Table of Contents:
- Introduction
- Applications of Rapid Prototyping in Medical Instruments
- Materials Used in Rapid Prototyping of Medical Instruments
- Rapid Prototyping Techniques used in Medical Instrument Design
- Design Considerations in Rapid Prototyping of Medical Instruments
- Innovations and Advantages of Rapid Prototyping in Medical Instruments Products
- Future of Rapid Prototyping in the Medical Instruments Industry
- Conclusion
-
1.Introduction
Rapid prototyping is a technology used to create physical models and parts directly from digital designs, allowing engineers or designers to quickly fabricate and test their designs. The primary objective is to speed up the design and development process, adapt to changing design requirements, and reduce the costs of the overall product design. It’s an essential component of the design process across several industries, including medical instruments.
-
2.Applications of Rapid Prototyping in Medical Instruments
Rapid prototyping has proven to be a valuable tool in medical instrument development in the following applications:
- Surgical Instruments
Rapid prototyping offers designers and engineers the flexibility to experiment with new designs and concepts before implementing them in actual surgical procedures. It allows medical professionals with the chance to assess the ease of use, durability and cost-effectiveness of new designs. Rapid prototyping in surgical instruments also supports functions like custom grips or imprinting the surgeon’s name on the instrument to improve the handling qualities of surgical instruments during complex procedures. - Implantable Devices
Rapid prototyping techniques are useful in developing customized medical implant devices, such as dental implants, craniomaxillofacial implants and spinal implants. These implants are designed to fit individual patients’ anatomies, more effectively and efficiently than traditional mass-produced implants. Rapid prototyping plays an essential role in reducing the turnaround time, reducing costs, and ensuring that implants have greater accuracy and compatibility with the patient’s anatomy. This ultimately leads to better outcomes in patient recovery. - Wearable Medical Devices
Wearable medical devices are becoming increasingly popular for health monitoring, fitness tracking, and preventative health care. Rapid prototyping plays a crucial role in the production of wearable medical devices. For example, 3D printing has become a common technique used in the development of prosthetics, such as hearing aids, orthotics and even custom-fitting casts. The speed and accuracy provided by rapid prototyping in producing implants and assistive medical devices have revolutionized the healthcare sector.
In conclusion, the utilization of rapid prototyping in surgical instruments, implantable medical devices, and wearable medical devices is increasing in the medical instruments industry, leading to improvements in functionality, accuracy, and reduced costs. Rapid prototyping is vital in driving innovations, precision and development of better medical instrument designs.
-
3.Materials Used in Rapid Prototyping of Medical Instruments
Rapid prototyping in medical instrument design requires the use of materials that are biocompatible and safe for medical use. It is essential to ensure that the material chosen for a specific medical instrument application meets biocompatibility standards, such as ISO 10993 and USFDA 21 CFR Part 820.30. The following are the primary materials used in rapid prototyping of medical instruments:
- Biocompatible Materials
Biocompatible materials used in rapid prototyping of medical instruments have to be safe for human use and selective in their toxicity, degradation, and biostability. Examples of biocompatible materials used in rapid prototyping include Polyether ether ketone (PEEK), Polylactic acid (PLA), Polycarbonate (PC), and titanium alloys. - Materials Suitable for Specific Applications
Different medical instruments require different material properties to achieve their purposes accurately. For instance, materials such as silicone, latex, and urethane typically are used in the production of catheters, syringes or other fluid transfer components. Glass and quartz are essential materials for optical systems, orthopedic instruments use stainless steel or titanium. Depending on the medical instrument’s application, materials with specific energy absorption, density, electromagnetic properties, and mechanical strength may be needed to optimize performance.
In conclusion, rapid prototyping requires the use of different specialized materials that meet the requirements of the medical industry. The material choice depends on the medical instrument design and its intended application. Biocompatible materials, which are tested for biostability and toxicity, are used to ensure patient safety. The specific performance requirements of the instrument also impact the material selection. Material selection requires a carefully considered balance between material properties, clinical applications, and production costs.
-
4.Rapid Prototyping Techniques used in Medical Instrument Design
Rapid prototyping offers several techniques that can be utilized in various medical instrument designs. The following are the widely used rapid prototyping techniques used in medical instrument design:
- Stereolithography (SLA)
Stereolithography is one of the earliest rapid prototyping technologies that uses a light-sensitive polymer to build a 3D object from a digital model file. SLA works by using an ultraviolet (UV) laser beam to cure or harden the liquid resin layer by layer. SLA technique is ideal for creating intricate geometries, such as those found in dental impressions or surgical aids. - Fused Deposition Modeling (FDM)
Fused Deposition Modeling works by melting a thermoplastic material in a nozzle and depositing it layer-by-layer according to a pre-programmed path. This technique is commonly used in developing custom surgical guides or anatomical models. - Selective Laser Sintering (SLS)
Selective Laser Sintering is a technique used in rapid prototyping by using a high-powered laser to fuse a powdered material, typically a plastic or metal polymer. This method is ideal for producing small surgical tools, dental implants, and mechanical parts. - Material Jetting
Material jetting works by jetting small droplets of material that are cured with UV light. This technique has high accuracy and produces parts with a smooth finish. Clinicians use material jetting for developing patient-specific prosthetics, implants, and dental models.
