Table of Contents:
- Introduction to Aluminium Die Casting
- Applications of Aluminium Die Casting
- Techniques in Aluminium Die Casting
- Aluminium Die Casting Alloys
- Innovation in Aluminium Die Casting
- Quality Control in Aluminium Die Casting
- Maintenance and Care for Aluminium Die Casting Machines
- Environmental Impact of Aluminium Die Casting
- Conclusion
-
1. Introduction to Aluminium Die Casting
Aluminum die casting is a process that involves the injection of molten aluminum into a high-quality steel mold, or die, under high pressure. The process is used to produce complex and intricate shapes with high precision and accuracy. Aluminium die casting is widely used across various industries, including automotive, aerospace, consumer goods, and electronics, among others.
Aluminum die casting is ideal for the production of lightweight and strong parts with excellent heat dissipation and corrosion resistance properties. The process provides flexibility in design and reduces the need for secondary operations, reducing costs and increasing efficiency. The resulting products have high durability and are capable of withstanding harsh environments.
In the die casting process, molten aluminum is injected into a die under high pressure, and then the mold is cooled until the aluminum solidifies. The final product is then removed from the die before being subjected to finishing operations like machining, trimming, and painting. The die casting process can produce complex shapes with tight tolerances and high precision, making it suitable for high volume production.
Overall, aluminum die casting is a versatile and cost-effective process that is used across various industries and benefits from the material’s unique properties resulting in the creation of high-quality and durable products.
-
2. Applications of Aluminium Die Casting
Aluminum die casting is a versatile process that can be used to produce high-quality aluminum alloy parts with a wide range of properties. It is used in many industries and applications, including:
- Automotive Industry: Aluminum die casting is commonly used in the production of automotive parts, including engine and transmission components, door handles, and brake systems. The process can produce parts with tight tolerances, high strength, and excellent heat dissipation properties, making them ideal for performance-critical components.
- Aerospace Industry: The aeronautical industry utilizes aluminum die casting to create various structural components, including engine and gearbox housings and other parts. Aluminum die cast parts can help improve fuel efficiency by reducing overall weight, while offering exceptional strength.
- Electronics Industry: Aluminum die casting is used to manufacture electrical components, including heat sinks and casings, used in electronic devices like computers, TVs, and smartphones.
- Consumer Goods Industry: Aluminum die casting is used to create a variety of consumer goods, including kitchen utensils, sporting goods, and furniture components, due to their strength and durability.
- Medical and Healthcare: Medical equipment’s application like surgical tools and other medical devices rely on a high precision process that results in parts free of porosity and capable of combating the environment.
Overall, the aluminum die casting process offers numerous advantages, enabling it to produce intricate, strong, and lightweight parts that meet specific application requirements. The process is continuously evolving, with improved technology and innovation resulting in expanded accessibility in the market, high-volume and cost-effective production, and generating superior quality and reliability to the products.
-
3. Techniques in Aluminium Die Casting
Aluminum die casting is a highly versatile manufacturing process used to produce high-quality parts for a wide range of industries. Different techniques are used within the die casting process to create various parts with specific properties. Here are some common techniques in aluminum die casting:
- Cold Chamber Die Casting: This method utilizes a cold chamber linked inside of the die casting machine. Molten aluminum is poured into the chamber and then injected into the die. The technique is predominantly used for processing aluminum alloys with a high melting point and ensures that the molten aluminum does not come into direct contact with high-temperature components.
- Hot Chamber Die Casting: This particular method is frequently used with alloys that have lower melting points, such as magnesium and zinc. In this process, a small portion of the metal is remelted each time it is cast, eliminating the need for a separate melting furnace.
- Vacuum Die Casting: This technique safeguards the cast’s quality from porosity when higher-quality finishes are required. The vacuum technique involves removing air from the die chamber before injection of molten aluminum, reducing the occurrence of flaws and defects during casting.
- Squeeze Die Casting: This variation of die-casting makes use of two core parts of dies, between which the molten aluminum is injected under high pressures. This method produces parts that are compact, have a high tolerance, and provide an aesthetics finish.
All of these techniques involve precise control of variables such as temperature, pressure, dwell time, and flow rate, and are designed to produce intricate and precise aluminum parts. The choice of die casting technique depends on the specific needs of the application, the alloy being used, and the desired final product properties.
