Table of Contents:
- Introduction
- Injection Moulding Process
- Injection Moulding Materials
- Injection Moulding Applications
- Injection Moulding Advancements and Future Trends
- Advantages and Disadvantages of Injection Moulding
- Troubleshooting Injection Moulding Process
- Conclusion
-
1.Introduction
Injection moulding is a manufacturing process in which molten plastic or other materials are injected into a mould to create a finished product. The process is widely used in the production of a variety of products across different industries, from automotive and aerospace to consumer goods and medical devices.
The importance of injection moulding lies in its ability to produce high-quality, complex parts with excellent accuracy and consistency. The process allows for the creation of intricate designs and shapes that would be impossible to achieve using other manufacturing methods. Additionally, injection moulding is a highly efficient and cost-effective process, making it an ideal choice for mass production.
-
2.Injection Moulding Process
The injection moulding process typically consists of several stages: melting, injecting, packing, cooling, and ejection.
Here is a brief overview of each stage:
- Melting: The raw material, usually plastic pellets, is heated to its melting point in a hopper.
- Injecting: The molten material is then injected into a mould at high pressure through a nozzle.
- Packing: Once the mould is filled with molten plastic, pressure is applied to pack the material into the mould and ensure that it fills all the cavities.
- Cooling: The mould is then cooled to solidify the plastic and form the desired shape.
- Ejection: Finally, the mould is opened and the finished part is ejected.
There are several types of injection moulding machines, including:
- Hydraulic: This type of machine uses hydraulic power to clamp the mould and inject the plastic. It is the most common type of injection moulding machine.
- Electric: Electric machines use electric motors to power the clamping and injection systems, making them more energy-efficient than hydraulic machines.
- Hybrid: Hybrid machines combine hydraulic and electric systems to provide high performance and energy efficiency.
There are also several types of moulds used in injection moulding, including:
- Two-plate mould: This is the simplest and most common type of mould, consisting of two plates that separate to eject the finished part.
- Three-plate mould: A three-plate mould includes an additional plate that separates the runner system from the finished part, allowing for easier ejection.
- Hot runner mould: A hot runner mould uses a heated runner system to keep the plastic molten as it flows into the cavities, resulting in faster cycle times and reduced waste.
-
3.Injection Moulding Materials
Injection moulding can use a variety of materials, including thermoplastics, thermosets, and elastomers. Here is an overview of these materials:
- Thermoplastics: These materials are the most commonly used in injection moulding. They can be melted and re-melted without undergoing significant chemical changes, making them easy to recycle. Common thermoplastics used in injection moulding include polyethylene, polypropylene, and polystyrene.
- Thermosets: Unlike thermoplastics, thermosets cannot be re-melted once they have been formed. They are typically used in applications that require high heat resistance, such as electrical components and automotive parts. Common thermosets used in injection moulding include epoxy and phenolic resins.
- Elastomers: Elastomers are materials that can stretch and return to their original shape without breaking. They are commonly used in applications that require flexibility and durability, such as seals and gaskets. Common elastomers used in injection moulding include silicone and rubber.
Each material has its own unique properties and advantages, and the choice of material will depend on the specific requirements of the application. Factors such as strength, durability, heat resistance, and flexibility will all be considered when selecting a material for injection moulding.
-
4.Injection Moulding Applications
Injection moulding is used across a wide range of industries to manufacture a variety of products. Here are some common applications of injection moulding:
- Automotive Industry: Injection moulding is used to manufacture a wide range of automotive components, such as dashboards, bumpers, and interior trim. The process allows for the production of high-quality, complex parts with excellent durability and precision.
- Packaging Industry: Injection moulding is used to manufacture a variety of plastic packaging products, such as bottles, containers, and lids. The process allows for the creation of lightweight, strong, and versatile packaging solutions.
- Consumer Goods Industry: Injection moulding is used to manufacture a wide range of consumer products, such as toys, appliances, and household items. The process allows for the production of high-quality, intricate designs with excellent consistency and accuracy.
- Medical Industry: Injection moulding is used to manufacture a variety of medical devices, such as syringes, inhalers, and surgical instruments. The process allows for the creation of precise, sterile products with excellent durability and biocompatibility.
- Aerospace Industry: Injection moulding is used to manufacture a variety of aerospace components, such as interior panels, ducting, and seat frames. The process allows for the creation of lightweight, strong, and durable parts that can withstand extreme temperatures and conditions.
- Electrical and Electronics Industry: Injection moulding is used to manufacture a variety of electrical and electronic components, such as connectors, switches, and housings. The process allows for the production of high-quality, intricate designs with excellent consistency and accuracy, while also providing excellent electrical insulation and durability.
