Introduction
Aluminum alloy die casting is a widely used manufacturing process that involves injecting molten aluminum into a mold cavity under high pressure to produce intricate and lightweight metal components. This process offers numerous advantages, making it a popular choice for various industries. In this comprehensive blog post, we will delve into the knowledge of aluminum alloy die casting, its benefits, applications, and the factors that contribute to successful die casting.
The Benefits of Aluminum Alloy Die Casting
Aluminum alloy die casting offers a plethora of benefits that make it a preferred method for producing metal components:
- Lightweight: Aluminum is inherently lightweight, making die-cast aluminum components suitable for applications where weight reduction is critical, such as in the automotive and aerospace industries.
- Excellent Strength: Despite its lightweight nature, aluminum alloys possess excellent strength, providing structural integrity and reliability to the die-cast parts.
- Corrosion Resistance: Aluminum alloys naturally form a protective oxide layer, granting them excellent corrosion resistance, making them ideal for outdoor and marine applications.
- High Thermal Conductivity: Aluminum alloys exhibit high thermal conductivity, allowing for efficient heat dissipation in electronic and heat-sensitive components.
- Precision and Complexity: The die casting process allows for the production of intricate and complex shapes with tight tolerances, meeting the stringent requirements of various industries.
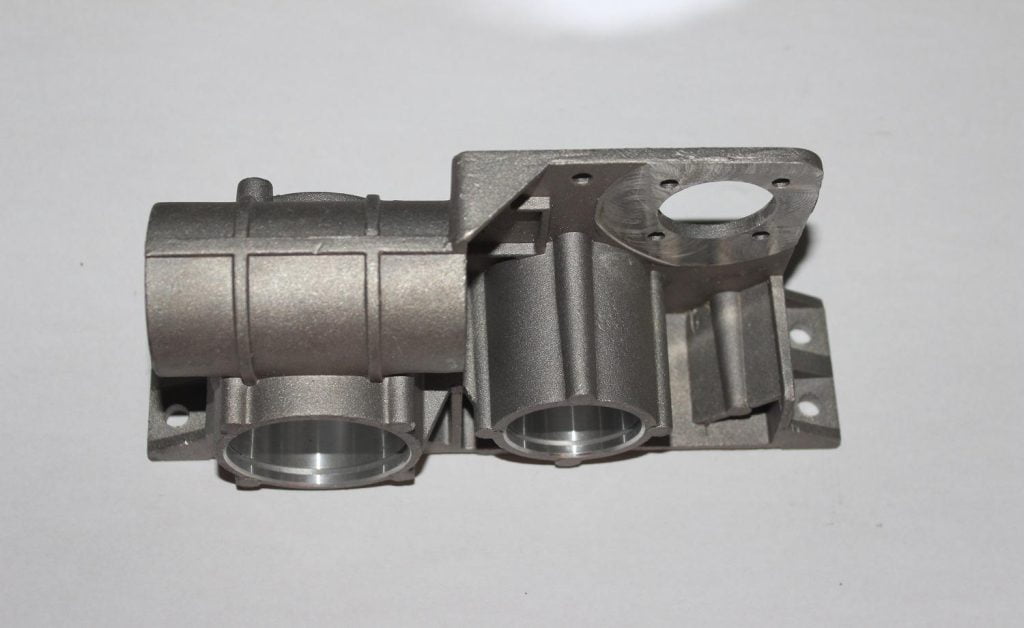
Applications of Aluminum Alloy Die Casting
Aluminum alloy die casting finds applications in a wide range of industries, owing to its versatile properties and cost-effectiveness:
1. Automotive Industry
In the automotive sector, aluminum alloy die casting is widely used for manufacturing components such as engine blocks, transmission cases, and suspension parts. The lightweight and high-strength properties of aluminum alloys contribute to fuel efficiency and improved vehicle performance.
2. Electronics and Electrical Appliances
The electronics and electrical industries utilize aluminum die castings for heat sinks, motor housings, and enclosures. The excellent thermal conductivity of aluminum ensures efficient heat dissipation, enhancing the performance and reliability of electronic devices.
3. Aerospace
In the aerospace industry, aluminum alloy die casting is utilized for producing aircraft components, including wing brackets, hydraulic manifolds, and structural parts. The lightweight nature of aluminum alloys contributes to aircraft fuel efficiency and overall weight reduction.
4. Consumer Goods
Aluminum die castings are commonly found in consumer goods such as laptops, smartphones, and household appliances. The aesthetic appeal, precision, and lightweight properties of aluminum contribute to the popularity of die-cast components in consumer goods.
5. Telecommunications
The telecommunications industry relies on aluminum alloy die castings for producing components like antenna brackets and communication enclosures. The durability and corrosion resistance of aluminum alloys make them suitable for outdoor and harsh environmental conditions.
Factors Influencing Successful Aluminum Alloy Die Casting
Several factors contribute to the success of aluminum alloy die casting:
1. Mold Design
The mold design plays a critical role in the die casting process. Proper mold design ensures uniform filling of the molten aluminum, minimizes the risk of defects, and allows for easy ejection of the finished part.
2. Alloy Selection
The choice of aluminum alloy is essential in achieving the desired properties of the die-cast part. Different aluminum alloys offer varying strengths, corrosion resistance, and other characteristics, allowing manufacturers to tailor the material to specific applications.
3. Temperature Control
Accurate temperature control during the die casting process is crucial to prevent premature solidification and achieve uniform filling of the mold cavity. Proper temperature control ensures high-quality parts with consistent properties.
