Table of Contents:
- Introduction to CNC Prototype Machining
- Understanding the CNC Prototype Machining Process
- Choosing the Right CNC Prototype Machining Service Provider
- Advantages of CNC Prototype Machining over Traditional Methods
- Limitations of CNC Prototype Machining
- Best Practices for CNC Prototype Machining
- Conclusion
-
1.Introduction to CNC Prototype Machining
Definition:
CNC Prototype Machining refers to the process of using computer-controlled machines to create functional prototypes quickly and accurately. CNC (Computer Numerical Control) machines cut and shape materials according to a set of programmed instructions. This process allows for the creation of highly detailed 3D models with great accuracy, replicating the intended design.
Benefits of CNC Prototype Machining:
- Speed: CNC machines work much faster than traditional machining processes, allowing prototypes to be created in a matter of days or even hours instead of weeks.
- Precision: CNC machines can produce highly detailed and accurate prototypes that meet tight tolerances and specifications, which is important for industries that require precise parts.
- Cost-effectiveness: CNC Prototype Machining is a cost-effective alternative to traditional machining processes for the creation of prototypes or low-volume production runs.
- Customization: CNC machines can quickly and easily produce a range of complex shapes and designs, making it ideal for creating customized prototypes.
Applications:
CNC Prototype Machining is widely used in various industries and applications, including but not limited to:
- Aerospace: creating parts for airplanes, rockets, and other aerospace equipment.
- Automotive: designing and prototyping parts for cars and other vehicles.
- Medical: developing instruments and equipment, such as prosthetics, implants, and surgical tools.
- Product Development: creating prototypes for consumer products, such as toys and electronics.
- Industrial: producing machine parts and other equipment.
CNC Prototype Machining can be applied to almost any industry or application where precise, customized prototyping is necessary.
-
2.Understanding the CNC Prototype Machining Process
CNC Prototype Machining involves several steps that ensure the accurate and efficient production of a prototype. These steps include:
- CNC Machine Types:
The CNC machines used for prototyping come in various types, such as CNC mills, lathes, routers, and grinders. Each of these machines has a specific function and is used to produce a particular type of prototype.
- CNC Programming:
CNC machines require specific instructions for creating a prototype. These instructions are generated using Computer-Aided Manufacturing (CAM) software, which converts a 3D design into a set of instructions for the CNC machine to follow.
- Materials Used:
CNC Prototype Machining can use a wide range of materials such as metals (aluminum, steel, brass), plastics (ABS, polycarbonate, nylon), and composites. The material chosen depends on the application and functional requirements of the prototype.
- Tools and Techniques:
CNC machines use a variety of cutting tools, such as end mills, drills, and reamers, to shape the material into the desired shape. The cutting tools chosen are based on the material being used and the type of cut required.
Overall, the CNC Prototype Machining process involves the use of carefully selected materials, programming, and cutting tools to create precise and functional prototypes.
-
3.Choosing the Right CNC Prototype Machining Service Provider
Choosing the right CNC Prototype Machining service provider is critical to the success of your project. Here are some factors to consider when selecting a service provider:
- Experience: Look for a provider with significant experience in CNC Prototype Machining. This ensures that they have the expertise and knowledge to produce high-quality prototypes.
- Quality: Ensure that the provider has quality control measures in place. This includes ensuring that the finished prototype meets the required specifications and tolerances.
- Materials: Ensure that the provider can work with the materials you require for your project.
- Pricing: Compare the pricing of various service providers to find a provider that suits your budget.
- Communication: Look for a provider who communicates well with clients, providing regular updates on the progress of the project.
Comparing Service Providers:
When comparing different CNC Prototype Machining service providers, consider the following:
- Quality of work: Look at the quality of their previous work, and reviews from previous clients.
- Communication: Look for providers who communicate well, and provide regular updates throughout the project.
- Pricing: Compare pricing from different providers, and ensure that there are no hidden costs.
- Lead time: Compare the lead times of different providers, and their ability to deliver the finished prototype within the required timeframe.
Overall, when choosing a CNC Prototype Machining service provider, ensure that they have the necessary expertise, knowledge, and equipment to deliver a high-quality and functional prototype within your budget and lead time requirements.
Click on the V1 Prototype website to gain more information.
-
4.Advantages of CNC Prototype Machining over Traditional Methods
CNC Prototype Machining offers several advantages over traditional methods for the creation of prototypes. These advantages include:
- Speed: CNC machines work much faster than traditional machining processes, allowing prototypes to be created in a matter of days or even hours instead of weeks.
- Precision: CNC machines can produce highly detailed and accurate prototypes that meet tight tolerances and specifications. Traditional machining processes are more prone to errors, and it may take more time and resources to achieve precision.
- Cost-effectiveness: CNC Prototype Machining is more cost-effective than traditional machining processes, especially for smaller production runs. Traditional machining processes require more time and manual labor, which can be expensive.
- Customization: CNC Prototype Machining allows for the easy creation of customized prototypes. CNC machines can produce a wide range of complex shapes and designs, which is important for industries that require unique and specific prototypes.
Overall, CNC Prototype Machining offers several advantages over traditional machining processes. The speed, precision, cost-effectiveness, and customization capabilities make it an ideal choice for the creation of high-quality and functional prototypes.
