Table of Contents:
- Introduction
- Types of Plastic Parts
- Materials Used in Plastic Parts Manufacturing
- Manufacturing Processes
- Designing Plastic Parts
- Quality Control in Plastic Parts Manufacturing
- Applications of Plastic Parts
- Sustainability and the Environment
- Conclusion
-
1.Introduction
Plastic parts are an essential component in various manufacturing industries, ranging from consumer goods to medical equipment, automotive, and electronics. In this article, we aim to provide an overview of the plastic parts industry, including its definition, significance, and objectives.
The plastic parts industry encompasses the design, manufacture, and distribution of plastic products for multiple applications. Plastic parts offer various advantages over other materials, such as metal or glass, including lower production costs, lighter weight, versatility, and durability.
The objectives of this overview include providing a comprehensive understanding of the plastic parts industry, the different types of plastic parts and their applications, the manufacturing processes, sustainability concerns, and future trends. We aim to highlight key considerations in selecting plastic parts, quality control measures in manufacturing, and various applications across industries.
-
2.Types of Plastic Parts
Plastic parts are a critical component of modern manufacturing, with a wide range of products available to meet different applications. These parts can be categorized based on several factors, including their manufacturing process, materials used, and intended purpose. Here are some common types of plastic parts used in different industries:
- Injection-Molded Parts:Injection molding is a widely used manufacturing process for plastic parts. The process involves melting plastic pellets and injecting them into a mold cavity. Injection-molded parts are known for their strength, complexity, and precision, making them ideal for use in automotive, medical, and electronic applications.
- Blow-Molded Parts:Blow molding is another manufacturing process used to create hollow plastic products, such as bottles and containers. The process involves extruding a hot plastic tube that is then inflated in a mold to create the desired shape. Blow-molded products are lightweight, durable, and used in applications such as packaging, automotive ducting, and toys.
- Extruded Parts:Extrusion is a manufacturing process where plastic pellets are melted and pressed through a die to produce continuous-length plastic products such as tubes and pipes. Extruded parts are known for their excellent uniformity and consistency and are extensively used in the construction and electrical industries.
- Thermoformed Parts:Thermoforming is a manufacturing process whereby a plastic sheet is heated and molded to create a particular shape. These parts are lightweight, cost-effective, and have excellent impact resistance, making them ideal for use in medical devices, food packaging, and consumer goods.
- Overmolded Parts:Overmolding occurs when one material is molded onto another to create a cohesive, single product. This process creates a finished product with greater functionality, reducing production complexity, and costs. Overmolded parts are commonly used in handles, grips, and other consumer products.
Plastic parts find diverse applications in different industries. Here are some examples of how plastic parts are used in various sectors:
- Automotive Industry:Automotive parts such as bumpers, dashboards, and door panels use plastic parts due to their lightweight, durability, and design flexibility. Plastic parts are not prone to rust and exhibit excellent impact resistance, making them ideal for use in impact-sensitive locations.
- Electronics Industry:Electronic devices such as smartphones, tablets, and laptops rely on plastic parts to enhance functionality and design. The lightweight and flexible nature of plastic enable design choices that can improve ergonomics and reduce cost, facilitating on-time delivery of gadgets.
- Medical Industry:Plastic parts are extensively used in the medical industry, primarily for their biocompatibility, strength and resistance to chemicals. Medical devices such as catheters, implantable devices, surgical instruments, and diagnostic equipment use plastic parts for their low cost, versatility, and ease of sterilization.
- Packaging Industry:The packaging industry utilizes plastic parts to produce different products, including bottles, jars, and containers. Plastic packaging is lightweight, durable, and cost-effective, demands less transportation costs while displaying appealing aesthetics widely.
- Consumer Goods Industry:Consumer goods such as toys, cooking utensils, and household appliances use plastic parts for their durability and design flexibility. Plastic parts enable the production of extraordinary designs that can’t be achieved with other materials while boasting economic efficiency by reducing production costs.
Overall, plastic parts are an essential component in different manufacturing industries, playing a crucial role in enhancing functionality, design, and cost-effectiveness of products.
