Table of Contents:
- Introduction to Nylon Injection Molding
- Types of Nylon Used in Injection Molding
- Nylon Injection Molding Techniques
- Nylon Injection Molding Applications
- Design Considerations for Nylon Injection Molding
- Common Nylon Injection Molding Defects and Solutions
- Quality Control and Testing in Nylon Injection Molding
- Best Practices for Nylon Injection Molding
- Conclusion
-
1.Introduction to Nylon Injection Molding
Nylon injection molding is a manufacturing process used to produce parts made from nylon polymer material. It involves the use of an injection molding machine to inject molten nylon into a mold cavity, where it cools and solidifies to form the desired shape.
Definition and Overview:
Nylon injection molding is a popular method for manufacturing a wide range of parts due to the excellent properties of nylon such as high strength, rigidity, toughness, and good resistance to chemicals and abrasion. Nylon injection molding is used in various industries such as automotive, consumer goods, electrical and electronics, industrial equipment, and medical devices.
.
Advantages and Disadvantages of Nylon Injection Molding:
Advantages:
- High strength and toughness
- Good resistance to chemicals and abrasion
- High melting point
- Low coefficient of friction
- High stiffness and rigidity
- Easy to process
Disadvantages:
- Susceptible to moisture absorption, which can affect dimensional stability
- Can be difficult to mold due to its high melting point
- Prone to warping and cracking if not molded correctly
- Can be expensive compared to other plastics
Overall, the advantages of nylon injection molding outweigh its disadvantages, making it a popular choice for producing parts with high strength and durability requirements.
-
2.Types of Nylon Used in Injection Molding
There are several types of nylon used in injection molding, each with its own unique properties and characteristics. The most common types of nylon used in injection molding are Nylon 6 and Nylon 6/6.
Nylon 6 vs Nylon 6/6:
- Nylon 6: This type of nylon is a thermoplastic material that is commonly used in injection molding due to its high strength and toughness. It has a lower melting point compared to Nylon 6/6, making it easier to process. Nylon 6 is also more flexible than Nylon 6/6, which makes it a good choice for parts that require flexibility and impact resistance.
- Nylon 6/6: This type of nylon is a thermoplastic material that is known for its high strength, stiffness, and resistance to heat and chemicals. It has a higher melting point compared to Nylon 6, which makes it more difficult to process. Nylon 6/6 is also more rigid than Nylon 6, which makes it a good choice for parts that require high stiffness and dimensional stability.
Other Types of Nylon for Injection Molding:
- Nylon 4/6: This type of nylon is a copolymer of Nylon 4 and Nylon 6, and is known for its high melting point and good resistance to impact and abrasion. It is commonly used in automotive and industrial applications.
- Nylon 6/10: This type of nylon has a lower melting point compared to Nylon 6/6, and is known for its good resistance to moisture and chemicals. It is commonly used in electrical and electronic applications.
- Nylon 12: This type of nylon is a thermoplastic material that is known for its high flexibility, toughness, and resistance to impact and chemicals. It is commonly used in medical device and consumer product applications.
The choice of nylon material depends on the specific requirements of the part being produced, including strength, stiffness, flexibility, impact resistance, and resistance to heat and chemicals.
Click on the V1 Prototype website to gain more information.