-
5.Injection Moulding Advancements and Future Trends
Injection moulding is a constantly evolving technology, with new advancements and trends emerging regularly. Here are some recent advancements and future trends in injection moulding:
- Industry Advancements: In recent years, injection moulding has seen advancements in areas such as process control, automation, and additive manufacturing. For example, the use of Industry 4.0 technologies, such as artificial intelligence and the internet of things, is helping to improve process efficiency, reduce waste, and increase product quality.
- Technological Advancements: Technological advancements in injection moulding include the use of 3D printing for tooling, the development of new materials with advanced properties, and the use of simulation software to optimize the injection moulding process. These advancements are helping to make the injection moulding process more efficient, cost-effective, and environmentally sustainable.
- Future Trends in Injection Moulding: One of the key trends in injection moulding is the development of sustainable materials and processes. This includes the use of biodegradable plastics, the recycling of post-consumer waste, and the development of closed-loop systems that minimize waste and energy use. Other trends include the use of multi-component injection moulding to create complex parts with multiple materials and colors, and the development of micro-injection moulding for the manufacture of small, precise parts.
As injection moulding continues to evolve, it is likely that we will see further advancements and innovations in the coming years, as the industry seeks to improve efficiency, reduce costs, and minimize its environmental impact.
Click on the V1 Prototype website to gain more Injection Molding Services information.
-
6.Advantages and Disadvantages of Injection Moulding
Injection moulding has several advantages and disadvantages that should be considered when selecting a manufacturing process. Here are some of the key advantages and disadvantages of injection moulding:
- Advantages of Injection Moulding:
- High production volumes can be achieved with excellent consistency and accuracy.
- Complex shapes and designs can be easily created.
- A wide range of materials can be used, with excellent properties and characteristics.
- Injection moulding is a highly automated process, which can help to reduce labor costs and increase efficiency.
- The process can be easily scaled up or down to meet changing production demands.
- Disadvantages of Injection Moulding:
- The upfront costs of tooling and equipment can be high.
- The process can be time-consuming, with long lead times for tooling and setup.
- The process can generate waste material and may require additional processing or disposal steps.
- The process may not be suitable for very small or very large parts, or for parts with very complex geometries.
- The process may require significant energy consumption and may have a higher environmental impact compared to other manufacturing processes.
Overall, the advantages of injection moulding make it a highly effective and versatile manufacturing process for a wide range of industries and applications. However, the high upfront costs and potential environmental impact should also be carefully considered when selecting a manufacturing process.
-
7.Troubleshooting Injection Moulding Process
Injection moulding is a complex process, and various problems can occur during the manufacturing process. Here are some common injection moulding problems and their causes and solutions:
- Common Injection Moulding Problems:
- Warpage and distortion of parts
- Surface defects, such as sink marks, flash, and weld lines
- Short shots, where parts are not fully formed
- Gate blush or blemishes near gate area
- Voids or empty spaces in parts
- Color variations or inconsistencies
- Burn marks or discoloration of parts
- Causes and Solutions of Injection Moulding Problems:
- Warpage and distortion: Caused by uneven cooling, inadequate wall thickness or incorrect material selection. Solutions include optimizing cooling, changing wall thickness or selecting appropriate material.
- Surface defects: Caused by excessive heat, mold damage, or issues with the material flow. Solutions include reducing heat, repairing molds, or adjusting flow rate.
- Short shots: Caused by incorrect injection pressure, insufficient material, or improper temperature settings. Solutions include increasing pressure, adding material, or adjusting temperature.
- Gate blush: Caused by improper gate design or excessive gate pressure. Solutions include redesigning gate, or reducing gate pressure.
- Voids: Caused by trapped gas or air pockets. Solutions include increasing the injection speed, increasing back pressure or adjusting temperature.
- Color variations: Caused by inconsistent mixing of colorants or materials. Solutions include verifying the colorant mixing process and ensuring proper proportion of colorants.
- Burn marks: Caused by excessive heat or resin degradation. Solutions include reducing the injection speed, reducing cycle time, or reducing melt temperature.
It is essential to address and troubleshoot these problems promptly to ensure the production of high-quality parts, reduce waste, and minimize downtime. Regular maintenance and inspection of equipment can also help to prevent injection moulding problems before they occur.
