Explore the fascinating world of SLA prototype factory and its impact on modern manufacturing. Discover the benefits, applications, and differences between SLA and SLS prototyping methods. Gain insights into how SLA is transforming the industry and revolutionizing the way products are brought to life.
Table of Contents:
- Introduction
- Understanding SLA Prototype Factory
- 2.1 What is SLA Method for Prototyping?
- 2.2 How Does SLA Work?
- 2.3 Key Advantages of SLA Prototype Factory
- Exploring SLA in Manufacturing
- 3.1 The Role of SLA in the Manufacturing Process
- 3.2 Applications of SLA in Various Industries
- 3.3 Benefits of Using SLA in Manufacturing
- SLA vs. SLS Prototype: A Comparative Analysis
- 4.1 What is SLS Prototype?
- 4.2 Key Differences between SLA and SLS Prototyping Methods
- 4.3 Choosing the Right Prototyping Method
- The Impact of SLA Prototype Factory on the Industry
- 5.1 Accelerating Product Development
- 5.2 Enhancing Design Iterations
- 5.3 Reducing Time-to-Market
- 5.4 Enabling Complex Geometries
- Conclusion
- Frequently Asked Questions
- 7.1 What is SLA method for prototyping?
- 7.2 What is SLA in manufacturing?
- 7.3 What is SLA vs. SLS prototype?
1. Introduction
In the realm of manufacturing, innovation and efficiency play a vital role in the success of any business. To meet the ever-evolving demands of the market, companies need to explore cutting-edge technologies. One such groundbreaking technique is SLA (Stereolithography Apparatus) prototype factory. This article delves into the realm of SLA prototype factory, shedding light on its method, applications, and the advantages it offers over traditional manufacturing processes.
2. Understanding SLA Prototype Factory
2.1 What is SLA Method for Prototyping?
The SLA method for prototyping is a revolutionary technique that uses photosensitive resins and a laser to create three-dimensional (3D) objects with exceptional precision and accuracy. This process involves curing liquid resin layer by layer using an ultraviolet (UV) laser, resulting in a solidified prototype. SLA is highly regarded for its ability to create intricate and complex geometries that traditional manufacturing processes struggle to achieve.
2.2 How Does SLA Work?
SLA begins with a 3D model of the desired object, which is sliced into thin layers by specialized software. The software then communicates with the SLA machine, instructing it to cure each layer of liquid resin. A UV laser traces the pattern of each layer, solidifying the resin and bonding it to the previous layers. This layer-by-layer process continues until the complete object is formed. Once the prototype is ready, it is carefully removed from the liquid resin and subjected to post-processing to enhance its surface finish.
2.3 Key Advantages of SLA Prototype Factory
The SLA prototype factory offers several advantages over conventional manufacturing processes. Firstly, it allows for rapid prototyping, enabling businesses to iterate and refine designs quickly. Additionally, SLA offers high accuracy and resolution, ensuring the production of intricately detailed prototypes. The versatility of SLA allows for the creation of complex geometries and delicate structures that are challenging to achieve using traditional methods. Furthermore, SLA is compatible with a wide range of materials, providing flexibility in material selection for prototypes.
3. Exploring SLA in Manufacturing
3.1 The Role of SLA in the Manufacturing Process
SLA plays a crucial role in the manufacturing process, particularly in the early stages of product development. It allows designers and engineers to validate their concepts and ideas by creating physical prototypes. By having a tangible representation of their designs, they can evaluate the form, fit, and functionality of the product before proceeding to mass production. This iterative process helps identify and address any design flaws or optimization opportunities, ultimately leading to improved final products.
3.2 Applications of SLA in Various Industries
SLA finds applications in a wide range of industries. In the automotive sector, SLA prototypes are used for testing aerodynamics, evaluating the ergonomics of interior components, and verifying the fit of various parts. The medical industry leverages SLA to produce patient-specific anatomical models for surgical planning, dental aligners, and custom prosthetics. Additionally, the consumer electronics industry benefits from SLA by using it to develop functional prototypes for new devices, ensuring they meet user requirements.
3.3 Benefits of Using SLA in Manufacturing
Using SLA in manufacturing processes offers numerous benefits. Firstly, it significantly reduces the time required for prototyping. Traditional manufacturing methods, such as injection molding, involve creating molds, which can be time-consuming. SLA eliminates the need for molds, allowing for rapid production of prototypes. Secondly, SLA enables cost savings by eliminating the need for tooling and reducing material waste. Additionally, the high accuracy and resolution of SLA ensure that the prototypes closely resemble the final product, providing accurate representations for testing and evaluation.