-
3.Manufacturing Processes
When it comes to manufacturing plastic parts, there are several processes available, each offering unique advantages and disadvantages. Below are some common plastic part manufacturing processes:
- Injection Molding Process:Injection molding is a popular manufacturing process for creating plastic parts in high volumes. The process involves melting plastic pellets in a heated barrel, which is then injected into a mold cavity at high pressure. The material is cooled and solidified into the desired shape, allowing the mold to be opened, and the part ejected. Injection molding is known for its high repeatability, speed, and precision but requires high initial tooling & equipment investment.
- Blow Molding Process:Blow molding is a manufacturing process used to create hollow plastic parts. This process involves extracting molten plastic through an extruder to create a thin-walled tube. The tube is then inflated to the desired shape inside a mold cavity using air pressure, then cooled and solidified in the mold. Blow molding is commonly used to create products such as bottles, containers, and tanks, and it is relatively cost-effective for high volume production.
- Extrusion Process:Extrusion is a manufacturing process used to create continuous lengths of plastic products such as pipes, tubing, and profiles. The process involves feeding plastic pellets into a heated barrel where they are melted and forced through a die to form the desired shape of the product section. The product then passes through a cooling system before being spooled or cut to the desired length.
- Thermoforming Process:Thermoforming is a process used to create plastic parts by heating a plastic sheet and placing it over a mold to shape it. The plastic sheet is heated to a specific temperature until it is soft and malleable. It is then stretched over a mold and vacuum-formed to take the shape of the mold. The part is cooled and then trimmed to the desired shape. This process is used to create a wide range of products, including food packaging, medical device casings, and automotive parts.
Each manufacturing process has advantages and disadvantages depending on the product requirements, application, and production volume. Companies must choose the most suitable process to ensure that their plastic parts are consistent, high-quality, and cost-efficient in their production.
-
4.Designing Plastic Parts
Designing plastic parts involves several considerations to ensure that the final product is functional, durable, and cost-effective. Here are some factors to consider when designing plastic parts:
- Material selection:Choosing suitable materials is fundamental to the success of the design. Different plastic materials have varying physical and chemical properties, such as strength, stiffness, flexibility, and chemical resistance. Selecting the right material for the project will dictate how the part will perform, how it will be produced, and its final cost.
- Part geometry:Part geometry includes factors such as wall thickness, draft angles, and tolerance, which directly influence the material flow, quality, and ease of manufacturing. The geometry will also have an impact on the overall part strength and durability.
- Cost:The cost of production directly impacts the product’s final price, which affects the customer’s purchasing decision. Designers must consider the size, complexity, and volume of production to determine a suitable manufacturing process and material for the part.
- Assembly:How the part will be assembled must be taken into account during its design phase. Parts that will be joined with other parts must have suitable features such as notches, hooks, or snap fits to allow for easy assembly.
- Aesthetics:Designers must also consider the visual appearance of the part. This includes factors such as surface finish, color, and texture, which can impact the product’s look and feel.
Several tools and software applications are available for designing plastic parts, including CAD software, mold flow analysis tools, and prototyping software. Some popular software solutions for designing plastic parts include:
- SolidWorks
- AutoCAD
- CATIA
- Moldflow
- ANSYS
- Fusion 360
Designers use these software tools to create drawings or 3D models of the part, carry out simulations and analysis, and make necessary changes before starting with the manufacturing process.
Once the design process is complete, the next step is to develop a prototype for testing to ensure the plastic part meets the desired specifications. Prototyping allows designers to identify potential design flaws and make improvements before moving to full production. Several prototyping methods can be used, including 3D printing, CNC machining, and injection molding of a small batch of test parts.
Testing of plastic parts is essential in ensuring that they meet the required functionality, durability, and standards. Some common tests for plastic parts include stress testing, fatigue testing, and standardized testing to confirm the part’s quality and functionality. These tests are essential in helping designers identify any areas that need improvement and make the necessary changes.
