Table of Contents:
- Introduction
- The Die Casting Process
- Best Practices for Die Casting
- Die Casting Techniques
- Applications of Die Casting
- Die Casting vs Other Manufacturing Processes
- Sustainability in Die Casting
- Future of Die Casting
- Conclusion
-
1.Introduction to Die Casting
Die casting is a manufacturing process used to produce high-quality metal parts by injecting molten metal into a mold cavity. The process was developed in the early 1800s and has since evolved to become one of the most widely used metalworking processes in the world. Die casting allows for the production of complex shapes and geometries that would be difficult or impossible to achieve through other manufacturing processes. This guide will explore the die casting process, its history, techniques, applications, and best practices.
The origins of die casting can be traced back to the mid-1800s, when a patent was filed for the first manually operated die-casting machine. Over the years, improvements were made to the process, including the development of automated casting machines and the use of computers for design and simulation. Today, die casting is used across various industries, including the automotive, aerospace, electronics, and medical industries.
Die casting offers numerous benefits, including the ability to produce parts with high precision, excellent surface finish, and dimensional stability. The high production rate makes it an affordable and efficient manufacturing process. Die casting is also highly versatile and can be used to create a wide range of complex shapes and parts.
In this guide, we will explore how the die casting process works, the types of die casting techniques, best practices for die casting, its applications across various industries, and the future of this critical manufacturing process. By the end of this guide, you will have a comprehensive understanding of the die casting process and how it can help improve your manufacturing operation.
-
2.The Die Casting Process
There are several types of die casting methods used in the manufacturing industry, including:
- Cold chamber die casting – In this method, molten metal is poured into a cold chamber, then injected into the mold at high pressure.
- Hot chamber die casting – This technique is used for alloys with a low melting point, where the metal is melted inside the machine and then injected into the mold.
- High-pressure die casting – This technique uses a hydraulic press to inject molten metal into the mold at high speeds and pressures.
- Low-pressure die casting – The low-pressure casting technique pours molten metal into the mold under low pressure.
- Gravity die casting – In this type of die casting, molten metal is poured into the mold by gravity, producing quality castings with good dimensional accuracy.
.
Advantages and Disadvantages of Die Casting
Some of the advantages of die casting include:
- High production rate – Die casting allows for the production of high volumes of parts in a short period. This makes it an ideal manufacturing process for components used in automobiles and appliances.
- High dimensional accuracy – The die casting process produces parts that are highly precise, with tight tolerances and excellent dimensional stability.
- Good surface finish – The process produces parts with good surface finish, which can be enhanced by polishing, painting or coating.
- Complex shapes – Die casting is suitable for producing complex shapes and parts that would be difficult to create through other processes.
.
However, there are some limitations to die casting, including:
- High initial investment costs – Die casting machines and molds are expensive to acquire, making it a capital-intensive process.
- Limited material selection – Die casting is ideal for use with metals with low melting points such as aluminum, magnesium, and zinc. This limits the types of materials that can be cast through the process.
- Welding and assembly – Parts produced through die casting may require welding or assembling, which can add to the overall manufacturing cost.
.
The Basic Die Casting Process:The die casting process begins with the design of the mold to be used in the casting process. The mold is then fitted into the die casting machine, which injects molten metal into the mold at high pressure. The metal is forced to fill the mold cavity, forming the part’s shape. Once the part has solidified, it is ejected from the mold and undergoes finishing processes such as trimming, shaping, and sandblasting. Quality control is performed on the finished parts to ensure they meet the required specifications.
In Conclusion, the die casting process is a highly versatile manufacturing process used to produce high-quality metal parts utilized in various industries worldwide. The use of several die casting techniques, and best practices ensures that die casting remains a vital manufacturing tool.
-
3.Best Practices for Die Casting
Die casting is a complex manufacturing process that requires adherence to specific guidelines to ensure optimal quality of the final product. Here are several best practices that manufacturers can follow to ensure the success of the die casting process.
Die Casting Design Considerations:The design of the part to be cast is essential when considering die casting. Factors such as draft angle, wall thickness, and radii must be carefully considered to ensure successful casting. Draft angle allows the part to eject from the mold, while wall thickness ensures that the part has enough material to give it strength. Radii reduce stress concentration in corners that may lead to cracking. Also, adding fillets to sharp corners eliminates the possibility of porosity occurring in the casting.
Material Selection for Die Casting:To ensure that the finished part withstands various environmental and chemical exposures, the appropriate material should be chosen for the die casting. Factors such as mechanical properties, corrosion resistance, and ease of casting should be considered when selecting materials for die casting. The commonly used materials for die casting include aluminum alloys, brass alloys, copper alloys, zinc alloys, and magnesium alloys.
