Results and Discussion of Die Casting Zinc Alloy
Introduction
Die casting is a popular manufacturing process for producing metal components with high precision and complex shapes. Among the various materials used in die casting, zinc alloys offer unique advantages due to their excellent properties, cost-effectiveness, and ease of casting. In this article, we will delve into the results and discussion of die casting zinc alloy, comparing its costs with other processes and summarizing the benefits it offers.
Die Casting with Zinc Alloys
1. Properties of Zinc Alloys
Zinc alloys are known for their exceptional properties, making them well-suited for die casting applications. They exhibit excellent fluidity, allowing for intricate and thin-walled designs to be cast with ease. Zinc alloys also have good dimensional stability, high strength, and excellent corrosion resistance, making them suitable for a wide range of industries, including automotive, electronics, and consumer goods.
2. Process of Die Casting Zinc Alloys
The die casting process involves injecting molten metal into a mold cavity under high pressure. For zinc alloys, hot chamber die casting machines are commonly used due to the lower melting point of zinc. The process begins with the preparation of the mold, which consists of two halves - the cavity and the core. Once the mold is closed, the molten zinc alloy is injected into the cavity, filling the space and taking the shape of the mold. After cooling and solidification, the part is ejected from the mold, ready for further processing or assembly.
3. Advantages of Die Casting Zinc Alloys
Die casting zinc alloys offer several advantages:
i. Cost-Effectiveness
Zinc is a relatively affordable material, making die casting with zinc alloys a cost-effective choice, especially for high-volume production.
ii. High Production Efficiency
The die casting process is highly efficient, with rapid cycle times that enable mass production of parts in a short period.
iii. Complex Geometry
Zinc alloys have excellent fluidity, allowing for the production of parts with intricate and complex geometries, including thin walls and fine details.
iv. Surface Finish
Zinc alloys produce parts with a smooth and aesthetically pleasing surface finish, reducing the need for additional finishing processes.
v. Recycling Capability
Zinc is fully recyclable, promoting sustainable manufacturing practices and reducing environmental impact.
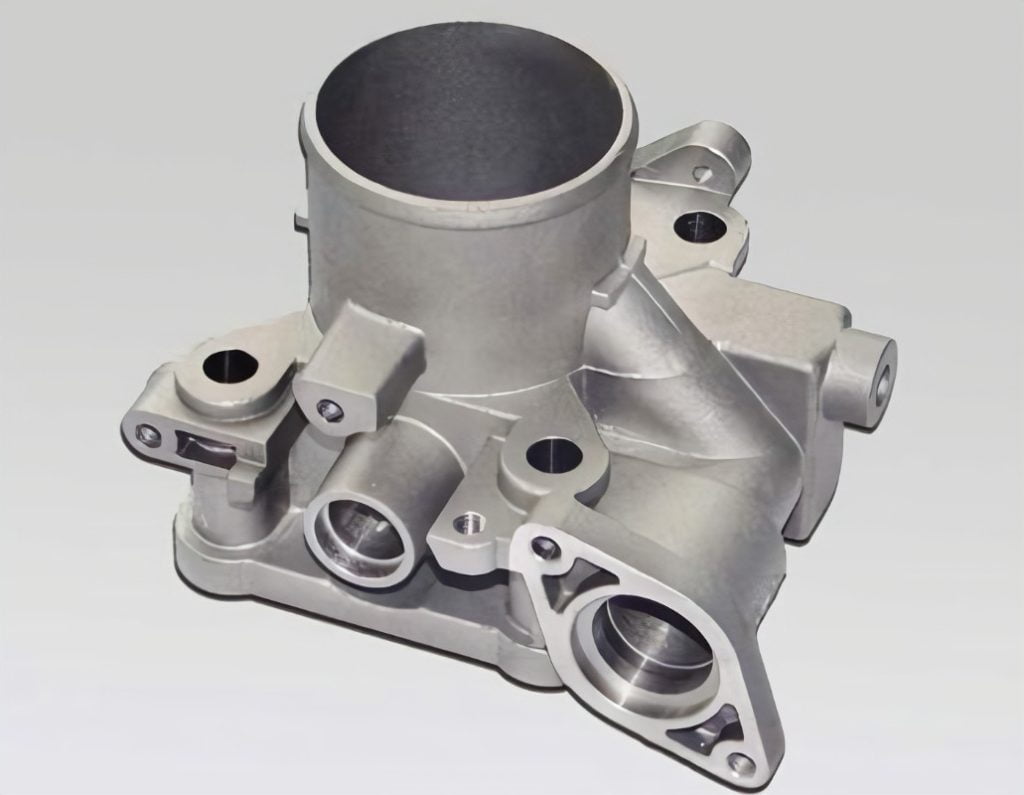
Comparison of Die Casting Zinc Alloys with Other Processes
1. Comparison with Aluminum Die Casting
Zinc alloys offer advantages over aluminum die casting in certain applications. While aluminum is lighter and has higher strength-to-weight ratio, zinc alloys have superior fluidity and can fill intricate molds more effectively. Additionally, zinc die castings require less machining due to their close-tolerance capabilities, leading to cost savings in post-processing.
2. Comparison with Plastic Injection Molding
Plastic injection molding is an alternative process for producing complex parts, but it may not match the mechanical properties of die-cast zinc components. Zinc alloys offer higher strength and better temperature resistance, making them suitable for demanding engineering applications. However, plastic injection molding may be preferred for certain lightweight and non-structural parts due to its lower material costs and ease of molding.
