Precision CNC Machining Services
Provide Plastic and Metal Part CNC Machining services including:CNC Milling, CNC turning, Rapid drilling, CNC Grinding, CNC Cutting, Wire EDM machining etc.
CNC Machining Application Parts
CNC machining bares multi-feature, high strength, high accuracy and various material choices, etc., which allow CNC machining a larger application ranges.
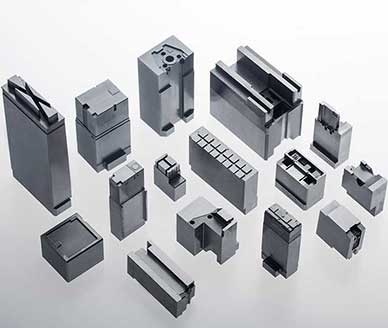
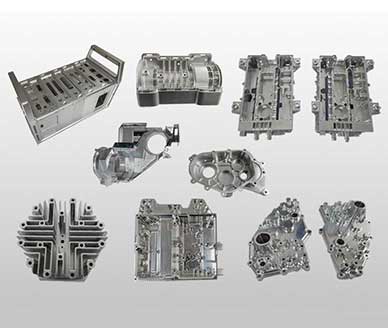
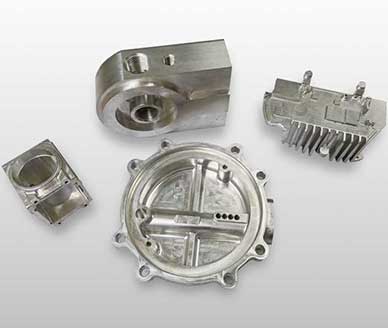
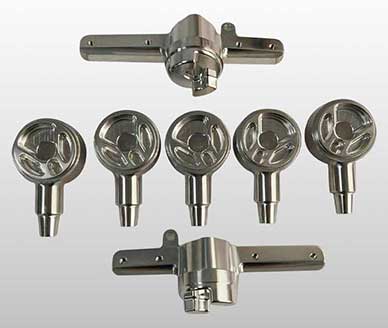
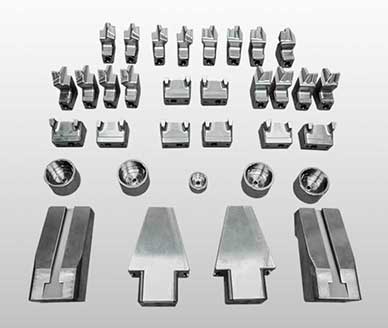
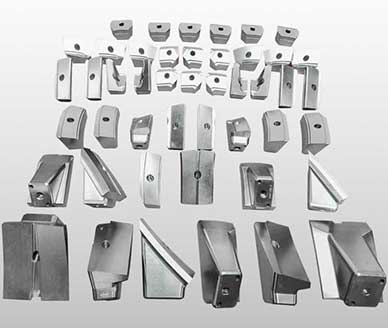
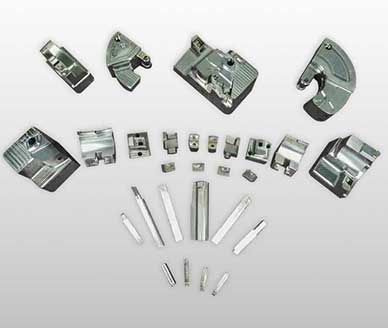
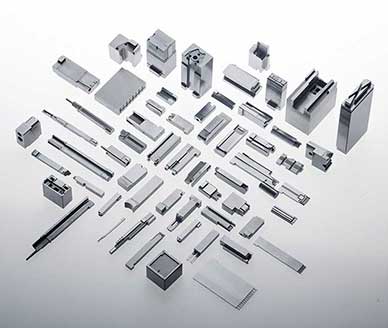
Parts CNC Machining Processing Capability
Provide CNC Machining services including:
- CNC Milling
- CNC Cutting
- CNC Rapid prototyping
- CNC Grinding
- CNC turning
- Rapid drilling
- CNC cutting
- Wire EDM machining
CNC Machining products are mainly used in:
- Precision connectors
- Electronic
- Optical parts
- Communication system
- Automotive parts
- Medical parts
Precision CNC Machining Services
CNC machining technology processes target products directly with high accuracy through three-dimensional data programming and splitting. The machined parts can be sprayed, plated, silk-screened, coated or finished by other surface treatments, and can be assembled and reflect effectively the product design features.
