Table of Contents:
- Introduction
- The Plastic Extrusion Process
- Materials Used in Plastic Extrusion
- Applications of Plastic Extrusion
- Advancements and Future Trends in Plastic Extrusion
- Quality Control and Inspection in Plastic Extrusion
- Conclusion
-
1.Introduction
Plastic extrusion is a manufacturing process that involves the heating and melting of plastic raw materials, forcing them through a die, and shaping them into a continuous profile. The process can be used to create a wide variety of plastic products, including tubes, sheets, film, and other custom shapes.During the extrusion process, various plastic materials are extruded using a range of techniques, such as hot extrusion, cold extrusion, and impact extrusion. Extruding plastics offers various advantages, including reduced waste, lower costs, and faster production times compared to other manufacturing processes, such as injection molding.
The plastic extrusion process has evolved from traditional manufacturing techniques to incorporate technological advancements, such as the integration of automation, data exchange, digital twins, and sustainable manufacturing methods. As the industry continues to grow, innovative approaches to quality control and regulatory requirements, such as safety and environmental impact, have become increasingly essential.
In summary, the plastic extrusion process is a vital component of modern manufacturing, offering numerous benefits and advantages over traditional manufacturing techniques. Its versatility and adaptability make it a popular choice for high-volume production in various industries, and its evolution with technological advancements reflects its ongoing importance and potential growth.
-
2.The Plastic Extrusion Process
Plastic extrusion is a complex process that requires precise control of numerous parameters. The extrusion process involves several stages, including material feeding, heating, melting, conveying, shaping, and cooling. Here are the main elements and steps involved in the plastic extrusion process:
Main Elements of the Extruder:
An extruder is the primary machine used in the extrusion process. It consists of several elements, including:
- Screw: The screw is the primary component of the extruder and is responsible for feeding the raw plastic materials into the barrel and pushing the melted material downstream.
- Barrel: The barrel encloses the screw and provides a pathway for the plastic material to flow through the machine.
- Hopper: The hopper serves as a storage container for the raw plastic materials and feeds them into the machine.
- Die: The die is a component at the end of the extruder that shapes the plastic material into the desired product shape.
.
Steps in the Extrusion Process:
The extrusion process typically includes the following steps:
- Material Feeding: The raw plastic materials are fed from the hopper into the extruder through the screw.
- Heating and Melting: The plastic materials are heated and melted as they move through the barrel, using heat generated by friction from the turning screw.
- Conveying and Shaping: The melted material is then conveyed through the die, which determines the shape and size of the extruded product.
- Cooling and Cutting: As the plastic material leaves the die, it is cooled and solidified using a cooling process. The extruded product is then cut to the desired length.
.
Types of Extrusion Processes:
There are various types of extrusion processes. The most commonly used processes include:
- Blown Film Extrusion: In this process, the plastic material is extruded into a tube through a circular die. Air is then blown into the tube to create a thin film.
- Sheet Extrusion: In this process, the plastic material is fed through a flat die to create a sheet or film.
- Profile Extrusion: This process involves the extrusion of plastic materials into a specific shape or profile using a custom die.
- Co-extrusion: In this process, two or more plastic materials are extruded at the same time to create a product with multiple layers or colors.
In summary, the plastic extrusion process comprises several steps and elements, including the extruder, hopper, barrel, and die. The process can be used to create various products such as films, sheets, profiles, and more using different types of extrusion processes, including blown film, sheet, profile, and co-extrusion. Understanding the different elements and types of extrusion processes is important to ensure precise control of the extrusion process and to produce high-quality extruded products with accuracy and consistency.
-
3.Materials Used in Plastic Extrusion
Plastic extrusion can use several types of polymers and additives to achieve the desired properties in the final product. The selection of materials depends on the requirements of the application and the extrusion process. Here are the most common types of polymers, additives, fillers, and specialty plastics used in extrusion:
Types of Polymers Used:
The most common types of polymers used in plastic extrusion include:
- Polyethylene (PE): PE is a widely used thermoplastic that has high chemical resistance, good impact strength, and excellent electrical insulation properties.
- Polyvinyl chloride (PVC): PVC is a thermoplastic with high chemical resistance and high dimensional stability. It is also flame-resistant and easy to customize with additives.
- Polypropylene (PP): PP is a thermoplastic with high chemical and heat resistance, excellent electrical conductivity, and a low density.
- Polystyrene (PS): PS is a versatile thermoplastic with low cost, excellent dimensional stability, and good thermal insulation properties.
.
Additives and Fillers Used in Extrusion:
Additives and fillers are often used to modify the properties of polymers used in plastic extrusion. Common additives and fillers include:
- Plasticizers: Plasticizers are added to the polymer to increase flexibility, durability, and resistance to cracking.
- Stabilizers: Stabilizers are used to improve the plastic’s resistance to high temperatures, ultraviolet light, and environmental agents.
- Pigments: Pigments are added to the plastic to give it a specific color.
