Table of Contents:
- Introduction to Casting Materials
- The Casting Process
- Types of Casting
- Advanced Techniques in Casting
- Casting Materials Applications
- Advantages and Disadvantages of Casting Materials
- Safety Considerations for Casting Materials
- Future of Casting Materials
- Conclusion and Resources
-
1. Introduction to Casting Materials
Casting is a manufacturing process in which a liquid material is poured into a mold to create a specific shape. There are a variety of casting materials available, each with its own unique properties and distinct advantages. In this guide, we will discuss the various casting materials, the casting process, and their applications.
A. Overview of Casting Materials
Casting materials can range from metals, such as aluminum and steel, to polymers, ceramics, and even concrete. The choice of material depends on the product requirements, such as strength, durability, weight, and cost.
B. Properties of Casting Materials
The properties of casting materials vary, and it is important to choose the right material according to the requirements of the specific application. Properties of casting materials can include strength, ductility, hardness, melting point, and density.
C. Types of Casting Materials
There are various types of casting materials, including metals, polymers, ceramics, and concrete. The most commonly used casting metals include aluminum alloy, brass, iron, and steel. Polymer casting materials include epoxy, polyester, and, silicone.
-
2. The Casting Process
Casting involves several steps, from the initial design to the final product. The casting technique used can vary depending on the material, product design, and quantity required.
A. Design Process
The casting process starts with the design of the product. A 3D model is essential to the process, as it will be used to create the mold and determine the correct amount of material. Software like SolidWorks helps create and optimize accurate designs for casting.
B. Molding Preparation
The mold is an essential part of the casting process. Patterns or molds are created to shape the liquid material into the desired product. Materials like sand, plaster, and rubber can be used to create the molds.
C. Molten Material Preparation
The casting materials are melted and formulated to meet the product requirements. This requires precise temperature control and accurate measurement of the material.
D. Pouring and Solidification
Once the molten material is prepared, it is poured into the mold. During this process, the mold is kept at a specific temperature to ensure the material will solidify correctly.
E. Post-Casting Process
After the material has solidified, the final product must go through a post-casting process. This can include cutting, polishing, or painting. This process can refine the product and improve its properties.
-
3. Types of Casting
There are various casting techniques, depending on the material used and the application requirements. Common techniques include sand casting, die casting, investment casting, continuous casting, and lost foam casting.
A. Sand Casting
Sand casting is the most common method used for casting. It involves creating a mold using sand and a binder, and then pouring molten metal into the mold. Sand casting is relatively inexpensive and offers flexibility in design choices.
B. Die Casting
Die casting is a high-pressure technique designed to create accurate, repeatable parts. It involves creating a mold that is then filled with metal under high pressure. Die casting is used to create complex shapes with tight tolerances.
C. Investment Casting
Investment casting is a complex process that involves creating a wax pattern and then coating it with ceramic. The wax is melted out, and the mold is filled with molten metal. Investment casting allows the creation of intricate shapes and details.
D. Continuous Casting
Continuous casting involves slowly pulling solidified material through a liquid bath, resulting in a continuous length of material. Continuous casting is most often used for metal production.
E. Lost Foam Casting
Lost foam casting is a process in which a foam model is coated with a refractory material before being immersed in molten metal. The foam burns away and the metal fills the cavity left behind. Lost foam casting is used for complex shapes and large quantities.
-
4. Advanced Techniques in Casting
Advanced casting techniques can help optimize the casting process and create high-quality products.
A. Melting Techniques
Melting techniques include induction melting, electric arc melting, and vacuum melting, and are used to create the precise metal or material suitable for casting.
B. Castability and Shrinkage Control
Castability and shrinkage control are critical to the success of the casting process. Techniques used to manage this include controlled cooling, gating design, and molten metal composition.
C. Cleaning and Finishing
Cleaning and finishing processes include shot blasting, sandblasting, and polishing, and are essential to remove excess material and improve the product’s properties.
D. Ductile Iron Treatment
Ductile iron treatment involves adding nodularizing agents to molten iron to prevent brittle iron formation. This treatment results in a product with improved ductility and toughness.
E. Surface and Heat Treatment
Surface and heat treatments can be used to refine the casting’s properties, such as strength and corrosion resistance. Heat treatment techniques include annealing, quenching, and tempering, while surface treatments include plating and powder coating.
If you need more about other information ,You can click on the V1 Prototype website to find it.
-
5.Casting Materials Applications
Casting materials are used in a wide range of industries, from manufacturing and industry to art and jewelry making.