CNC machining materials:
Plastics: ABS、PC、PP、PE、POM、PA、PMMA、EPS…
Metals: stainless steel, Aluminum, Zinc, Brass, Copper, Bronze...
CNC Machining Materials
Metals Parts Machining
- Aluminum
- Brass
- Copper
- Stainless Steel
- Steel Alloy
- Steel Mild Low Carbon
- Titanium
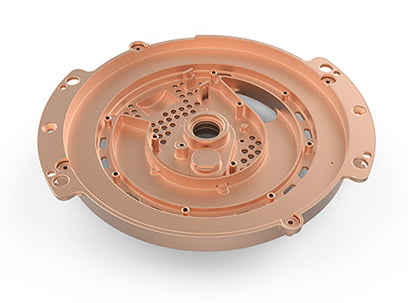
Plastics Parts Machining
- ABS
- Acetal
- CPVC
- Delrin (POM)
- HDPE
- LDPE
- Nylon
- PEEK
- PEI
- PET
- PMMA
- Polycarbonate
- Polypropylene
- PPSU
- PS
- PSU
- PTFE
- PVC
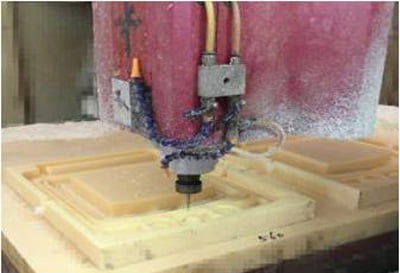
CNC machining prototypes advantages:
There are unique advantages in CNC machined prototypes other than rapid prototypes, fast machining, lower cost, and much wider range of choices of materials, what's more, the processed parts are featured with higher strength, high-temperature resistance, and high tenacity. CNC prototyping has become one of the major modern machining means.
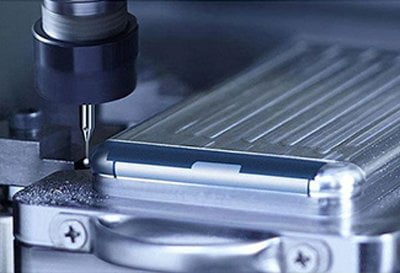
CNC machining cautions
During CNC machining , Confirmation of machining routines normally adheres to the following principles:
① Should assure the accuracy and surface roughness of the parts
② Maximally shorten machining routine to cut routine time and improve machining efficiency
③ Try best to simplize data calculation works to simplize machining program
④ Use subprograms for those repeat programs
CNC machining prototoypes finishes
By varaious of surface treatments, many beautiful, real-like prototypes can be made.
Those prototypes can meet the final design requirements of appearance, assembly and function verfication, and can be used to present in exhibition.
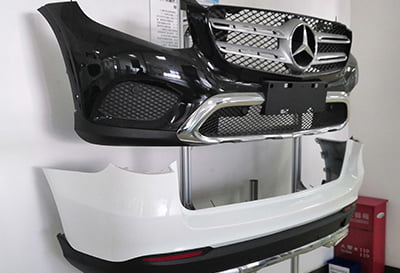
V1 Machining precision parts processing
V1 precision company has a team of 110 professional staff with focusing on the precision part from development, design and manufacturing, over 60 sets of high-end machining equipment. Most of our equipment are imported from Japan and Germany.
We passed high qualified management system ISO 9001:2015,ISO 14001:2015 and IATF 16949 certificates to guarantee the high-level and high-precision parts.Meanwhile,we have introduced advanced ERP management system to control the production progress at any time, to make high-quality parts,fast lead time and offer satisfactory services to customers are the company’s value.
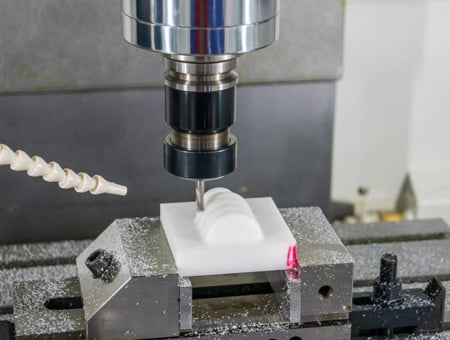
CNC machining Manufacturing FAQs
Machining is a manufacturing process that uses machine tools (such as lathes, mills, drills, etc.) and other tools and equipment to shape raw materials into desired shapes and sizes.
