Table of Contents:
- Introduction
- Tools and Materials for Sheet Metal Folding
- Techniques for Sheet Metal Folding
- Safety Precautions for Sheet Metal Folding
- Applications of Sheet Metal Folding
- Common Sheet Metal Folding Mistakes and How to Avoid Them
- Conclusion
-
1.Introduction
Sheet metal folding is a manufacturing process that involves bending and shaping thin sheets of metal into various shapes and sizes. It is a crucial technique used in many industries such as automotive, construction, HVAC, and aerospace.
The importance of sheet metal folding in manufacturing lies in its ability to create complex and precise shapes with high accuracy and efficiency. It also allows for the production of parts that are lightweight yet strong, making it ideal for applications where weight reduction is critical. Sheet metal folding is an essential part of the manufacturing process, and its significance cannot be overstated.
-
2.Tools and Materials for Sheet Metal Folding
Sheet metal folding requires specific tools and materials to achieve the desired results. Here are some of the essential tools and materials needed for sheet metal folding:
Types of Sheet Metal:
- Aluminum: Lightweight, corrosion-resistant, and easy to work with.
- Steel: Durable and strong, commonly used in construction and automotive industries.
- Copper: High thermal and electrical conductivity, used in electrical components.
Types of Folding Machines:
- Manual Folding Machines: Used for small scale and basic sheet metal folding, operated by hand.
- Hydraulic Folding Machines: Ideal for medium to large-scale production, powered by hydraulic cylinders.
- CNC Folding Machines: The most advanced and efficient type of folding machine, capable of handling complex and large-scale sheet metal folding.
Other Tools Needed for Sheet Metal Folding:
- Shears: Used for cutting sheet metal into desired shapes and sizes.
- Brake: Used to bend the sheet metal to the desired angle.
- Mallet: Used to tap and bend sheet metal into place.
- Squaring Arm: Used to ensure accurate measurements and angles.
- Protractor: Used to measure angles and ensure precise folding.
-
3.Techniques for Sheet Metal Folding
There are various techniques used in sheet metal folding to achieve different shapes and designs. Here are some of the basic and advanced folding techniques, along with tips for achieving perfect folds:
Basic Folding Techniques:
- Simple Bends: The most basic type of fold, used for creating straight bends in sheet metal.
- Hemming: Used for creating an overlap in sheet metal, commonly used for joining two sheets.
- Box and Pan: Used for creating boxes or containers with sheet metal, involves multiple bends in different directions.
Advanced Folding Techniques:
- Roll Forming: Used for creating curved shapes, involves feeding the sheet metal through rollers to gradually form the desired shape.
- Air Bending: Used for creating bends at different angles, involves using a brake with adjustable fingers to achieve the desired angle.
- Rotary Bending: Used for creating complex shapes, involves using a rotating tool to bend the sheet metal to the desired shape.
Tips for Achieving Perfect Folds:
- Use the right tool for the job, ensure that the tool is appropriate for the thickness and type of sheet metal being used.
- Use accurate measurements and markings to ensure precision in the folding process.
- Take care when handling the sheet metal, avoiding scratches or damage that could affect the final result.
- Practice good technique, such as using the correct amount of force and maintaining consistent pressure throughout the fold.
- Make sure the sheet metal is properly clamped or held in place during the folding process to avoid movement or slippage.
-
4.Safety Precautions for Sheet Metal Folding
Sheet metal folding can be hazardous if proper safety precautions are not taken. Here are some of the common hazards and protective gear required for sheet metal folding:
Common Hazards in Sheet Metal Folding:
- Cuts and Lacerations: Sharp edges and tools used in sheet metal folding can cause cuts or lacerations.
- Pinch Points: The folding machine or brake can trap fingers or other body parts, causing injury.
- Eye Injuries: Small particles or debris from sheet metal can fly into the eyes, causing injury or damage.
Protective Gear Required for Sheet Metal Folding:
- Safety Glasses or Goggles: Required to protect eyes from debris or particles.
- Gloves: Required to protect hands from cuts and lacerations.
- Ear Plugs: Recommended for workers who operate noisy folding machines for extended periods.
- Protective Clothing: Long-sleeved shirts, pants, and closed-toe shoes are recommended to protect skin from sharp edges and debris.
- Respirator Masks: Recommended when working with certain types of sheet metal that produce harmful fumes or dust.
It is important to always follow proper safety procedures and use the appropriate protective gear when working with sheet metal.
-
5.Applications of Sheet Metal Folding
Sheet metal folding has a wide range of applications across various industries. Here are some of the industries where sheet metal folding is commonly used:
Automotive Industry:Sheet metal folding is extensively used in the automotive industry to create various components such as body panels, doors, hoods, and trunks. The ability to create precise and lightweight parts using sheet metal folding has made it an essential process in the manufacturing of automobiles.
Construction Industry:Sheet metal folding is used in the construction industry for various applications, including roofing, cladding, and facades. Sheet metal is folded into different shapes and sizes to create durable and weather-resistant building components that can withstand harsh conditions.
