Technology foundation
The production process
The process of machine production refers to the whole process of making products from raw materials (or semi-finished products). For machine production, it includes transportation and storage of raw materials, preparation of production, manufacturing of blanks, processing and heat treatment of parts, assembly and commissioning of products, painting and packaging, etc. The content of the production process is very extensive. Modern enterprises use the principles and methods of systems engineering to organize and guide production, and regard the production process as a production system with input and output.
In the production process, usually change the shape, size, position and nature of the production object, so that it becomes a finished product or semi-finished product process called the process. It is a major part of the production process. Process: casting, forging, stamping, welding, machining, assembly processes, such as machinery manufacturing process generally refers to the part machining process and machine of the sum of the assembly process, other process is known as the auxiliary process, such as transportation, storage, power supply, equipment maintenance, etc. The process is composed of one or more sequential processes, a process is composed of a number of work steps.
Working procedure is the basic unit of machining process. The so-called process refers to a (or a group of) workers, in a machine tool (or a working place), the same workpiece (or several workpiece at the same time) continuous completion of that part of the process. The main characteristics of a process is not to change the processing object, equipment and operators, and the content of the process is continuous completion.
Work step is a process according to the processing process is divided into components. It is characterized by the machining surface and the tools used, machine tools and cutting parameters are unchanged.
Cutting also called working stroke, refers to the process of metal cutting, when the surface is processed, the cutting speed and cutting amount of the tool and cutting parameters are unchanged, each layer of metal cutting process. A work step sometimes only - - knife, sometimes it takes several times.
The formulation of mechanical processing process, must determine the workpiece to go through several processes and the process of the sequence, only listed the name of the main process and processing order of the brief process process, called process route.
The formulation of the process route is to develop the overall layout of the process, the main task is to choose the surface of the processing method, determine the processing order of each surface, and the number of orders in the whole process. The process route must follow certain principles.
The production type
The types of production are usually divided into three categories:
1.Single production: The production of products of different structures and sizes individually, with few repetitions.
2.Batch production: The production of the same product in batches over the course of a year, with some degree of repeatability.
3.Mass production: Products are manufactured in large quantities, and most work sites often repeat the processing of a certain process of a part.
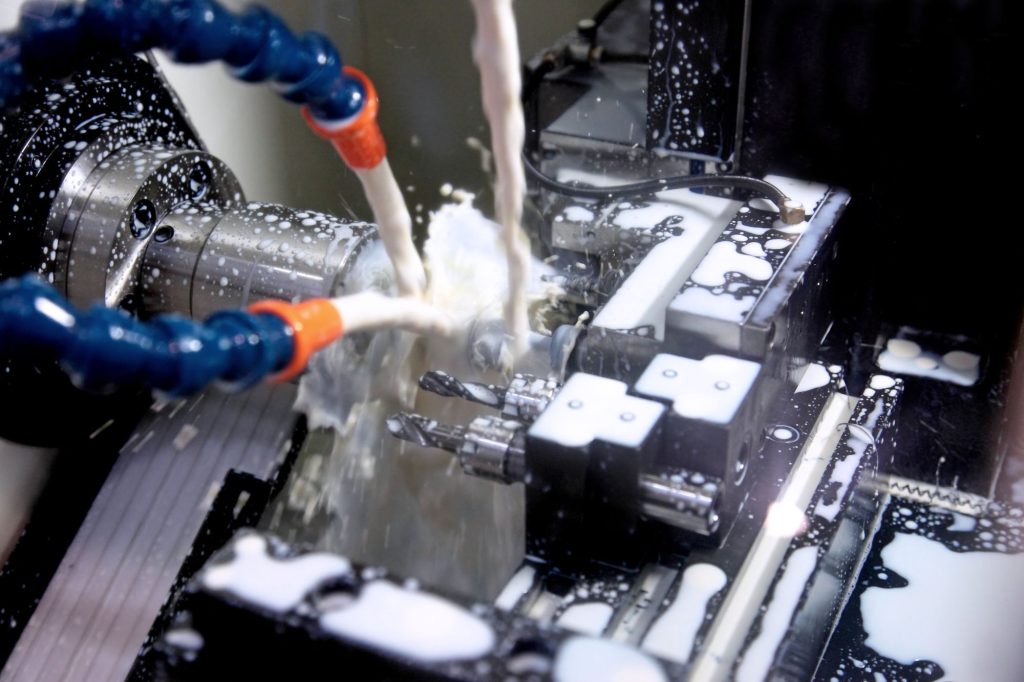
Process specification design
Design Principles:
(1) The designed process procedures should be able to ensure the machining quality of the machine parts (or the assembly quality of the machine), to meet the technical requirements specified on the design drawing.
(2) The technological process should have high productivity, so that the product can be put on the market as soon as possible.
(3) Try to reduce manufacturing costs
(4) Pay attention to reduce the labor intensity of workers to ensure production safety.
Original Data:
(1) Product assembly drawing and parts drawing.
(2) Product acceptance quality standards.
(3) Annual production program of products.
(4) Production conditions of the factory, including specifications, performance and existing state of machine tools and process equipment, the technical level of workers, the ability of the factory to make homemade process equipment, and the ability of the factory to supply power and gas, etc.
(5) Design manuals and relevant standards required for process design and process equipment design.
(6) Domestic and foreign advanced manufacturing technology information, etc.
Step content:
(1) Analyze and study assembly drawings and parts drawings of products.
(2) Determine the blank.
(3) Formulate the process route and select the positioning base surface.
(4) Determine the equipment used in each process.
(5) Determine the tools, fixtures, measuring tools and auxiliary tools used in each process.
(6) Determine the technical requirements and inspection methods of each main process.
(7) Determine the processing allowance of each process, and calculate the size and tolerance of the process.
(8) Determine the cutting parameters.
(9) Determine the quota of working hours.
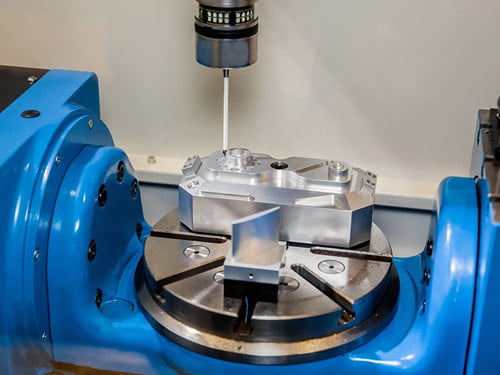