In modern manufacturing, machining technology has become an important means of producing high-precision and high-quality parts due to its excellent performance and wide range of applications. This technology not only produces high-precision, high-quality parts, but its production process can be automated and batched, thereby significantly improving production efficiency and product consistency.
First, let’s explore how machining enables high-precision and high-quality part production. Through precision mechanical equipment and professional operators, machining can accurately control the shape, size and surface roughness of parts, thereby ensuring that the accuracy and quality of parts meet design requirements. In addition, because every step in the machining process can be precisely controlled and adjusted, the accuracy and quality of each part is guaranteed to be consistent, even in mass production.
Secondly, the production process of mechanical processing can be automated and batch-oriented. This means that through the use of advanced automation equipment and software, complex machining processes can be simplified into a series of standard operating steps, thereby greatly improving production efficiency. At the same time, through mass production, the production cost of a single part can be further reduced, thereby improving the competitiveness of the product.
Additionally, machining can process many different materials, including metals, plastics, ceramics, and more. This is because machining technology can select the most suitable processing methods and equipment according to different material properties, thereby achieving efficient processing of various materials. This not only expands the application scope of machining, but also enables it to meet various production needs.
In general, machining technology has become an indispensable part of modern manufacturing due to its high precision, high quality, high efficiency and wide material adaptability.
In manufacturing, the main types of machining include turning, milling, drilling, grinding, etc. Each of these different types of machining has its own unique machine tools and processing methods.
First, let's look at turning. Turning is a machining method that uses rotating tools to remove material from a workpiece. It is commonly used to manufacture cylindrical parts such as shafts, sleeves and hubs. The main feature of turning is the combination of the rotational motion of the tool and the feed motion of the workpiece, thereby achieving continuous cutting of the workpiece. During the turning process, there is relative motion between the tool and the workpiece, so the position and speed of the tool need to be precisely controlled to ensure processing quality and efficiency.
Secondly, milling is a processing method that uses rotating tools to cut on the surface of the workpiece. Milling can be used to manufacture parts with complex shapes such as flat surfaces, curved surfaces, and slots. The main feature of milling is the combination of the rotational motion of the tool and the feed motion of the workpiece, thereby achieving continuous cutting of the workpiece surface. During the milling process, there is also relative motion between the tool and the workpiece, so the position and speed of the tool need to be precisely controlled to ensure processing quality and efficiency.
Next comes drilling. Drilling is a processing method that uses a rotating drill bit to form a hole in a workpiece. Drilling is commonly used to create threaded holes, pin holes, bolt holes, etc. The main feature of drilling is the combination of the rotary motion of the drill bit and the feed motion of the workpiece, thereby achieving continuous cutting of the workpiece. During the drilling process, there is relative motion between the drill bit and the workpiece, so the position and speed of the drill bit need to be precisely controlled to ensure processing quality and efficiency.
Finally comes grinding. Grinding is a processing method that uses a grinding wheel or grindstone to cut the surface of a workpiece. Grinding can be used to manufacture high-precision and high-finish parts such as bearings, gears, and threads. The main feature of grinding is the combination of the high-speed rotational motion of the grinding wheel or grinding stone and the feed motion of the workpiece, thereby achieving continuous cutting of the workpiece surface. During the grinding process, there is relative motion between the grinding wheel or grinding stone and the workpiece, so the position and speed of the grinding wheel or grinding stone need to be precisely controlled to ensure processing quality and efficiency.
To summarize, turning, milling, drilling and grinding are the four main types of machining. Each type of machining has its own unique machine tools and processing methods to meet the processing needs of different parts. Through the reasonable selection and application of these mechanical processing methods, production efficiency and product quality can be improved to meet the development needs of the manufacturing industry.
A CNC machine tool, also known as a computer numerical control machine toolA CNC machine tool, also known as a computer numerical control machine tool, is an advanced type of machine tool that utilizes computer programming to precisely control the movement and operation of the cutting tools. This technology allows for high-precision and high-efficiency machining, resulting in accurate and consistent finished products.
