Table of Contents:
- Introduction
- Designing Injection Molds
- Materials Used in Injection Mold Making
- Injection Mold Manufacturing Process
- Injection Mold Testing and Quality Control
- Maintenance and Repair of Injection Molds
- Advanced Injection Mold Making Technologies
- Applications of Injection Molds
- Conclusion
1.Introduction
Injection mold making is the process of manufacturing molds that are used to create plastic parts through the injection molding process. The molds are made from high-quality materials such as steel or aluminum and are designed to withstand the high pressures and temperatures involved in the injection molding process.
Injection mold making is an essential process in the manufacturing industry as it plays a critical role in the production of high-quality plastic parts. The quality of the mold is directly related to the quality of the final product, and a poorly made mold can result in defects, production delays, and increased costs.
The injection mold making process involves several stages, including designing the mold, selecting the right materials, manufacturing the mold, testing it, and maintaining and repairing it. Each stage of the process is crucial in ensuring the production of high-quality molds that meet the specific requirements of the manufacturing industry.
In the following sections, we will explore the importance of injection mold making in detail, including the benefits of using high-quality molds, the different types of molds, and the various stages involved in the injection mold making process. We will also discuss the importance of mold maintenance and repair and explore ways to reduce injection mold making costs. Finally, we will look at future trends in injection mold making, including advancements in technology and the impact of industry 4.0 on the mold making process.
-
2.Designing Injection Molds
Designing injection molds is a critical stage in the injection mold making process. The design of the mold will affect the quality of the final product, the manufacturing process, and the cost of production. In this section, we will explore the key considerations in designing injection molds and the different types of injection molds.
Key Considerations in Designing Injection Molds:
- Part design: The design of the plastic part to be molded is critical in determining the design of the mold. The part design will affect the complexity of the mold and the number of cavities required in the mold.
- Material selection: The selection of the right material for the mold is crucial in ensuring the mold’s longevity and durability. The material should be able to withstand the high pressures and temperatures involved in the injection molding process.
- Mold type: The type of mold used will depend on the part design, the material used, and the expected production volume. The most common types of molds are single-cavity molds, multi-cavity molds, and family molds.
- Mold layout: The layout of the mold will depend on the part design and the number of cavities required. The mold layout should be optimized to reduce material waste and ensure efficient cooling of the mold.
- Injection molding machine selection: The selection of the right injection molding machine is critical in ensuring the proper functioning of the mold. The machine should be able to apply the required pressure and temperature to the mold.
Types of Injection Molds:
- Single-cavity molds: Single-cavity molds are used to produce a single part at a time. They are suitable for low-volume production and are often used for prototyping.
- Multi-cavity molds: Multi-cavity molds are used to produce multiple parts at a time. They are suitable for high-volume production and can produce identical parts with high precision.
- Family molds: Family molds are used to produce multiple parts that are similar in shape and size. They are suitable for high-volume production and can produce multiple parts in a single molding cycle.
- Hot runner molds: Hot runner molds use a heating system to keep the plastic material in the runner system in a molten state. This allows for faster production cycles and reduces material waste.
- Cold runner molds: Cold runner molds use a runner system that is not heated, resulting in longer cycle times and more material waste.
-
3.Materials Used in Injection Mold Making
Materials used in injection mold making play a critical role in the quality and durability of the mold. The materials should be able to withstand the high pressures and temperatures involved in the injection molding process while maintaining their shape and accuracy. In this section, we will explore the common materials used in injection mold making and the selection criteria for injection mold materials.
Common Materials Used in Injection Mold Making:
- Steel: Steel is the most common material used in injection mold making due to its durability, strength, and ability to maintain accuracy over time. The most common types of steel used are P20, H13, and S7.
- Aluminum: Aluminum is a lightweight and highly conductive material that is suitable for low-volume production or prototyping. It is less durable than steel and is prone to wear and tear over time.
- Copper alloys: Copper alloys are highly conductive and have excellent thermal conductivity, making them suitable for molds that require fast cooling. They are also highly resistant to corrosion.
- Beryllium copper: Beryllium copper is a highly durable and corrosion-resistant material that is suitable for molds that require high precision and accuracy.
- Ceramic: Ceramic materials are highly resistant to wear and corrosion, making them suitable for molds that require high precision and accuracy. However, they are expensive and can be brittle.
Selection Criteria for Injection Mold Materials:
- Material properties: The material used should have the necessary properties to withstand the high pressures and temperatures involved in the injection molding process. The material should also be able to maintain its accuracy and shape over time.
