.
- Tonnage:Tonnage refers to the amount of clamping force the machine can exert on the mold. The tonnage needed will depend on the size and shape of the product you intend to make. The larger the product, the greater the tonnage the machine will need to produce the product. It is essential to choose a machine with the appropriate tonnage to avoid damaging the mold or producing defective products.
- Shot Size:The shot size refers to the maximum amount of material that the injection machine can inject into the mold cavity at one time. The machine’s shot size should be proportional to the size of the product being produced. Choosing the right shot size is critical in preventing over filling or under filling of the mold.
- Career Size:The career size is the maximum size of the mold that the machine can accommodate. The career size needed is determined by the size of the product being produced. It is essential to choose a machine that accommodates the career size of the product you intend to produce.
Other factors to consider when selecting a plastic injection machine include the level of automation, the machine’s cycle time, the level of energy consumption, the machine’s reliability, and the cost of the machine.
In conclusion, it is essential to consider the material, tonnage, shot size, and career size when selecting a plastic injection machine. The machine you choose should be capable of producing the product you want to make with precision and accuracy, at a reasonable cost, and with high reliability.
-
7.Maintenance and Troubleshooting
Proper maintenance and troubleshooting are essential for the efficient and reliable operation of plastic injection machines. Regular inspection and cleaning of machine parts will extend the machine’s life and reduce the risk of equipment failure. In this section, we will look at some critical maintenance and troubleshooting tips for plastic injection machines.
Maintenance Tips:
- Keep the barrel and screw clean to prevent contamination of the material
- Lubricate the machine’s components regularly, ensuring that they are well greased.
- Check the hydraulic system for leaks and damage
- Ensure that the machine’s cooling system is functioning correctly
- Regularly inspect the machine’s o-ring, nozzle, and check ring for wear and tear.
Troubleshooting Tips:
- Check the machine’s temperature settings, ensuring they are within the recommended range
- Check the hydraulic system for leaks and damage
- Verify that the screw is rotating correctly and that the material is flowing smoothly
- Check the injection pressure and verify that it is within the recommended range
- Monitor the machine’s cycle time and adjust as necessary.
It is essential to consult the operator’s manual or contact the machine’s manufacturer when carrying out maintenance or troubleshooting exercises. The operator’s manual contains detailed information on how to maintain the machine, the recommended replacement parts, and the troubleshooting procedures to follow when the machine develops technical issues.
In conclusion, proper maintenance and troubleshooting are essential for the efficient and reliable operation of plastic injection machines. Regular inspection and cleaning of the machine’s components will extend the machine’s life and significantly reduce the risk of equipment failure. It is crucial to follow the recommended maintenance and troubleshooting procedures provided by the machine’s manufacturer.
-
8.Future Trends in Plastic Injection Machine Technology
The plastic injection machine technology is continually evolving to meet the growing demand for high-quality plastic products with increased efficiency and lower production costs. Here are some of the emerging trends in injection machine technology.
- Industry 4.0:Industries are moving towards the integration of digital technologies and the automation of production processes. The injection molding industry is no exception. The future of injection machine technology will revolve around Industry 4.0, which leverages digitalization, artificial intelligence, and automatic control to optimize production processes, reduce costs, and enhance productivity.
- Hybrid Injection Machines:Hybrid injection machines are an emerging trend in plastic injection machine technology. They combine the quick production speed of electric machines and the clamping force of hydraulic machines. Hybrid machines reduce energy consumption and carbon emissions while producing high-quality plastic products.
- Three-Dimensional Printing:Manufacturers are experimenting with 3D printing as an alternative to traditional injection molding techniques. The use of 3D printing for the small volume production of complex plastic parts has been growing in popularity, and future advancements in the technology could make it a viable option for large volume production.
- Self-Correcting Machines:Emerging machine-learning technology is being integrated into injection molding machines to enhance quality control and efficiency. Self-correcting machines leverage machine learning technologies such as artificial intelligence (AI) to recognize and resolve issues before production is affected, thereby reducing the frequency of errors or malfunctions.
- Sustainable Materials:The plastic industry has come under increasing public scrutiny because of environmental concerns. The push for sustainable materials is leading to the development of bioplastics and other environmentally-friendly alternatives. Future injection machine technology will focus on processing these materials, reducing waste, and enhancing environmental sustainability.
In conclusion, the future of plastic injection machine technology will center on digitalization, automation, sustainability, and innovation. Emerging trends such as Industry 4.0, hybrid injection machines, 3D printing, self-correcting machines, and sustainable materials will shape the future of injection machine technology, leading to more efficient and sustainable production processes that deliver high-quality plastic products.
If you need about Plastic Injection Services,You can click on the V1 Prototype website to find it.
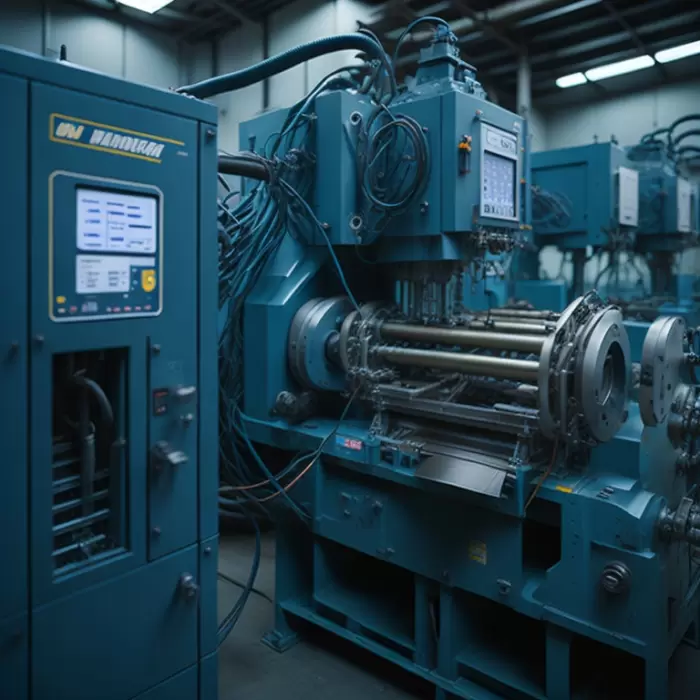
-
9.Conclusion: Is a Plastic Injection Machine the Right Choice for Your Business?
Plastic injection machines are an ideal choice for businesses that require high-volume production of precision plastic products. The machines offer several advantages, including cost-effectiveness, consistency, versatility, high efficiency, and precision.
However, deciding whether a plastic injection machine is the right choice for your business will depend on several factors, including the type of products you intend to produce, production volume, and the cost of machine acquisition, operation, and maintenance.
If your business intends to produce large volumes of plastic products consistently and cost-effectively, a plastic injection machine may be the right choice for you. However, if you plan to produce smaller volumes or products that require other manufacturing processes such as 3D printing or CNC machining, you may need to consider other options.
In conclusion, plastic injection machines are a reliable and efficient option for high-volume production of plastic products. Before investing in a machine, it is essential to evaluate your business needs, production requirements, and the costs involved to make an informed decision.