One of the key features of CNC machine tools is their ability to control the tool path and cutting parameters through a computer program. This means that the machine can automatically adjust its movements and operations based on the specific requirements of the task at hand. By using sophisticated algorithms and mathematical calculations, the CNC machine tool can achieve precise cuts and shapes with minimal human intervention.
CNC machine tools are particularly well-suited for complex geometric shapes and processing processes. With their advanced capabilities, they can easily handle intricate designs and intricate details, making them ideal for industries such as aerospace, automotive, and medical devices. Whether it's creating intricate molds or producing precision parts, CNC machine tools have revolutionized the manufacturing industry by providing unparalleled accuracy and efficiency.
In addition to their precision and versatility, CNC machine tools also offer a certain degree of automation and flexibility. They can be programmed to perform repetitive tasks with ease, reducing the need for manual labor and minimizing the risk of errors. Furthermore, CNC machine tools can be easily modified and adjusted to accommodate different materials and production requirements, making them highly adaptable to changing needs.
Overall, CNC machine tools represent a significant advancement in manufacturing technology. Their ability to control tool path and cutting parameters through a computer program enables high-precision and high-efficiency machining, while their versatility and automation make them indispensable in various industries. As technology continues to evolve, CNC machine tools will undoubtedly play an increasingly important role in shaping the future of manufacturing.
In modern manufacturing, machining technology is widely used in various fields, including but not limited to aerospace, automobile manufacturing, electronic equipment production, medical equipment manufacturing, mold manufacturing, etc. The application range of this technology is so wide that it covers almost all fields related to manufacturing.
First, let's look at the aerospace industry. In this industry, machining technology is used to manufacture various parts of aircraft, such as engine parts, fuselage structural parts, etc. The accuracy and quality of these parts directly affect the performance and safety of the aircraft. Therefore, the aerospace industry has very high requirements for machining technology.
Secondly, the automotive industry is also an important application field of machining technology. A car is a complex system composed of thousands of parts, and the manufacture of these parts is almost all inseparable from machining technology. For example, key components such as gears, bolts, nuts, and bearings in engines require precision machining to be manufactured.
In addition, the electronics industry also makes extensive use of machining technology. Circuit boards and electronic components in electronic equipment all need to be manufactured through mechanical processing. Moreover, as electronic equipment becomes increasingly miniaturized, the requirements for machining technology are also becoming higher and higher.
In the field of medical device manufacturing, machining technology also plays an important role. For example, artificial joints, dental equipment, medical devices, etc. all require precision machining to manufacture. The accuracy and quality of these equipment are directly related to the life safety of patients. Therefore, the medical equipment manufacturing industry also has very strict requirements for machining technology.
Finally, mold manufacturing is also an important application area of machining technology. Molds are tools used to produce parts of various shapes and sizes, and the manufacturing of molds requires mechanical processing. Therefore, the demand for machining technology in the mold manufacturing industry is also very large.
In general, no matter which manufacturing field it is, it is inseparable from the support of mechanical processing technology. This technology can not only improve production efficiency, but also ensure product accuracy and quality, thereby meeting various complex manufacturing needs.
During the machining process, we usually use some indicators to measure its machining accuracy. These indicators include dimensional tolerances, shape tolerances and surface roughness.
First, let’s look at dimensional tolerances. Dimensional tolerance refers to the size of machined parts and the allowable tolerance range. In other words, it describes the degree of difference between the actual size of the machined part and the designed size. By measuring dimensional tolerances, we can determine whether a part meets design requirements and ensure it will function properly during assembly and use.
Secondly, shape tolerance is another important indicator. Form tolerance focuses on the geometric shape and positional accuracy of machined parts. This means we need to ensure that the shape of the part matches the design requirements and that the positional relationship between the various parts is accurate. By measuring the shape tolerance, we can determine whether the part has the correct geometry, thereby ensuring its stability and reliability during use.
Finally, surface roughness is also one of the important indicators to measure processing accuracy. Surface roughness refers to the smoothness and roughness level of the surface of machined parts. A smooth surface usually means higher machining accuracy, while a rough surface may indicate some problems during the machining process. By measuring surface roughness, we can evaluate the quality and appearance of a part's surface and ensure it does not suffer unnecessary wear or damage due to surface problems during use.
To sum up, dimensional tolerance, shape tolerance and surface roughness are key indicators to measure the accuracy of machining. Through accurate measurement and control of these indicators, we can ensure that the quality and performance of processed parts meet expected requirements, thereby improving the efficiency and reliability of the entire production process.