- Part design: The material used should be suitable for the specific part design, including the complexity and size of the part.
- Production volume: The material used should be able to withstand the expected production volume. For high-volume production, more durable materials such as steel or beryllium copper may be required.
- Budget: The cost of the material used should be considered when selecting injection mold materials. While more expensive materials such as steel or beryllium copper may be more durable, they may not be cost-effective for low-volume production or prototyping.
- Maintenance: The maintenance requirements of the mold should be considered when selecting injection mold materials. Materials that are prone to wear and tear may require more frequent maintenance and repair.
-
4.Injection Mold Manufacturing Process
Injection mold manufacturing is a complex process that involves several steps and techniques to produce high-quality molds. In this section, we will explore the steps involved in the injection mold manufacturing process and the techniques used.
Steps in Injection Mold Manufacturing Process:
- Design: The first step in the injection mold manufacturing process is to create a design for the mold. The design includes specifications for the part, including the size, shape, and material, as well as the mold design.
- Tooling: Once the design is finalized, the next step is to create the tooling. Tooling involves creating a mold base, cavity, and core. The mold base is the foundation of the mold, while the cavity and core are used to create the shape of the part.
- Machining: After the tooling is created, the mold components are machined to their final dimensions. This involves using computer-controlled machines such as CNC milling machines, lathes, and EDM machines to create the precise shapes and features required for the mold.
- Polishing and Texturing: Once the components are machined, they are polished and textured to create the desired surface finish on the molded part.
- Assembly: The components of the mold are then assembled and fitted together. This involves inserting the cavity and core into the mold base and attaching the necessary components such as ejector pins, slides, and cooling channels.
- Testing: The final step in the injection mold manufacturing process is testing. The mold is tested to ensure that it is functioning correctly and producing parts to the required specifications.
Injection Mold Manufacturing Techniques:
- Conventional Injection Molding: This is the most common injection molding technique, where the material is melted and injected into the mold under high pressure.
- Gas-Assisted Injection Molding: This technique involves injecting a gas into the mold to hollow out the part and reduce material usage.
- In-Mold Decorating: This technique involves applying a decorative film or label to the mold before injection molding to create a finished part with a pre-printed design.
- Insert Molding: This technique involves inserting a pre-formed component, such as a metal insert, into the mold before injection molding to create a finished part with added features.
-
5.Injection Mold Testing and Quality Control
Injection mold testing and quality control are essential steps in the injection mold manufacturing process to ensure that the molds produce high-quality parts consistently. In this section, we will explore the importance of injection mold testing, the types of testing performed, and the quality control measures used.
Importance of Injection Mold Testing:
Injection mold testing is essential to ensure that the mold produces parts that meet the required specifications. Testing allows manufacturers to identify any defects or issues with the mold before it is put into production. This helps to minimize scrap and rework and ensures that the parts produced are of high quality.
Types of Injection Mold Testing:
- First Article Inspection: This involves testing the first part produced by the mold to ensure that it meets the required specifications.
- Dimensional Testing: This involves measuring the dimensions of the parts produced by the mold to ensure that they meet the required tolerances.
- Material Testing: This involves testing the material used in the mold to ensure that it meets the required specifications.
- Flow Analysis: This involves simulating the flow of the material through the mold to identify any potential issues that may affect the quality of the parts produced.
- Mold Function Testing: This involves testing the function of the mold, such as the opening and closing of the mold and the ejection of the parts.
Quality Control Measures for Injection Molds:
- Regular Maintenance: Regular maintenance of the mold is essential to ensure that it operates correctly and produces high-quality parts consistently.
- Inspection and Testing: Regular inspection and testing of the mold can help identify any defects or issues that may affect the quality of the parts produced.
- Material Selection: Careful selection of the material used in the mold is essential to ensure that it meets the required specifications and produces high-quality parts.
- Documentation: Proper documentation of the mold and the production process can help ensure that the mold is consistently producing high-quality parts.
-
6.Maintenance and Repair of Injection Molds
Maintenance and repair are crucial aspects of the injection mold manufacturing process that ensure the mold’s longevity and consistent production of high-quality parts. In this section, we will explore the importance of maintenance and repair, common issues with injection molds, and the steps involved in repairing them.
Importance of Maintenance and Repair:
Injection molds are subjected to high pressures, temperatures, and mechanical stresses during the injection molding process, which can cause wear and tear over time. Regular maintenance and repair can help identify and fix any issues before they become major problems that could affect the mold’s performance and produce subpar parts.