-
3.Nylon Injection Molding Techniques
Injection molding is a widely used manufacturing process for producing nylon parts. The process involves the use of an injection molding machine to melt the nylon pellets and inject the molten material into a mold cavity. The molten material then cools and solidifies to form the desired shape. The following are the basic techniques used in nylon injection molding:
- Injection Molding Process:
The injection molding process involves four stages: clamping, injection, cooling, and ejection. In the clamping stage, the mold is closed and held under pressure. In the injection stage, the melted nylon is injected into the mold. In the cooling stage, the molten material solidifies and cools in the mold. In the ejection stage, the part is ejected from the mold. - Preparing Nylon Pellets for Injection Molding:
Before the nylon pellets can be used in the injection molding process, they must be properly dried to remove any moisture that may have been absorbed during storage. Moisture can cause defects in the finished parts, such as warping and cracking. The drying process typically involves placing the pellets in a hopper and subjecting them to a hot air stream. - Injection Molding Machine Setup:
To set up the injection molding machine, the mold is mounted on the machine and the mold cavity is cleaned and lubricated. The machine is then calibrated to ensure that the correct amount of material is injected into the mold. The temperature of the barrel and mold is also set to ensure proper melting and cooling of the material. - Injection Molding Parameters:
The injection molding parameters are the settings that control the injection molding process. These include the temperature of the barrel and mold, injection pressure, injection speed, holding pressure, and holding time. These parameters must be set correctly to ensure that the part is produced to the desired specifications and with minimal defects.
Overall, nylon injection molding requires careful attention to the injection molding process, preparation of the nylon pellets, setup of the injection molding machine, and optimization of the injection molding parameters to ensure high-quality parts.
-
4.Nylon Injection Molding Applications
Nylon injection molding is a versatile manufacturing process that can be used to produce a wide range of parts with varying shapes, sizes, and properties. The following are some of the industries and applications where nylon injection molding is commonly used:
- Automotive Industry:
Nylon injection molding is used extensively in the automotive industry to produce parts such as engine covers, air intake manifolds, and fuel system components. Nylon’s high strength, stiffness, and resistance to heat and chemicals make it a popular choice for these applications. - Consumer Goods:
Nylon injection molding is used to produce a variety of consumer goods, including kitchen utensils, toys, and sports equipment. Nylon’s toughness, durability, and resistance to impact and abrasion make it ideal for these applications. - Electrical and Electronics:
Nylon injection molding is used in the electrical and electronics industry to produce parts such as connectors, switches, and housings for electronic devices. Nylon’s high dielectric strength, resistance to moisture, and good dimensional stability make it well-suited for these applications. - Industrial Equipment:
Nylon injection molding is used in the production of industrial equipment such as gears, bearings, and rollers. Nylon’s high strength, toughness, and resistance to wear make it an ideal material for these applications. - Medical Devices:
Nylon injection molding is also used in the production of medical devices such as catheters, syringes, and surgical instruments. Nylon’s biocompatibility, flexibility, and resistance to chemicals and sterilization make it a good choice for these applications.
Overall, nylon injection molding is a versatile manufacturing process that can be used in a wide range of industries and applications where high strength, toughness, and resistance to heat, chemicals, and wear are required.
-
5.Design Considerations for Nylon Injection Molding
Nylon injection molding requires careful consideration of the design of the part, the mold, and the selection of materials. The following are some important design considerations to keep in mind when designing parts for nylon injection molding:
- Part Design:
The design of the part should take into account the specific requirements of the application and the manufacturing process. For example, the part should be designed with features such as ribs, gussets, and fillets to increase stiffness and reduce warping. It’s also important to avoid sharp corners and edges that can cause stress concentrations and lead to cracking. - Mold Design:
The mold should be designed to produce parts that meet the desired specifications with minimal defects. The mold should be designed with sufficient draft angles to ensure that the part can be easily ejected from the mold. The mold should also be designed with appropriate cooling channels to ensure even cooling of the part and minimize cycle time. - Material Selection:
The selection of the appropriate nylon material is critical to ensure that the part meets the required performance characteristics. Different nylon grades have varying properties such as strength, stiffness, and heat resistance, and selecting the right grade can significantly impact the part’s performance. - Wall Thickness:
The wall thickness of the part should be designed to achieve the desired strength and stiffness while minimizing material usage. Wall thickness that is too thin can cause the part to be weak and prone to breaking, while walls that are too thick can result in excessive material usage and longer cycle times. - Draft Angle:
Draft angle is the angle at which the mold walls taper away from the part’s surface, which allows for easy ejection of the part from the mold. Appropriate draft angles are essential to prevent the part from sticking to the mold and causing damage. - Gate Design:
The gate is the opening in the mold where the molten material enters the cavity. The gate should be designed to minimize the appearance of weld lines and reduce the chance of air entrapment, which can cause cosmetic defects and weaken the part.
