Table of Contents:
- Introduction
- Mold Design Considerations
- Mold Flow Analysis and Simulation
- Advanced Mold Design Techniques
- Mold Maintenance and Repair
- Trends in Injection Mold Design
- Conclusion
-
1.Introduction
Injection mold design is a critical aspect of production, where the right mold design is essential for producing high-quality components that meet the required specifications. Poor mold design can lead to defects, inconsistencies, and even failures in the production process. This article will outline the importance of proper mold design and how it can impact the production process positively.
Efficient mold design ensures that the production process runs smoothly, with the molds performing their intended function without fail. The mold design process aims to achieve a balance between simplicity and complexity. The design should be simple enough to produce efficiently and effectively, while also being complex enough to meet the required part functionality and durability.
In conclusion, the proper design of molds highlights the importance of optimizing the injection molding process to achieve maximum efficiency, product quality, and production cost reduction. The investment in efficient mold design and fabrication often results in significant savings during the production process’s lifetime. The importance of continuous improvement in mold design cannot be overemphasized, and with advances in engineering, new technologies facilitate the production of highly efficient and durable molds.
-
2.Mold Design Considerations
Proper mold design is crucial for effective manufacturing of high-quality components. Key considerations for mold design include design for manufacturability, mold materials selection, component design considerations, mold tooling and manufacturing processes, and surface finishes and texturing.
Design for Manufacturability:Design for manufacturability (DFM) is an important consideration in mold design. DFM focuses on designing the mold for the most efficient and cost-effective production process. This includes reducing the complexity of the design while meeting functional and aesthetic requirements. By optimizing the mold design for manufacturability, manufacturers can reduce production time, minimize material waste, and increase efficiency.
Mold Materials Selection:Mold materials selection is a crucial consideration in mold design. Common types of mold materials include steel, aluminum, and beryllium copper, and the choice of the material depends on various factors such as part geometry, material compatibility, and production volume. The selected mold material should have corrosion and wear resistance, dimensional stability under varying temperatures, and minimal warpage during production. An optimal material selection reduces mold maintenance and repair costs while improving mold durability and production efficiency.
Component Design Considerations:Component design considerations take into account the factors that influence the ease of manufacturing molded components. These considerations include draft angles, parting line placement, gate placement, and ejection systems. The proper design of these components ensures efficient production and reduces the likelihood of defects. The design must take into account both the functional requirements and the aesthetic aspects of the final components.
Mold Tooling and Manufacturing Processes:The tooling and manufacturing processes determine the efficiency and cost-effectiveness of the mold design. Mold tooling should be designed to achieve the desired part geometry and appropriate functioning. Computer-controlled machining and precision manufacturing help to increase the accuracy and efficiency of mold production. Processes such as injection molding require proper cooling channels, ejection systems, and gating systems to be designed for efficient and consistent mold performance.
Surface Finishes and Texturing:Surface finishes and texturing are essential considerations in mold design, adding both aesthetic and functional value to the final components. Proper surface finishes and texturing help to avoid defects such as warpage, improving the appearance, and increasing the component’s wear resistance. Mold response should be considered when designing for polishing to avoid degradation of mold performance.
In conclusion, proper mold design plays a crucial role in efficient production and high-quality components. Design for manufacturability, mold materials selection, component design considerations, mold tooling and manufacturing processes, and surface finishes and texturing are vital considerations in mold design for achieving efficient and effective manufacturing of high-quality components. By taking these considerations into account, manufacturers can increase efficiency, reduce production costs, and improve the final product quality.
-
3.Mold Flow Analysis and Simulation
Mold flow analysis and simulation are essential tools in mold design and production. The process uses specialized software and techniques to simulate and test the mold’s performance, allowing for improved design, production, and quality control.
Why Mold Flow Analysis is Important:Mold flow analysis is important because it allows for the identification of potential defects and optimization of the mold design before production. This ensures that the final product meets the necessary quality standards while reducing waste, production time, and overall costs.
