Table of Contents:
- Introduction to Plastic Parts Manufacturing
- Designing the Plastic Parts
- The Manufacturing Process for Plastic Parts
- Preparing for Plastic Parts Manufacturing
- Quality Control of Plastic Parts Manufacturing
- Advancements in Plastic Parts Manufacturing
- Comparison of Plastic Parts Manufacturing Methods
- Common Issues with Plastic Parts Manufacturing
- Conclusion
I. Introduction to Plastic Parts Manufacturing:
The use of plastic parts has become widespread across various industries. The ability to manufacture customized plastic parts to a high degree of accuracy makes them the preferred choice in manufacturing processes. This article will provide an in-depth guide to the processes involved in the manufacturing of plastic parts, the advantages of plastic parts, and best practices for manufacturing.
Overview of Plastic Parts:
Plastic parts can be a broad range of products or components made entirely of plastic or plastic components integrated into a finished product. With the ability to customize plastics, manufacturers can cater to specific requirements of various applications, resulting in the production of unique and distinct products.
Advantages of Using Plastic Parts:
Plastic parts offer several advantages in manufacturing, including low cost of production, ease of manufacturing, flexibility in design, and environmental friendliness due to the recyclable nature of plastics.
-
2. Designing the Plastic Parts:
Factors to Consider in Plastic Parts Design:
Designing plastic parts requires a specific approach that considers not only the final appearance of the parts but also the manufacturing process required to produce the finished product. Factors such as the material used, part features (gates, runners, vents), and thickness must be considered for a successful design.
Design for Moldability:
A fundamental principle of designing plastic parts is designing for moldability, which means creating a design that can be easily produced by the specified plastic manufacturing method.
-
3. The Manufacturing Process for Plastic Parts:
Injection molding is the most common and versatile method of manufacturing plastic parts. It involves melting plastic pellets and injecting them under high pressure into a mold, where they cool and harden into the desired shape.
Blow Molding:
Blow molding is a manufacturing process used to create hollow parts, such as water bottles or containers. The process involves melting polymer pellets and blowing them into a hollow mold.
Rotational Molding:
Rotational molding is a manufacturing process that produces hollow parts using a heated hollow mold rotating on its axis. The plastic is introduced into the mold and heated until it melts and takes the shape of the mold.
Thermoforming:
Thermoforming is a plastic manufacturing process that involves heating a plastic sheet to a pliable temperature and then forming and trimming it into a desired shape using a mold.
-
4. Preparing for Plastic Parts Manufacturing:
Creating the Mold:
A mold is a critical component in plastic parts manufacturing as it determines the final part’s shape and quality. The mold’s design must be optimized and approved before proceeding to the manufacturing process.
Choosing the Proper Plastics:
Plastics, which are used to manufacture the final product, must meet specific requirements such as durability, cost-effectiveness, and aesthetics. Factors such as environmental conditions and product lifespan must be considered while selecting the plastic material.
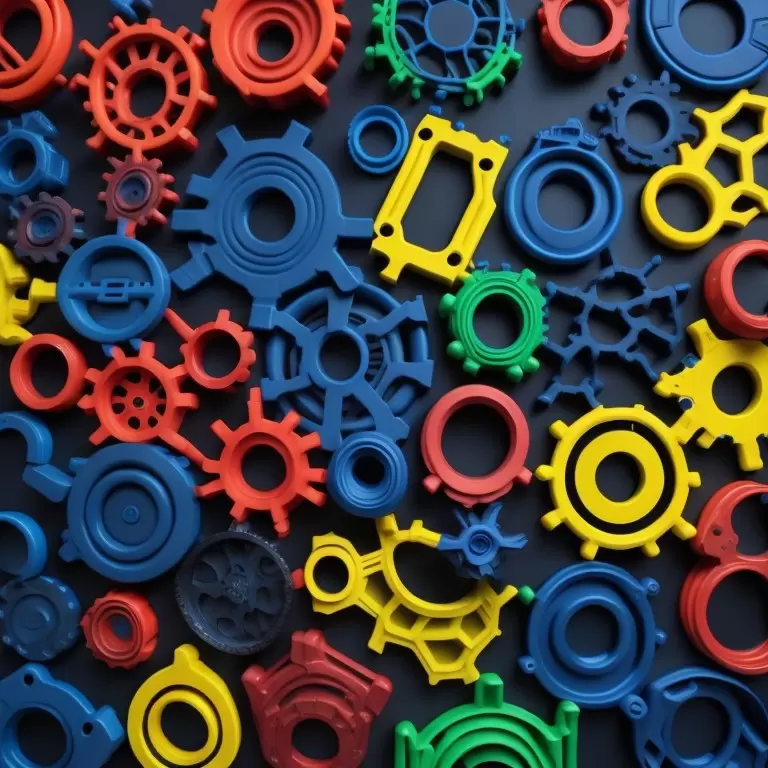
-
5. Quality Control of Plastic Parts Manufacturing:
Ensuring Consistency:
Quality control is a critical component of plastic parts manufacturing, and all products must pass stringent quality assurance before being released to the market. Quality control includes ensuring consistency in product quality and identifying inconsistencies in design and production.
