Table of Contents:
- Introduction
- Injection Molding Process
- Design Considerations for Injection Molded Plastic Parts
- Quality Control in Injection Molding
- Applications of Injection Molded Plastic Parts
- Future of Injection Molding
- Conclusion
-
1.Introduction
Injection molding is a manufacturing process used to create a wide range of plastic parts with high accuracy and consistency. This process involves melting plastic resin pellets and injecting the molten plastic into a mold cavity, where it solidifies and takes on the shape of the mold.
The history of injection molding dates back to the late 19th century when celluloid, a plastic material, was first used to create simple products. In the 1930s, the first injection molding machines were developed, and by the 1950s, the process had become widespread in the manufacturing industry.
The advantages of injection molded plastic parts include:
- High accuracy and consistency: Injection molding offers exceptional precision, allowing for the production of parts with tight tolerances and intricate geometries.
- Versatility: Injection molding can be used to create a wide range of parts with varying sizes, shapes, and complexities.
- Efficiency: Injection molding is a highly efficient process that can produce large volumes of parts quickly and cost-effectively.
- Material selection: Injection molding can be used with a wide variety of plastic resins, making it a versatile process for many different applications.
- Durability: Injection molded parts are often highly durable and can withstand significant wear and tear, making them ideal for many industrial and commercial applications.
-
2.Injection Molding Process
The injection molding process involves the following steps:
- Mold preparation: The mold is clamped shut, and the plastic resin pellets are melted and injected into the mold cavity.
- Injection: The molten plastic is injected under high pressure into the mold cavity.
- Cooling: The plastic is allowed to cool and solidify in the mold cavity.
- Ejection: The mold is opened, and the part is ejected from the mold cavity.
- Finishing: The part may undergo additional finishing processes, such as trimming, polishing, or painting.
Types of injection molding machines:
- Hydraulic injection molding machines: These machines use hydraulic pressure to drive the injection process.
- Electric injection molding machines: These machines use electric motors to power the injection process.
- Hybrid injection molding machines: These machines combine hydraulic and electric power sources to optimize the injection process.
Injection molding materials:
- Thermoplastics: These materials can be melted and re-molded multiple times, making them ideal for many injection molding applications.
- Thermosetting plastics: These materials undergo a chemical reaction when heated, making them irreversible once they have been molded.
- Elastomers: These materials have high elasticity and flexibility, making them ideal for creating molded parts that need to be soft and pliable.
- Composites: These materials are made by combining two or more materials to create a new material with unique properties. They are often used for injection molding parts that require high strength and durability.
-
3.Design Considerations for Injection Molded Plastic Parts
Designing an effective injection molded part requires careful consideration of several key factors. Here are some design considerations to keep in mind:
- Wall thickness: The wall thickness of a part can affect its strength, durability, and overall quality. Parts with uniform wall thickness will generally be stronger and more consistent than those with uneven thickness.
- Draft angles: Draft angles are the angles added to the walls of a part to facilitate easy ejection from the mold. Without draft angles, the part can become stuck in the mold, leading to defects and damage.
- Ribs and bosses: Ribs and bosses are structural features added to parts to increase their strength and rigidity. These features can help reduce material usage and improve the overall quality of the part.
- Gate placement: The placement of the injection gate can affect the overall quality of the part. A gate placed too close to a critical feature, such as a text or logo, can cause distortion or damage to the feature.
- Parting line: The parting line is the line where the two halves of the mold meet. It can leave a visible mark on the part and affect its overall appearance. Careful design can minimize the impact of the parting line on the finished part.
By considering these factors during the design process, injection molded parts can be optimized for quality, consistency, and cost-effectiveness.
-
4.Quality Control in Injection Molding
Ensuring quality control in injection molding is essential to producing high-quality parts consistently. Here are some quality control considerations:
- Inspection methods: There are several methods used to inspect injection molded parts, including visual inspection, dimensional measurement, and material testing.
- Tolerance and measurement standards: Tolerance refers to the acceptable range of variation in a part’s dimensions, and measurement standards define how the dimensions are measured. Adhering to tolerance and measurement standards can help ensure that parts meet the required specifications.
- Defects and troubleshooting: Common defects in injection molded parts include sink marks, flash, warpage, and voids. Troubleshooting these defects can involve adjusting process parameters, improving mold design, or changing the material used.
By implementing rigorous quality control measures, injection molding manufacturers can minimize the risk of defects and ensure that parts meet the required standards consistently.
