Table of Contents:
- Introduction
- Components of Injection Moulding Diagram
- The Injection Moulding Process
- Types of Injection Moulding Machines
- Applications of Injection Moulding
- Advantages and Disadvantages of Injection Moulding
- Conclusion
-
1. Introduction
Injection moulding is a widely used manufacturing process that involves the creation of intricate and complex parts by injecting molten material into a mould. The process is widely used in various industries such as automotive, packaging, medical devices, and consumer goods. The injection moulding diagram is a critical component of the process, providing a visual representation of the process components, and enabling better understanding and control of the manufacturing process. In this article, we will explore the various components of the injection moulding diagram, the injection moulding process, types of injection moulding machines, applications, advantages and disadvantages, and the future of injection moulding technology.
-
2. Components of Injection Moulding Diagram
The injection moulding diagram comprises several components, including the injection unit, clamping unit, mould, ejection system, and cooling system.
The injection unit is responsible for heating and melting the material, typically plastic, and injecting it into the mould. The clamping unit is responsible for securing the mould in place and applying the necessary force to keep it closed during the injection process.
The mould is the cavity that creates the shape of the part being produced. It is typically made of steel or aluminum and is custom-designed for each specific part. The ejection system is responsible for ejecting the part from the mould once the injection process is complete. Finally, the cooling system is responsible for rapidly cooling the material to solidify the part and allow for easy ejection from the mould.
-
3. The Injection Moulding Process
The injection moulding process typically involves four main steps: clamping, injection, cooling, and ejection.
The first step in the process is clamping. The mould is securely clamped shut, and the injection unit and clamping unit work together to apply the necessary force to keep the mould closed during the injection process.
The second step is injection, where the plastic material is melted and injected into the mould cavity using the injection unit. The material is then allowed to cool and solidify.
The third step is cooling, where the cooling system rapidly cools the material to allow for easy ejection from the mould. The cooling time can vary depending on the material being used and the complexity of the part being produced.
The final step is ejection, where the part is ejected from the mould using the ejection system. The process then repeats for the production of additional parts.
-
4. Types of Injection Moulding Machines
There are several types of injection moulding machines, including hydraulic, electric, and hybrid machines.
Hydraulic injection moulding machines are the most common and widely used type. They use hydraulic pressure to power the injection process and are typically less expensive than other types of machines. Electric injection moulding machines use electric motors to power the injection process, making them more energy-efficient and environmentally friendly. Hybrid injection moulding machines combine the best features of both hydraulic and electric machines, providing a balance between power and efficiency.
-
5. Applications of Injection Moulding
Injection moulding is used in a wide range of industries, including automotive, packaging, medical devices, and consumer goods. In the automotive industry, injection moulding is used to produce various parts such as interior and exterior trims, engine components, and electrical parts. In the packaging industry, injection moulding is used to produce containers, bottles, and other packaging materials. In the medical industry, injection moulding is used to produce various medical devices such as syringes, catheters, and surgical instruments. In the consumer goods industry, injection moulding is used to produce various products such as toys, electronic components, and household appliances.
If you want more about Injection Moulding information ,You can click on the V1 Prototype website to find it.
-
6. Advantages and Disadvantages of Injection Moulding
Injection moulding has several advantages, including high production rates, the ability to create complex parts with precision and consistency, low labor costs, and minimal waste production. It is also a highly versatile process, allowing for the use of a wide range of materials, colors, and finishes.
However, injection moulding also has some disadvantages, such as the high initial cost of tooling and equipment, long lead times for tooling design and production, and the difficulty in making changes to the tooling once it has been created. Additionally, the process can be affected by environmental factors such as temperature and humidity, which can impact the quality and consistency of the parts being produced.
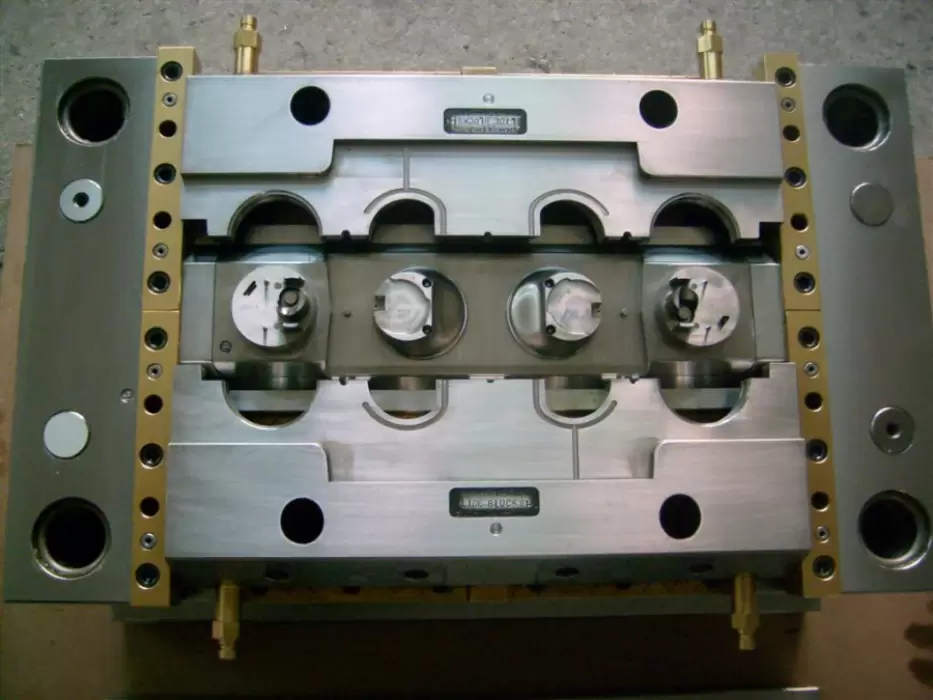
-
7. Conclusion
In conclusion, the injection moulding diagram is a critical component of the injection moulding process, providing a visual representation of the process components and allowing for better control and optimization of the manufacturing process. The process is widely used in various industries, producing complex and intricate parts with precision and consistency. While injection moulding has several advantages, it also has some drawbacks, making it important to carefully consider the process and its suitability for each specific application. Looking ahead, the future of injection moulding technology is bright, with continued advancements in materials, equipment, and process optimization expected to drive continued growth and innovation in the field.