Table of Contents:
- Introduction
- Manufacturing Techniques for Precision Machining Parts
- Materials Used for Precision Machining Parts
- Applications of Precision Machining Parts
- Quality Control and Inspection of Precision Machining Parts
- Advancements in Precision Machining Parts
- Future Outlook for Precision Machining Parts
- Conclusion
-
1.Introduction
Precision machining parts refer to components that are manufactured using various techniques to achieve extremely tight tolerances and high accuracy. These parts are typically used in industries such as aerospace, defense, medical, automotive, and electronics, where quality, reliability, and precision are of utmost importance.
Precision machining techniques involve removing material from a workpiece using specialized tools such as lathes, mills, and grinders to produce parts with precise dimensions and surface finishes. The manufacturing process can be automated using computer-controlled machines, which further enhances accuracy and consistency.
Precision machining parts are critical in many applications, such as in aircraft engines, where even the slightest deviation from specifications can result in catastrophic failure. In the medical industry, precision machining parts are used in surgical instruments, implants, and devices that require high precision and reliability. The importance of precision machining parts cannot be overstated, as they play a vital role in ensuring safety, functionality, and performance in various industrial and commercial applications.
-
2.Manufacturing Techniques for Precision Machining Parts
There are several techniques for precision machining parts, each with its own advantages and applications. Some of the most common techniques include:
- CNC Machining: CNC (Computer Numerical Control) machining involves the use of computer-controlled machines to remove material from a workpiece. The machines can perform a variety of operations, including drilling, milling, and turning, and can produce highly complex shapes with great accuracy and precision.
- Turning: Turning is a process that involves rotating a workpiece against a cutting tool, which removes material to produce a cylindrical shape. This technique is commonly used for producing parts such as shafts, pins, and screws.
- Milling: Milling is a process that involves removing material from a workpiece using a rotating cutting tool. This technique is used to produce parts with complex shapes, such as gears, molds, and turbine blades.
- Drilling: Drilling involves creating holes in a workpiece using a rotating cutting tool. This technique is used to produce holes with precise dimensions and tolerances.
- Grinding: Grinding is a process that involves using an abrasive wheel to remove material from a workpiece. This technique is used to produce parts with very tight tolerances and high surface finishes.
- EDM (Electrical Discharge Machining): EDM involves using a spark to erode material from a workpiece. This technique is commonly used to produce complex shapes with high precision, such as molds and dies.
- Laser Cutting: Laser cutting involves using a laser beam to cut through a workpiece. This technique is used to produce parts with very high precision and accuracy, particularly in applications such as electronics and medical devices.
-
3.Materials Used for Precision Machining Parts
Precision machining parts can be made from a wide range of materials, depending on the specific application requirements. Some of the most commonly used materials include:
- Metals: Metals are among the most commonly used materials in precision machining. Steel, aluminum, and titanium are popular choices due to their strength, durability, and resistance to corrosion. These materials are commonly used in aerospace, defense, and automotive industries.
- Plastics: Plastics are lightweight, versatile, and offer excellent chemical resistance. They are commonly used in medical and electronics industries where non-conductivity and biocompatibility are important.
- Composites: Composites are made up of a combination of materials, such as fibers and resins, and offer excellent strength-to-weight ratios. They are commonly used in aerospace and defense industries for producing lightweight, high-strength components.
Other materials used in precision machining parts include ceramics, glass, and exotic alloys, depending on the specific requirements of the application. The selection of the material depends on factors such as the part’s function, environment, and cost.
-
4.Applications of Precision Machining Parts
Precision machining parts are used in a wide range of industries where high accuracy, reliability, and performance are critical. Some of the most common applications of precision machining parts include:
- Aerospace and Defense: Precision machining parts are widely used in the aerospace and defense industries for producing critical components such as turbine blades, landing gears, and engine parts. These parts must meet stringent specifications and tolerances to ensure safety and reliability.
- Medical: Precision machining parts are used in the medical industry for producing surgical instruments, implants, and devices such as pacemakers and insulin pumps. These parts must be biocompatible, non-reactive, and able to withstand harsh sterilization processes.
- Automotive: Precision machining parts are used in the automotive industry for producing engine components, transmission parts, and other critical systems. These parts must meet stringent quality and safety standards to ensure performance, durability, and reliability.