-
5.of Injection Molded Plastic Parts
Injection molded plastic parts have a wide range of applications across various industries. Here are some common applications:
- Consumer products: Injection molded plastic parts are widely used in the production of consumer products such as toys, kitchen appliances, and personal care items.
- Automotive industry: Many components of automobiles, such as dashboards, instrument panels, and interior trims, are produced using injection molding.
- Medical devices: Injection molding is used to produce a variety of medical devices, such as syringes, IV tubes, and surgical instruments.
- Aerospace industry: Injection molded plastic parts are used in the aerospace industry for various applications, including interior components of airplanes and spacecraft.
- Electronics industry: Injection molding is used to produce components for electronic devices such as smartphones, computers, and televisions.
The versatility and cost-effectiveness of injection molding make it a popular choice for producing plastic parts across a wide range of industries.
Click on the V1 Prototype website to gain more Injection Molding information.
-
6.Future of Injection Molding
As with any industry, injection molding is evolving and adapting to meet new challenges and opportunities. Here are some future considerations for injection molding:
- New materials and technologies: New materials, such as bioplastics and advanced composites, are emerging that could offer new possibilities for injection molding. Additionally, advancements in automation, robotics, and artificial intelligence are expected to transform the injection molding process.
- Sustainability in injection molding: Environmental concerns are driving a shift towards more sustainable materials and processes. This includes the use of biodegradable and recyclable plastics, as well as the implementation of energy-efficient technologies in injection molding.
- Market trends and forecasts: The global injection molding market is expected to continue to grow, driven by demand from industries such as automotive, packaging, and medical devices. The Asia-Pacific region is expected to be a key growth market, driven by the expanding manufacturing industry in countries such as China and India.
As injection molding continues to evolve, manufacturers will need to stay up-to-date with the latest materials, technologies, and market trends to remain competitive and meet the needs of their customers.
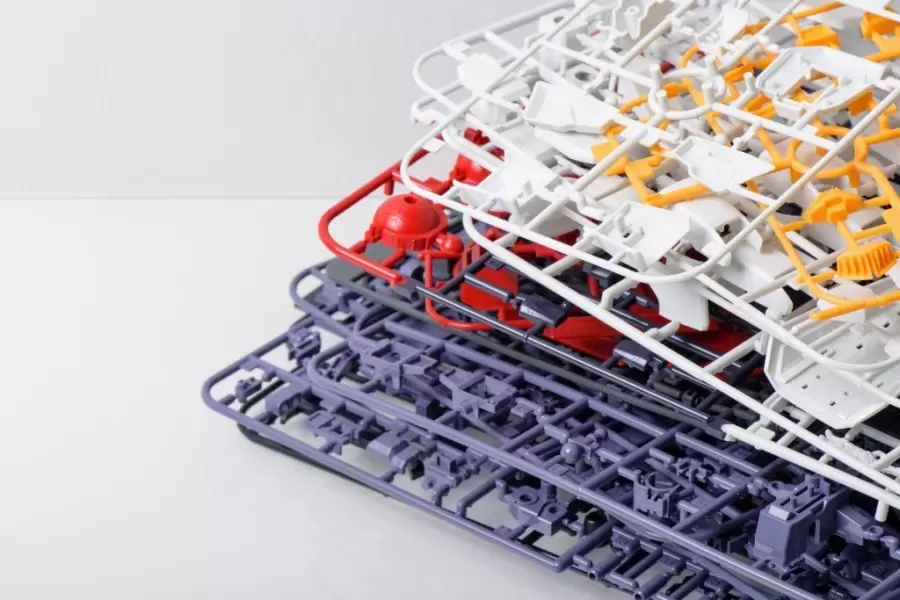
-
7.Conclusion
Injection molded plastic parts are ubiquitous in modern manufacturing, used in a wide range of industries and applications. From consumer products to medical devices and aerospace components, injection molding offers a cost-effective and versatile solution for producing high-quality plastic parts.
Design considerations such as wall thickness, draft angles, and gate placement, as well as rigorous quality control measures, are critical to ensuring the consistency and quality of injection molded parts. As the industry continues to evolve, new materials, technologies, and sustainability considerations will shape the future of injection molding.
In conclusion, injection molding will continue to be a critical manufacturing process in the coming years, and manufacturers will need to stay abreast of the latest developments to remain competitive and meet the needs of their customers.