Common Issues with Injection Molds:
- Wear and Tear: Over time, the mold’s components, such as the cavity and core, can wear out, causing defects in the parts produced.
- Parting Line Issues: Parting line issues, such as flashing or incomplete filling of the mold, can occur due to misalignment or damage to the mold components.
- Warping: Warping of the mold can occur due to uneven heating or cooling of the mold, causing the parts produced to have deformities.
Steps in Repairing Injection Molds:
- Identify the Issue: The first step in repairing an injection mold is to identify the problem through inspection and testing.
- Disassemble the Mold: The mold must be disassembled to access the damaged components.
- Repair or Replace the Components: Depending on the issue, the damaged components can be repaired or replaced.
- Reassemble the Mold: After the components are repaired or replaced, the mold is reassembled and tested.
- Final Inspection: A final inspection is performed to ensure that the mold is functioning correctly and producing high-quality parts.
-
7.Advanced Injection Mold Making Technologies
Injection mold making technology has come a long way since its inception, and advancements continue to emerge. In this section, we will explore the emerging trends in injection mold making and the latest advancements in injection mold making technologies.
Emerging Trends in Injection Mold Making:
- 3D Printing: 3D printing is rapidly emerging as a valuable tool in injection mold making. The technology allows for faster prototyping and manufacturing of complex geometries.
- Additive Manufacturing: Additive manufacturing, also known as 3D printing, can also be used to produce high-quality injection molds. This technology allows for the production of molds with conformal cooling channels, which can increase the mold’s lifespan and improve part quality.
- Automation: Automation technology is being implemented in injection mold making to increase efficiency and reduce labor costs. Robotics and other automated systems are being used to automate processes such as mold assembly and quality control.
Advancements in Injection Mold Making Technologies:
- Hot Runner Systems: Hot runner systems have been used in injection molding for decades, but recent advancements have made them more efficient and reliable. Hot runner systems help reduce material waste and increase cycle times, resulting in higher productivity and lower costs.
- Simulation Software: Simulation software is becoming increasingly popular in injection mold making, allowing manufacturers to simulate the injection molding process and identify potential issues before production. This technology helps reduce the time and cost associated with trial and error.
- High-Speed Machining: High-speed machining technology is being used to produce injection molds faster and more efficiently. This technology allows for the production of molds with complex geometries and surface finishes, which were previously impossible or difficult to achieve.
- In-Mold Decorating: In-mold decorating is an emerging technology that allows for the production of parts with a decorative finish during the injection molding process. This technology eliminates the need for post-molding finishing, reducing production time and cost.
Click on the V1 Prototype website to gain more Injection Molds information.
-
8.Applications of Injection Molds
Injection molding is a versatile manufacturing process that is used in a wide range of industries and for a variety of applications. In this section, we will explore the industries that use injection molds and the common products made with injection molds.
Industries that use Injection Molds:
- Automotive Industry: Injection molding is used extensively in the automotive industry for the production of interior and exterior parts, such as dashboards, bumpers, and door panels.
- Medical Industry: Injection molding is used in the medical industry for the production of surgical instruments, drug delivery devices, and diagnostic equipment.
- Consumer Goods Industry: Injection molding is used in the production of a wide range of consumer goods, such as toys, household appliances, and electronics.
- Packaging Industry: Injection molding is used in the packaging industry for the production of bottles, caps, and containers.
Common Products Made with Injection Molds:
- Bottles: Injection molding is commonly used in the production of bottles for the packaging industry. These bottles can be made from a variety of materials, including PET, HDPE, and PVC.
- Toys: Injection molding is used extensively in the production of toys, such as action figures, dolls, and building blocks.
- Electronic Components: Injection molding is used in the production of electronic components, such as computer keyboard keys, phone cases, and chargers.
- Medical Devices: Injection molding is used in the production of medical devices, such as syringes, IV bags, and catheters.
- Automotive Parts: Injection molding is used in the production of automotive parts, such as bumpers, dashboards, and door panels.
- Household Items: Injection molding is used in the production of a wide range of household items, such as kitchen utensils, storage containers, and cleaning tools.
-
9.Conclusion
Injection mold making is a critical process in modern manufacturing, providing a cost-effective and efficient method for producing high-quality parts in large quantities. In this article, we have explored the various aspects of injection mold making, including the design process, materials selection, manufacturing techniques, testing, and quality control.
We have also highlighted the importance of maintenance and repair of injection molds and the emerging trends and advancements in injection mold making technologies.
