sheet metal services
Custom sheet metal parts and assemblies in as fast as 1 day. Get an online quote today.
Sheet Metal Products
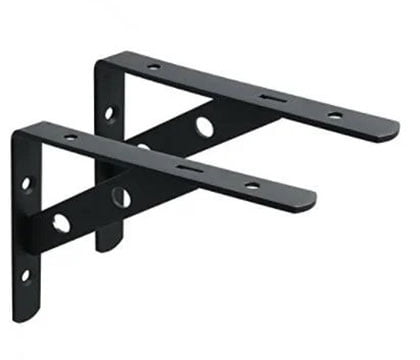
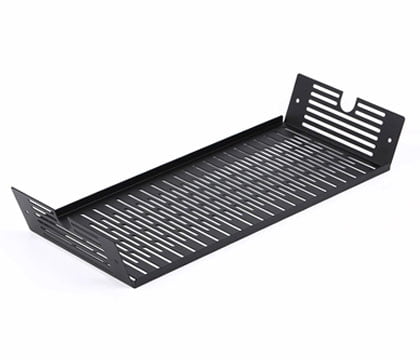
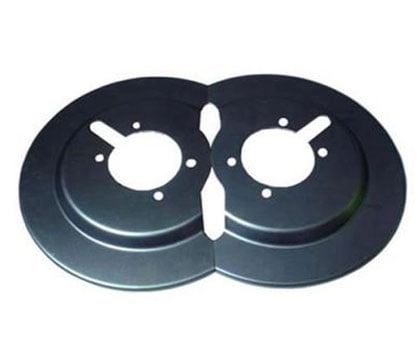
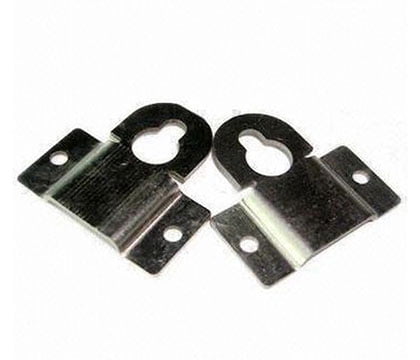
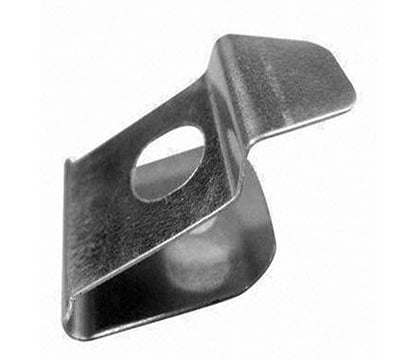
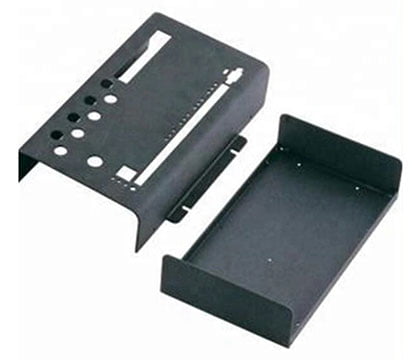
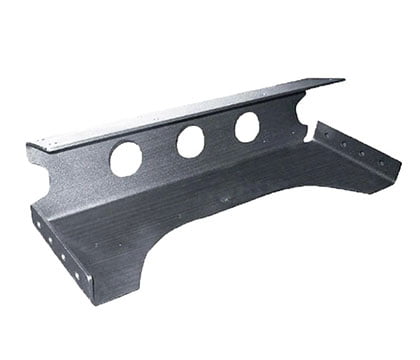
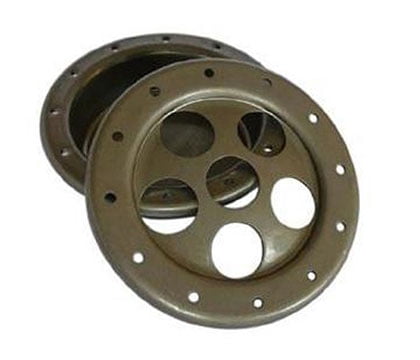
Sheet Metal Fabrication services
Sheet metal fabrication involves slicing, punching, bending, and assembling flat steel or aluminium sheets into metal structures or items. Cutting and burning sheet metal into almost any form allows the machine to slice, fold, or stretch it into virtually any shape.