-
5.Quality Control in Plastic Parts Manufacturing
Quality control plays a critical role in the manufacturing process of plastic parts. To ensure that the final product meets the desired quality, several quality assurance measures, inspection techniques, and compliance standards must be put in place.
To ensure the quality of plastic parts manufactured, the following measures need to be taken:
- Proper material selection: Selecting suitable materials with the necessary physical and chemical properties to ensure the final product meets the required standards.
- Adherence to design specifications: Following the design specifications and requirements to guarantee the plastic part meets the required functionality and standards.
- Controlling the manufacturing process: Monitoring the manufacturing process to ensure that the plastic parts are produced consistently and to specification.
- Testing and validation: Regularly testing and validating the plastic parts to ensure they meet the desired quality and functionality.
.
Below are some common inspection techniques performed in the plastic parts manufacturing process:
- Visual Inspection: Examining the part for surface defects or inconsistencies, such as cracks or bubbles.
- Dimension Inspection: Checking the dimensions of the part against the design specifications using measurement tools such as calipers or coordinate measurement machines.
- Mechanical Testing: Conducting tests such as strength, flexibility, and durability to ensure the plastic part meets the required standards.
- X-ray Inspection: Using x-ray technology to examine the internal structure of the plastic part to detect any defects, voids or inconsistencies.
.
Compliance standards play a central role when it comes to ensuring the quality and safety of plastic parts. Below are some common compliance standards related to plastic parts manufacturing:
- ISO 9001: Quality management system for any organization seeking to demonstrate its ability to consistently provide products and services that meet customer needs.
- ISO 13485: Quality management system for medical devices, ensuring that the manufacturer adheres to strict standards for the part’s design, development, and manufacture.
- UL certification: This certification ensures that parts comply with safety standards.
- RoHS: Restriction of Hazardous Substances Directive, which limits the use of hazardous materials in the manufacture of electronic components.
By complying with these standards, manufacturers can verify that their plastic parts meet the required quality and safety standards, ensuring customer satisfaction and enhancing the marketability of their products.
-
6.Applications of Plastic Parts
Plastic parts are used in a wide range of industries due to their versatility, cost-effectiveness, and durability. Below are some common applications of plastic parts in different industries:
- Automotive Industry:Plastic parts are used extensively in the automotive industry due to their high strength, resistance to wear and tear, and relatively low weight. Plastic parts can be found in several components, such as body panels, interior trims, and engine components.
- Electronics Industry:The electronics industry uses plastic parts extensively in the production of electronic components and devices. Plastic parts can be found in several electronic products such as mobile phones, computers, and household appliances.
- Medical Devices:Plastic parts are commonly used in the manufacture of medical devices due to their biocompatibility, chemical resistance, and sterilizability. Medical devices made with plastic parts include surgical instruments, catheters, and diagnostic equipment.
- Packaging Industry:Plastic parts are used widely in the packaging industry due to their high strength, flexibility, and ability to be easily molded into different shapes and sizes. Plastic packaging products include bottles, containers, and bags, among others.
Overall, the applications of plastic parts are widespread, covering different industrial sectors based on their excellent blend of properties, such as lightweight, good thermal insulation, biocompatibility, strength and durability, and affordability, facilitating several functional and technological solutions. The specific appropriateness of each material will depend on the specific applications and requirements.
If you want more about Plastic Parts information ,You can click on the V1 Prototype website to find it.
-
7.Sustainability and the Environment
With the increasing demand for plastic parts, there is a growing concern about their environmental impact. Below are some ways to address the sustainability challenges posed by the plastic parts manufacturing process:
- Recycling of Plastic Parts:Recycling of plastic parts is one of the ways to reduce the plastic waste generated from manufacturing. Recycling can be achieved by collecting used or discarded plastics, sorting them based on material types, and processing them into new products. The process of recycling mitigates the negative effects of plastic waste on the environment while creating opportunities for raw material recovery.