Machining is a process that uses machine tools for CNC processing, which has the advantages of high efficiency, high precision and high repeatability. In contrast, manual processing is performed by manual operations, which requires the skills and experience of technicians to be taken into account, so the processing accuracy and efficiency are relatively low.
In machining, CNC processing is one of the key steps. CNC stands for Computer Numerical Control, which uses a computer control system to control the movement and operation of machine tools. Through pre-programmed instructions, the CNC system can accurately control the position, speed and feed of the tool, thereby achieving precise processing of the workpiece. This automated process greatly improves the efficiency of processing and also reduces the possibility of human error.
Manual machining requires more manual intervention and operations than mechanical machining. Technicians need to use hand tools to perform cutting, grinding, drilling and other operations according to the requirements of the workpiece. Since these operations are completed by relying on the experience and skills of technicians, the accuracy and efficiency of processing are greatly limited. In addition, manual processing is also susceptible to human factors, such as fatigue, lack of concentration, etc., which may also lead to a decrease in processing quality.
Although machining has many advantages, there are also some challenges and limitations. First, machining requires professional equipment and technical support, which may be a burden for some small businesses. Secondly, the cost of machining is relatively high, especially in mass production. In addition, mechanical processing also requires strict quality control and inspection to ensure that the processed workpieces meet the requirements.
To sum up, mechanical processing is an efficient, high-precision and highly repeatable processing method, suitable for mass production and processing of complex workpieces. However, for some small businesses and individual craftsmen, manual machining may be more affordable and flexible. Whether it is mechanical processing or manual processing, it is necessary to choose the appropriate processing method according to the specific situation to meet the requirements of the workpiece and the needs of production efficiency.
In modern manufacturing, machining is a vital task that involves a variety of essential skills. First, we need to master the operating skills of machine tools. This includes how to properly use various mechanical equipment, such as lathes, milling machines, grinders, etc., as well as how to maintain and maintain the equipment. Mastering these skills is crucial to ensuring the quality and efficiency of machining.
Secondly, we need to have CNC programming skills. CNC (computer numerical control) technology is one of the important technologies in modern manufacturing, which can realize the automated operation of mechanical equipment. Therefore, mastering the skills of CNC programming can not only improve our work efficiency, but also enable us to better adapt to the development of modern manufacturing.
In addition, we also need to master the skills of tool selection and replacement. During the machining process, choosing the right tools and replacing worn tools in time are very important to ensure the processing quality and maintain the service life of the equipment.
Finally, we need skills in process optimization. This includes how to improve processing efficiency and reduce production costs by improving process methods, as well as how to improve product quality and performance by optimizing process flows.
These skills are not acquired overnight; they require continuous learning and practice to develop and improve. Only through continuous training and practice can we better master these skills and play a greater role in machining work.
In the mechanical processing process, common materials include metal materials, plastic materials, wood, etc. These different materials have their own unique properties and processing characteristics, so it is necessary to select the appropriate material and process it accordingly according to specific conditions.
Metal materials are the most commonly used materials in mechanical processing. They usually have high strength, hardness and wear resistance, and are suitable for manufacturing various mechanical parts and structural parts. When processing metal materials, factors such as their thermal conductivity, melting point, and thermal expansion coefficient need to be considered to ensure the stability and quality of the processing process.
Plastic material is a lightweight, easy-to-process material that is widely used in the manufacture of various plastic products and packaging materials. Compared with metal materials, plastic materials have lower strength and hardness, but have good insulation properties and chemical stability. When processing plastic materials, attention needs to be paid to controlling temperature and pressure to avoid material deformation and damage.
Wood is a natural, renewable material widely used in the manufacture of furniture, building structures, and ships. Wood has good plasticity and toughness and is easy to process and shape. However, the density of wood is low, and its strength and durability are relatively poor. Therefore, when processing wood, attention needs to be paid to selecting the appropriate wood species and treatment methods to improve the quality and service life of the product.
In addition to the common materials mentioned above, there are also some special materials such as ceramic materials and composite materials that are also commonly used in the field of mechanical processing. These materials have their own unique properties and application ranges and need to be selected and processed based on specific engineering requirements.