Surface Finish and Coatings for Die Casting:To prevent external or internal corrosion, increase part hardness, and provide the finished part an aesthetically pleasing appearance, surface finishes such as painting or coatings should be applied to the part. Some common coating methods used include anodizing, plating, and powder coating.
Quality Control for Die Casting:Quality control is crucial in the die casting process to ensure the parts produced meet design specifications. Statistical Process Control (SPC) is used to monitor and ensure that the parts produced meet the required standards. This process involves taking measurements at each stage of production and making adjustments accordingly. A critical process such as X-ray and chemical analysis may be required to detect any porosity, cracks or surface defects in the casting.
In conclusion, following best practices when designing, selecting materials, applying finishes and coatings, and quality control can significantly impact the success of the die casting process. It is important for manufacturers to continually improve and evaluate their processes for optimal performance, cost-effectiveness and to ensure they meet all quality standards. Die casting is an incredibly reliable and efficient method of producing quality metal parts on a mass-scale, with adaptability to various industries, proving to be a fantastic addition to the manufacturing sector.
-
4.Die Casting Techniques
Die casting techniques are crucial in the manufacturing process, and knowing the right technique for the application is essential to achieve the desired outcome. Here are the most common die casting techniques.
Cold Chamber Die Casting:In cold chamber die casting, metal is melted outside the die casting machine using a furnace. Molten metal is then ladled into the cold chamber by a ladle, and a piston injects the metal into the mold. This process is ideal for metals with a high melting point, such as aluminum and copper alloys.
Hot Chamber Die Casting:For hot chamber die casting, metal is melted inside the machine using a container called a gooseneck. The plunger is used to inject molten metal into the mold. This method is perfect for metals with a low melting point, such as zinc and magnesium alloys.
High-Pressure Die Casting:This die casting process uses a hydraulic press to inject molten metal into the mold at high pressure and speed. The high pressure causes the metal to fill the mold quickly and sharply, resulting in a smooth and high-quality surface finish. High-pressure die casting is ideal for producing complex parts with fine details.
Low-Pressure Die Casting:Low-pressure die casting involves pouring molten metal into the mold under low pressure, drawing the metal into the cavity, in a method similar to gravity casting. This process allows for the production of high-quality parts with minimal turbulence, lower porosity than gravity die casting, and a reduced risk of scarring, making it ideal for mass production of high-quality components.
Gravity Die Casting:Gravity die casting or permanent mold casting refers to the process in which molten metal flows into the mold cavity by its weight force as gravity, without additional forceful injection. This process uses a reusable metal mold, which can produce many parts and produce high quality and precise parts with smooth surfaces.
Die casting techniques are essential in the manufacture of complex metal parts with high precision and accuracy. The type of die casting technique used will depend on the properties of the metal, the complexity of the part and the required production rate. By utilizing the appropriate die casting technique, manufacturers can produce high-quality parts efficiently and economically, meeting the required design specifications.
-
5.Applications of Die Casting
Die casting is a versatile manufacturing process that produces high-quality parts, that finds application in a wide range of industries. Here are some of the most common applications of die casting.
Automotive Industry:Die casting plays a crucial role in the automotive industry, producing essential parts such as engine blocks, transmission cases, and wheels. The process’s high efficiency and ability to produce large volumes of parts quickly make it an ideal process for mass-producing automotive components.
Aerospace Industry:The aerospace industry requires high-quality, lightweight, and robust parts, which is where die casting comes into play. Die casting produces durable and lightweight parts of intricate shape and size, which meet the stringent requirements of the aerospace industry.
Consumer Goods:Die casting is widely used in the production of consumer goods such as toys, sporting equipment, household appliances, and decorative items. The manufacturing process produces high-quality parts with tight tolerances, making them an ideal choice for the consumer goods industry.
Medical Equipment:The medical equipment industry requires parts that are lightweight and precise, with smooth surfaces that can be easily cleaned. Die casting produces parts meeting hygiene and quality standards, which are essential in the medical industry.
Electronics:Die casting is used in the electronics component manufacturing process, producing parts such as heat sinks, power boxes, and connectors. These parts require high dimensional accuracy and superior surface finish, which the die casting process provides. Die casting can efficiently produce parts with complex geometries, making it an ideal manufacturing process for electronic components.
Defense Industry:The defense industry requires parts to withstand high mechanical stresses and harsh environments. Die casting can produce high-strength, lightweight parts with intricate design aspects, making it a trusted process in the defense industry.
