Concrete Measures to improve the Life of Die Casting Mold (1)
In THIS PAPER, THE FORMS AND CAUSES OF DIE CASTING DIE FAILURE ARE DISCUSSED, AND THE FACTORS AFFECTING DIE LIFE and specific countermeasures are discussed from the aspects of die material, heat treatment, design, manufacturing and processing, die casting technology, production operation, die maintenance and so on.
The main forms of die casting die failure are:
①the alternating stress of thermal expansion and cold contraction, the long-term frequent repeated cycle, and the thermal fatigue cracking crack on the surface of the die;
②The mold overall cracking and damage caused by thermal stress and mechanical stress;
③Under the action of injection force and thermal stress, the mold will crack at the weakest point of strength, so that the cavity is broken;
④Mold erosion caused by chemical corrosion, mechanical wear, erosion, melting erosion;
⑤Plastic deformation of the mold caused by the action of mold locking, core inserting pressure and filling pressure. The reasons for the failure defects of these molds are complex and diverse. The following part discusses some specific measures to improve the life of die casting molds from the practical application.
Concrete measures to improve the life of Die Casting Mold (2)
Matters needing attention when selecting die casting mold materials
Mold materials should have good machinability, easy to finish; Has high heat treatment hardenability, so that after quenching internal and surface structure and performance uniform, and small size deformation; Durable high temperature plastic resistance and heat resistance fatigue strength, so that the mold will not crack prematurely; High high temperature strength, hardness and high temperature wear resistance, small coefficient of thermal expansion, to ensure the stability of the mold size in the process of use; High resistance to liquid die casting alloy chemical erosion and mechanical erosion ability to prevent mold adhesion and melting loss of meat;
It has high oxidation resistance at high temperature, corrosion resistance at room temperature, and is not easy to rust. In order to improve the impact toughness, the current commonly used H13 steel chemical composition purity requirements: the sulfur content of the superior steel should be less than 0.005%; Super H13 steel is required to contain less than 0.003% sulfur and less than 0.015% phosphorus. There is no eutectic carbide inclusion in the grain boundary of steel, and the large eutectic carbide and impurities have very little strength, which can not resist thermal fatigue, reduce the ductility of steel, and is the origin point of cracking.
To use electroslag remelting furnace refined steel, it is not only high purity, but also has dense structure, excellent thermal fatigue resistance, good thermal cracking resistance, excellent toughness and ductility, excellent polishing, better anisotropic properties. The uniformity of steel requires the organization of the material to be uniform, and the steel embryo has the same mechanical properties in any direction, without the performance differences in the longitudinal, horizontal and deep directions.
Correct selection of die material and high strength alloy material can improve the service life of die. It is suggested that the mold with high life requirements should choose 8407, DIEVAR, 2344, H13 (4Gr5MoV1Si) and SKD61 material from Sweden. Hitachi's DAC55, ZHD435 and Yisheng Hundred DIEVAR have good toughness and high temperature strength in high hardness, and the die life is also good.
Concrete measures to improve the life of Die Casting mold (3)
Matters needing attention in heat treatment of die casting mold
Heat treatment is the operation of changing the metallographic structure of die casting die materials by heating and cooling to obtain the necessary strength, hardness, toughness, dimensional stability at high temperature, thermal fatigue resistance, machinability and other properties of die materials. Note when heat treatment of die casting mold: for the same material, the same hardness after heat treatment, if different heat treatment process methods will make the quality performance is completely different. The heat treatment process and metallographic structure of H13 die steel after heat treatment shall refer to the regulations of the North American Die Casting Institute (NADCA 207-2003). It is suggested that the company selling mould steel should be responsible for the heat treatment of the mould, so as to avoid quality disputes caused by different materials and heat treatment manufacturers.
H13 steel is quenched by high pressure liquid nitrogen gas cooling high vacuum furnace with good quality, which can effectively prevent decarbonization, oxidation, deformation and cracking of the mold surface. Increase the quenching temperature to 1020℃ ~ 1050℃ (DIEVAR steel in 1000 ~ 1030℃), according to the size of the module material, and the required strength and toughness of each part, properly control the temperature and holding time, so that the alloy carbide fully dissolved into austenite, which can reduce the die due to heat treatment carbide dissolution is not sufficient.