Finally, we have looked at the applications of injection molds in various industries, such as automotive, medical, consumer goods, and packaging, and the common products produced with injection molding.
In conclusion, injection mold making is a vital technology that plays a significant role in modern manufacturing. By understanding the key considerations and best practices in injection mold making, manufacturers can produce high-quality parts at a lower cost and stay competitive in today’s global market. The future of injection mold making looks promising, with advancements in technology and materials that will continue to improve the efficiency and effectiveness of this critical process.
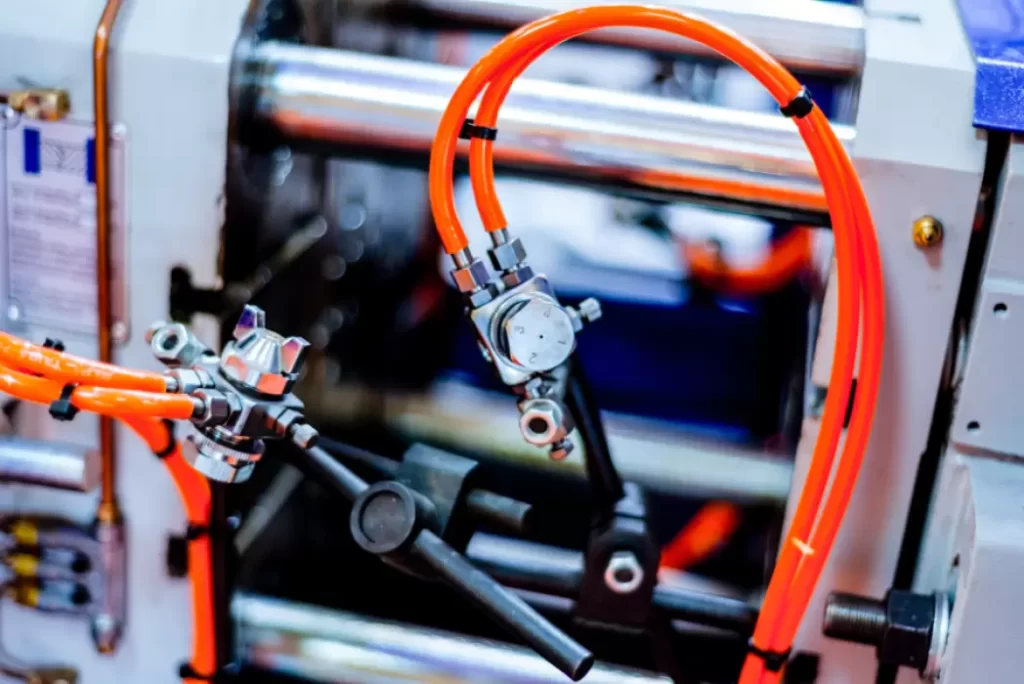
Injection mold making is a complex process that requires precision, skill and experience. Injection molds are used to produce plastic parts with intricate shapes and features, such as medical devices, automotive components, consumer products and more. Injection molds are composed of two or more parts that fit together to form a cavity where molten plastic is injected and cooled. The quality of the injection mold affects the quality of the plastic part, as well as the production efficiency and cost.
To manufacture high-quality injection molds, several steps are involved:
- Design: The injection mold design is based on the specifications of the plastic part, such as dimensions, geometry, material, function and appearance. The injection mold design also considers factors such as mold flow analysis, cooling system, ejection system, venting system, runner system and gate location. The injection mold design is usually done using computer-aided design (CAD) software and validated using computer-aided engineering (CAE) software.
- Material selection: The injection mold material is chosen according to the properties of the plastic part, such as strength, hardness, wear resistance, corrosion resistance and thermal expansion. The injection mold material also affects the mold life and maintenance. Common injection mold materials include steel, aluminum, copper and brass.
- Machining: The injection mold parts are machined using various tools and techniques, such as milling, drilling, turning, grinding, EDM and CNC machining. The machining process must ensure high accuracy and surface finish of the injection mold parts.
- Assembly: The injection mold parts are assembled together using screws, pins, springs and other components. The assembly process must ensure proper alignment and fit of the injection mold parts.
- Testing: The injection mold is tested for functionality and quality before mass production. The testing process may include trial runs, dimensional inspection, pressure testing, leak testing and defect analysis.
- Maintenance: The injection mold is maintained regularly to ensure optimal performance and durability. The maintenance process may include cleaning, lubricating, repairing and replacing worn or damaged parts.