Overall, designing parts for nylon injection molding requires a thorough understanding of the manufacturing process, material properties, and specific requirements of the application. Careful consideration of these design factors can help ensure that the parts produced are of high quality and meet the desired performance characteristics.
-
6.Common Nylon Injection Molding Defects and Solutions
While nylon injection molding is a reliable and efficient manufacturing process, defects can still occur. Here are some common nylon injection molding defects and possible solutions:
- Warping:
Warping occurs when the part experiences uneven cooling, resulting in distortion or bending of the part. The solution to warping is to modify the part design to include more even wall thickness, reduce the cooling time, and use a mold temperature controller to control the cooling of the part. - Sink Marks:
Sink marks occur when the part cools and shrinks unevenly, resulting in a depression on the surface of the part. To avoid sink marks, design parts with uniform wall thickness, adjust the injection molding parameters, and use a mold with a high-quality surface finish. - Flashing:
Flash is the excess material that protrudes from the parting line of the mold. This occurs when the molten material flows into the space between the mold plates or when the mold is not properly clamped. To prevent flashing, inspect the mold and the clamping mechanism, adjust the injection pressure, and ensure that the mold plates are aligned correctly. - Voids:
Voids are air pockets or bubbles trapped inside the part. This can occur when the molten material is not properly pressurized, or when there is inadequate venting in the mold. To avoid voids, ensure that the mold is properly vented, increase injection pressure and injection speed, and use a lower melt viscosity nylon material. - Cracks:
Cracks can occur when the part is subjected to excessive stress, thermal shock, or overfilling the mold. To prevent cracks, select a nylon material with high impact resistance, ensure that the mold is adequately cooled and use an appropriate wall thickness.
Overall, proper design, molding parameter settings, and careful attention to the manufacturing process can help to avoid common nylon injection molding defects.
-
7.Quality Control and Testing in Nylon Injection Molding
Quality control and testing are essential in the nylon injection molding process to ensure that the parts produced meet the required specifications. Here are some testing methods, quality control measures, and troubleshooting techniques for nylon injection molding:
- Testing Methods:
The following are some common testing methods for nylon injection molded parts:
- Tensile strength testing: This measures the maximum amount of force the material can withstand before breaking.
- Flexural strength testing: This measures the amount of force required to bend the material.
- Impact testing: This measures the energy required to break the material under high impact loads.
- Heat deflection testing: This measures the temperature at which the material will begin to deform under load.
- Quality Control Measures:
The following are some quality control measures for nylon injection molding:
- In-process inspection: Inspection during the molding process to detect defects such as flashing, sink marks, and voids.
- Final inspection: Inspection after the parts are molded to check for cosmetic defects such as scratches, discoloration, and warping.
- Statistical Process Control (SPC): Statistical analysis of the molding process data to detect and correct any process variations and prevent defects.
- Calibration of equipment: Regular calibration of the injection molding machine, mold, and other equipment to ensure that the process is producing parts within specification.
- Troubleshooting:
The following are some common troubleshooting techniques for nylon injection molding:
- Adjusting molding parameters such as injection speed, temperature, and pressure to reduce defects.
- Checking the mold for damage or wear and tear, and repairing or replacing it if necessary.
- Modifying the part design to prevent defects such as sink marks, warping, and flashing.
- Inspecting the raw material for quality and consistency before molding.
Overall, proper testing, quality control, and troubleshooting can help to ensure that the nylon injection molding process produces high-quality parts that meet the desired specifications.
-
8.Best Practices for Nylon Injection Molding
To achieve high-quality parts and optimize the production process, here are some best practices for nylon injection molding:
- Choosing the Right Equipment and Materials:
Selecting the right injection molding machine and materials is crucial for achieving consistent and high-quality parts. Consider the following:
- Injection molding machine: Choose a machine with the appropriate tonnage, shot capacity, and injection pressure for the nylon material being used.