- Reinforcing Fillers: Fillers such as glass fibers, carbon fibers, and other inorganic materials can be added to provide improved strength and stiffness.
.
Specialty plastics used in Extrusion:
Specialty plastics can be used in plastic extrusion to enhance the properties of the final product for specific applications. Some of the most commonly used specialty plastics include:
- Nylon: Nylon is a thermoplastic with excellent abrasion resistance, high strength, and stiffness.
- Polycarbonate: Polycarbonate has excellent impact resistance, clarity, and is an ideal choice for safety applications.
- Acrylonitrile Butadiene Styrene (ABS): ABS is a thermoplastic that is easy to process, offers good impact resistance, and is used for automotive parts, toys, and consumer electronics.
- Ethylene Vinyl Acetate (EVA): EVA is a thermoplastic that is used in applications requiring flexibility, durability, and good optical properties such as packaging or shoe soles.
In summary, plastic extrusion can use several types of polymers, additives, fillers, and specialty plastics to achieve the desired properties in the final product. The selection of materials depends on the requirements of the application and the extrusion process, such as tensile strength, flexibility, transparency, and more. The careful selection of materials and additives is essential to ensure the quality and consistency of the extruded products.
-
4.Applications of Plastic Extrusion
Plastic extrusion has a wide range of applications across various industries, thanks to its versatility and ability to produce complex shapes and sizes in large volumes. Here are some of the most common applications of plastic extrusion:
Building and Construction Industry:
In the building and construction industry, plastic extrusion is used to create a variety of profiles and components for windows and doors, flooring, roofing, and insulation. These extruded profiles can be customized to fit specific applications, providing reliable and cost-effective solutions while reducing waste compared to traditional building materials.
Automotive Industry:
In the automotive industry, plastic extrusion is used to produce components such as bumper guards, spoilers, and trims. Extruded plastic is ideal for these applications due to its low weight, high impact resistance, and the ability to create complex shapes easily.
Packaging Industry:
In the packaging industry, plastic extrusion is used to produce tubes, films, and other custom shapes for packaging products such as beverages, food, and consumer goods. Plastic extruded packaging materials provide high levels of protection, stability and, often offer solid barriers to moisture, light or oxygen, extending the shelf life of the product.
Medical Industry:
In the medical industry, plastic extrusion is used to produce catheters, tubing, and other medical and dental devices. Extruded plastic medical components can offer excellent biocompatibility, precision, and reduced health risks along with the flexibility to create a wide range of geometries subject to FDA regulations.
Other industries that use plastic extrusion include the electrical and electronics, marine, furniture, and recreational industries. The use of plastic extrusion is constantly expanding and finding new applications due to material and process improvements.
In summary, plastic extrusion is a versatile and efficient manufacturing process with applications in various industries. Customizable shapes and sizes, along with the ability to combine multiple materials, fillers and colors, make extruded plastics one of the most reliable and easily reproducible processes for manufacturing a wide range of products. As new materials and processes become available the potential for expansion and exploring new applications across industries continues to expand rapidly.
-
5.Advancements and Future Trends in Plastic Extrusion
Plastic extrusion has come a long way from traditional manufacturing techniques, and new advancements have continued to improve the process. Here are some notable advancements and future trends in plastic extrusion:
Advancements in Extrusion Technology:
Extrusion technology has seen several advancements, including improved process control, co-extrusion, multi-layer extrusion, and extrusion blow molding. Advancements in sensors, data collection, and real-time monitoring technologies allow manufacturers to optimize the process for quality, productivity, and efficiency.
The Impact of Sustainability on Extrusion:
Sustainability has become a significant driver of innovation in plastic extrusion. Manufacturers are investing in more sustainable materials and recycling technologies, with biodegradable polymers and reusable materials becoming more common. Additionally, some manufacturers are developing strategies that focus on waste reduction throughout the extrusion process, through reusing scrap materials, carefully regulating raw materials, and optimizing recycling initiatives.
The Prospect of Industry 4.0 in Extrusion:
Industry 4.0 is poised to revolutionize the way plastic extrusion is conducted. The integration of smart technologies such as cloud computing, IoT sensors, and artificial intelligence offers the potential for the automation of the entire extrusion process, from material management and quality control to production scheduling and maintenance. Alongside real-time data analysis of materials, equipment performance, and supply chain, Industry 4.0 promises a significant reduction in costs and production time.
Other advancements and future trends in plastic extrusion include the development of micro-extrusion technology for miniature components, that are essential in the medical and electronic industries, as well as 3D extrusion printing to expand the potential of additive manufacturing. Manufacturers continue to work with new and innovative materials, with composite materials and hybrid extrusion processes providing an expanding range of product development opportunities.
In conclusion, Plastic extrusion is a rapidly evolving manufacturing process that has continued to grow alongside technological advancements, sustainability initiatives, and the digitalization of the production process. The potential of Industry 4.0 and the evolution of 3D printing promise continued improvement in terms of productivity, efficiency, and sustainability. The development of new materials and hybrid extrusion processing techniques provide new opportunities, prompting manufacturers to continue venturing into new areas across industries.
