High vacuum die-casting technology has developed rapidly, and has been widely used in aerospace, weapons, ships, instruments, valve bodies, household appliances, automobiles and other industries. The core of high vacuum die casting technology is the innovative design of vacuum exhaust valve. By accepting the die casting machine's opening, closing and injection signals, the operation procedures of vacuuming, measuring vacuum degree and blowing compressed air to clean vacuum valve are completed to ensure that the alloy liquid is pressed and formed under vacuum. The products formed by this vacuum die-casting technology have strong toughness and strength, which can enhance the core competitiveness of enterprises in the high-end die-casting market, and also make important contributions to improve the economic benefits of enterprises.
I. Working principle of high vacuum die casting
(1)The so-called vacuum refers to the space with absolutely no material. When we talk about a vacuum, we mean that air and other gases are pushed out. High vacuum die-casting method refers to the gas part of the cavity is extruded or fully evacuated, so that the pressure in the cavity will be reduced, but also can promote the gas discharge in the alloy liquid, help the alloy liquid forming as soon as possible. The die castings formed by high vacuum die casting have very high compactness, high strength and toughness, which can be used in a variety of manufacturing industries, and the development prospect is very broad.
(2) High vacuum die casting method and working principle High vacuum die casting technology is a new technology development project. At present, there are two main methods of high vacuum die casting technology. These two high vacuum die casting technologies are both from Germany. One is the VA-Cural method developed by Muller-Weingarten and Vaw, and the other is the MFT method developed by AlCAN-BDW. The working principle of VA-Cural high vacuum die casting method is shown in Figure 1. l Holding furnace 2. Pressure shot punch 3. Dynamic model 4. Vacuum valve 5. Cavity 6. Fixed mold 7 injection chamber 8.
Working principle of high vacuum die casting: connect the molten furnace with the rising pipe to the injection chamber, first draw out the gas in the alloy liquid to reach a high vacuum degree (pressure below 10kPa), and then use multiple sprays to ensure that the alloy liquid fills the cavity in the shortest time. Especially the MFT method, the common die casting machine is widely used, which can greatly reduce the production cost, and the application prospect is very broad. Secondly, high vacuum die-casting technology involves many technical fields, such as metal solution treatment, mold structure design, casting process and selection of release agent production, etc. Only by achieving multiple integration, can the value of high vacuum die-casting technology be reflected.
2.Development of high vacuum die casting technology
(1) High vacuum die-casting vacuum cut-off valve The cut-off valve is the core of high vacuum die-casting technology. The exhaust passage is closed by the inertial impact force of the alloy liquid, and connected by lever mode. The connection mode is driven by active one driven by two pistons. The vacuum globe valve uses both active and driven piston levers to enable the piston to obtain large displacement, which greatly improves the sensitivity and reliability of globe valve closing.
(2) High vacuum die-casting vacuum system When casting in high vacuum, it is necessary to ensure that the vacuum in the cavity reaches more than 91kPa, and only maintain a large pumping speed can be completed in the shortest time. Therefore, it is necessary to use a large buffer tank to extract the gas in the cavity. The gas in the buffer tank needs to be continuously pumped out by a vacuum pump.
(3)High vacuum die casting powder coating Powder release agent is an essential lubrication material for casting. The action principle of the release agent is based on the raw wax, put these release agents into the pressure chamber, under the action of cavity temperature, begin to melt and adhere to the surface of the mold wall, can play the role of lubrication. Powder release agent has excellent film performance and good environmental protection, which can greatly improve the production efficiency. In order to reduce the production cost of powder release agent, the development of powder release agent has achieved remarkable results.
Nowadays, most of the powder release agents used in alloy die casting choose quartz, mica, talc and graphite as the main components, appropriate to add boron nitride, microcrystalline wax, etc. According to the experiment, when talC accounted for 50%, graphite accounted for 25%, boron nitride accounted for 15%, microcrystalline wax and other components accounted for 10% in the production of powder release agent, the spraying property and release property reached a very high standard.
(4) high vacuum die casting mould sealing method is the key technology of high vacuum die casting technology is the effect of extraction to meet the requirements, the use of the buffer tank vacuum degree and extraction time, can effectively promote the high vacuum extraction index, but the sealing problem of die casting mould still nots allow to ignore, once the seal is not good, always the volume is too big, can also lead to high vacuum. Therefore, in high vacuum die casting, it is necessary to carry out relevant technical improvement operations.
First of all, a sealing plate is added behind the moving die plate, and the sealing groove and the buffer groove are arranged on the sealing plate; The second is in the injection chamber and die bottom plate, punch, and injection chamber wall on the sealing groove; In addition, all buffer gas tanks are connected with the exhaust system. If a small amount of gas enters the seal ring, the buffer gas tank can be used to extract it to avoid entering the mold cavity.
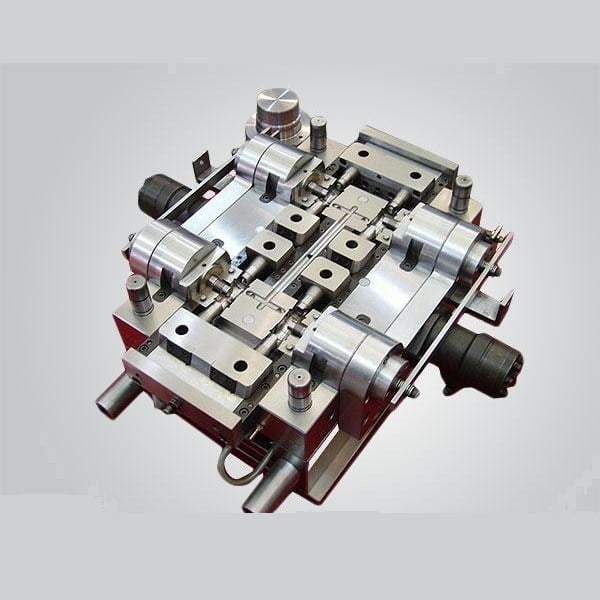
3.Development trend of high vacuum die casting
(1)Technical Advantages of high vacuum die casting High vacuum die casting technology has more technical advantages than ordinary die casting.
