Table of Contents:
- Introduction
- Manufacturing Process of High Precision Milled Parts
- Applications of High Precision Milled Parts
- Quality Control of High Precision Milled Parts
- Advancements in High Precision Milling
- Challenges in High Precision Milling
- Conclusion
-
1.Introduction
High precision milled parts refer to components that are manufactured using milling machines to achieve very tight tolerances and precise specifications. These parts are typically used in applications where accuracy, consistency, and repeatability are critical.
High precision milled parts play a crucial role in many industries, including aerospace, medical devices, electronics, automotive, and many others. In aerospace, for example, high precision milled parts are used in critical components such as engines, landing gear, and control systems. In the medical industry, high precision milled parts are used in surgical instruments, implants, and diagnostic equipment. In electronics, high precision milled parts are used in microelectronics, circuit boards, and other electronic devices. The use of high precision milled parts helps to improve product performance, reduce costs, and increase efficiency.
-
2.Manufacturing Process of High Precision Milled Parts
The manufacturing process of high precision milled parts involves several steps, including CNC machining, tooling and fixturing, and quality control measures.
CNC Machining:
CNC (Computer Numerical Control) machining is a manufacturing process that uses computerized controls and machines to produce high precision milled parts. CNC machines are programmed to execute specific instructions for cutting, drilling, and milling operations, which results in precise and repeatable outcomes. The use of CNC machining technology enables manufacturers to achieve high accuracy and precision while reducing the likelihood of human error.
Tooling and Fixturing:
Tooling and fixturing are essential aspects of the high precision milling process. Tooling refers to the cutting tools used to remove material from the workpiece, while fixturing refers to the methods used to hold the workpiece in place during milling. The selection of appropriate tooling and fixturing is critical to achieving high precision results. High-quality tooling and fixturing can improve the stability and accuracy of the milling process, reduce vibration, and increase the lifespan of the cutting tools.
Quality Control Measures:
Quality control measures are an essential part of the manufacturing process for high precision milled parts. Quality control measures may include inspection techniques such as coordinate measuring machines (CMMs), laser scanners, and vision systems. Quality control measures may also involve statistical process control (SPC), which is used to monitor and control the manufacturing process to ensure that parts are consistently produced within specified tolerances. The use of quality control measures helps to ensure that high precision milled parts meet the required specifications and performance requirements.
-
3.Applications of High Precision Milled Parts
Aerospace:
In the aerospace industry, high precision milled parts are used in critical components such as engines, landing gear, and control systems. These parts must meet stringent quality and performance requirements to ensure the safety and reliability of aircraft. High precision milled parts are also used in the production of satellites, rockets, and unmanned aerial vehicles (UAVs).
Medical Devices:
High precision milled parts are used extensively in the medical device industry, where they are used to produce surgical instruments, implants, and diagnostic equipment. These parts must meet strict regulatory requirements and must be produced with biocompatible materials to ensure patient safety.
Electronics:
High precision milled parts are used in the production of microelectronics, circuit boards, and other electronic devices. These parts must meet precise specifications to ensure the reliable operation of electronic devices.
Automotive Industry:
High precision milled parts are used in the automotive industry to produce critical components such as engines, transmissions, and chassis. These parts must meet stringent quality and performance requirements to ensure the safety and reliability of vehicles.
Others:
High precision milled parts are also used in a range of other industries, including defense, energy, and industrial automation. They are used to produce a wide range of components, including bearings, gears, shafts, and housings, among others.
-
4.Quality Control of High Precision Milled Parts
Quality control is critical to ensuring that high precision milled parts meet the required specifications and performance requirements. The quality control of high precision milled parts can be achieved through several methods, including inspection techniques, metrology equipment, and adherence to ISO standards.
Inspection Techniques:
Inspection techniques are used to evaluate the quality of high precision milled parts. Common inspection techniques include visual inspection, dimensional measurement, and non-destructive testing. Visual inspection is used to identify surface defects or imperfections that can affect the performance of the part. Dimensional measurement is used to verify that the part meets the required specifications. Non-destructive testing is used to detect internal defects or imperfections that cannot be detected by visual inspection.
Metrology Equipment:
Metrology equipment is used to measure the dimensions and features of high precision milled parts. Common metrology equipment includes coordinate measuring machines (CMMs), optical comparators, and laser scanners. CMMs are used to measure the three-dimensional coordinates of the part, while optical comparators and laser scanners are used to measure the dimensions and features of the part.
ISO Standards:
Adherence to ISO (International Organization for Standardization) standards is critical to ensuring the quality of high precision milled parts. ISO standards provide guidelines for quality management, quality assurance, and quality control, and can help manufacturers ensure that their processes and products meet the required standards. Adherence to ISO standards can also help manufacturers improve their processes and reduce costs.