Checking and Inspecting the Parts:
Plastic parts need to be checked for any defects, which may result from the manufacturing process. Inspection techniques such as visual inspections or non-destructive testing are used to ensure the parts are of high quality.
-
6. Advancements in Plastic Parts Manufacturing:
The Role of Technology:
Advancements in technology have led to improvements in plastic parts manufacturing, such as high-speed machines, automated inspection systems, and computer-aided design software. Moreover, the development of sustainable plastics, such as bioplastics, is a significant advance in the industry.
The Future of Plastic Parts Manufacturing:
The future of plastic parts manufacturing will continue to see the integration of technology in the design and production process. Consumers are increasingly seeking environmentally-friendly and sustainable products, and manufacturers must pivot their focus to meet these demands.
If you need about Plastic Parts or Plastic Injection Molding Services,You can click on the V1 Prototype website to find it.
-
7. Comparison of Plastic Parts Manufacturing Methods:
Comparison of Injection Molding Vs Blow Molding:
Injection molding is a suitable method for producing a range of plastic parts, while blow molding is limited to creating hollow plastic parts. Injection molding is often used for the production of small parts, while blow molding is used for larger products.
Comparison of Rotational Molding Vs Thermoforming:
Rotational molding is ideally for manufacturing large and complex hollow plastic parts, while thermoforming is best suited for smaller parts, such as packaging materials.
-
8. Common Issues with Plastics Parts Manufacturing:
Warping, Defects, and Cracking:
Common issues in plastic parts manufacturing include warping or distortion, which can occur due to the quality of the mold and improper temperature control. Defects can also result from improper injection molding processes or poor design.
Causes and Solutions:
These issues can be mitigated by addressing the root cause, such as improving the design or optimizing temperature and pressure controls in the molding process.
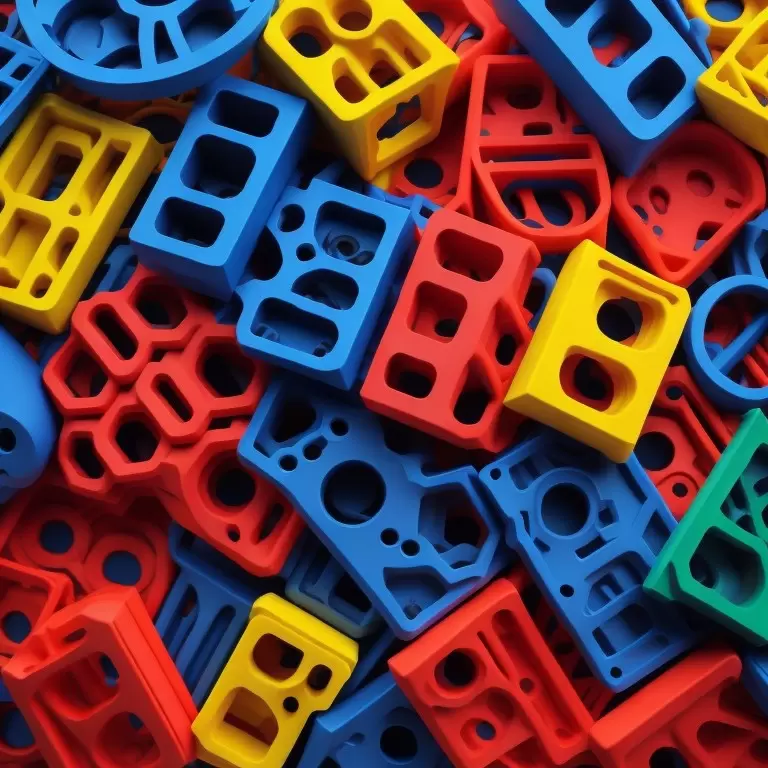
-
9. Conclusion:
The production of plastic parts requires attention to detail, adherence to best practices, and the use of technology in all aspects of the process. Combining these elements with a commitment to sustainability and quality produces high-quality plastic parts that meet industry demands while also reducing production costs. Manufacturers must prioritize design for moldability to ensure successful production and minimize defects. Ongoing advancements in technology, such as 3D printing, automation, and robotics, are revolutionizing the industry and its processes. The trend towards sustainable and environmentally-friendly plastics is driving new developments in materials and processes, showing a promising future for the industry. As the demand for plastic parts continues to rise across various industries, manufacturers must remain agile and innovative to remain competitive in the market. By following best practices and leveraging the latest technology, plastic parts manufacturers can produce high-quality products that meet industry standards while achieving cost and sustainability goals.