The industrialization process of our industry is speeding up, and the competition of die casting industry is becoming more and more fierce, but there are still many die casting enterprises directly using aluminum injection method, which has low efficiency and high cost. Therefore, this paper focuses on the discussion and analysis of die casting die preheating methods, hoping to provide help for peers.
1.Mold heat transfer mode
There are several main modes of mold heat transfer:
(1) thermal radiation
Thermal radiation is one of the three ways heat is transferred. Anything with a temperature above absolute zero produces thermal radiation, which gives off energy in the form of electrical radiation. The higher the temperature, the greater the total amount of energy radiated. At the same time, the larger the surface area of an object, the greater the radiation. Die casting dies lose part of their heat energy through thermal radiation at high temperatures.
(2) heat conduction
The transfer of heat from one part of a system to another, or from one system to another, is called heat conduction. Heat conduction is the main way of heat transfer in solids. Heat is transferred from the high temperature part of the object to the low temperature part. As long as there is a temperature difference in the object, heat transfer will certainly occur. Heat conduction is the main heat transfer method of die casting die.
(3) heat convection
In a liquid or gas, the hotter part rises and the cooler part falls, circulating and mixing with each other to make the temperature tend to be uniform. Convection is an important way of heat transfer in gas. It can be divided into natural convection and forced convection.
The heat of the mold is transmitted to the ambient air, and the peripheral hot air takes away a small amount of heat by convection. The moisture in the release agent is suddenly vaporized by heat, and the heat is taken away by natural convection. The fluid in the cooling channel takes away the heat of the mold by forced convection.
In die casting production, the heat source of the die is liquid metal and the heat generated by the die casting machine itself, but the main source is liquid metal. Each time the liquid metal is injected, the heat is transferred to the surface of the mold through heat conduction, and the surface of the mold rapidly heats up. Then the heat is transferred to the inside of the mold, and then the heat is transferred out through the water transport of the mold and the spraying of the release agent on the surface of the mold.
2.Die preheating method
The following lists three kinds of die preheating methods, and comparative analysis of data.
(1) Injection liquid aluminum preheating method
After the die casting mold is installed, the machine is directly turned on and hot die is made of aluminum. First, 20 die is injected at low speed, then 10 die is injected at high speed, then 5 die is pressurized at high speed, and finally normal production is transferred. During this period, 30 die aluminum material is lost. If the model of 250 ~ 400 t is taken as an example, and the capacity of 80 die /h is taken as a reference, it will take about 27 min.
The method of preheating aluminum material is to inject liquid metal into the mold cavity continuously and directly rely on liquid metal to achieve the effect of heating up. However, since the spraying and mold retention time are set according to the process parameters of normal mass production, the temperature loss of the circulating mold is faster in each production process, which leads to the poor heating effect of the mold. It also needs to consume a lot of die times to heat up the mold to the temperature required by the process, and the time is relatively long. In addition, at the beginning, the mold is in the state of cooling, and the metal is directly hydraulic into the mold cavity. The temperature difference on the surface of the mold is large in each cycle, and the mold is prone to turtle cracks.
(2) Preheating method of mold temperature machine
After the die casting mold is set up, connect the oil pipe on the mold, close the mold first (but not closed, the moving and fixed mold need to leave a 5-10 mm gap), then open the mold temperature machine, set the temperature of the mold temperature machine at 100 ℃, when the oil return temperature reaches the set temperature, keep for 5 minutes; Then adjust the temperature of the mold temperature machine to 150 ℃, and keep it for 5 min when the return oil temperature reaches the set temperature.
Then adjust the temperature to 200 ℃ and keep it for 5 min after the temperature reaches the set temperature. Finally open the mold, boot, with aluminum and then hot die, first low speed injection 5 die, then high-speed injection 3 die, then high-speed pressurization 2 die, and finally turn to normal production, during which the loss of 10 die aluminum, if 250 ~ 400 t model as an example, with 80 die /h capacity as a reference, it will take about 45 minutes.