In short, during the machining process, selecting the right materials and performing appropriate processing are the keys to ensuring product quality and performance. Through the understanding and mastery of different materials, engineering needs can be better met and production efficiency and economic benefits can be improved.
In machining, common tools include milling cutters, turning tools, drills, and cutting tools. These tools play an important role in the manufacturing industry, and they are widely used in various machining processes.
First of all, a milling cutter is a tool used for machining flat or curved surfaces. It is usually made of carbide and has a sharp cutting edge and rotating cutting surface. Milling cutters can be used for operations such as milling, engraving, drilling and grooving on a variety of materials including metal, plastic and wood.
Secondly, turning tools are tools used to rotate workpieces for machining. It is usually made of high-speed steel or carbide and has cutting edges and cutting surfaces. Turning tools can be used for turning outer circles, inner circles, end faces and threads, etc., and are suitable for processing shafts, discs and sleeve parts.
Third, a drill bit is a tool used to drill holes. It is usually made of high-speed steel or carbide, with sharp cutting edges and spiral cutting surfaces. Drill bits can be used for drilling, reaming and reaming operations, and are suitable for processing metal and non-metal materials.
Finally, cutting tools are tools used to cut materials. It is usually made of high-speed steel or carbide, with sharp cutting edges and straight or curved cutting surfaces. Cutting tools can be used to cut various materials such as metal, plastic and wood, and are suitable for manual operations and mechanical processing.
To sum up, milling cutters, turning tools, drill bits and cutting tools are common tools used in machining. They play an important role in the manufacturing industry, providing efficient, precise and reliable solutions for various machining processes.
CNC (Computer Numerical Control) machine tool is a highly automated mechanical equipment with many types, including CNC lathe, CNC milling machine, CNC drilling machine , CNC grinder, etc. Each of these different types of machine tools has unique functions and characteristics and is suitable for different processing technologies and processing objects.
First of all, a CNC lathe is a device used to rotate workpieces for cutting. It controls the position and motion trajectory of the tool through a computer control system to achieve precise processing of the workpiece. CNC lathes are widely used in the processing of shaft parts, such as gears, threads, etc.
Secondly, a CNC milling machine is a device used for flat and curved surface processing. It uses a rotating tool to cut on the surface of the workpiece to form the desired shape and size. CNC milling machines can be used for processing various materials, such as metals, plastics, etc.
Third, a CNC drilling machine is a device used for hole processing. It drills holes in the workpiece by rotating the drill bit, thereby achieving precise machining of the hole. CNC drilling machines are widely used for hole machining tasks in machining, such as automotive parts, aerospace components, etc.
Finally, a CNC grinder is a device used for precision machining. It grinds the workpiece through a grinding wheel or grinding stone to obtain high-precision surface quality. CNC grinders are widely used in the processing of precision parts, such as molds, bearings, etc.
In short, different types of CNC machine tools are suitable for different processing technologies and processing objects. They realize highly automated processing processes through computer control systems, improving production efficiency and product quality. With the continuous advancement of science and technology, CNC machine tools are increasingly used in the manufacturing industry, providing efficient and precise processing solutions for all walks of life.
Common question in CNC Machining Production
In order to ensure the quality of machining, it is necessary to use high-quality machine tools and cutting tools, as well as precise measuring and testing equipment. In addition, proper tool path planning and reasonable cutting parameter settings are required to ensure machining quality and process stability.
There are many factors we need to consider when choosing the right cutting tool. These factors include processing material, processing shape and processing volume. Different materials and shapes require different types of tools. For example, for milling operations, we need to use milling tools; for turning operations, we need to use turning tools.
In addition, according to the requirements of processing volume and processing quality, we also need to select appropriate parameters. These parameters include cutting speed, feed rate and depth of cut. Cutting speed refers to the distance the tool moves per unit time, which directly affects processing efficiency and processing quality. The feed speed refers to the feed amount of the tool per unit time, which also affects the processing efficiency and processing quality. Cutting depth refers to the depth of the tool cutting into the workpiece, which will affect the machining accuracy and surface quality.
Therefore, selecting appropriate cutting tools and setting appropriate parameters are the keys to ensuring processing quality and improving processing efficiency.
In the process of improving machining production efficiency, we need to consider it from multiple perspectives. First, choosing the right machine tool and tooling is crucial. This requires us to select machine tools and cutting tools with superior performance, high precision and durability based on specific production needs and material characteristics to ensure the stability and efficiency of the production process.