Mold flow analysis also helps to identify critical aspects of the mold design, such as gate location, gate type, and cooling channel design. This type of analysis allows for the optimization of the mold’s design to ensure uniform filling throughout the cavity and efficient cooling during the production process.
Finite Element Analysis and Mold Simulation Software:Mold flow analysis uses finite element analysis and simulation software to simulate and test the performance of the mold design. Finite element analysis is a computer-based technique that researches the behavior of complex systems by breaking them down into smaller, more manageable elements. This allows for a more detailed analysis of potential issues that may arise during production, helping to improve mold design.
Mold simulation software utilizes finite element analysis to simulate the behavior of molten plastic during the production process. This software helps to predict the fluid flow rate, pressure, temperature, and cooling effects to optimize gate and cooling channel location, managing warpage and optimize cavity packing.
Benefits of Mold Flow Analysis:Mold flow analysis offers a wide range of benefits for mold design and production. By simulating the production process before the actual production, mold flow analysis helps to identify defects and their root causes, allowing for design optimization before production, reducing production costs of corrective action and producing quality products.
Using mold flow analysis and simulation software as a quality control method can result in more efficient production cycles, improved product quality, and overall cost savings. Improved cycle times and reduced waste represent saving directly impacting production costs, while the ability to predict potential issues helps reduce production time and lead to increased customer satisfaction.
In conclusion, mold flow analysis and simulation software are essential tools in mold design and production. The analysis process helps identify potential design flaws, optimization of designs, and how to troubleshoot product issues in real time. The benefits of using mold flow analysis and simulation are clear and allow for efficient and effective production, improved product quality, and reduced production costs in the long term, leading to better customer satisfaction.
-
4.Advanced Mold Design Techniques
Advanced mold design techniques offer new possibilities for injection molding production, allowing for more complex, multi-functional design elements, and enhanced production techniques. The following sections outline a few advanced mold design techniques: multi-cavity and family molds, hybrid and overmolds, hot runner systems, and in-mold decoration.
Multi-Cavity and Family Mold:Multi-cavity molds allow manufacturers to produce multiple components in a single injection cycle. Multiple cavities placed inside a mold can be identical or designed to manufacture different parts simultaneously. This technique increases efficiency, reduces production cycles, and is cost-effective. Family molds are similar to multi-cavity molds, allowing for the production of different parts with the same mold; this requires the tool to have features to cater to different parts but with a common approach. The resulting molds have a longer lifespan since the individual cavities undergo less wear and tear than individually created molds for specific parts.
Hybrid and Overmolds:Hybrid and overmolding involve the use of multiple materials or colors in a single mold. This technique can create functional components that combine the benefits of different materials or multiple aesthetic features such as multiple colors, textures, and transparency. This allows for more complex and multi-functional designs, usually for parts requiring a complex sealing function or visible features.
Hot Runner Systems:Hot runner systems are intricate technologies designed to retain heat in the runner system utilized to feed the molten material to the cavity. Hot runner systems allow the mold to maintain a stable temperature, reducing the need for additional heating and cooling cycles. Due to the lower risk of cooling contraction in the runners, Hot runner systems enable the production of larger or thicker parts, with high precision and consistency.
In-Mold Decoration:In-mold decoration involves embedding decorative features within the mold during production. These features could be logos, textures, or information pertaining to the part being produced. Integrating decorative elements in the mold reduces the time and cost of post-production. In-mold decoration offers high quality, detail, and consistency across mass production.
In conclusion, advanced mold design techniques offer limitless possibilities for injection molding production. These techniques enhance production efficiency, material savings reducing production time, and labor cost. Multi-cavity and family molds, hybrid and overmolding, hot runner systems, and in-mold decoration expand the opportunities for complex designs, multi-functional parts, and production of aesthetic features in one production cycle. Using these advanced techniques to improve part characteristics will benefit manufacturers resulting in better products and higher customer satisfaction.