Mold cracking caused by residue between grain boundaries. However, the critical points Ac1 and Ac3 of steel and the holding time should be paid attention to to prevent austenite coarsening. Die casting die after quenching with different temperatures at least 3 tempering, according to 2 ~ 3 hours/time insulation, special attention to tempering temperature and hardness effect, H13 steel can not be tempered at 425 ~ 550℃, DIEVAR steel can not be tempered at 500 ~ 550℃, to avoid tempering brittleness. If nitriding treatment is also performed, one tempering treatment can be reduced.
Tempering brittleness of steel
1.Tempering brittleness refers to the decreased toughness of quenched steel after tempering. With the increase of tempering temperature, the hardness decreases and the toughness increases. However, there are two low valleys in the relation curve between tempering temperature and impact toughness of many steels. One is between 200 ℃ and 400℃, which is low temperature tempering brittleness. The other is between 450 and 650℃, which is high temperature tempering brittleness. In the range of tempering brittleness temperature, the impact toughness decreases with the increase of tempering temperature.
2.After the martensite structure is obtained by quenching, the alloy steel is tempered in the temperature range of 450 ~ 600℃. Or after tempering at 650℃ at a slow cooling rate after 350 ~ 600℃; Or after tempering at 650℃, heating in the temperature range of 350 ~ 650℃ for a long time, all the steel produces embrittlement. If the steel that has been embrittlement is reheated to 650℃ and then cooled quickly, toughness can be restored, so it is also called "reversible tempering brittleness".
3.The reason of tempering brittleness: because of the segregation of impurity elements at the grain boundary, the fracture strength of the grain boundary is reduced, resulting in tempering brittleness.
The mechanism of high temperature tempering brittleness:
① When the tempering brittleness occurs, Ni, Cr, Sb, Sn, P and so on all converge to the original A (austenite) grain boundary (which is the main reason for the second kind of tempering brittleness), and all concentrate on the grain boundary with the thickness of 2~3 atoms. The tempering brittleness increases with the increase of impurity elements. Ni and Cr not only self-polymerize but also promote the polymerize of impurity elements.
②No segregation phenomenon of alloying elements and impurity elements was found in quenching without tempering or tempering without embrittlement.
③ The alloying element Mo can inhibit the segregation of impurity elements to the grain boundary of A, and it does not have segregation itself. Carbon also plays a role. The general carbon steel is not sensitive to high temperature tempering brittleness, but the binary or multiple alloy steel containing chromium, manganese, nickel and silicon is very sensitive. The degree of brittleness sensitivity varies with the type and content of alloying elements.
4.Methods to prevent tempering brittleness:
①Improve the purity of steel, minimize impurities;
②Adding appropriate amount of Mo, W and other beneficial alloying elements; When the content of molybdenum in steel increases to 0.7%, the embrittlement tendency of high temperature tempering decreases greatly, and when the content of molybdenum in the matrix decreases, the embrittlement tendency of steel increases. For the parts working in the high temperature tempering embrittlement area for a long time, single molybdenum addition is difficult to prevent embrittlement, only to reduce the content of impurities in the steel element, improve the purity of steel.
③for small size, simple shape parts, using the method of quick cooling after tempering;
④the use of sub-temperature quenching (below the A1~A3 temperature line) : refine grain, reduce impurities bias. After heating, it is A+F (F is ferrite, thin strip), impurities will be enriched in F, and F has A greater ability to dissolve impurity elements, which can inhibit the segregation of impurity elements to the grain boundary of A.
⑤The high temperature deformation heat treatment can make the grain superfine, increase the grain boundary area, and reduce the concentration of impurity element segregation.
⑥After high temperature tempering, oil cooling or water rapid cooling can inhibit the segregation of impurity elements at grain boundaries.
5.Tempering or stress-relieving annealing of die casting mold should be avoided in the range of high temperature brittleness as far as possible.