3. Comparison with Investment Casting
Investment casting is a traditional process used for producing complex metal parts, but it can be costlier and time-consuming compared to die casting with zinc alloys. While investment casting may be suitable for producing intricate and one-off parts, die casting offers better cost-efficiency for high-volume production.
4. Comparison with Sand Casting
Sand casting is a versatile process for producing metal parts, but it is less suitable for intricate and thin-walled designs. Die casting with zinc alloys provides better dimensional accuracy and surface finish, making it ideal for mass production of parts with complex geometries.
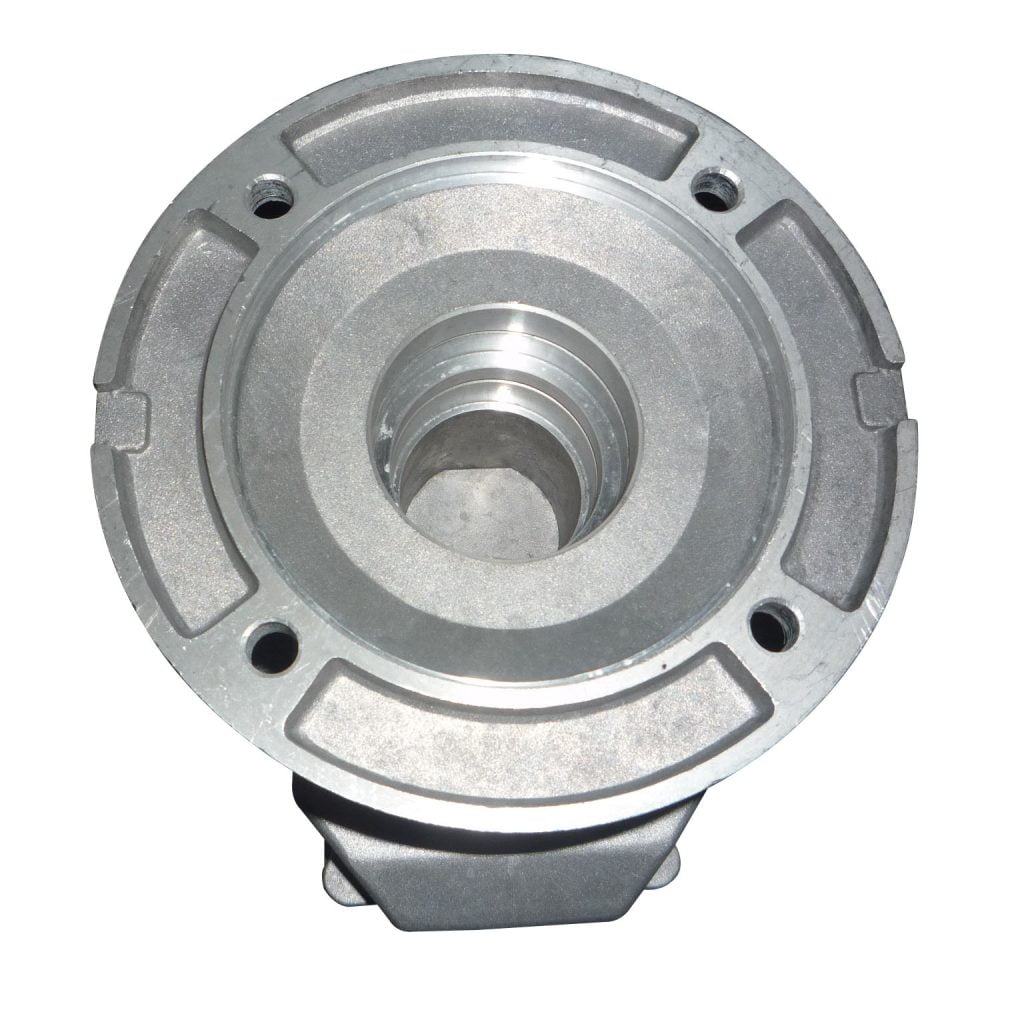
Summary of Different Process Costs
The costs of different processes vary depending on factors such as material, tooling, production volume, and post-processing requirements. Here is a summary of the cost considerations for die casting zinc alloys and other processes:
- Die Casting with Zinc Alloys:
- Cost-effective for high-volume production due to shorter cycle times and reduced material waste.
- Lower material costs compared to other metal alloys.
- Initial tooling costs, but amortized over large production runs.
- Aluminum Die Casting:
- Material costs may be higher than zinc alloys.
- Longer cycle times compared to zinc alloys, impacting production efficiency.
- Greater post-processing and finishing costs.
- Plastic Injection Molding:
- Lower material costs compared to metal alloys.
- Suitable for lightweight and non-structural parts.
- Longer cycle times for complex designs.
- Investment Casting:
- Higher tooling and setup costs compared to die casting.
- Suitable for producing intricate and one-off parts.
- Longer lead times for production.
- Sand Casting:
- Versatile for producing large and complex parts.
- Slower cycle times and less precise compared to die casting.
- Higher post-processing costs for finishing.
Conclusion
Die casting with zinc alloys is a versatile and cost-effective manufacturing process, offering advantages such as high production efficiency, complex geometries, and superior mechanical properties. When compared to other processes, zinc die casting stands out as an excellent choice for high-volume production of metal components with intricate designs and close tolerances. However, the selection of the manufacturing process should consider factors beyond costs, including part complexity, material properties, and production volume. By carefully evaluating these factors, manufacturers can make informed decisions and achieve optimal results in their production processes.