Stainless steel, aluminum, zinc, and copper are common sheet metals, with gauges ranging from 0.006 to 0.25 inches (0.015 to 0.635 centimetres) thick. Thick gauges are better appropriate for heavy-duty components with demanding applications, whereas thinner gauges are more flexible.
Sheet metal manufacturing may also make use of specialized equipment like band saws and chop saws. This process guarantees that the machine does the cutting evenly throughout the procedure. Cutting torches can quickly and efficiently cut vast pieces of sheet metal.
Technology made sheet metal fabrications easier by employing press brakes, which aid in creating sharp curves and angles in the metal. There are several distinct types of press brakes, each with its own set of functions and applications.
Welding is another essential aspect of sheet metal manufacturing. After it has produced all of the components, combines them and tack welds in place. Manufacturers may employ a variety of welding methods to avoid warping or other irregularities in sheet metal production. These methods include sanding the metal during the cooling phase, a unique straightening procedure, staggered welding, and the use of a strong fixture.
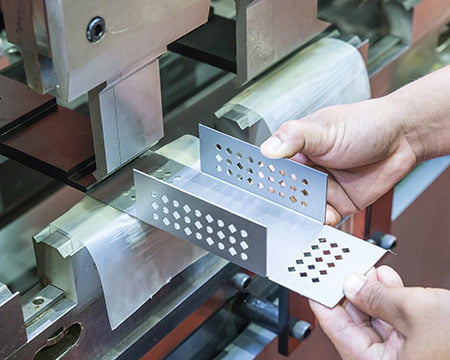
Sheet Metal Fabrication Process
V1 engineers will identify the shape, size, appearance and material based on product performance as required. Take mould production in priority, then focus on cutting-easy, bend, weld, assemble and delivery etc.
Cutting sheet metal is one of the three primary methods of manipulating sheet metals. You may call sheet metal fabrication, like CNC manufacturing, a subtractive manufacturing technique since it can create useable components by merely removing portions of the material.
You may cut sheet metal using various machines, some of which are specific to sheet metal production.
Laser cutting is one of the most important techniques for cutting sheet metal. A laser cutter works by focusing an intense laser via a lens. Although it may struggle with the most challenging materials, it’s a precise and energy-efficient machine that works well with thin and medium sheet metal gauges.
Water jet cutting is another option for sheet metal cutting. This cutting method is a sheet metal manufacturing technique that involves cutting the metal using a high-pressure water jet. Water jet cutters are ideal for cutting sheet metals with low melting points since they do not produce heat that might cause the metal to distort.
Plasma cutting is a third alternative for sheet metal cutting. A plasma cutter creates a hot plasma jet that quickly penetrates even thick gauges of metal sheets by creating an electrical channel of ionized gas.
Sheet metal deformation is another vital area of sheet metal manufacturing techniques. This category of techniques includes various methods for changing and manipulating sheet metal without cutting it.
Sheet metal bending is one of the most common deformation techniques. A sheet metal business can bend sheet metal into V forms, U shapes, and channels up to 120 degrees using a brake machine. Sheet metal with a thinner gauge is simpler to bend. Decambering allows sheet metal producers to eliminate the horizontal curve from strip-shaped pieces of sheet metal.
Stamping is a kind of deformation that you may look at as a subcategory of its own. It includes using a hydraulic or mechanical stamping press with a tool and die, and it works similarly to punching, but it doesn’t permanently remove the material. Curling, sketching, embossing, flanging, and hemming are all activities you may accomplish using stamping.