Die casting is a versatile manufacturing process that finds applications across many industries, delivering accurate, cost-effective, and durable parts with high efficiency. Manufacturers rely on die casting to produce parts that meet critical engineering specifications required for products such as automobiles, aerospace, consumer goods, medical equipment, electronics, and defense industries.
-
6.Die Casting vs Other Manufacturing Processes
Die casting is a commonly used manufacturing method in the production of high-quality metal parts. It is often compared to other manufacturing processes like injection moulding, sand casting, investment casting, and permanent mold casting. Here are some key differences between die casting and other manufacturing processes.
Comparison to Injection Moulding:Injection moulding and die casting are both used to produce large volumes of parts quickly. However, injection moulding uses thermoplastic materials, while die casting uses molten metal. Die casting can produce more complex parts with a better surface finish than injection moulding. Die casting is well-suited for strong, durable, and heat-resistant metal parts, while injection moulding is advantageous for producing plastic parts with excellent color, texture, and shape.
Comparison to Sand Casting:Sand casting is a process where molten metal is poured into a sand mold. While die casting is best suited for medium to high volume and mass production, sand casting produces large single parts. Die casting produces parts with high surface finish and dimensional accuracy, while sand casting yields lower dimensional accuracy and surface finish.
Comparison to Investment Casting:Investment casting is a process in which a ceramic mold is created from a wax pattern. Die casting produces parts with high precision, reduces materials wastage and requires minimal finishing processes, whereas investment casting comes with an additional finishing process to remove the patterns.
Comparison to Permanent Mold Casting:Permanent mold casting is a process that utilizes reusable metal molds. Like die casting, permanent mold casting allows for the production of high-quality parts with tight tolerances and good surface finish. One significant difference is the cost of the mold; permanent mold casting molds are more expensive but can be re-used multiple times, reducing material costs for large production runs. Die casting offers faster cycle times and generates more precise and accurate parts, mitigating defects that would be higher in permanent mold casting.
There is a vast array of manufacturing processes available when making products, and selecting the right process for the task depends on the application, production volume, part size, dimensions, complexity, tolerances, and functional requirements. While die casting, injection molding, sand casting, investment casting and permanent molding all have their unique benefits and shortcomings, die casting remains one of the most efficient, precise and effective methods of manufacturing intricate metal parts in medium to high volumes.
-
7.Sustainability in Die Casting
Sustainability in die casting is an essential factor, as the process can result in waste generation and energy consumption. Here are some ways to promote sustainability in die casting.
Recycling and Reusing Materials:Die casting employs the use of metal alloys that can be reused or recycled. Recycling materials used in die casting can help protect the environment by reducing waste generation, reducing energy consumption and greenhouse gas emissions. Recycling scrap metal produced during manufacturing, instead of disposing of it in landfills, can significantly minimize the amount of waste generated during the process.
Development of Eco-Friendly Materials:Manufacturers are continually developing more eco-friendly materials that can be used in die casting. For example, some companies are producing eco-friendly and lightweight alloys suitable for use in die casting, such as aluminum and magnesium alloys that have high strength and are recyclable. The development of additional eco-friendly alternatives promotes sustainability practices in die casting.
Best Practices for Reducing Waste:Manufacturers can use several best practices that promote sustainability and reduce waste during the die casting process. For instance, implementing measures that reduce excess metal used in casting, such as optimizing gate and runner placement, using appropriate fill rates, and reducing overflows. Other measures could include increasing machine efficiency, and incorporating lean manufacturing principles, which involve creating efficient and streamlined manufacturing processes.
Sustainability is vital in all aspects of manufacturing, including die casting which plays an essential part in many industries. Promoting sustainability practices can significantly impact the environmental impact and reduce the strain on resources, lowering waste generation and energy consumption. By implementing strategies such as recycling and reusing materials, adopting eco-friendly materials, and optimizing manufacturing processes, die casting manufacturers can create sustainable and efficient manufacturing practices.
-
8.Future of Die Casting
The future of die casting looks promising, with many advancements in technology, new applications opening up, and a focus on sustainable manufacturing. Here are some significant trends shaping the future of die casting.
Advancements in Technology:Die casting continues to evolve with advancements in technology, which is driving innovation and greater efficiency. For example, the use of high-pressure die casting has increased in recent years due to its ability to produce complex parts with precision and speed. Also, new digital technologies such as artificial intelligence, machine learning, and data analytics are being integrated into die casting, enhancing automation.
