Table of Contents:
- Introduction
- Techniques of Insert Molding
- Advantages of Insert Molding
- Applications of Insert Molding
- Materials used in Insert Molding
- Considerations for Designing Insert Molding Parts
- Conclusion
-
1.Introduction
Insert molding is a manufacturing process that combines two or more materials to create a single part. It involves the insertion of a pre-formed component, such as a metal or plastic insert, into a mold, which is then filled with a thermoplastic or thermoset material. The resulting part has the strength and durability of the insert, combined with the design flexibility and efficiency of the molded material.
The history of insert molding can be traced back to the early 20th century when metal inserts were used in rubber molding. In the 1960s, plastic inserts were introduced, which led to the development of overmolding techniques. Since then, insert molding has become increasingly popular in various industries, including automotive, electronics, medical devices, and aerospace, among others. The process has continued to evolve, with advancements in materials, techniques, and equipment, leading to improved performance and cost-effectiveness.
-
2.Techniques of Insert Molding
There are several techniques for insert molding, each with its own advantages and disadvantages. Some of the most commonly used techniques are:
- Overmolding technique: This involves placing a pre-formed insert into a mold, and then injecting a second material around it to create a single, integrated part. Overmolding is ideal for creating soft-touch grips, non-slip surfaces, or parts with multiple colors.
- Injection molding technique: This involves placing a pre-formed insert into a mold and then injecting a thermoplastic material around it under high pressure. Injection molding is a highly efficient process that allows for the creation of complex shapes and precision parts.
- Two-shot molding technique: This involves using two injection molding machines to create a part with two different materials. The first machine creates the base material, and the second machine injects the second material, which forms around the base material to create a single part.
- Compression molding technique: This involves placing a pre-formed insert into a heated mold and then compressing the mold to force the thermosetting material around the insert. Compression molding is ideal for creating high-strength parts, such as electrical components, circuit boards, and automotive parts.
Each technique has its own strengths and limitations, and the choice of technique depends on the specific requirements of the part and the manufacturing process.
-
3.Advantages of Insert Molding
Insert molding offers several advantages over other manufacturing methods, including:
- Cost savings: Insert molding can be more cost-effective than traditional manufacturing methods because it combines multiple steps into a single process. This eliminates the need for secondary operations, such as assembly, welding, or adhesive bonding, which can save time and money.
- Increased design flexibility: Insert molding allows for the creation of complex, multi-material parts that are difficult or impossible to produce with other manufacturing methods. This enables designers to create parts with unique shapes, textures, and functionalities, which can improve product performance and user experience.
- Enhanced component durability: Insert molding can improve the durability and reliability of parts by combining the strength and properties of different materials. The pre-formed inserts provide added strength, stiffness, or conductivity, while the molded material provides protection, insulation, or cushioning.
- Improved manufacturing efficiency: Insert molding is a highly automated process that can reduce labor costs and improve consistency and quality. The process can be easily scaled up or down to meet changing production needs, which makes it a flexible and efficient manufacturing solution.
Overall, insert molding offers a range of benefits that can help manufacturers produce high-quality, cost-effective, and innovative products.
-
4.Applications of Insert Molding
Insert molding has a wide range of applications in various industries, including:
- Automotive industry: Insert molding is commonly used in the automotive industry to produce high-strength, lightweight parts, such as dashboard components, door handles, and sensor housings. The process can help reduce costs and improve performance, durability, and safety.
- Consumer electronics industry: Insert molding is widely used in the consumer electronics industry to create parts with intricate designs and functionalities, such as mobile phone covers, camera lenses, and computer keyboards. The process can enhance the look, feel, and functionality of electronic devices while improving their durability and reliability.
- Medical device industry: Insert molding is becoming increasingly popular in the medical device industry due to its ability to create complex, multi-material parts with high precision and consistency. The process can produce parts with superior biocompatibility, sterilizability, and mechanical properties, making them ideal for use in implantable devices, surgical instruments, and diagnostic equipment.
- Aerospace industry: Insert molding is used in the aerospace industry to produce lightweight, high-strength parts for aircraft and spacecraft, such as control panels, seat frames, and sensor housings. The process can help reduce weight, increase fuel efficiency, and improve performance and safety.
Overall, insert molding is a versatile manufacturing process that can be used in a wide range of industries to produce high-quality, cost-effective, and innovative products.
-
5.Materials used in Insert Molding
The materials used in insert molding can vary depending on the requirements of the part and the application. Some of the most commonly used materials include:
- Thermoplastics: These are materials that can be melted and re-molded multiple times without losing their original properties. Common thermoplastics used in insert molding include ABS, polycarbonate, nylon, and polypropylene. These materials offer a range of properties such as toughness, heat resistance, chemical resistance, and flexibility.