HVAC Industry:Sheet metal folding is used in the HVAC industry to create ductwork, ventilation systems, and other components. The precise and efficient nature of sheet metal folding makes it an ideal process for creating complex and accurate shapes needed in HVAC systems.
Aerospace Industry:Sheet metal folding is extensively used in the aerospace industry to create aircraft components such as wings, fuselages, and engine parts. The lightweight and strong nature of sheet metal make it an ideal material for aerospace applications, and the precise folding techniques used in sheet metal folding allow for complex and intricate designs to be achieved.
If you need about Sheet Metal Services,You can click on the V1 Prototype website to find it:Custom Sheet Metal Parts And Assemblies In As Fast As 1 Day. Get An Online Quote Today.
-
6.Common Sheet Metal Folding Mistakes and How to Avoid Them
While sheet metal folding is a precise and efficient process, mistakes can happen that can lead to defects or errors in the final product. Here are some of the most common sheet metal folding mistakes and how to avoid them:
Overbending:Overbending occurs when the sheet metal is bent past the desired angle, leading to a part that is either too sharp or too large. To avoid overbending, ensure that the folding machine is set to the correct angle and that the sheet metal is positioned properly.
Underbending:Underbending occurs when the sheet metal is not bent enough, leading to a part that is too flat or too small. To avoid underbending, ensure that the folding machine is set to the correct angle and that the sheet metal is positioned properly. Applying more pressure during the folding process may also help to achieve the desired angle.
Incorrect Folding Sequence:Incorrect folding sequence occurs when the sheet metal is folded in the wrong order, leading to a part that does not fit together properly. To avoid incorrect folding sequence, create a folding sequence plan before starting the folding process and double-check the plan to ensure that the correct sequence is being followed.
Other common mistakes in sheet metal folding include using the wrong tool for the job, using the wrong type of sheet metal, or not taking proper safety precautions. By taking care to avoid these mistakes and following proper folding techniques, high-quality sheet metal parts can be produced consistently and efficiently.
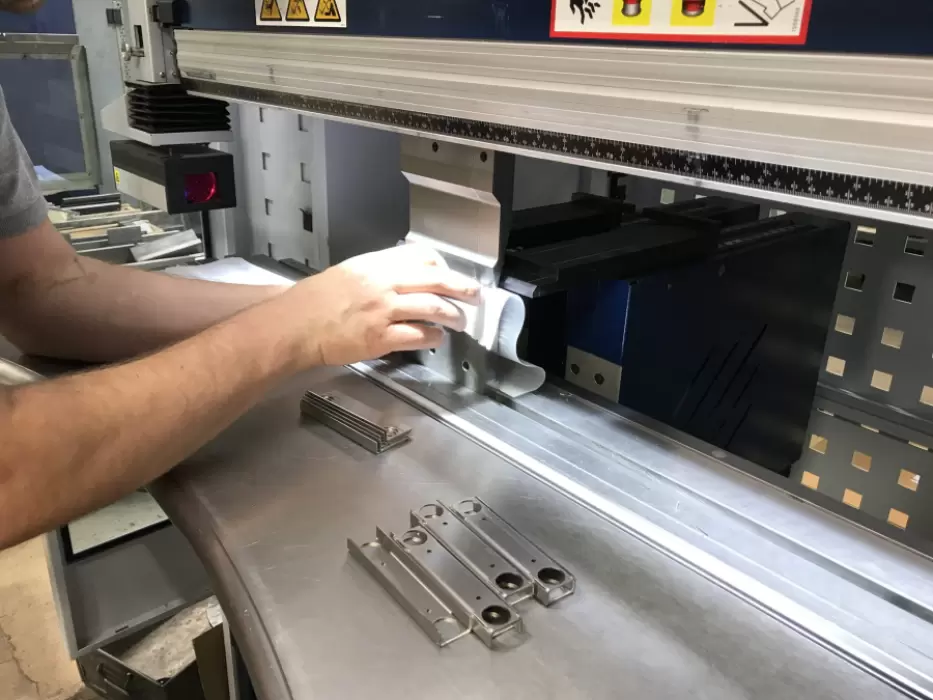
-
7.Conclusion
In conclusion, sheet metal folding is an essential process in various industries, including automotive, construction, HVAC, and aerospace. The ability to create precise and complex shapes using sheet metal folding has made it an important aspect of manufacturing processes, allowing for the creation of durable and lightweight components.
The future of sheet metal folding techniques is promising, with advances in technology and automation making the process more efficient and accurate. As manufacturing processes continue to evolve, sheet metal folding techniques will undoubtedly play an important role in meeting the demands of various industries.
In conclusion, the importance of sheet metal folding in various industries cannot be overstated, and the future of the process looks bright. By following proper techniques and safety procedures, high-quality sheet metal parts can be produced consistently and efficiently, contributing to the growth and development of various industries.