- Electronics: Precision machining parts are used in the electronics industry for producing components such as connectors, switches, and housings. These parts must be able to withstand harsh environments and meet strict dimensional and electrical specifications.
- Industrial Machinery: Precision machining parts are used in the industrial machinery industry for producing components such as bearings, shafts, and gears. These parts must be able to withstand high loads, extreme temperatures, and harsh operating conditions.
Overall, precision machining parts are essential for many industrial and commercial applications, where high accuracy, reliability, and performance are critical.
-
5.Quality Control and Inspection of Precision Machining Parts
Quality control and inspection are critical aspects of precision machining to ensure that the final product meets the required specifications and tolerances. Some of the most common quality control and inspection techniques used for precision machining parts include:
- Dimensional and Geometric Tolerances: Tolerances are the allowable variation in dimensions or geometry of a part. Tolerances are specified in the design and manufacturing stages and are used to ensure that the parts fit together correctly and function properly.
- Surface Roughness: Surface roughness refers to the texture of a machined surface, which can affect the part’s function and performance. Surface roughness is measured using techniques such as profilometry, and surface roughness testers.
- Non-destructive Testing: Non-destructive testing is used to detect defects or discontinuities in materials without damaging the part. Techniques such as ultrasonic testing, X-ray inspection, and magnetic particle inspection are commonly used for precision machining parts.
Other quality control and inspection techniques used for precision machining parts include hardness testing, material testing, and visual inspection. The specific techniques used depend on the part’s material, application, and requirements.
In conclusion, quality control and inspection are critical aspects of precision machining to ensure that the final product meets the required specifications and tolerances. This helps to ensure that the parts fit together correctly, function properly, and meet the necessary safety and performance requirements.
-
6.Advancements in Precision Machining Parts
The field of precision machining is constantly evolving, with new advancements and technologies being developed to improve accuracy, efficiency, and performance. Some of the most significant advancements in precision machining parts include:
- Additive Manufacturing: Additive manufacturing, also known as 3D printing, is a revolutionary technology that allows for the creation of complex parts with high precision and accuracy. Additive manufacturing enables the production of parts with complex geometries that would be difficult or impossible to achieve using traditional machining methods.
- Automation and Robotics: Automation and robotics are being increasingly integrated into precision machining processes to improve efficiency, speed, and accuracy. These technologies can help to reduce lead times, increase productivity, and improve safety in the manufacturing environment.
- Simulation and Modeling: Simulation and modeling are important tools for optimizing precision machining processes and predicting the behavior of parts under various conditions. These tools can help to identify potential issues and optimize the manufacturing process before the parts are produced.
Other advancements in precision machining parts include the development of new materials, coatings, and surface treatments to improve performance and durability. These advancements are driving innovation and creating new opportunities for precision machining in a wide range of industries.
In conclusion, the advancements in precision machining are providing new opportunities for manufacturers to create complex parts with high accuracy, efficiency, and performance. Additive manufacturing, automation and robotics, and simulation and modeling are just a few examples of the exciting new technologies that are transforming the field of precision machining.
-
7.Future Outlook for Precision Machining Parts
The future outlook for precision machining parts is influenced by a range of market trends, technological developments, opportunities, and challenges. Some of the most significant factors shaping the future of precision machining parts include:
- Market Trends: The demand for precision machining parts is driven by a range of industries, including aerospace, defense, medical, automotive, and electronics. These industries are expected to continue growing, which is likely to drive demand for precision machining parts in the coming years.
- Technological Developments: As technology continues to evolve, precision machining is likely to become increasingly automated and integrated with other manufacturing processes. Advancements in materials science, coatings, and surface treatments are also likely to lead to new opportunities for precision machining parts.
- Opportunities and Challenges: The growing demand for precision machining parts presents significant opportunities for manufacturers. However, there are also challenges to be addressed, such as the shortage of skilled labor and the need to invest in new technologies to remain competitive.
In conclusion, the future outlook for precision machining parts is positive, with strong demand expected to continue across a range of industries. Technological advancements are likely to drive innovation and create new opportunities, while challenges such as the shortage of skilled labor will need to be addressed. Overall, precision machining is likely to remain a critical component of the manufacturing industry, providing high-quality, reliable parts for a range of applications.