4. Gating and Venting
Optimal gating and venting designs allow for smooth flow of molten aluminum into the mold cavity and efficient escape of gases during the injection process. This helps minimize defects such as porosity and improve the overall quality of the die-cast parts.
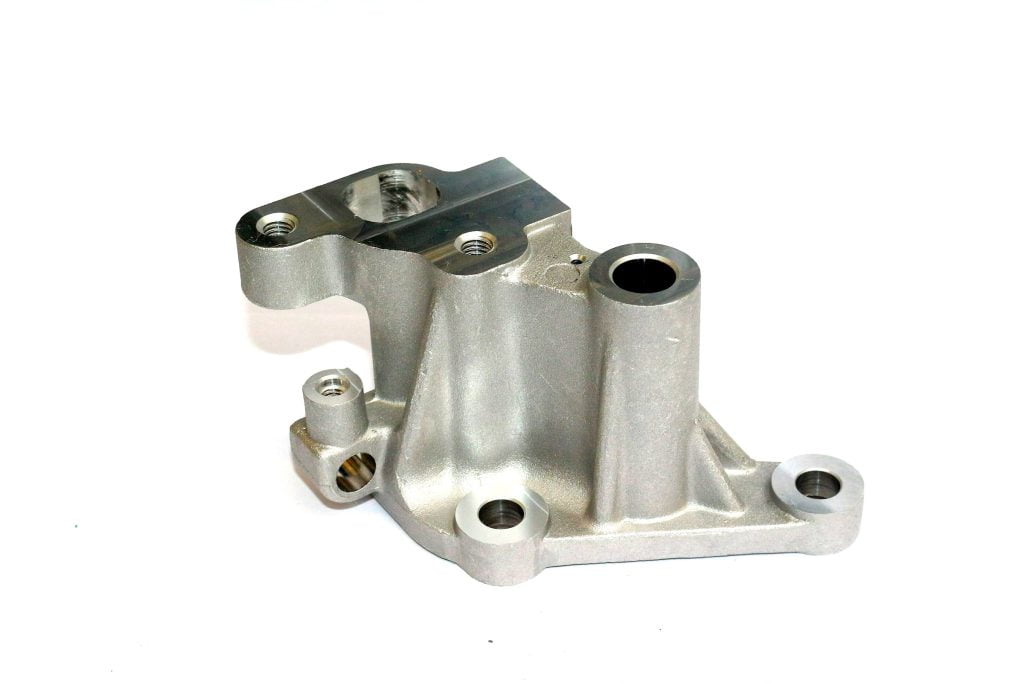
Frequently Asked Questions
Q1. What are the benefits of aluminum alloy die casting?
Aluminum alloy die casting offers several benefits that make it a preferred manufacturing method:
- Lightweight: Aluminum is inherently lightweight, making it ideal for applications where weight reduction is crucial.
- Excellent Strength: Despite its lightweight nature, aluminum alloys exhibit excellent strength, providing structural integrity to the die-cast parts.
- Corrosion Resistance: Aluminum alloys form a protective oxide layer, granting them excellent corrosion resistance, making them suitable for outdoor and marine applications.
- High Thermal Conductivity: The high thermal conductivity of aluminum allows for efficient heat dissipation in electronic and heat-sensitive components.
- Precision and Complexity: The die casting process allows for the production of intricate and complex shapes with tight tolerances, meeting the stringent requirements of various industries.
Q2. What are the applications of aluminum alloy die casting?
Aluminum alloy die casting finds extensive applications in various industries, including:
- Automotive Industry: Engine blocks, transmission cases, and suspension parts.
- Electronics and Electrical Appliances: Heat sinks, motor housings, and enclosures.
- Aerospace: Aircraft components, wing brackets, and hydraulic manifolds.
- Consumer Goods: Laptops, smartphones, and household appliances.
- Telecommunications: Antenna brackets and communication enclosures.
Q3. What factors influence the success of aluminum alloy die casting?
The success of aluminum alloy die casting depends on several factors:
- Mold Design: Proper mold design ensures uniform filling of the molten aluminum and allows for easy ejection of the finished part.
- Alloy Selection: Choosing the right aluminum alloy ensures that the die-cast part possesses the desired properties for its intended application.
- Temperature Control: Accurate temperature control during the die casting process prevents premature solidification and ensures uniform filling of the mold cavity.
- Gating and Venting: Optimal gating and venting designs allow for smooth flow of molten aluminum and efficient escape of gases during injection, minimizing defects.
Q4. How does temperature control impact the die casting process?
Temperature control is a critical aspect of the die casting process. Proper temperature regulation ensures that the molten aluminum maintains its optimal flowability and viscosity during injection. Controlling the temperature prevents premature solidification, which could lead to incomplete fill of the mold cavity and defects in the die-cast part. Additionally, accurate temperature control ensures consistency in the quality and properties of the finished parts, reducing variability and improving the overall efficiency of the die casting process.
Conclusion
Aluminum alloy die casting is a highly versatile and widely used manufacturing process that offers numerous advantages, including lightweight, excellent strength, corrosion resistance, and precise complexity. This process finds applications in various industries, including automotive, electronics, aerospace, consumer goods, and telecommunications. The success of aluminum alloy die casting relies on factors such as mold design, alloy selection, temperature control, and gating and venting designs. By understanding the knowledge of aluminum alloy die casting and employing the best practices, manufacturers can produce high-quality and reliable components that meet the stringent requirements of diverse industries.