Secondly, we need to set cutting parameters reasonably. This includes the setting of cutting speed, feed speed, cutting depth and other parameters. The setting of these parameters directly affects the cutting effect and production efficiency. Therefore, we need to set these parameters reasonably according to the actual production conditions and material characteristics to achieve the best cutting effect and the highest production efficiency.
Furthermore, optimizing tool path planning is also an important means to improve production efficiency. Through reasonable tool path planning, unnecessary idle strokes can be reduced, cutting efficiency can be improved, and production efficiency can be improved.
In addition, automated production processes are also an effective way to improve production efficiency. By introducing automation equipment and technology, the production process can be automated, manual intervention reduced, and production efficiency improved.
Finally, regular maintenance and upkeep of machine tools and equipment is also very important. This can not only ensure the normal operation of the equipment and extend the service life of the equipment, but also detect and solve potential problems of the equipment in time to prevent equipment failure from affecting production. Therefore, we need to develop a reasonable maintenance plan and regularly inspect and maintain the equipment to ensure the normal operation and service life of the equipment.
When selecting the appropriate processing method, we need to consider many factors, including the shape of the part being processed, the material, and the processing requirements. For example, for surface machining and complex contour machining, we usually choose milling; for shaft components, we usually choose turning.
First, we need an in-depth understanding and analysis of the shape of the parts being processed. This is because different shapes may require different processing methods. For example, for some complex geometric shapes, we may need to use milling or turning methods to process them. Therefore, understanding the shape is an important basis for selecting appropriate processing methods.
Secondly, we need to consider the material of the parts being processed. Different materials may have different requirements for processing methods. For example, for some materials with higher hardness, we may need to use more powerful processing equipment and methods for processing. Therefore, understanding of materials is also an important basis for selecting appropriate processing methods.
Finally, we also need to consider the processing needs of the parts being processed. This includes factors such as processing accuracy, efficiency, and cost. For example, for some parts that require high-precision processing, we may need to choose more precise processing equipment and methods; for some parts that require high-efficiency processing, we may need to choose more efficient processing equipment and methods; for some parts that require low-cost processing For parts, we may need to choose more economical processing equipment and methods. Therefore, understanding and analysis of processing requirements is also an important basis for selecting appropriate processing methods.
Taking surface processing and complex contour processing as an example, we usually choose milling as the main processing method. This is because milling can effectively handle complex geometries and achieve high accuracy and efficiency. However, this is not to say that milling is the best option in every situation. In some cases, we may also need to choose other processing methods based on specific needs and conditions.
Similarly, for shaft components, we usually choose turning as the main processing method. This is because turning can effectively handle shaft components and achieve high accuracy and efficiency. However, this does not mean that turning is the best option in every situation. In some cases, we may also need to choose other processing methods based on specific needs and conditions.
Cleaning and debris removal of mechanical parts are critical steps during the manufacturing process. This is because only when the surface finish and accuracy of the part are guaranteed can it be ensured that it can perform the expected function in subsequent use. Therefore, we need to clean the mechanical parts thoroughly to remove all residue and dirt.
In addition, according to the processing requirements, we also need to carry out strict inspection and measurement of the parts. The purpose of this step is to ensure that the quality of the parts meets our standards and requirements. We need to use professional measuring tools to accurately measure key parameters such as size, shape and surface roughness of parts. At the same time, we also need to conduct a comprehensive visual inspection of the part to find and eliminate any problems that may affect its quality.
In general, cleaning, debris removal, inspection and measurement of mechanical parts are all indispensable aspects of the manufacturing process. Only through these steps can we ensure the quality of our parts to meet our customers' needs.
CNC programming is an important task, which requires writing corresponding program instructions according to the shape and processing requirements of the part to control the machine tool for processing operations. During the CNC programming process, various programming software can be used, such as CAD/CAM software and G-code programming software.
First of all, the core of CNC programming is writing program instructions. These instructions are designed according to the shape and processing requirements of the part, and they tell the machine tool how to perform processing operations. By writing precise program instructions, you can ensure that the processing quality and accuracy of the parts meet the expected requirements.
Secondly, CNC programming can be accomplished using a variety of programming software. One of the commonly used software is CAD/CAM software. CAD (computer-aided design) software can help engineers design and draw three-dimensional models of parts, while CAM (computer-aided manufacturing) software can convert designed models into executable program instructions. Through CAD/CAM software, engineers can design and program parts on the computer, greatly improving work efficiency and accuracy.