A. Manufacturing and Industry
Casting materials are frequently used for producing large and complex industrial parts with high accuracy and repeatability. These parts can range from engine blocks to aircraft components.
B. Jewelry and Art
Casting materials are also used for jewelry making and the creation of art objects. These materials allow for the precise creation of delicate and intricate shapes and are often used to cast precious metals and gemstones.
C. Construction and Infrastructure
Casting materials are also used in the construction industry to create unique architectural features and decorative elements. Examples of this include cast concrete facades and ornamental ironwork.
D. Transportation
The transportation industry heavily relies on casting materials, particularly for components used in aircraft and automobiles. Casting materials are valued for their high strength and durability in these applications.
E. Energy and Environment
Casting materials are used in various applications related to energy and environmental sustainability, such as the creation of wind turbine blades and biodegradable plastics.
-
6. Advantages and Disadvantages of Casting Materials
Understanding the advantages and limitations of casting materials is critical to selecting the right material for the job.
A. Strengths of Casting Materials
Casting materials offer several advantages, including the ability to create complex shapes, high accuracy, and the ability to mass-produce identical parts.
B. Limitations of Casting Materials
Limitations of casting materials include high production costs, the potential for porosity formation in the final product, and difficulty in producing thin-walled parts.
C. Comparison to Other Fabrication Techniques
Casting materials are compared to other manufacturing techniques, including forging and machining. In some applications, casting offers advantages in precision, material cost, or scalability.
-
7. Safety Considerations for Casting Materials
Working with casting materials involves potential hazards, including high-temperature environments and the use of heavy machinery. Safety procedures should include protective clothing and equipment, proper material handling, and the implementation of safety protocols.
A. Protective Equipment
Protective equipment, such as heat-resistant gloves and goggles, should be worn to protect workers’ eyes and skin from exposure to high-temperature materials.
B. Material Handling and Storage
Proper handling and storage of casting materials are critical to prevent accidents and maintain quality. Materials should be stored in a dry and well-ventilated area, and guidelines for handling and moving heavy tools and equipment should be followed.
C. Precautions during the Casting Process
Precautions during the casting process should include secure storage and handling of the molten materials, ensuring venting during the casting process, and the implementation of emergency response protocols in the event of accidents or injuries.
D. Waste Disposal and Recycling
Safe disposal of waste materials, including casting sand or broken molds, should be managed to prevent environmental pollution. Efforts to recycle materials can also reduce impacts on the environment.
-
8. Future of Casting Materials
The future of casting materials is likely to involve new materials and technologies that offer greater accuracy, speed, and environmental sustainability.
A. New Developments and Emerging Technologies
New developments in casting technology can lead to improvements in accuracy and speed, such as improved computer simulations, new machining technologies, and the use of robotics in casting.
B. Sustainable Materials and Processes
The casting industry is also moving towards more environmentally-sustainable materials and processes, including the use of recycled materials, biodegradable plastics, and new technologies for reducing energy consumption.
C. Forecast for the Casting Industry
The casting industry is expected to continue to grow in the coming years, driven by demand in the automotive, aerospace, and construction industries, among others.
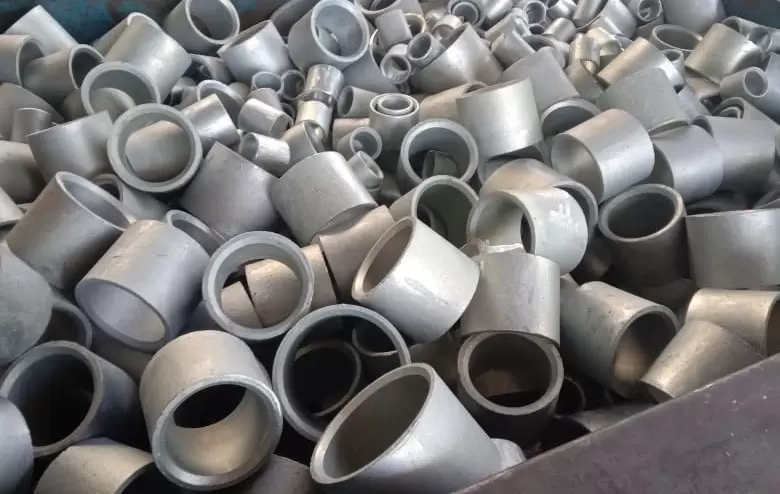
-
9. Conclusion and Resources
Casting materials are a critical component of manufacturing, art, and infrastructure industries. By understanding the casting process, the properties of casting materials, and safety considerations, designers and manufacturers can create accurate, high-quality products. Additional resources for learning about casting materials include industry associations, online forums, and technical publications.