Table of Contents:
- Introduction
- Steps in the Injection Molding Process
- Design Considerations for Plastic Gears
- Applications of Plastic Gears
- Challenges and Limitations of Plastic Gear Injection Molding
- Future of Plastic Gear Injection Molding
- Conclusion
-
1. Introduction
Plastic gear injection molding is a manufacturing process that involves creating gears from thermoplastic materials through the use of injection molding machines. It is a cost-effective, efficient, and precise method of manufacturing gears that have become essential components in many industries. This article will cover the step-by-step process of plastic gear injection molding, the design considerations for plastic gears, their applications, challenges, and limitations.
-
2. Steps in the Injection Molding Process
The injection molding process involves several steps that must be followed precisely to create high-quality gears.
The first step is mold design, which involves designing the gear mold based on the desired gear specifications. The mold should contain the desired number of cavities or cavities, depending on the expected production volume. The mold materials must be chosen based on the specific requirements of the gear’s end-use application.
The second step is material selection, which involves choosing the appropriate thermoplastic material for the gear based on the desired properties such as temperature resistance, strength, durability, and chemical resistance.
The third step is melting and injection, where the chosen plastic is melted and injected into the mold cavity using the injection molding machine. It is essential to control the temperature and timing of this process for consistent and high-quality gears.
Finally, the gears are cooled and ejected from the mold. The cooling process may involve water or other cooling agents to ensure the gear’s proper solidification and geometry. The gear is then removed from the mold and trimmed to the desired shape.
-
3. Design Considerations for Plastic Gears
When designing plastic gears, several factors must be taken into account. These include gear geometry, material selection, surface finish, tolerance, and fit.
The gear geometry should be optimized for the specific application of the gear, such as torque, speed, and load-carrying capacity. It is also essential to consider the mating gears and their geometry to ensure optimal performance.
Material selection should be based on the desired property requirements of the gear’s end-use application. The material’s wear resistance, temperature resistance, and chemical resistance should be considered, among other factors.
Surface finish must also be considered when designing plastic gears. A smooth surface finish can reduce wear and tear and improve the gear’s overall performance.
Tolerance and fit are also crucial factors in gear design. The gear’s tolerance should be precise, and the fit should be tight to ensure proper meshing with mating gears and optimal performance.
-
4.Applications of Plastic Gears
Plastic gears have become essential components in various industries due to their cost-effectiveness, versatility, and lightweight properties. Some of the applications of plastic gears include:
- Automobile Industry: Plastic gears are used in various automotive applications, such as power windows, windshield wipers, and door locks, due to their lightweight and durability properties.
- Robotics and Automation: Plastic gears are extensively used in robotics and automation, where lightweight and precision are critical in achieving accurate movement and control.
- Medical Industry: Plastic gears have become prevalent in medical applications, such as medical devices, dental equipment, and diagnostic tools, due to their biocompatibility and sterilization properties.
- Consumer Electronics: Plastic gears are widely used in various consumer electronics, such as printers, cameras, and toys, where low cost and lightweight are essential.
-
5. Challenges and Limitations of Plastic Gear Injection Molding
Plastic gear injection molding has some limitations and challenges that must be taken into account during the manufacturing process.
Part size and complexity can have a significant impact on the injection molding process’s feasibility and cost. The larger and more complex the gear, the more challenging and expensive it is to manufacture using injection molding.
Material properties and selection are also crucial factors in plastic gear injection molding. Some materials may require specific molding conditions or may not be suitable for injection molding, limiting their use in gear manufacturing.
Finally, cost and investment are significant challenges in plastic gear injection molding. The initial investment in molds and equipment can be high, and the cost per part may be higher than other manufacturing methods, depending on the gear’s complexity and production volume.
-
6. Future of Plastic Gear Injection Molding
The future of plastic gear injection molding is promising, with advancements in technology and new materials being developed constantly. Emerging technologies, such as 3D printing and nanotechnology, may offer new opportunities for improving the injection molding process’s efficiency and precision. Advanced materials, such as reinforced thermoplastics and biomaterials, may also offer new properties and applications for plastic gears.
If you need about Plastic Gear Injection Molding Services,You can click on the V1 Prototype website to find it:V1 is a comprehensive processing and manufacturing enterprise, which has been committed to precision plastic gear mold manufacturing, precision gear injection molding and sales.
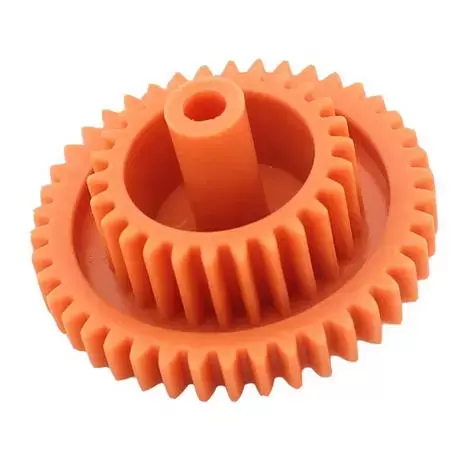
-
7. Conclusion
In summary, plastic gear injection molding is a cost-effective, efficient, and precise method of producing gears from thermoplastic materials. When designing gears for injection molding, several factors must be taken into account, such as material selection, geometry, and surface finish. The applications of plastic gears are widespread across various industries, such as automotive, robotics, consumer electronics, and healthcare. However, the process has some limitations and challenges that must be considered, such as cost, part complexity, and material properties. Overall, the future of plastic gear