-
5.Advancements in High Precision Milling
Advancements in high precision milling have enabled manufacturers to achieve even greater levels of accuracy and precision. Some of the recent advancements in high precision milling include:
Nanomachining:
Nanomachining is a type of high precision milling that involves the fabrication of structures and features with dimensions of less than 100 nanometers. Nanomachining requires specialized equipment and techniques, such as electron beam lithography and focused ion beam milling, and is used in a wide range of applications, including nanoelectronics, photonics, and biomedical engineering.
Micro Milling:
Micro milling is a type of high precision milling that involves the production of small features and structures with dimensions in the range of 1 to 100 micrometers. Micro milling requires specialized equipment and techniques, such as high-speed spindles and ultra-precise cutting tools, and is used in a wide range of applications, including microfluidics, MEMS (Micro-Electro-Mechanical Systems), and optical components.
Hybrid Machining:
Hybrid machining is a type of high precision milling that combines two or more machining processes to achieve greater levels of accuracy and precision. Hybrid machining can involve the combination of milling with other processes such as laser machining, electrochemical machining, or ultrasonic machining. Hybrid machining is used in a range of applications, including aerospace, medical devices, and microelectronics.
-
6.Challenges in High Precision Milling
Despite the many advantages of high precision milling, there are also several challenges that manufacturers face in this process. Some of the main challenges in high precision milling include:
Material Selection:
The selection of materials for high precision milling can be a challenge, as the properties of the material can affect the machinability and the accuracy of the milling process. Some materials, such as alloys and composites, can be difficult to machine and may require specialized tooling and techniques.
Tool Wear:
Tool wear is a common challenge in high precision milling, as the cutting tools used in the process are subjected to high forces and temperatures. Tool wear can lead to reduced accuracy and surface finish, as well as increased tool replacement costs. Manufacturers must carefully select cutting tools and machining parameters to minimize tool wear and ensure consistent performance.
Surface Finish:
Achieving a high-quality surface finish is critical in high precision milling, as the surface finish can affect the performance and reliability of the final product. Achieving a high-quality surface finish can be a challenge, as it depends on a range of factors, including the cutting tool geometry, cutting speed, and feed rate.
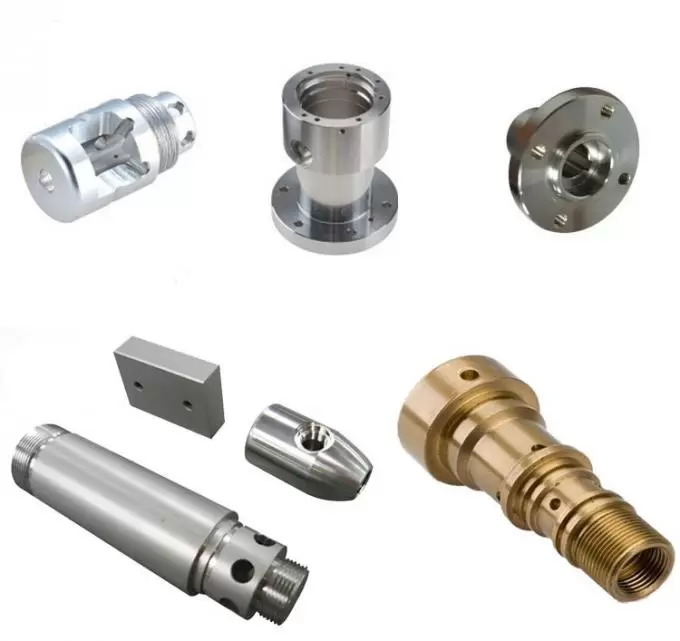
-
7.Conclusion
High precision milled parts play a critical role in a range of industries, including aerospace, medical devices, electronics, and automotive. As advancements in technology continue to drive demand for higher precision and greater complexity, the importance of high precision milling will only continue to grow.
In order to achieve the required level of precision, it is essential that manufacturers maintain a focus on quality control and manufacturing expertise. This includes using advanced metrology equipment and inspection techniques, adhering to ISO standards, and investing in the development of skilled personnel.
Looking ahead, the future of high precision milling is bright, with new advancements in nanomachining, micro milling, and hybrid machining opening up new possibilities for the production of complex and intricate parts and structures. However, in order to fully realize the potential of these advancements, manufacturers must continue to prioritize quality control and manufacturing expertise, ensuring that they are equipped to meet the demands of a rapidly evolving technological landscape.
Click on the V1 Prototype website to gain more information.