① High vacuum die casting technology is easy to operate, high efficiency, and the casting dimensional accuracy is greatly improved;
②High vacuum die-casting manufacturing is controlled by computer, using touch screen display, input data, very intuitive and simple;
③The high vacuum die casting control system matches the die casting machine, which can automatically detect the vacuum degree in the mold cavity, and can also automatically detect, clean and alarm the vacuum pipeline.
④High vacuum die-casting technology with stop valve, mostly lever type, "main - from" piston movement mode. This operation mode, switch sensitive, reasonable structure, quick response, has the characteristics of long life, convenient maintenance, short travel and so on;
⑤ High vacuum die casting mold adopts sealing structure, less leakage, high vacuum in the cavity.
(2) Application Prospect of high vacuum die-casting castings The development of high vacuum die-casting technology is amazing. In order to pursue the fineness and lightweight of parts, parts have begun to be pieced together and cast as a whole. Especially in some demanding industries, such as aerospace, weapons, ships, etc., all need to have large, thin wall, complex and other characteristics. If the United States ADM a 89B cruise missile, is the use of such technology production, greatly reducing the quality and production costs.
(3) Technical countermeasures for process suitability
① Alloy liquid filling. When die casting thin-wall and complex castings, the wall thickness is mostly 1-1.5mm, even the thickness is as thin as 0.75mm, and the shape is complex and diverse, especially for some large and super large integral castings, the size of 5005000mm, the alloy liquid filling problem is difficult to complete. Although the shape of some castings is simple, the surface area is large and the filling flow diameter is too long, which also brings problems to the alloy liquid filling. If the high vacuum die-casting technology is adopted, the three main factors affecting the alloy liquid filling can be effectively eliminated, and the heat conductivity of the dispersed inner runner can be greatly reduced by the hot film casting and the gypsum casting process, which can successfully solve the difficult problem of the alloy liquid filling of long and narrow and complex castings.
②Reinforcing of dispersed hot joints. In the ordinary casting, if the surface area of the casting is large, the wall thickness is thin, it is difficult to complete in the complete sequence solidification temperature field, and the dispersion hot joint is difficult to fill, it is easy to cause shrinkage cavity, shrinkage porosity and other defects of the casting. The high vacuum die-casting technology can make the casting uniform compression in the solidification process, avoid the phenomenon of uneven compression cavity, shrinkage porosity and so on, and effectively realize the feeding of dispersed hot joints.
(4)the application of high vacuum die casting technology and look forward to high vacuum die casting technology rapid development, but in some technology, has technology need to through many experiments to gain a systemic process parameters, according to the test data analysis form high vacuum die casting solidification characteristics, alloy material performance parameters such as the database. It is necessary to improve the mechanization, automation and serialization degree of high vacuum die-casting equipment through technical reform, so as to make the high vacuum die-casting technology become more and more mature, and create good conditions for vigorously promoting this technology.
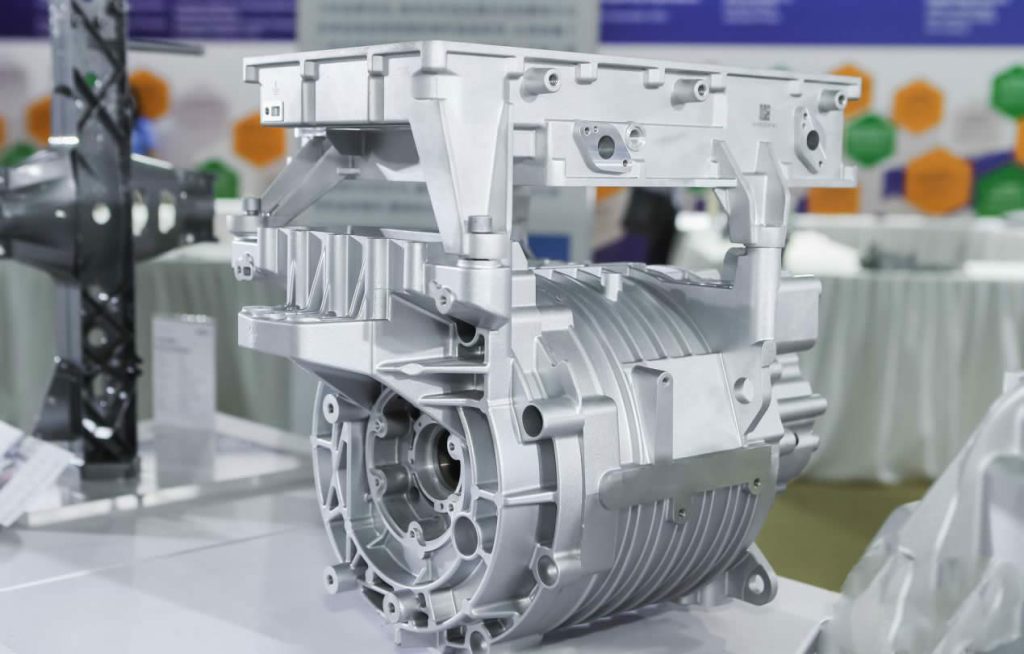