Mould temperature machine preheating method is through the mould temperature machine to transfer heat conduction oil (mould temperature oil) to the mould interior for repeated circulation heating, the mould interior preheating first, and then through heat conduction heat transfer to the mould surface, to achieve the heating effect, and finally 10 injection molding, so that the mould temperature is more uniform. Mold temperature machine preheating method from the inside out way
The mold preheating is the least harmful to the mold. However, because this method is time-consuming and strict in the design of the mold oil circuit, it can not ensure the uniform preheating of the mold, so this method is rarely used. It should be noted that it takes about 10 minutes for the mold temperature machine to rise from room temperature to 100 ℃, and about 5 minutes for the mold temperature machine to rise from 100 ℃ to 150 ℃ and then from 150 ℃ to 200 ℃.
(3)Quick preheating method
After the die casting mold is good, the surface of the die casting mold is evenly daubed with the wax (anti-welding wax), and then the mold is preliminarily preheated with the gas flame. The length of the gas flame is generally 20 ~ 30 cm, during which the mold should be heated evenly and preheated continuously for about 10 minutes. After the preheating of the gas flame, the machine was turned on and the aluminum material was used for hot mold.
First, 3 molds were injected at low speed, then 1 mold was injected at high speed, then 1 mold was pressurized at high speed, and finally normal production was transferred. During the period of loss of 5 die aluminum, aluminum injection needs to set the mold retention time to 2 ~ 3 times of the normal parameters, spraying time is 50% of the normal parameters, high speed injection speed is 80% of the normal parameters, if 250 ~ 400 t model as an example, with 80 die /h capacity as a reference, it will take about 151 min.
