Selective laser sintering (SLS) is a groundbreaking additive manufacturing technology that has revolutionized product design and manufacturing. This article delves into the intricacies of SLS, discussing its working principle, materials used, and the diverse applications it has in various industries. Discover how SLS is shaping the future of manufacturing, pushing boundaries in design freedom, material properties, and production efficiency.
I. Introduction to Selective Laser Sintering (SLS)
The Landscape of SLS Technology
Selective Laser Sintering (SLS) emerges as a transformative force in the realm of additive manufacturing, reshaping the way we conceptualize and produce three-dimensional objects. This groundbreaking technology, born out of the marriage between precision engineering and digital design, epitomizes the evolution of manufacturing processes. Unlike its traditional counterparts, SLS operates on an additive principle, constructing objects layer by layer, offering unparalleled design possibilities and manufacturing flexibility.
Unraveling the Mechanism: Principles of Operation
At its essence, SLS relies on a precise interplay of laser technology and powdered materials. The process unfolds with a laser selectively fusing powdered materials layer by layer, guided by a digital 3D model. This bed of powder, comprising polymers, ceramics, or metals, acts as the raw material canvas for the intricate construction that follows. As each layer solidifies under the laser's meticulous touch, a new layer of powder is laid down, continuing the symphony of creation until the final object takes shape.
The Evolutionary Journey of SLS
From its nascent stages as a prototyping tool to its current stature as a cornerstone of additive manufacturing, the journey of SLS is a testament to human ingenuity. Over the years, advancements in laser technology, material sciences, and process optimization have catapulted SLS from a specialized tool to a versatile and widely adopted method across diverse industries. Its ability to traverse the realms of prototyping to end-use production showcases the technology's adaptive prowess and enduring relevance.
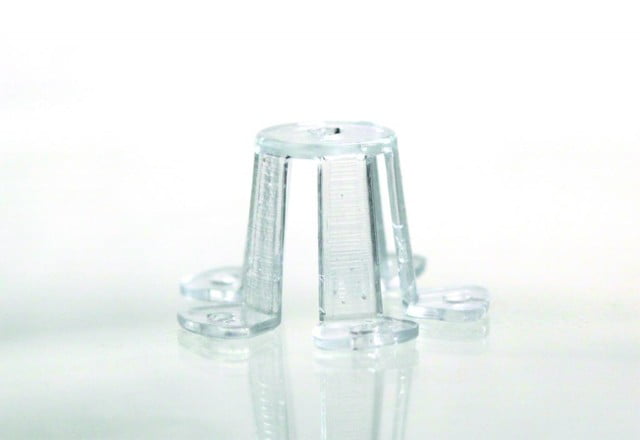
II. Materials for Selective Laser Sintering
Polymers: The Cornerstone of SLS
Polymeric materials, particularly thermoplastics like nylon and polyamide, form the bedrock of SLS. This class of materials strikes a delicate balance between strength, flexibility, and cost-effectiveness. The ability to selectively sinter polymers has ushered in an era of rapid prototyping, where intricate designs and functional parts are brought to life with unprecedented speed.
Pioneering with Ceramics
The integration of ceramics into the SLS repertoire marks a significant expansion of its capabilities. Ceramics, with their exceptional strength, durability, and resistance to high temperatures, find applications in electronics, aerospace, and the medical field. The ability of SLS to navigate the complexities of ceramic sintering opens new avenues for high-performance applications.
Metal Mastery in SLS
Metal SLS represents a pinnacle in additive manufacturing, allowing the construction of components from metals such as aluminum, titanium, and stainless steel. This development propels SLS into the heart of high-performance engineering, where the technology's precision and adaptability give rise to customized metal components with intricate geometries.
Hybrid Materials: A Symphony of Possibilities
The marriage of polymers with reinforcing elements, such as fibers or nanoparticles, exemplifies the versatility of SLS. These hybrid materials elevate the properties of the end product, offering a wider spectrum of applications and performance characteristics. The synergy between different material components in SLS presents a rich canvas for innovation and exploration.
Navigating Material Properties
Central to the success of SLS applications is a nuanced understanding of material properties. Thermal conductivity, mechanical strength, and chemical resistance become pivotal considerations in the material selection process. As SLS delves into diverse applications, from aerospace to healthcare, material properties take center stage in ensuring the functionality and reliability of the final products.
III. Applications of Selective Laser Sintering (SLS)
Crafting the Future with Functional Prototyping
The realm of functional prototyping has undergone a revolution with the advent of SLS. Engineers and designers now have a dynamic tool at their disposal, allowing them to iterate and refine concepts at an unprecedented pace. SLS's unique ability to produce complex geometries with high precision serves as a catalyst for accelerating product development cycles.
Beyond Prototyping: Direct Manufacturing Unleashed
The evolution of SLS from a prototyping tool to a direct manufacturing powerhouse marks a paradigm shift. Now, finished products emerge directly from digital designs, transforming the landscape of production. This leap allows for on-demand manufacturing of low-volume, high-complexity components, reducing waste and offering new avenues for customization.