-
5.Limitations of CNC Prototype Machining
While CNC Prototype Machining offers several advantages, there are still some limitations that should be considered when selecting this manufacturing method. These limitations include:
- Material limitations: CNC machines cannot work with all types of materials. For example, some materials may be too tough or brittle to be machined effectively with CNC machines.
- Design limitations: CNC machines work effectively with designs that are well-suited for machining. Parts with extremely narrow walls or extremely thin sections may not be suitable for CNC machining due to tool limitations.
- Size limitations: CNC machines have size limitations, which means they can only create prototypes within a certain size range. Large or bulky prototypes may need to be produced using other manufacturing methods.
- Technical limitations: CNC machines require a skilled technician to operate and are only as effective as the CAM software used to program the machine. The complexity of the design can also affect the programming and machining process.
Overall, while CNC Prototype Machining is a great manufacturing method for the creation of high-quality prototypes, it does have some limitations. The type of material, design complexity, size, and technical expertise required are all factors that should be considered when choosing this method of prototyping.
-
6.Best Practices for CNC Prototype Machining
To ensure that CNC Prototype Machining is successful in producing high-quality prototypes, there are several best practices that should be followed. These include:
- Design considerations: The design of the prototype should be optimized for CNC Machining. This includes designing parts with easy-to-machine features, reducing complexity, and minimizing waste.
- Machining techniques: The machining techniques chosen should be optimized for the material being used and the design of the prototype. This includes choosing the right cutting tools, feed rates, and spindle speeds.
- Quality control: Quality control measures should be put in place to ensure that the finished prototype meets the required specifications and tolerances. This includes inspecting the parts during and after machining, verifying dimensions, and identifying any defects.
- Maintenance and upkeep: Regular maintenance and upkeep of the CNC machines are crucial for ensuring that they operate reliably and produce accurate prototypes. This includes regular cleaning, lubrication, and replacement of worn parts.
Overall, by following these best practices, CNC Prototype Machining can be highly successful in producing high-quality and functional prototypes. The design, machining techniques, quality control, and maintenance of the CNC machines all play a crucial role in the success of this manufacturing process.
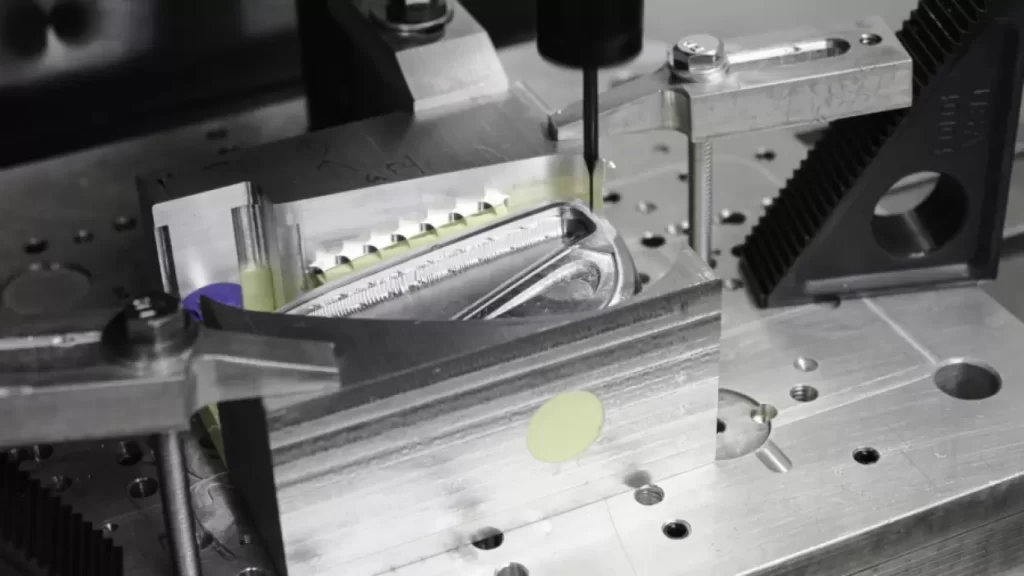
-
7.Conclusion
CNC Prototype Machining is an effective and efficient method for the creation of high-quality and functional prototypes. Its benefits include speed, precision, cost-effectiveness, and customizable capabilities, making it a popular choice in several industries.
Recap of Key Points:
- CNC Prototype Machining involves the use of computer-controlled machines to create prototypes quickly and accurately, using a variety of materials.
- The advantages of CNC Prototype Machining include speed, precision, cost-effectiveness, and customization.
- The limitations of CNC Prototype Machining include material, design, size, and technical limitations.
- Best practices for CNC Prototype Machining include optimizing the design for machining, choosing the right machining techniques, quality control measures, and regular maintenance and upkeep.
Future Outlook for CNC Prototype Machining:
As technology advances, CNC Prototype Machining is likely to become even more efficient and cost-effective than traditional manufacturing methods. With the rapid rise of automation and artificial intelligence, CNC machines will continue to become even more sophisticated, leading to better precision and faster lead times. Additionally, with the advent of 3D printing and new materials, CNC Prototype Machining is likely to become even more versatile in its capabilities.