- Nylon material: Choose the appropriate type of nylon for the application and ensure it has the right additives and fillers.
- Optimizing the Injection Molding Process:
Optimizing the injection molding process can help reduce defects and improve part quality. Here are some tips:
- Set up the mold and injection molding machine correctly.
- Monitor and adjust the process parameters such as temperature, pressure, injection speed, and cooling time.
- Use process monitoring tools such as Statistical Process Control (SPC) and Process Failure Modes and Effects Analysis (PFMEA) to optimize the process.
- Ensure proper material handling and preparation.
- Regular Maintenance and Inspection:
Proper maintenance and inspection of the injection molding equipment and mold are essential for minimizing downtime and ensuring part quality. Here are some tips:
- Regularly inspect and maintain the injection molding machine and mold, including cleaning, lubrication, and replacing worn components.
- Perform regular calibration of the injection molding machine, temperature controllers, and other equipment.
- Conduct regular inspections of the molded parts to detect any defects and implement corrective actions.
Overall, following these best practices for nylon injection molding can help achieve high-quality, consistent parts, reduce defects, and optimize the production process.
-
9.Conclusion
Nylon injection molding is a versatile and widely used manufacturing process for producing high-quality parts for various industries, including automotive, consumer goods, electrical and electronics, industrial equipment, and medical devices. Choosing the right equipment and materials, optimizing the injection molding process, and regular maintenance and inspection are essential for achieving consistent and high-quality parts.
Recap of Key Points:
- Nylon injection molding is a widely used manufacturing process for producing high-quality parts for various industries.
- Choosing the right equipment and materials, optimizing the injection molding process, and regular maintenance and inspection are essential for achieving consistent and high-quality parts.
- Proper testing, quality control, and troubleshooting are necessary to ensure that the nylon injection molding process produces high-quality parts that meet the desired specifications.
Future of Nylon Injection Molding:
The future of nylon injection molding looks promising, with advancements in materials, technology, and automation. Some future developments include:
- The development of new nylon materials with improved strength, stiffness, and wear resistance.
- Advancements in automation technology to increase production efficiency, reduce waste, and improve quality control.
- The use of simulation and modeling software to optimize the injection molding process and reduce lead times.
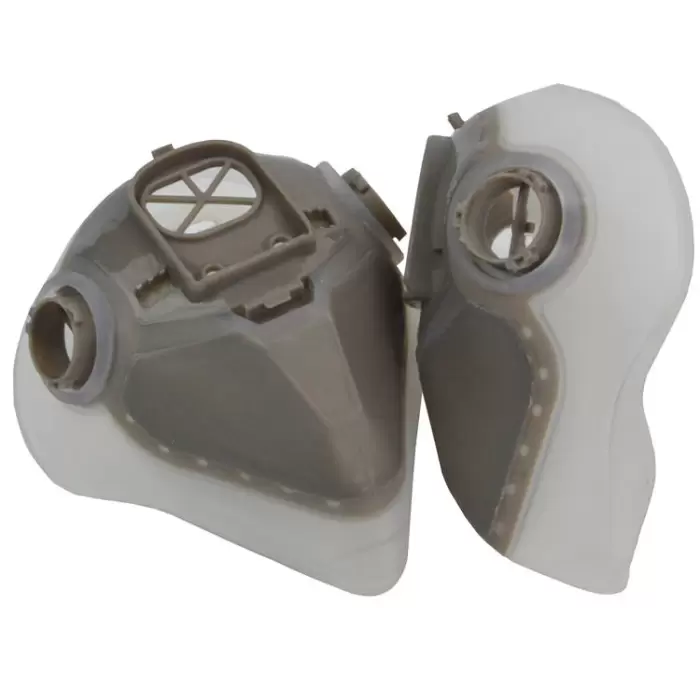