Correct expended lofting is the important process of sheet metal products, and also decides the final quality of product.Sheet metal programming should consider easy-making, low cost, fast speed and high precision, so as to improve high efficiency and quality.
V1 sheet metal baiting main methods are laser cut, water cut, plasma cut, CNC mechanical machine, punch and shear etc.
The study forms sheet metal in two ways: cutting and deformation. Assembly is a third option, which you do with or without the use of conventional fasteners.
The assembling of diverse components of sheet metal parts using fasteners such as bolts, screws, and rivets is an essential element of the entire manufacturing process, even though the study usually doesn’t consider it a fabrication process. You may use other sheet metal manufacturing techniques, such as punching,
Welding is a method of joining sheet metal components together in which the technique uses heat to melt a portion of the metal where it connects with another element. The two components’ molten metal fused to create a solid connection. Weldability is excellent in common sheet metals like stainless steel and aluminium, but various metals may weld better with different kinds of welding: arc, electron beam, resistance, and so on.
Metal plate bending and forming is made by bending machine and related bending mould, it has fixed bending sequence, the principle is bending the area firstly which not interfere with the next cut, and the area with interference next, the minimum bending radius is the function of the ductility and thickness of the forming metal.
Pressing rivet is forming a non-removable connector by riveting two objects.We main use squeeze riveter combining frock clamp to make nuts, screws and bolts completely pressed or implanted in workpiece, and can assure the fastness, perpendicularity and flatness of the product.
Sheet metal weld is a technique that achieve permanent connection via partial heating or making welded parts permanent plastic deformation. The commonly used welding methods are: manual arc welding, gas shielded arc welding, laser welding, tack and contact welding. GREFEE main adopt gas shielded arc welding.
The fabrication service may finish the product once it completes the fabrication procedure. This process usually entails polishing surfaces and edges and adds different coatings, such as powder coating.
Metal finishing is the process of applying a coating to a material to enhance its look or durability. Surface finishing is the removal of a layer from a material to improve its functioning or appearance.
Various kinds of metal fabrication finishing exist in this study. One of the most popular is anodizing, an electrochemical procedure that forms a coating of oxide on the surface of a metal component to improve its corrosion resistance. Another word to consider is metal plating, an exterior covering for a different kind of metal.
Similarly, in the industry, blackening and or coating are popular metal fabrication finishing techniques. In addition, surface finishing terminology like deburring and graining are essential in metal fabrication finishing.
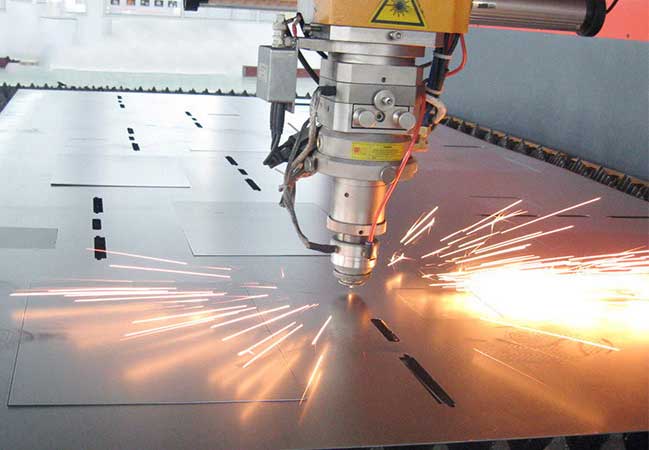
Why Choose V1 Company for Sheet Metal Parts?
- Fast and Simple Quoting Our engnieer offers an average one-day upload-to-quote lead time. Easily configure part specifications like material selection, and finishing options.
- Reliable DeliveryQuality parts delivered within our five-day standard lead time.
- Expansive CapacityWith more than 200 machines all under one roof, we’re dedicated to continuously evolving our capabilities.
- Sheet Metal Technical ExpertiseWork with our team of engineering experts that offer technical design guidance and can inform you on manufacturability and cost-saving opportunities.