Blow Molding Services
One-stop blow molding mold manufacturer fine processing technology, including automobile parts mold, tray mold, float mold, daily necessities mold and chemical oil barrel industrial mold.
Blow Molding Services
The company offer you full range of plastic injection moulding services from design,prototyping, mould making and a wide range of additional services.
We can manufacture a complete series of blow molding molds, including automobile parts mold.tray mold. float mold, daily necessities mold, transportation facilities mold and chemical oil barrel industrial mold. We have complete advanced processing eguipment and machine tools to ensure the supply of high-quality, high-precision mold. Our main design teams have more than 15 years of professional experience, With the latest CAD/ CAE/ CAM software, we can provide customers with accurate and professional design drawings.
More than 50% of our moulds are exported to Europe, North America and Australia, we are your good choice and reliable partner for injection moulds-quality and reliability guaranteed.
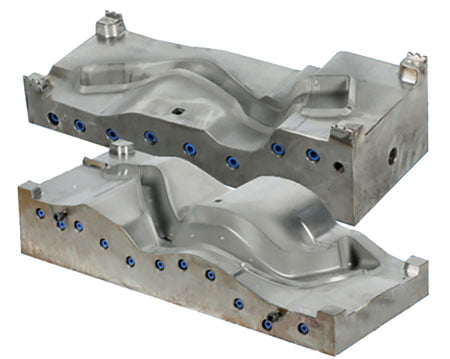
Blow Molding Auto Products
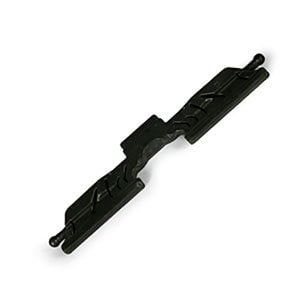
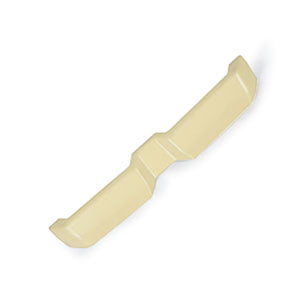
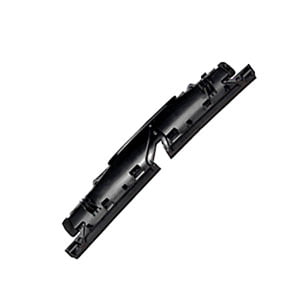
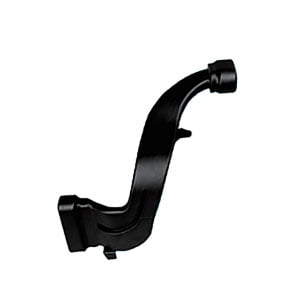
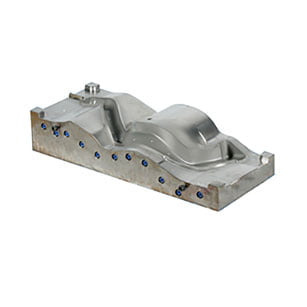
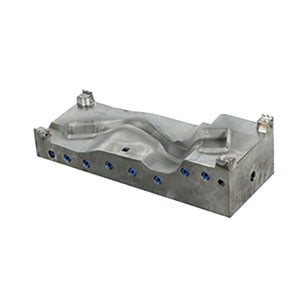
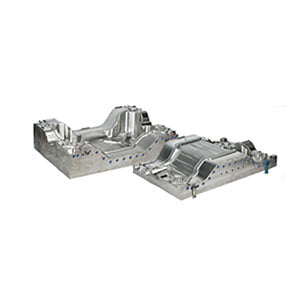
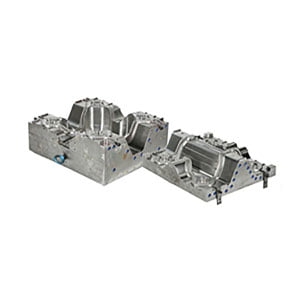
Our Blow Molding manufacturing Capability
The company useful mold assembly workshop, mold processing workshop, mould assembly workshop, mold testing workshop and a series of perfect workshop configuration, Made it to the mold layer. upon layer the control, the attitude of the best, toensure the high quality of high stability.
Blow Molding Manufacturing FAQs
Blow molding is a method of processing plastics by blowing heated plastic material into a mold, which is then shaped into the desired shape by applying pressure.
Blow molding is mainly divided into three types: single-layer blow molding, multi-layer blow molding and injection blow molding.
Blow molding works by placing heated plastic material into a mold and blowing it with air or nitrogen to conform to the surface of the mold to form a molded part.
Blow molding can process most thermoplastics, such as polyethylene, polypropylene, polyvinyl chloride, polycarbonate, polystyrene, etc.
Blow molding can process various shapes, such as cylindrical, spherical, bottle-shaped, flat, special-shaped, etc.
The advantages of blow molding are high production efficiency, low cost, short production cycle, smooth surface of finished product, and high complexity of product shape.
The disadvantages of blow molding are long production cycle, low product dimensional accuracy, difficulty in controlling wall thickness and size, and inability to process high-temperature materials.
The difference between blow molding and injection molding is that blow molding is formed by blowing heated plastic material, while injection molding is formed by injecting heated plastic material into a mold.
The difference between blow molding and extrusion molding is that blow molding is formed by blowing heated plastic material, while extrusion molding is formed by extruding heated plastic material.
The difference between blow molding and thermoforming is that blow molding is formed by blowing heated plastic material, while thermoforming is formed by pressing or extruding heated plastic material.
The production process of blow molding generally includes raw material processing, preform preparation, preform heating and blowing, mold forming, cooling, cutting, finishing and other steps.
Common question in Blow Molding Production
Blow molding is widely used in the production of plastic bottles, plastic buckets, plastic toys, plastic pipes, auto parts, medical equipment and other fields.
The mold in blow molding is a tool used to prepare molded parts, and its shape and size should match the molded parts.
The material of the mold has an impact on blow molding, and the mold material is generally required to have high strength, high wear resistance, high corrosion resistance and other characteristics.
Blow-molded products have a smooth surface and can usually be used directly without secondary processing.
The uniformity of wall thickness of blow-molded products is affected by many factors, such as mold design, fluidity of plastic materials, blowing pressure, etc.
The dimensional accuracy of blow-molded products is generally low and difficult to control. Generally, the dimensional error of the product can only be guaranteed within a certain range.
Blow molded products can be recycled, but due to the poor mixing of materials during their manufacture, recycled materials can be of lower quality and require secondary processing.
The production cycle of blow molding varies according to the shape and size of the product, generally ranging from a few seconds to a few minutes.
The production cost of blow molding is relatively low because of its high production efficiency, high utilization of raw materials, and relatively low mold manufacturing costs.
Blow molding has a high degree of automation, most of the production process can be automatically controlled and monitored, and the production efficiency is high.
The durability of blow-molded products varies depending on the product material and manufacturing process. Generally speaking, its products have better wear resistance and corrosion resistance.
Blow-molded products can be customized as needed and generally can withstand higher temperatures and pressures.
Blow-molded products can be printed and sprayed, but factors such as the smoothness and adhesion of the product surface need to be considered.