1> Introduction to Injection Molding Processing
2>The Process of Injection Molding
3>Design Considerations for Injection Molding
4>Material Selection for Injection Molding
5>Troubleshooting Injection Molding Issues
6>Advantages and Disadvantages of Injection Molding
7>Conclusion
Introduction to Injection Molding Processing:
Injection molding is a manufacturing process used to produce complex plastic parts with high precision and accuracy. The process involves melting plastic pellets and injecting them into a mold cavity under high pressure, where they cool and solidify to form the desired part. Injection molding is widely used in various industries, including automotive, medical, electronics, and consumer goods, due to its ability to produce high-quality parts at high volumes and low costs.
The Process of Injection Molding:
The injection molding process can be divided into several stages: clamping, injection, cooling, and ejection.
Clamping: In the clamping stage, the two halves of the mold are closed and held together with high pressure to ensure that the plastic material is held in place during the injection process.
Injection: In the injection stage, the plastic pellets are melted and injected into the mold cavity under high pressure using a screw or piston. The plastic material fills the cavity, taking the shape of the mold.
Cooling: In the cooling stage, the plastic material is left to cool and solidify within the mold. This is a critical stage in the injection molding process, as it determines the final part's quality and dimensional accuracy.
Ejection: In the ejection stage, the mold is opened, and the part is ejected from the mold cavity. The cycle is then repeated for the next part.
Design Considerations for Injection Molding:
Designing a part for injection molding requires careful consideration of several factors, including part geometry, wall thickness, draft angles, and undercuts. The goal is to create a part that can be easily molded, with consistent quality and minimal waste.
Part Geometry: The part geometry should be designed to allow for proper flow of the plastic material during injection, avoiding any areas of stagnation or turbulence that can result in defects.
Wall Thickness: The wall thickness of the part should be designed to ensure adequate strength and stiffness while minimizing material usage and cycle time.
Draft Angles: Draft angles are critical to allow the part to be easily ejected from the mold cavity. The recommended draft angle is typically 1-2 degrees per side.
Undercuts: Undercuts are areas of the part that cannot be easily ejected from the mold and require additional design features or special tooling.
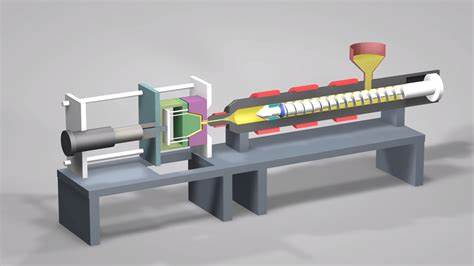
Material Selection for Injection Molding:
The selection of material for injection molding is a critical factor that can affect the part's performance, cost, and manufacturability. Common materials used in injection molding include thermoplastics, thermosets, and elastomers.
Thermoplastics: Thermoplastics are the most commonly used materials in injection molding due to their excellent mechanical properties, high stiffness, and low cost. Examples of thermoplastics include polyethylene, polypropylene, and polycarbonate.
Thermosets: Thermosets are materials that undergo a chemical reaction during the molding process, resulting in a cross-linked polymer network. They offer excellent heat and chemical resistance but are typically more expensive than thermoplastics. Examples of thermosets include epoxy and phenolic resins.
Elastomers: Elastomers are materials that exhibit high elasticity and resilience, making them suitable for applications requiring flexibility or vibration damping. Examples of elastomers include silicone rubber and polyurethane.
Troubleshooting Injection Molding Issues:
Injection molding is a complex process that can be affected by a variety of factors, resulting in defects or quality issues. Some common issues that can arise during injection molding include:
- Sink Marks: Sink marks occur when the plastic material shrinks as it cools, resulting in depressions or dimples on the part surface. To prevent sink marks, the part's design should have uniform wall thickness, and the cooling rate should be controlled.
- Warping: Warping occurs when the part cools unevenly, resulting in a distorted shape. To prevent warping, the mold should be designed with uniform cooling channels and the part's geometry should have a consistent wall thickness.
- Flash: Flash occurs when excess plastic material escapes from the mold cavity, resulting in a thin layer of material on the part surface. To prevent flash, the mold should be designed with proper venting and clamping force should be controlled.
- Short Shots: Short shots occur when the plastic material does not completely fill the mold cavity, resulting in incomplete parts. To prevent short shots, the injection speed, pressure, and temperature should be optimized.
- Bubbles: Bubbles occur when trapped air is compressed during the injection process, resulting in voids or air pockets in the part. To prevent bubbles, the mold should be designed with proper venting, and the plastic material should be dried before injection.
Advantages and Disadvantages of Injection Molding:
Injection molding offers several advantages over other manufacturing processes, including:
- High Production Rates: Injection molding can produce high volumes of parts in a short amount of time, making it suitable for large-scale production.
- Design Flexibility: Injection molding can produce complex parts with high precision and accuracy, allowing for intricate designs and features.
- Cost-Effective: Injection molding can be cost-effective for high-volume production due to its ability to use low-cost materials and reduce waste.
However, there are also some disadvantages to injection molding, including:
- High Initial Tooling Costs: The cost of designing and manufacturing the mold can be high, making it less cost-effective for small-scale production.
- Limited Material Selection: Some materials may not be suitable for injection molding due to their properties, limiting the range of materials that can be used.
- Environmental Concerns: Injection molding produces waste material that can be difficult to recycle, making it less environmentally friendly than other manufacturing processes.
Conclusion Injection Molding Processing:
Injection molding is a versatile and cost-effective manufacturing process used to produce high-quality plastic parts with precision and accuracy. Successful injection molding requires careful consideration of several factors, including part design, material selection, and process parameters. By understanding the injection molding process and its challenges, manufacturers can produce high-quality parts at high volumes and low costs, making it a popular choice for various industries.