Rapid Prototyping has provided the medical industry with an opportunity to develop unique designs that offer optimal functionality with high accuracy and reduce production time significantly. The application of these technologies has allowed the development of customized surgical tools, patient-specific implants and prosthetics, and wearable medical devices. The choice of the most suitable rapid prototyping technique depends on the specific design requirements and the selected material.
-
5.Design Considerations in Rapid Prototyping of Medical Instruments
Designing a medical instrument using rapid prototyping technologies requires designers to consider several crucial factors to get the desired outcome. The following are the primary considerations for medical instrument design using rapid prototyping methods:
- Geometry & Complexity
Rapid prototyping techniques are suitable for designing and producing highly complex geometries that traditional manufacturing processes may not effectively create. However, in practical applications, intricate or small features might not be clearly visible for medical users or hand-assemble to the actual product, resulting in challenges in achieving the desired outcome. Therefore, Designers should ensure that the geometries of the medical instrument are produced in a way that is clinically relevant and feasible to use. - Functionality and Performance
The primary purpose of a medical instrument is to perform its intended function efficiently and effectively. Performance specifications should be specific on the design requirements and the product’s intended use. User testing and evaluation should be conducted to ensure the instrument performs as intended. - Materials Selection
The material choice for the medical instrument should be biocompatible, durable, and safe for the intended use. Additionally, designers should consider the visual appearance of the material, as it can impact the instrument’s aesthetics. - Surface Finish & Aesthetics
In medical instruments, functionality and aesthetics go hand-in-hand, making the instrument appealing for use in clinical applications. The surface finish of the medical instrument should be smooth and free from any irregularities that could affect its performance or application. The surface finish will depend on the post-processing methods used to refine the design’s intended appearance, as this greatly affects the part aesthetic characteristic.
In conclusion, rapid prototyping of medical instruments provides new opportunities for designers to create complex and customized medical instrument designs. In addition, the design considerations of geometry and complexity, functionality and performance, materials selection, and surface finish and aesthetics must be taken into account to ensure that the final product is clinically relevant, meets the intended performance, and safe to use. Designers should collaborate with manufacturers to ensure that the design iterations and parts can be optimally manufactured and evaluated before mass production.
-
6.Innovations and Advantages of Rapid Prototyping in Medical Instruments Products
The rapid prototyping of medical instruments has brought significant innovations and advantages in medical instrument product development. Here are some of the innovations and benefits:
- Smart Medical Devices
Rapid prototyping has enabled the development of smart medical devices that use digital monitoring technology to detect physiological signals, disease symptoms, or other medical conditions. These devices can store or transmit the data to medical practitioners for human intervention. Rapid prototyping techniques allow for the integration of smart sensors, low-power devices, and small-scale actuators to improve the performance, reliability and accuracy of such medical devices. - Integration of Electronics and Sensors
Rapid prototyping facilitates the integration of electronics and sensors such as MEMS (micro-electro-mechanical systems) into the production of medical instruments. Integration of electronics and sensors is used to create miniaturized components, communication devices, and other systems required for medical instruments development. Electrical and sensor integration in medical instruments usually results in sustained and better performance and offers more accurate outputs. - Emerging Materials and Rapid Prototyping Techniques
Emerging materials are creating new opportunities in rapid prototyping technologies, which include new forms of hydrogels, nanodevices, and advanced biocompatible polymers. The technologies that are emerging regularly can enable new solutions for ongoing health needs, providing better protection and more efficient and effective drug delivery. For instance, 3D printed hydrogel scaffolds have applications in nerve regeneration and wound healing.
In conclusion, the rapid prototyping of medical instruments has ushered in new innovations and advancements in the medical field. Smart medical devices, the integration of electronics and sensors, and emerging materials and rapid prototyping techniques have played a vital role in developing new medical instruments products that are more efficient, reliable, and customized to individual patients’ needs. Rapid prototyping continues to be a significant player in driving the future of medical instrument design and production.