If you want more about Injection Mold information ,You can click on the V1 Prototype website to find it.
-
5.Mold Maintenance and Repair
Effective mold maintenance and repair play important roles in producing quality components and extending the life of the mold. Neglecting mold maintenance and repair can lead to significant downtime for repairs, affect product quality, and increase production costs. The following sections will discuss the importance of mold maintenance, common mold issues and their causes, and repair techniques in injection mold production.
Importance of Mold Maintenance:Molds are complex machines and, like any other machine, require periodic maintenance to operate at optimal levels. Mold maintenance is necessary to identify, repair, and prevent issues that can result in production downtime, component defects, and increased production costs. Regular mold maintenance ensures that the mold is working at its best, producing optimally performing and consistent quality components.
Common Mold Issues and Their Causes:Common issues that can arise in mold manufacturing include flash, warping, base/plate cracking, fatigue/pitting, rust, wear or damage to slides, subgates, and ejector pins. Critical causes of these deficiencies include wear and tear due to prolonged use, excessive heat, or moisture that might cause corrosion & pitting, aging, inadequate maintenance or daily upkeep, and incorrect material selection.
Repair Techniques:Various techniques can be utilized to efficiently restore molds to their original state, including maintenance and minor repairs, repairs to gauge dimensions involving polish after repair, and repairs involving welding, milling, and even coatings designed to improve their durability. Welding is commonly used to repair in cases of related material selection, while Texturing and polishing increase durability and functionality of complex molds.
The repair process begins with an inspection of the mold, isolating the defective parts and identifying problems. Depending on the nature of the repair, the areas to be repaired will be carefully prepared, removing damaged parts and restoring them to their original dimensions or with modifications. After the repair, the mold is tested extensively to ensure it operates according to specifications and meets the required standards.
In conclusion, effective mold maintenance and repair ensure that molds operate reliably, optimally, and last longer. Manufacturers should establish a maintenance and repair schedule to ensure that inconsistencies or defects are diagnosed, isolated, and repaired before they become critical issues. Prompt repairs, adequate daily upkeep, regular maintenance, and vigilant inspections reduce downtime, guarantee consistency and quality, and increase in productivity for molds throughout their life.
-
6.Trends in Injection Mold Design
Injection mold design is an ever-evolving industry that continues to see trends towards improved efficiency, performance, quality, and reduced costs. The following sections outline some of the latest trends in injection mold design, including the adoption of modular mold design, material and manufacturing advancements, and the application of smart systems and new technologies in the field.
Modular Mold Design:Modular mold design is becoming increasingly popular in the industry as it offers increased flexibility and versatility for designers, improved production efficiency, and reduced costs. Modular mold design allows for the use of a base mold with interchangeable features to enable manufacturers to create different parts with minimal tooling changes in a shorter timeframe. The versatility of this design allows for customization of the mold to suit multiple production runs and maximize the compatibility of the mold with different product runs.
Material and Manufacturing Advancements:Material and manufacturing advancements directly impact mold design and shape the ability to create high-quality parts cost-effectively. Available technologies are advancing to provide new possibilities in manufacturing, with a key focus on more sustainable, higher-performing, and more efficient production. New materials, such as bio-polymers, composites, and even recycled polymers, open a wide range of new possibilities for designers, offering environmental benefits and reduced production costs.
Application of Smart Systems and New Technologies:Integrating smart systems, automation, and advanced manufacturing technologies into injection mold design continues to transform how molds are designed and manufactured, such as sensors, robotic arms or artificial intelligence. Smart systems and new technologies offer enhanced precision, speed, and reduce the manual labor required to produce molds, resulting in more efficient and accurate manufacturing while reducing error. Smart systems, such as data analysis, help predict production cycles, optimize manufacturing methods, improve quality control, and increase production efficiency.