- Thermosetting plastics: These are materials that undergo a chemical reaction when heated, causing them to harden and become rigid. Common thermosetting plastics used in insert molding include epoxy, phenolic, and urethane. These materials offer excellent thermal stability, chemical resistance, and electrical properties.
- Metals: Metals such as aluminum, brass, copper, and stainless steel are commonly used in insert molding to add strength, conductivity, or weight to a part. The metal insert is placed in the mold cavity, and the plastic is injected around it, creating a strong, durable part.
- Ceramics: Ceramics are used in insert molding to add strength, abrasion resistance, or high-temperature resistance to a part. They are commonly used in applications such as automotive and aerospace industries, where parts must withstand extreme temperatures, pressures, and wear.
The choice of material depends on the specific requirements of the part, such as strength, durability, weight, or cost, and the manufacturing process. By selecting the right material, manufacturers can create parts that meet the desired specifications and perform well in their intended applications.
-
6.Considerations for Designing Insert Molding Parts
When designing parts for insert molding, there are several important considerations to keep in mind, including:
- Designing for manufacturability: The part design should take into account the specific requirements of the insert molding process, such as the number, size, and location of the inserts, and the flow of the plastic material. Parts that are designed for manufacturability can reduce costs, improve quality, and increase efficiency.
- Material selection: The choice of material should be based on the specific requirements of the part and the application. Factors to consider include strength, durability, thermal stability, chemical resistance, and cost. The material should also be compatible with the insert and the molding process.
- Tolerances and fit requirements: The part design should specify the required tolerances and fit requirements to ensure that the insert and the molded material fit together correctly. The design should also take into account any thermal expansion or contraction of the materials during molding or use.
- Part complexity: The part design should be optimized for the insert molding process. Complex geometries, thin walls, and small features can make molding more difficult, increase cycle times, and affect the quality of the finished part. Simplifying the design can help reduce costs and improve quality.
By taking these considerations into account, designers can create parts that are optimized for insert molding, and that meet the desired performance, quality, and cost requirements.
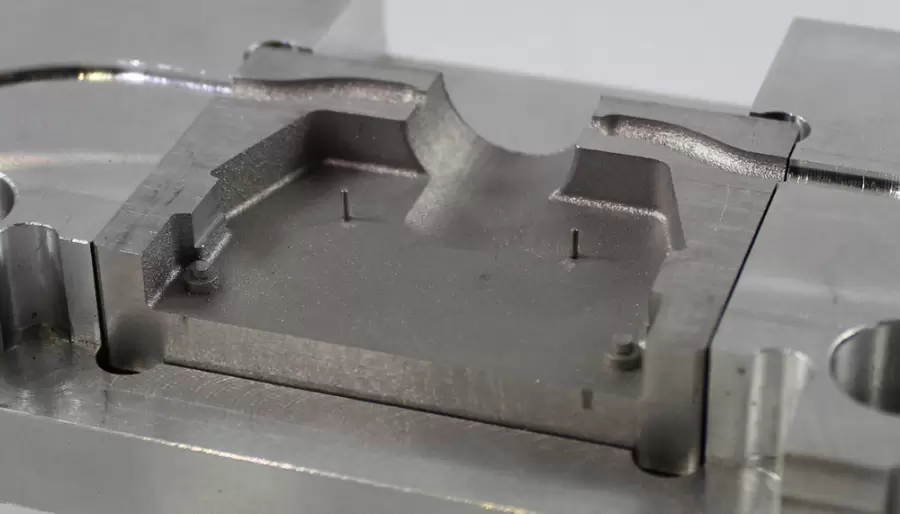
-
7.Conclusion
In conclusion, insert molding is a versatile manufacturing process that offers several advantages, including cost savings, increased design flexibility, enhanced component durability, and improved manufacturing efficiency. The process involves molding a plastic material around an insert, creating a strong, durable, and functional part.
We discussed the different techniques of insert molding, such as overmolding, injection molding, two-shot molding, and compression molding. We also explored the materials used in insert molding, including thermoplastics, thermosetting plastics, metals, and ceramics.
Designing parts for insert molding requires careful consideration of factors such as manufacturability, material selection, tolerances, and fit requirements. By optimizing the part design for the insert molding process, manufacturers can reduce costs, improve quality, and increase efficiency.
In the future, we can expect to see further advancements in the technology and materials used in insert molding. Research and development efforts will continue to focus on improving the performance, durability, and functionality of insert molded parts, while also reducing costs and environmental impact.
Overall, insert molding is an important manufacturing process that offers a range of benefits for various industries. By understanding the process and optimizing the part design, manufacturers can create high-quality, cost-effective, and innovative products that meet the demands of today’s market.