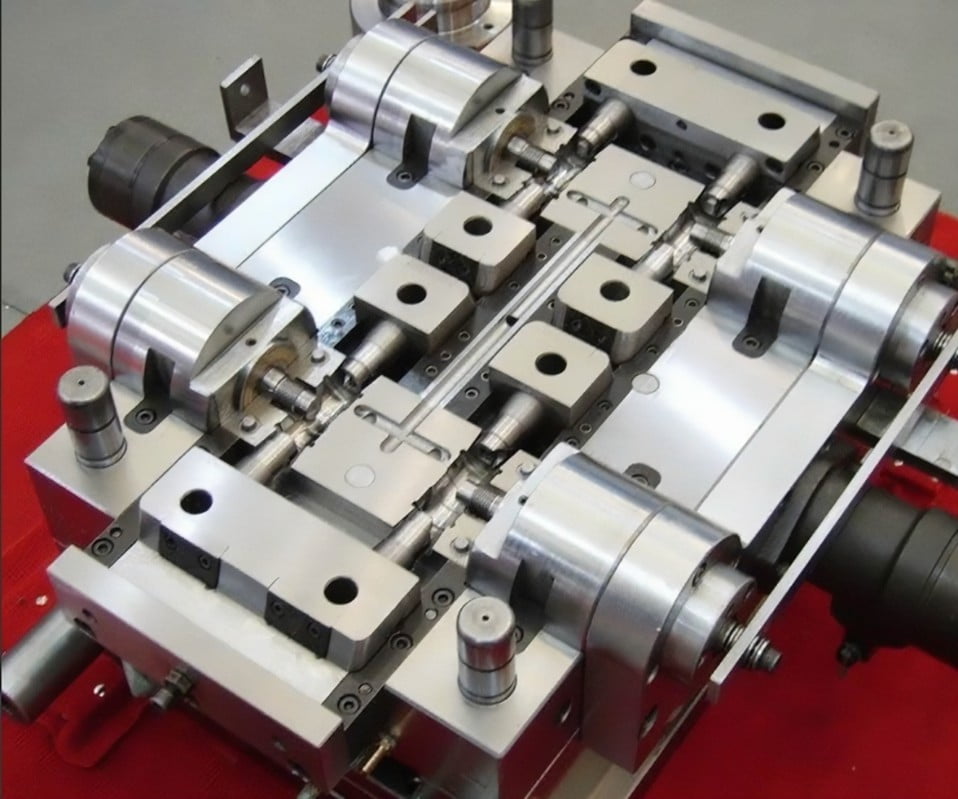
Concrete measures to improve the life of Die casting mold (4)
The cutting stress of die machining, the stress of EDM metamorphic layer and the thermal fatigue stress of die casting can be alleviated or eliminated by annealing. The mold should be annealed regularly to eliminate the stress: the first stress relief annealing should be arranged before quenching (annealing temperature of 700℃ ~ 750℃), the second stress relief annealing should be arranged before the mass production after the mold test is qualified, and then the annealing treatment is performed once in the die-casting of 10,000 mold and 30,000 mold, and the nitride can replace the annealing treatment once. The annealing temperature of H13 steel is 20℃ ~ 40℃ lower than the last tempering temperature during quenching, such as 560±10℃ for 1 ~ 1.5 hours according to the thickness of the module for stress relief annealing.
AISI H13 ESR materials in the United States are used for die casting molds. If the hardness is low, it is easy to appear sticky mold and early cracking, and if the hardness is too high, it will increase the risk of cracking. Therefore, it is generally recommended to use 47 ~ 52HRC for zinc alloy die casting molds. Medium and small aluminum, magnesium alloy die casting mold 46 ~ 48HRC; For large aluminum and magnesium alloy castings and thick or complex parts, the hardness should be appropriately reduced to 44 ~ 46HRC. Hitachi DAC55, ZHD435 and YISingbai DIEVAR steels have excellent toughness and high temperature resistance at high hardness, and the hardness can be increased by 2 ~ 4HRC compared with H13 when applied.
Concrete measures to improve the Life of Die Casting Mold (5)
On the surface of die casting mold cavity prone to sticky mold parts and all cores, should choose nitriding, carbonitriding, KANUC, Japan, evaporation (PVD physical evaporation, CVD chemical evaporation), nitriding plus evaporation, laser surface strengthening treatment, in order to reduce adhesion or erosion. At present, KANUC of Japan is used to deal with more. If nitriding is needed, the total depth of nitriding layer on the mold surface should be smaller than the previous 0.2 ~ 0.3mm, which should be controlled in 0.04 ~ 0.08 ~ 0.12mm according to the thickness of the casting wall from thick to thin, and there should be no compound white bright layer, so as to prevent the premature cracking of the mold caused by the fragmentation of too thick white bright layer.