-
7.Future of Rapid Prototyping in the Medical Instruments Industry
Rapid Prototyping is having a profound impact on the medical instruments industry, driving innovations and new solutions for healthcare professionals and patients alike. Here are some emerging trends, technologies, and opportunities that will shape the future of rapid prototyping in the medical instruments industry:
- Trends in Rapid Prototyping for Medical Applications
The trends in medical rapid prototyping are shifting towards customized designs and solutions for personalized devices. 3D printing, combined with other technologies like data acquisition, analysis, and internet-of-things (IoT) technology, has the potential to enable healthcare professionals to develop new and innovative products that meet the specific demands of individual patients or clinical applications. Wearable medical devices, customized implants, and smart medical devices will continue to drive rapid prototyping innovations in the medical industry. - Emerging Technologies and Opportunities
Emerging technologies, such as 4D printing, advanced materials, biomimicry, and artificial intelligence, have opened up new opportunities that will significantly impact the medical instruments industry. Using the combination of these technologies, designers can now produce complex medical instruments that simulate biological structures, including blood vessels, bone structures, nerves, and soft tissues. - New Horizon for Customized Medical Devices
Rapid Prototyping in the medical instruments industry provides new horizons for customized medicine as it enables clinicians to create patient-specific medical devices, implants, and prosthetics accurately, quickly, and efficiently. It allows professionals to fabricate models that replicate the anatomy of the patient, allowing for better understanding and planning before treatment.
In conclusion, the future of rapid prototyping in the medical instruments industry aims to develop personalized medical devices to meet specific patient requirements, using advanced materials, machine learning, and smart sensors. Emerging technologies and opportunities like 4D printing technology will also continue to revolutionize the medical industry, including the design of new ultra-precise and interactive medical devices. The future of rapid prototyping in the medical instruments industry promises to improve the quality and efficiency of the healthcare industry, ultimately improving patient outcomes.
If you want more about Rapid Prototyping In Medical Instruments information,You can click on the V1 Prototype website to find it.
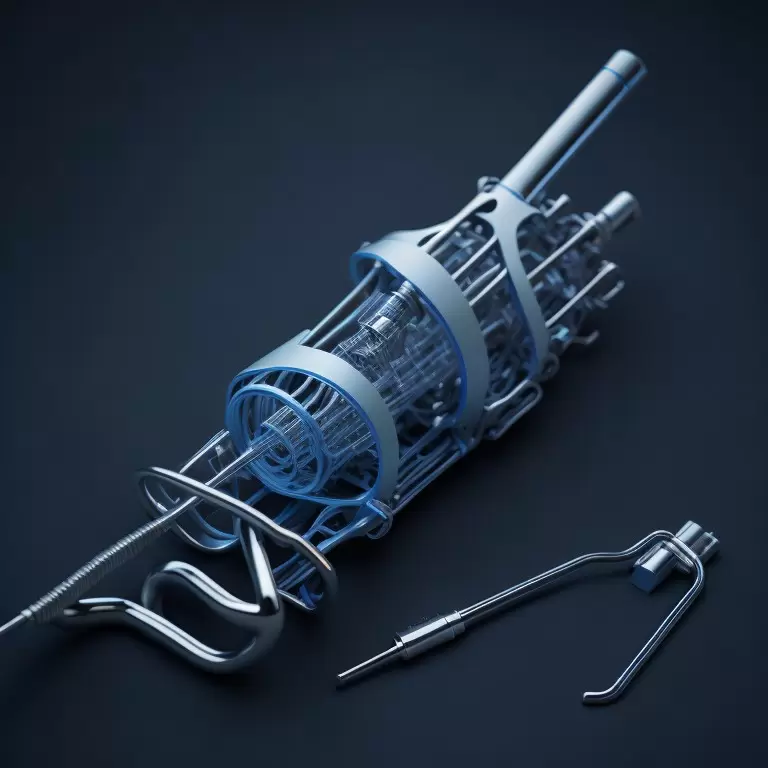
-
8.Conclusion
Rapid prototyping is a revolutionary technology that offers designers efficient, cost-effective, customized, and high-quality product development. In the medical instruments industry, rapid prototyping plays a vital role in developing innovative and effective devices, from wearable medical devices to customized implants and prosthetics. The technology offers several advantages such as improved patient outcomes, reduced development costs, and faster production time, making it an essential tool for medical instrument design and manufacture.
Rapid prototyping plays an essential role in the medical instrument design and manufacture process. It provides a flexible and agile approach to the production of medical devices, which minimizes costs for manufacturers and improves the patient’s experience. The technology enables the medical industry to develop customized devices to meet specific patient requirements, offering the best possible solutions for medical professionals and patients.
The future of rapid prototyping in the medical instruments industry promises to evolve with the development of new technologies such as 4D printing, advanced materials, biomimicry, and artificial intelligence. These technologies will likely continue to revolutionize the medical industry, leading to the design of more advanced medical devices. Future trends will focus on the personalization and customization of medical instruments, meeting the specific needs of individual patients. The medical instruments industry is an exciting field to be in, and the future of rapid prototyping promises innovative and sustainable solutions to the sector’s ongoing challenges.
In conclusion, rapid prototyping is an essential technology that has transformed the medical instruments industry. It has enabled the production of custom-made, functionally advanced, and safe devices that have transformed patient care. With the continuous advancements in technology, it is clear that the medical industry will continue to evolve, and rapid prototyping will remain a critical component of medical instrument design, manufacture, and innovation.