Click on the V1 Prototype website to gain more Precision Machining Parts information.
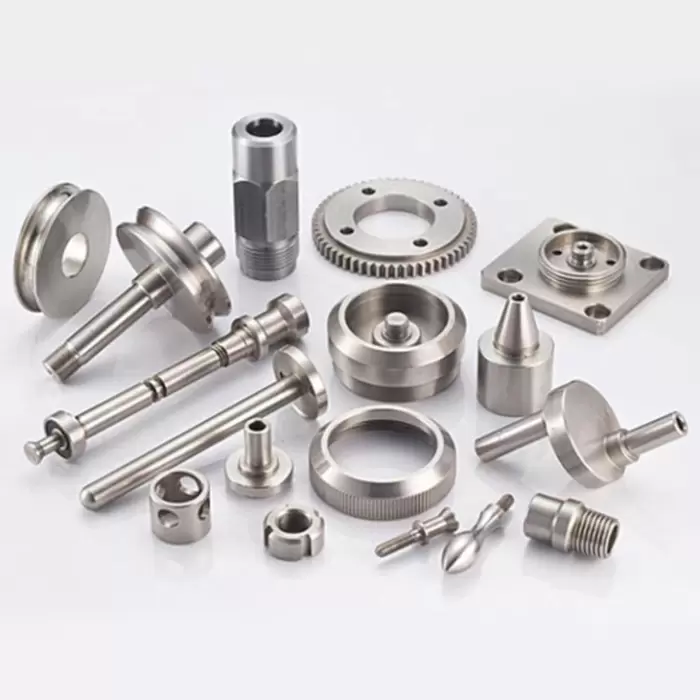
8.Conclusion
Precision machining parts play a critical role in the manufacturing industry, providing high-quality, reliable parts for a range of applications. Throughout this article, we have explored the definition, manufacturing techniques, materials, applications, quality control, advancements, and future outlook for precision machining parts.
Key points from this article include the importance of precision machining parts in industries such as aerospace, defense, medical, automotive, and electronics. We have also highlighted the variety of manufacturing techniques and materials used in the production of precision machining parts. Quality control and inspection are critical aspects of precision machining to ensure that the final product meets the required specifications and tolerances.
Advancements in precision machining, such as additive manufacturing, automation and robotics, and simulation and modeling, are driving innovation and creating new opportunities for manufacturers. However, there are also challenges to be addressed, such as the shortage of skilled labor and the need to invest in new technologies to remain competitive.
In conclusion, precision machining parts are critical components of the manufacturing industry, and their importance is only expected to grow in the coming years. Manufacturers should continue to invest in new technologies and processes to remain competitive and meet the growing demand for high-quality precision machining parts in a range of industries.
Precision machining parts are components that are produced by using advanced techniques and tools to achieve high accuracy and quality. Precision machining parts can be used for various applications, such as aerospace, medical, automotive, industrial, and more. Some of the common techniques for precision machining parts include:
- CNC machining: This technique uses computer-controlled machines to perform complex and precise operations on a workpiece. CNC machining can produce parts with tight tolerances, intricate shapes, and smooth finishes.
- EDM machining: This technique uses electrical discharges to cut or shape a workpiece. EDM machining can create parts with complex geometries, hard materials, and fine details.
- Laser machining: This technique uses a focused beam of light to cut or engrave a workpiece. Laser machining can create parts with high precision, speed, and flexibility.
- 3D printing: This technique uses a digital model to create a physical object by depositing layers of material. 3D printing can create parts with complex shapes, custom designs, and reduced waste.
Precision machining parts have many advantages, such as:
- Improved performance: Precision machining parts can enhance the functionality and efficiency of a system or device by reducing errors, friction, and wear.
- Reduced costs: Precision machining parts can lower the production costs by minimizing material waste, rework, and maintenance.
- Increased reliability: Precision machining parts can increase the durability and lifespan of a system or device by preventing failures, defects, and breakdowns.
Precision machining parts are essential for many industries and applications that require high standards of quality, accuracy, and performance. By using the appropriate techniques and tools, precision machining parts can be manufactured to meet the specific needs and specifications of the customers.