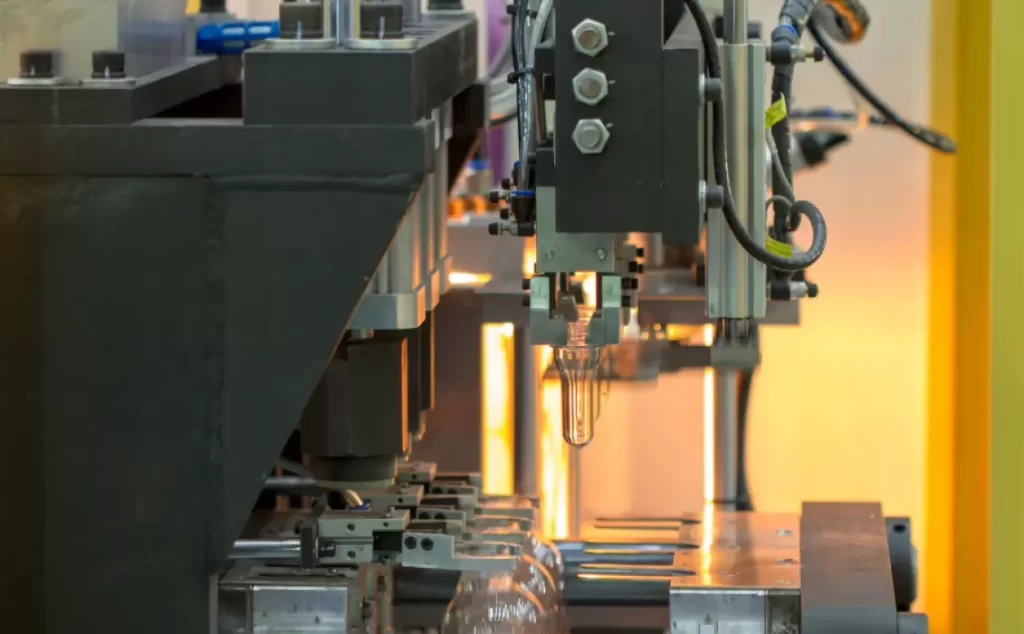
-
8.Conclusion
Injection moulding is a highly versatile and effective manufacturing process that has revolutionized the production of parts and products in various industries. The process involves the injection of molten material into a mould cavity, which then solidifies into the desired shape.
In this article, we have discussed the injection moulding process, types of machines and moulds used, various materials used, applications in different industries, advancements and future trends, advantages and disadvantages, and common troubleshooting problems.
Injection moulding offers several advantages, including high production volumes, accuracy, and consistency, while also having some disadvantages, such as high upfront costs and environmental impact. It is essential to consider these factors when selecting a manufacturing process.
The future outlook for injection moulding applications is promising, with the increasing demand for more complex and intricate parts in various industries. Technological advancements such as automation, robotics, and 3D printing are also likely to transform the injection moulding process in the future.
In conclusion, injection moulding has transformed the manufacturing industry, and with ongoing advancements, it is poised to continue to play a vital role in various industries.
Q1: What is the injection moulding process, and how does it work?
A1: The injection moulding process is a manufacturing technique used to produce plastic parts and products. It involves melting plastic materials (such as pellets) in an injection moulding machine and injecting the molten plastic into a custom-designed mould or cavity. Once the plastic cools and solidifies inside the mould, the part is ejected, and the process repeats. Injection moulding allows for high-volume production of complex and precise parts with minimal material wastage.
Q2: What are the common materials used in injection moulding, and how are they selected?
A2: Injection moulding utilizes a wide range of plastic materials, each with specific properties and applications. Common materials include polyethylene (PE), polypropylene (PP), polystyrene (PS), acrylonitrile-butadiene-styrene (ABS), and polyvinyl chloride (PVC), among others. The material selection depends on factors like the product's intended use, desired properties (e.g., flexibility, strength, transparency), and environmental considerations. Manufacturers carefully assess these factors to choose the most suitable material for the injection moulding process.
Q3: What are some recent advancements in injection moulding technology?
A3: Over the years, injection moulding technology has witnessed significant advancements to improve efficiency, precision, and sustainability. Some notable advancements include:
- Industry 4.0 Integration: Injection moulding machines equipped with smart sensors and connectivity to enable real-time monitoring and optimization of production processes.
- Multi-component Moulding: Simultaneously injecting different materials or colors into a single mould, enabling the production of complex and multi-layered parts.
- Micro-injection Moulding: Precisely manufacturing miniature parts, commonly used in medical devices and electronics.
- Sustainable Materials: The development of biodegradable and recycled plastic materials to reduce environmental impact.
Q4: What are common troubleshooting challenges in injection moulding, and how can they be addressed?
A4: Injection moulding can encounter various challenges during production. Some common troubleshooting issues include:
- Warping: When a part cools unevenly and distorts after ejection. Proper mould and cooling design can help reduce warping.
- Sink Marks: Indentations or depressions on the surface of a part due to uneven cooling. Adjusting processing parameters and material choice can mitigate sink marks.
- Flashing: Excess plastic material that protrudes from the parting line of the mould. Optimizing clamping force and maintaining precise mould dimensions can prevent flashing.
- Short Shots: When the molten plastic does not fully fill the mould cavity. This can be addressed by adjusting injection speed, temperature, or pressure.
Future Outlook: Injection moulding continues to be a dominant manufacturing process, and its future looks promising with ongoing technological advancements. The industry is likely to see further integration of automation and artificial intelligence, leading to more efficient and intelligent production systems. Additionally, the growing focus on sustainable materials and environmentally friendly practices will drive the development of eco-friendly plastics and recycling solutions, making injection moulding a greener and more sustainable manufacturing option.