If you need more the information ,You can click on the V1 Prototype website to find it.
-
6.Quality Control and Inspection in Plastic Extrusion
Quality control and inspection are essential in plastic extrusion to ensure that the final product meets the required specifications and standards. Here are some key aspects of quality control and inspection in plastic extrusion:
Key Quality Control Metrics in Extrusion:
The critical quality control metrics in plastic extrusion include dimensional accuracy, tensile strength, impact strength, clarity, color consistency, surface finish, and chemical resistance. These metrics are crucial to ensure that the extruded product meets its functional requirements and can be safely used in the application it was designed for.
QC Techniques and Approaches:
To achieve the required quality levels, different techniques and approaches are used in plastic extrusion, including Statistical Process Control (SPC), visual inspection, surface texture analysis, and mechanical testing. By adhering to the correct standards and protocols, manufacturers can minimize the potential for defects and mitigate the risk of non-conformance.
Safety and Regulatory Challenges and Considerations:
Safety and regulatory challenges are inherent in plastic extrusion, and manufacturers must follow strict guidelines to ensure safe and compliant operations. These regulations vary by country and even by region, such as regulations like RoHS, REACH, Food and Drug Administration, and other regional equivalents. These regulations encompass various aspects such as, fire and building codes, worker welfare or labelling and toxicity, among others. Additional challenges can arise from dealing with concentrated heat, electricity, and high-pressure machinery. Manufacturers should create a comprehensive safety plan and establish clear protocols that involve every aspect from development, usage, and regular maintenance of their equipment.
To ensure effective quality control and inspection in plastic extrusion, it is necessary to employ and train skilled personnel in the use of proper protocols and quality metrics, enforce stringent monitoring and record-keeping systems, creating detailed inspection protocols, and invest in quality monitoring equipment. Continuous monitoring of production, through real-time data analysis, can be leveraged to detect issues and quickly correct problems. By implementing and strictly following these best practices and quality control measures, manufacturers can deliver consistent and high-quality products, reduce downtime, increase productivity, and maintain a safe and compliant operation.
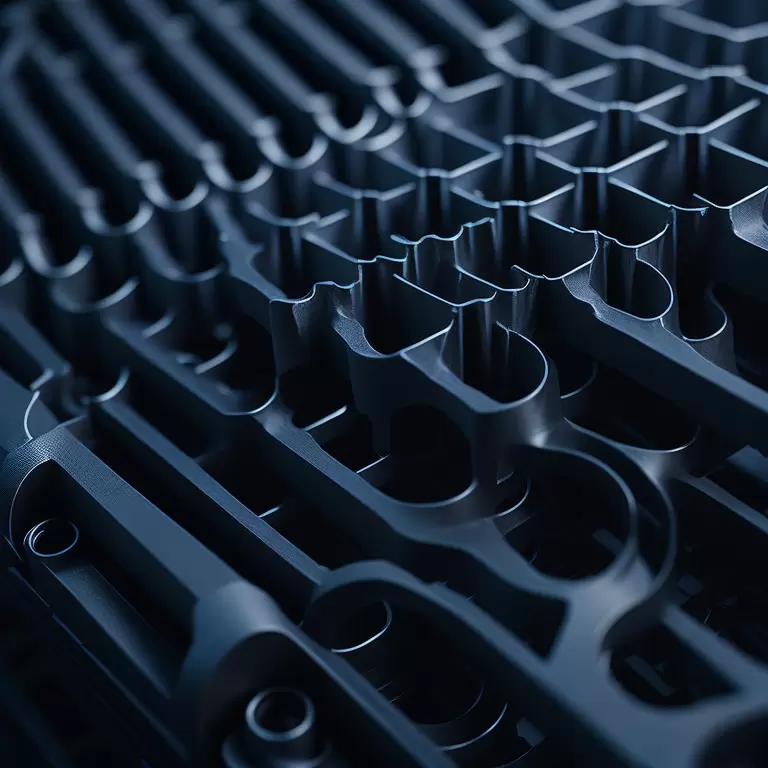
-
7.Conclusion
Plastic extrusion is a highly versatile and reliable process that has a vital role in modern manufacturing. It has become an essential manufacturing process across various industries, including building and construction, automotive, packaging, and medical, among others. The process enables the production of high-quality plastics in large volumes, ensuring consistency, cost-effectiveness, and minimal waste.
The advancement of new technologies, such as Industry 4.0, the rise of sustainable materials, and the expansion into new market segments, emphasize the potential for growth and development in the extrusion industry. As this manufacturing process continues to evolve, there will likely be more emphasis on the development of innovations that increase productivity, as well as improvements aimed at reducing waste and regulating emissions.
Manufacturers of extruded plastic products can maintain a competitive edge by integrating these new technologies, leveraging sustainable best practices, and focusing on effective quality control and monitoring. With an ever-increasing number of applications and new markets available, plastic extrusion is poised to remain an essential and growing process in modern manufacturing.