In conclusion, mold design is an ever-changing industry with trends towards more efficient manufacturing, improved quality, and reduced costs. Modular mold design, the adoption of new materials and manufacturing technologies, and the application of smart systems to mold design and production, are some of the latest trends in the industry. These trends have resulted in new possibilities, reduced waste, increased efficiency, enhanced quality, and responding to customer needs, allowing the industry to be more competitive and sustainable. The future of mold design is going to become an even more exciting journey with a focus on innovation to provide high-quality products efficiently and cost-effectively.
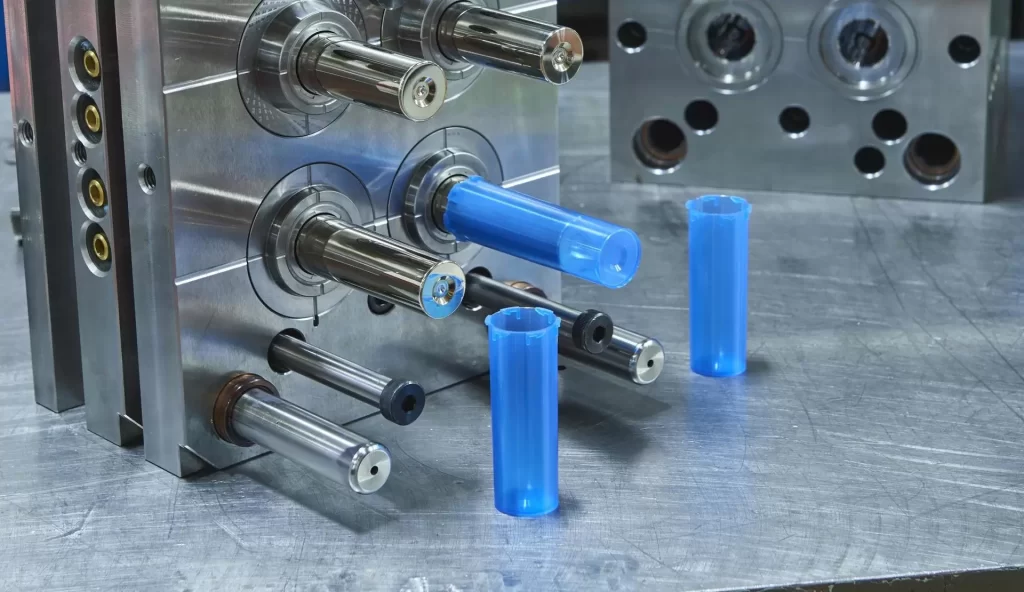
-
7.Conclusion
Injection mold design is a critical component of the manufacturing process that plays an important role in the production of high-quality, efficient, and cost-effective components. In this article, we have covered various aspects of injection mold design, including mold design fundamentals, mold flow analysis and simulation, advanced mold design techniques, mold maintenance and repair, and trends in injection mold design.
Recap of Key Points:Injection mold design involves several aspects, including mold design fundamentals, mold flow analysis and simulation, advanced mold design techniques, mold maintenance and repair, and trends in injection mold design. Key points worth noting include the importance of proper mold design to reduce cost, increase efficiency and produce high-quality parts. Maintenance and repair are essential to maintaining the sound working condition of molds, reducing downtime, and ensuring the quality of production.
Implications for the Future of Injection Mold Design:The future of injection mold design focuses on incorporating new technologies and materials to improve efficiency, sustainability, and production quality while reducing downtime and cost. The integration of smarter systems and Artificial Intelligence (AI) helps to save time, minimize waste while boosting the overall efficiency of the production process.
Final Thoughts:Injection mold design is a critical aspect of injection molding, demanding expertise and care to ensure the production of high-quality components. As we move towards an era of smarter production and sustainable manufacturing, there is bound to be a deeper focus on new technologies informing the future of injection mold design, reducing downtime, increasing efficiency, enhancing precision, and reducing costs. As such, the mold design and manufacturing industries shall continue to remain critical to the manufacturing industry as a whole.