The rapid preheating method is to heat the mold with gas first. Before heating, it is necessary to ensure that the surface of the mold must be coated with release wax to prevent local overheating and burning the mold. Then the mold retention time should be extended 2 ~ 3 times to increase the time that the casting stays in the mold cavity and speed up the temperature of the mold. The spraying time should also be reduced by 50% to reduce the heat taken away by the release agent in the process of hot mold, so as to further accelerate the heating effect. This method takes the shortest time, and only 5 molds can reach the mold temperature interval required by the process, so it is recommended to adopt the fast thermal mold method.
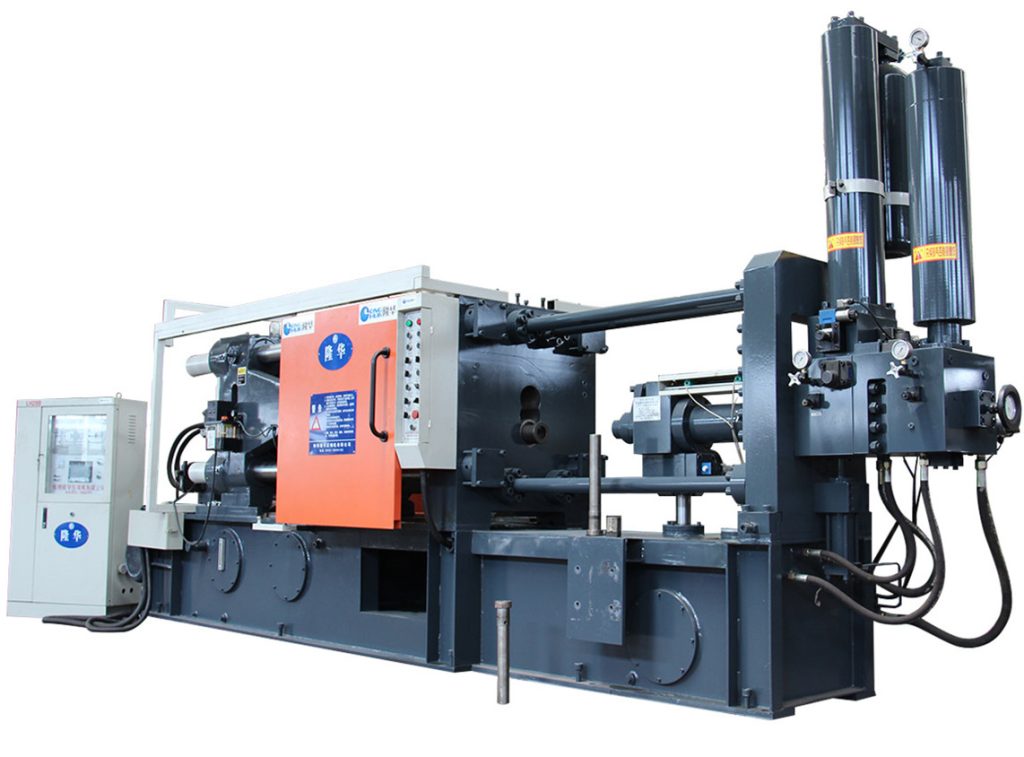
3.Comparative analysis of die preheating methods
It is recommended that the die temperature range of aluminum and magnesium alloy die casting mold is 150 ~ 250 ℃, within which the quality of the products can be guaranteed. Improper mold temperature will affect the quality of the casting. Too high mold temperature will lead to defects such as sticky mold, surface bubbling, ejecting difficulty, shrinkage cavity, shrinkage porosity, and even affect the dimensional accuracy of the casting. Low die temperature will lead to cold lines, cold grid, black casting, poor molding and other defects. Therefore, it is necessary to preheat the mold according to the required mold temperature interval when the mold is preheated, to ensure that there is a normal casting output immediately after the mold is preheated, and improve the delivery efficiency.
4.conclusion
The rapid preheating method can significantly reduce the number of hot molds, reduce the input of aluminum ingots, and can raise the mold temperature to the required temperature range in the shortest time, improve the production efficiency, and ensure the production quality. Due to the reduction of hot die times, the service life of the die has been extended accordingly, reducing the production cost of enterprises, enhancing the market competitiveness of enterprises, and creating good economic benefits for enterprises.
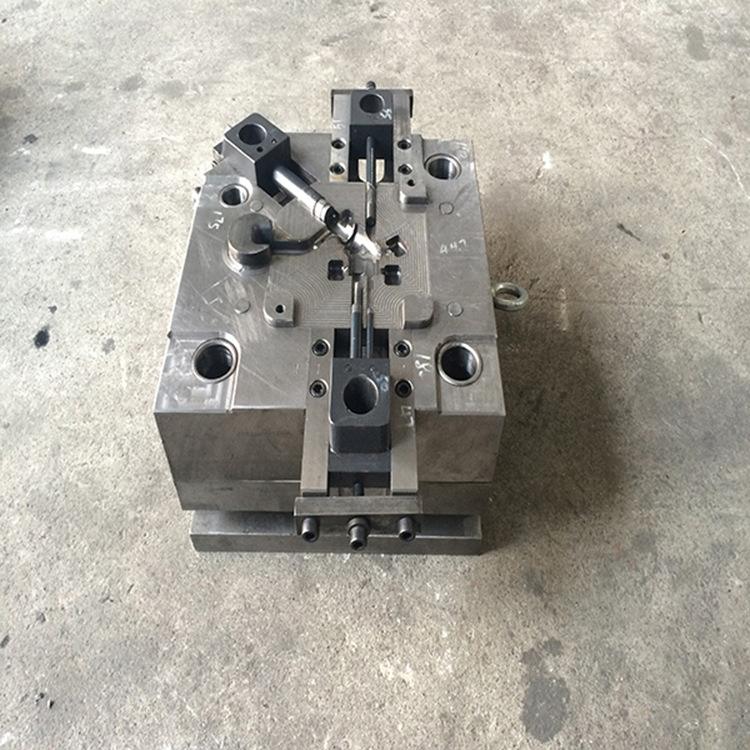