The higher the nitriding temperature, the higher the nitrogen potential concentration and the thicker the nitriding layer, the more likely the white bright layer will be produced. For the parts that are easy to stick to the mold, the surface treatment such as nitriding can be carried out once every 10 ~ 20 thousand die casting. Nitriding treatment can also be carried out when the die is cast 80 ~ 100 000 times, because the hardness is reduced and sticky die is easy to appear. Note that the die surface should be polished before and after each annealing and nitriding. In order to prevent the mold cavity from oxidizing and rusting before mass production, after the mold test is qualified, the mold should be subjected to 530 ~ 560 heat preservation oxidation treatment in the electric furnace for 1 ~ 1.5 hours.
Concrete Measures to improve the Life of Die Casting Mold (6)
Matters needing attention in die casting mold design
Reasonable design of casting, casting wall thickness should be uniform, not too thin, too thick, the general thickness of 2 ~ 3.5mm is good, angular transition should have rounded corners or slopes to reduce stress concentration, can use the reinforcement structure to eliminate hot joints formed by casting. Too thick die casting internal microstructure grain coarse, will form pores, shrinkage, oxidation, internal cracks, and accompanied by stress sources, so that its strength and durability will be lower than the product formed by reinforced reinforced structure.
For the easy to crack parts and easy to damage parts of the mold to adopt insert structure as far as possible, after damage is easy to repair and replace. But the molding parts of the inset hole, including the core hole to the edge of the mold or another hole near the distance is not too small, and the inset hole to have a large round chamfer, so as not to become a weak part of the mold early cracking.
To improve the rigidity of mold design, the stress of each part of mold cavity should be analyzed. The FORCES obtained BY the cavity INCLUDE THE PRESSURE, EXPANSION force AND impact force when the alloy liquid is filled, the tension and abrasion force when the product is released from the mold, the thermal stress caused by the change of temperature, the pressure, tension and preload force when the mold is opened and closed and the core is inserted.
The design should make the mold in each part, each part has enough thickness, width, so that the mold has enough rigidity to withstand various stresses. It is important that these forces are properly balanced to prevent deformation and cracking of the mold. When manufacturing, pay attention to the thin section of the mold and the concave Angle root of the module are the sensitive sources of mold fracture. It is necessary to ensure the accuracy of the matching. If the preloading force of the module is too large, it will concentrate the clamping force on one point, which is the main factor for the large area fracture of the mold.
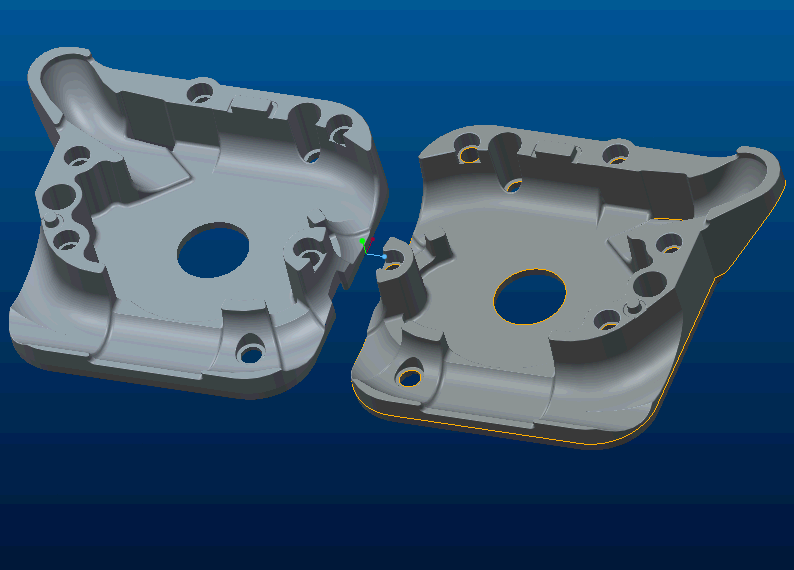