- Biodegradable and Sustainable Alternatives:The need for more sustainable plastics has led to the development of biodegradable and sustainable alternatives such as bioplastics, made from natural resources such as corn starch, cellulose, and other organic material. Biodegradable plastics break down into harmless materials through natural decomposition, reducing their impact on the environment.
- Future Trends in Sustainable Manufacturing:Advancements in green technology, such as additive manufacturing, are set to usher in a new era of sustainable plastic parts manufacturing. These technologies offer opportunities for decentralized production with minimal waste, requiring fewer resources for production.
In conclusion, the challenge of ensuring the sustainability of manufacturing is crucial for the long-term viability of plastic parts production. The adoption of alternative approaches such as recycling and biodegradable and sustainable alternatives can help minimize the impact of plastic waste generated from the manufacturing process while promoting a more sustainable future. Engaging stakeholders such as manufacturers, consumers, and regulatory agencies can contribute to the responsible use of plastic products while ensuring a sustainable future for generations to come.
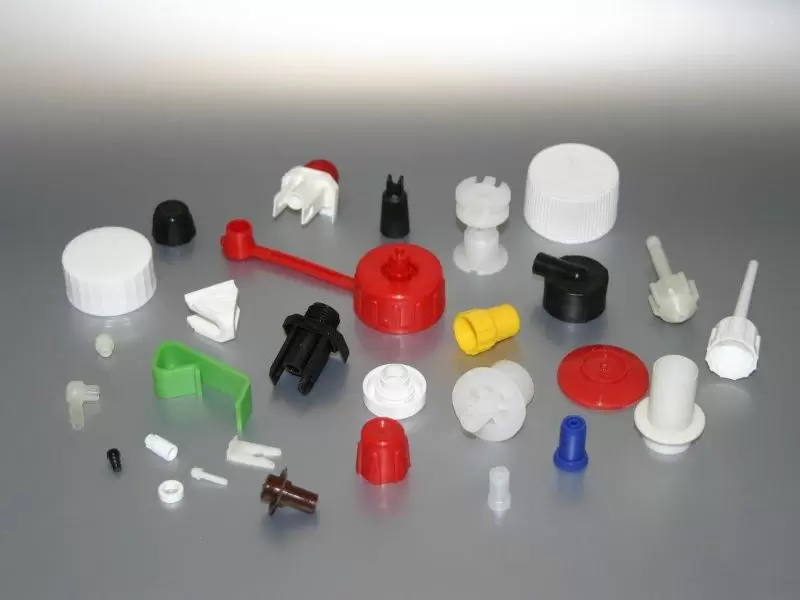
-
8.Conclusion
In conclusion, plastic parts manufacturing is an essential and dynamic industry that produces a wide range of products used in various applications. From automotive, electronics, medical devices, to packaging industries, plastic parts have become an indispensable component in modern-day manufacturing.
In this article, we explored different aspects of plastic part manufacturing, including the manufacturing processes, considerations in plastic part design, quality control measures, and the impact of sustainability on the industry. Here is a quick recap of some key points covered in this article:
- Plastic parts manufacturing involves various processes such as injection molding, blow molding, extrusion, and thermoforming.
- Material selection, part geometry, cost, assembly, and aesthetics are crucial considerations in designing plastic parts.
- Quality control measures such as proper material selection and control of the manufacturing process, testing, and validation, can help to ensure the final product meets the desired quality standard.
- Inspection techniques, including visual, dimension, mechanical testing, and x-ray inspection, help identify potential issues in the manufacturing process.
- Sustainability challenges in plastic parts manufacturing can be addressed through the recycling of plastic parts, and the development and adoption of biodegradable and sustainable alternatives.
For those interested in plastic part manufacturing, it is essential to stay abreast of emerging trends, advancements in technology, and regulatory changes to remain competitive in this dynamic industry. It is also important to remain mindful of the environmental impact of production and embrace sustainability practices to ensure a more eco-friendly future.
In summary, the plastic parts manufacturing industry, with its applications and diverse features, offers numerous opportunities for growth, innovation, and a rewarding experience, contributing significantly to the advancement in diverse sectors, enhance efficiency, and promote sustainable development.