Another commonly used CNC programming software is G-code programming software. G-code is a general-purpose programming language used to control the motion and functionality of CNC machine tools. By using G-code programming software, engineers can directly write G-code program instructions and input them into the machine tool for machining operations. G-code programming software usually has rich functions and flexible operation interface, making the programming process easier and more efficient.
To sum up, CNC programming is a key task. It requires writing corresponding program instructions according to the shape and processing requirements of the part to control the machine tool for processing operations. During the CNC programming process, tools such as CAD/CAM software and G-code programming software can be used to achieve this. These software provide rich functions and flexible operation interfaces, making CNC programming simpler, more efficient and more accurate.
During the machining process, machining accuracy is affected by many factors. These factors include, but are not limited to, the accuracy of the machine tool, the quality of the cutting tools, and the control of the machining process. In order to ensure machining accuracy, it is necessary to control and optimize from multiple aspects.
First, it is crucial to choose high-precision machine tools and cutting tools. High-precision machine tools can provide a more stable working platform, thereby reducing machining errors. High-quality cutting tools can ensure the stability and efficiency of the cutting process, thereby improving processing accuracy.
Secondly, optimizing processing parameters is also an important means to improve processing accuracy. By reasonably adjusting the processing parameters, the machine tool can achieve the best working condition during the processing, thereby improving the processing accuracy. This includes selecting appropriate parameters such as cutting speed, feed rate and depth of cut.
Finally, improving operating skills is also the key to ensuring machining accuracy. Skilled operators can accurately control the movement of the machine tool to avoid processing errors caused by improper operation. Therefore, regular training and assessment of operators to improve their operating skills is of great significance to improving processing accuracy.
In general, to ensure the accuracy of machining, it is necessary to control and optimize from many aspects such as selecting high-precision machine tools and cutting tools, optimizing processing parameters, and improving operating skills. Only in this way can the accuracy of mechanical processing be ensured and the needs of production be met.
In order to improve the production efficiency of CNC machining, we need to comprehensively consider many factors. These factors include, but are not limited to, machine tool production capabilities, process optimization, and operational efficiency. By optimizing the production process and adopting automated equipment and intelligent technology, we can effectively improve production efficiency.
First of all, the production capacity of machine tools is one of the important factors affecting production efficiency. A high-performance machine tool can complete machining tasks faster, thereby increasing overall production speed. Therefore, when choosing a machine tool, we should consider its maximum processing capacity and whether it can meet our production needs.
Secondly, the optimization of process flow is also the key to improving production efficiency. Through detailed analysis and improvement of the process flow, we can find more efficient processing paths and methods. For example, rationally arranging the processing sequence and reducing unnecessary processes and time waste can significantly improve production efficiency.
In addition, the use of automation equipment and intelligent technology is also an important means to improve production efficiency. Automation equipment can realize automated control of the production process, reduce manual intervention, and improve the stability and accuracy of production. Intelligent technology can help us better manage and optimize the production process through data analysis and prediction, and further improve production efficiency.
To sum up, to improve the production efficiency of CNC machining, we need to comprehensively consider the production capacity of the machine tool, the optimization of the process flow, and the efficiency of the operation. By optimizing the production process, adopting automated equipment and intelligent technology, we can effectively improve production efficiency to meet the growing production demand.
leave a message
Contact CNC Machining
Contact us now to bring your idea into reality, our professional team will respond you in 24 hours after we get your email.
- Email: [email protected]
- Office Address: 2nd Floor, NO. 10 Lianhu Road, Changan Town, Dongguan City, Guangdong Province, China, 523850
- Factory Address: No.38, Hexing Road, Shatou, Changan Town, Dongguan City, Guangdong Province, China, 523850
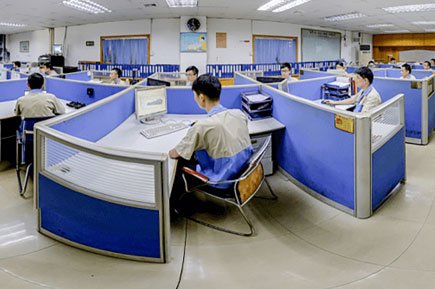