Personalization Redefined
SLS's inherent customization capabilities make it an ideal candidate for crafting personalized products. From consumer goods to medical implants, the technology enables the creation of unique, tailor-made items that align with individual preferences and requirements. The era of mass customization beckons, and SLS stands as a pioneer in this revolution.
Healing with Precision: SLS in Dentistry and Healthcare
In the healthcare sector, SLS has etched its mark by contributing to the creation of patient-specific implants, prosthetics, and dental components. The precision afforded by SLS, coupled with the ability to work with biocompatible materials, positions the technology as an indispensable tool for crafting custom solutions in the medical field.
Taking Flight and Hitting the Road: Aerospace and Automotive Marvels
The aerospace and automotive industries have found a formidable ally in SLS. The technology's prowess in crafting lightweight, high-performance components aligns seamlessly with the demands of these sectors. From intricate structures to reduced material waste, SLS plays a vital role in enhancing efficiency and fuel economy in vehicles and aircraft.
The Academic Canvas: SLS in Education and Research
Beyond industrial applications, SLS has become a vital educational tool, providing students and researchers with a tangible understanding of manufacturing processes. The accessibility of SLS systems in academic institutions fosters exploration and innovation, nurturing the next generation of additive manufacturing experts.
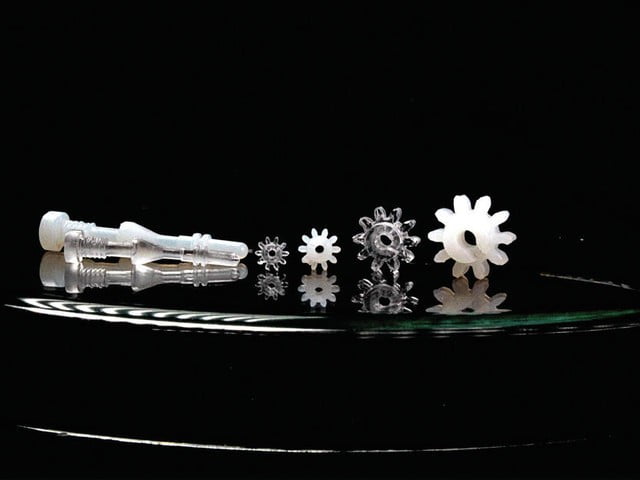
IV. Advantages and Limitations of Selective Laser Sintering (SLS)
Navigating the Maze of Design Complexity
At the forefront of SLS's advantages is its unparalleled ability to handle intricate designs and complex geometries. The layer-by-layer construction method breathes life into shapes that would be challenging or impossible to realize using traditional manufacturing methods. Designers are bestowed with newfound freedom, pushing the boundaries of what is conceivable.
The Efficiency Saga: SLS in Production
SLS emerges as an efficiency maestro, especially when it comes to low-volume, highly customized production runs. By eliminating the need for tooling and consolidating multiple components into a single, complex structure, SLS becomes a champion of time and cost savings. The production landscape witnesses a paradigm shift as SLS flexes its efficiency muscles.
Counting the Coins: Cost Considerations
While the advantages of SLS in design and production are evident, the cost considerations cannot be overlooked. The initial setup costs, particularly for metal SLS, may present challenges for smaller businesses or startups. Navigating the financial terrain requires a delicate balance between the benefits of SLS and the budgetary constraints.
Challenges and Limitations: Navigating the Terrain
No technology is without its challenges, and SLS is no exception. Post-processing requirements, limited material choices for certain applications, and the demand for skilled operators pose hurdles in the widespread adoption of SLS. Understanding and addressing these limitations becomes integral in charting the course for successful SLS applications.
V. Future Developments and Conclusion
Pioneering Tomorrow: Innovations in Materials and Processes
The future of SLS unfolds against the backdrop of continuous innovation in materials and processes. Researchers and engineers delve into uncharted territories, exploring materials with enhanced properties such as strength, conductivity, and biocompatibility. These innovations extend the boundaries of what is achievable with SLS, unlocking new dimensions in additive manufacturing.
Harmonizing Technologies: Integration with Other AM Technologies
As additive manufacturing weaves its intricate web, the integration of SLS with other technologies becomes a natural progression. The synergy with 3D scanning and generative design promises to streamline workflows, creating a seamless bridge from concept to creation. This integration heralds a new era where different additive manufacturing technologies collaborate to amplify their collective potential.
SLS in the Fourth Industrial Revolution: A Central Player
As we stand on the precipice of the Fourth Industrial Revolution, SLS emerges as a central player in the orchestration of change. Its capacity for on-demand, customized production aligns seamlessly with the tenets of Industry 4.0, where digitalization, connectivity, and smart manufacturing converge. SLS stands as a linchpin in reshaping the global manufacturing landscape.
In summation, Selective Laser Sintering transcends its role as a manufacturing technology; it embodies a transformative force driving innovation across industries. From its foundational principles to diverse material applications, SLS stands tall as a symbol of human ingenuity. As we traverse the uncharted territories of additive manufacturing, the journey of SLS continues to unfold, promising a future where the boundaries of creation are defined only by our imagination.