4. SLA vs. SLS Prototype: A Comparative Analysis
4.1 What is SLS Prototype?
SLS (Selective Laser Sintering) is another popular additive manufacturing technique used for prototyping and small-batch production. Unlike SLA, which uses liquid resin, SLS employs powdered materials, typically polymers or metals. During the SLS process, a high-powered laser selectively fuses the powdered material, layer by layer, to create a solid object.
4.2 Key Differences between SLA and SLS Prototyping Methods
While both SLA and SLS are additive manufacturing methods, there are significant differences between them. One major distinction is the materials used. SLA primarily uses liquid resins, while SLS utilizes powdered materials. This difference in materials results in variations in the properties of the final prototypes.
Another difference lies in the post-processing requirements. SLA prototypes often require additional steps, such as washing, curing, and sanding, to achieve the desired surface finish. On the other hand, SLS prototypes typically do not require extensive post-processing, as the powdered material acts as support during the printing process.
4.3 Choosing the Right Prototyping Method
The choice between SLA and SLS depends on various factors. SLA is ideal for producing highly detailed and intricate prototypes with smooth surface finishes. It is particularly suitable for applications that require visual and aesthetic validation. On the other hand, SLS is preferred for functional prototypes that need to withstand mechanical stresses. Additionally, SLS is capable of using a broader range of materials, including engineering-grade thermoplastics and certain metals.
5. The Impact of SLA Prototype Factory on the Industry
5.1 Accelerating Product Development
The advent of SLA prototype factories has revolutionized product development by accelerating the design iteration process. With rapid prototyping capabilities, designers can quickly create and test multiple iterations of their designs. This agility enables faster time-to-market, giving businesses a competitive edge in today's dynamic market.
5.2 Enhancing Design Iterations
SLA prototype factories empower designers and engineersto explore innovative design concepts without the limitations imposed by traditional manufacturing methods. The ability to quickly produce functional prototypes allows for more extensive testing and validation, leading to improved designs and optimized product performance.
5.3 Reducing Time-to-Market
By utilizing SLA prototype factories, manufacturers can significantly reduce the time required to bring a product from concept to market. The rapid turnaround time for prototypes enables faster feedback loops, allowing for prompt design refinements and adjustments. This streamlined process minimizes delays in product development, ultimately leading to quicker commercialization and revenue generation.
5.4 Enabling Complex Geometries
One of the key advantages of SLA prototype factories is their ability to produce complex geometries with high precision. Traditional manufacturing processes often struggle with intricate designs and delicate structures. SLA overcomes these limitations by precisely curing each layer of resin, resulting in intricate details and geometries that would otherwise be challenging to achieve. This capability opens up new possibilities for designers and engineers, enabling the creation of innovative and visually striking products.
6. Conclusion
The emergence of SLA prototype factories has transformed the manufacturing landscape. By leveraging the power of SLA, companies can expedite product development, enhance design iterations, reduce time-to-market, and realize complex geometries. This revolutionary technology offers a cost-effective and efficient solution for creating high-quality prototypes, enabling businesses to stay competitive in today's fast-paced market.
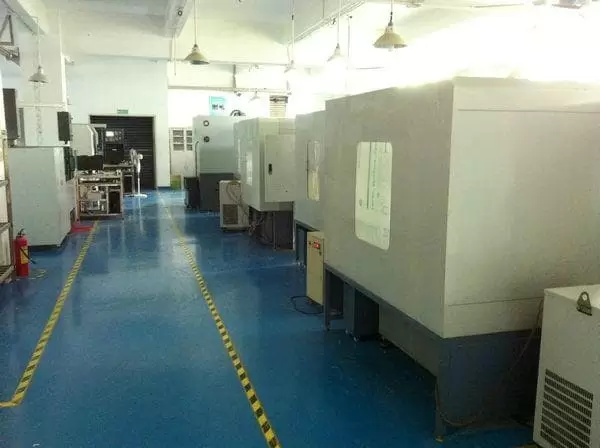
7. Frequently Asked Questions
7.1 What is the SLA method for prototyping?
The SLA method for prototyping is a technique that utilizes photosensitive resins and a laser to create three-dimensional objects with exceptional precision. This process involves curing liquid resin layer by layer using an ultraviolet laser, resulting in a solidified prototype.
7.2 What is SLA in manufacturing?
SLA in manufacturing refers to the application of SLA technology in the production process. It allows manufacturers to create accurate prototypes quickly, evaluate design concepts, and make necessary iterations before moving to mass production.
7.3 What is SLA vs. SLS prototype?
SLA and SLS are both additive manufacturing methods used for prototyping. SLA primarily uses liquid resins and offers high accuracy and intricate details. In contrast, SLS employs powdered materials and is suitable for functional prototypes that can withstand mechanical stresses.
By understanding the nuances between SLA and SLS, manufacturers can choose the appropriate prototyping method based on their specific requirements and objectives.