New Applications of Die Casting:As new materials and alloys are developed, new applications for die casting are emerging. For example, magnesium alloys are finding many uses in the automotive industry, while aluminum, copper and zinc alloys are being increasingly used in electronics, aerospace and construction sectors. Other areas of growth include medical equipment, defence, and consumer goods, with the demand for intricate and lightweight parts on the rise.
Shifting Towards Sustainable Manufacturing:Sustainable manufacturing is becoming increasingly important in the manufacturing industry. Die casting manufacturers are adopting sustainability practices such as recycling, reusing materials, reducing waste and emissions, and decreasing energy consumption. In the future, we can expect to see more innovative and sustainable die casting techniques to minimize environmental impact and waste generation.
Die casting has come a long way since its inception and continues to grow and adapt to meet the needs of various industries. Advancements in technology, increased applications, and sustainable manufacturing initiatives are the driving force behind this growth. The future of die casting looks promising, with new materials, alloys, innovative manufacturing methods and sustainable practices making the process more efficient, cost-effective, and environmentally friendly.
If you need about Metal Die Casting Services,You can click on the V1 Prototype website to find it.
-
9.Conclusion
In conclusion, die casting has become a crucial process in modern manufacturing, producing high-quality, reliable, and cost-effective metal parts with excellent dimensional accuracy and a smooth surface finish. It has become the favored method of manufacturing parts with high precision, intricate geometry and consistency, in mass production.
For a successful die casting process, various factors come into play, such as the choice of material used, mold design, injection details, surface treatment, and post-processing. Optimizing these factors plays a crucial role in achieving the desired part quality and efficiency of the process.
Die casting has a vast array of applications in many industries, such as automotive, aerospace, consumer goods, medical equipment, electronics, and defense, and the technology continues to evolve, driven by advancements in material sciences, data analytics, and artificial intelligence.
In the future, the focus will shift towards sustainable manufacturing practices, with the recycling of materials and optimizing energy consumption becoming essential in the die casting process. As new materials and alloys are developed, die casting will be able to produce lightweight, high-strength and sustainable parts for a wide range of applications, continually evolving according to the changing needs of modern manufacturing.
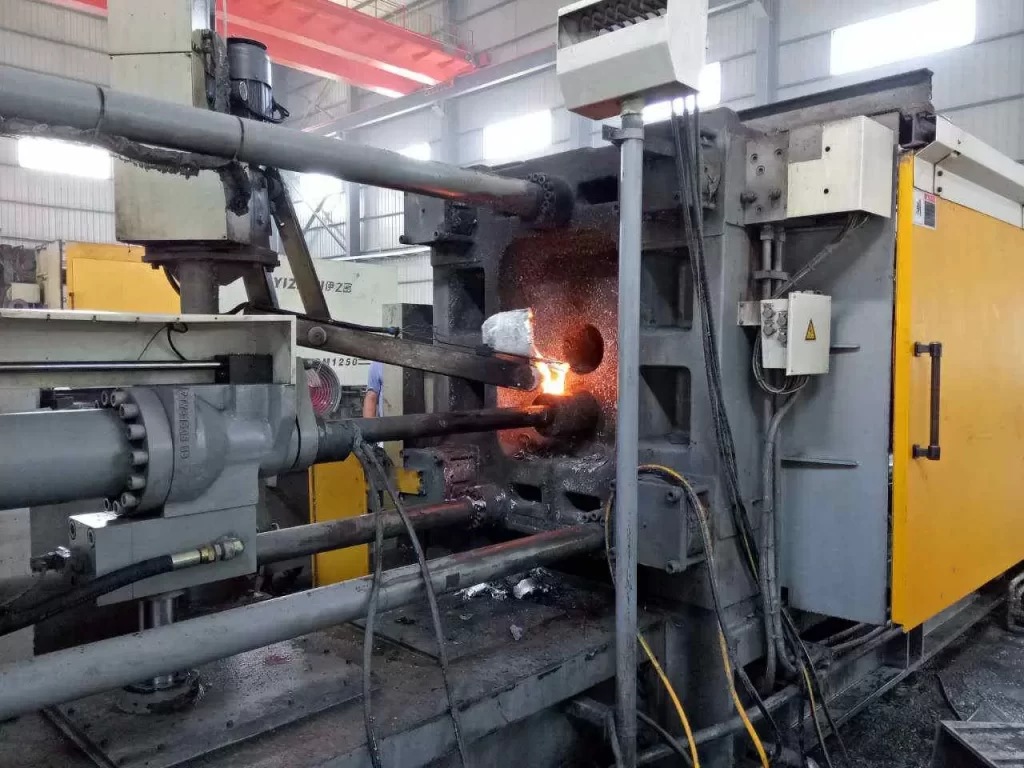