In conclusion, various techniques are involved in aluminum die casting, each with specific advantages such as increased accuracy, reduced porosity, and higher tolerances. The selection of the technique is critical in manufacturing aluminum parts that meet specific purposes and offer optimal quality and performance.
If you need about Die Casting Services,You can click on the V1 Prototype website to find it.
-
4. Aluminium Die Casting Alloys
Aluminum die casting alloys are essential components in the production of high-quality parts that are strong, durable, and lightweight. The selection of an alloy for a specific application depends on the desired properties of the final product, including strength, hardness, and corrosion resistance. Here are some of the most common aluminum die casting alloys used in manufacturing:
- A380: This aluminum die casting alloy is widely used in the automotive and appliance industries. It has good fluidity, excellent pressure tightness, and is easy to work with.
- 413: This alloy has excellent machining properties and is often used in applications where intricate parts need to be made. It contains a high level of silicon, offering increased resistance to thermal shock.
- 360: This alloy has excellent corrosion resistance and is used in applications where parts will be in contact with harsh chemicals and environments, such as marine applications.
- 6061: This high-strength aluminum alloy is used in applications that require excellent strength and durability, including aerospace and transportation.
- 383: This aluminum die casting alloy is known for its high resistance to cracking and excellent thermal conductivity, making it suitable for automotive applications like engine and transmission parts.
- ADC-12: This alloy contains a high level of silicon and other trace elements, providing excellent castability and light-weight characteristic. It is suitable for large intricate items like automotive engine blocks.
Overall, the selection of an aluminum die casting alloy depends on the specific requirements of the application. Consideration of factors such as strength, heat resistance, corrosion resistance, and machinability aids in the selection of the appropriate aluminum die casting alloy chosen for manufacturing.
-
5. Innovation in Aluminium Die Casting
The aluminum die casting industry is continually evolving, driven by the need for cost-effective, high-quality parts, and increased sustainability efforts. There has been significant innovation throughout the industry, and some of the latest advancements are described below.
- The use of High-pressure Die Casting Machines: A high-pressure die casting machine allows the use of thinner wall thicknesses, reducing the massive amount of material per part; that means, huge cost savings of the fixed costs involved. Also, utilizing automation reduces labor costs and production timeframe while prompting several aspects of high-quality properties to the parts.
- 3D Printing Applications: 3D printing technology enables testing of prototypes at a reduced cost since molds do involve exorbitant cost, the use of 3D printing supplements the ability to test structural integrity, offering a cost advantage with less material usage throughout the production process.
- Application of Hybrid Materials: Die casting combined with other materials encourages versatility on the finished products of manufacture, thus extending the ranges of product application. An example of such hybrids is die-casting aluminum with reinforced thermoplastics.
- Artificial Intelligence and Machine Learning: Integration of AI in manufacturing lines is helping improve productivity and quality control by refining the process, such as monitoring temperature and pressure fluctuations throughout the manufacturing process.
- Eco-Friendly Approaches: The use of eco-friendly materials such as recycled aluminum, and environmentally sustainable procedures, conserving energy usage and reducing waste throughout the production cycle, is an innovative approach being adopted by manufacturing companies.
The innovations mentioned above illustrate the advancements of aluminum die casting manufacturing, significantly reducing cost with low energy usage and less waste generation, and offering enhanced flexibility, functional quality, and high quality finished products. With pioneering technologies, sustainability, and cost-effectiveness, the future of the industry is continually growing to keep up with the ever-changing global trends.
-
6. Quality Control in Aluminium Die Casting
Quality control is essential to ensure that the manufactured aluminum die cast parts meet the required specifications, standards, and expectations concerning their performance, safety, and quality. In aluminum die casting, several quality control practices are implemented to inspect and test the quality of the final products. Here are some common quality control techniques used in aluminum die casting:
- Visual Inspection: This is one of the earliest stages of quality control where the parts are inspected against the desired specifications, checking for defects or deviations like porosity, deformation, cracks, and other abnormalities. Such inspections are time-efficient and less costly.
- Dimensional Inspection: Dimensions play an important role in the matching of machined parts or assembly. Therefore, it is necessary to ensure accurate specifications to avoid errors in production. Measurement tools and gauge are used to compare the final measurements to ensure their conformity to specifications, ensuring accurate adherences to design requirements.
- Material Inspection- Chemical and Mechanical: A significant part of the quality assurance process is the material inspection. The chemical composition of the alloy is analyzed to ensure that the finished casting has the desired properties for its specific purposes. Mechanical testing functions to verify the alloy’s strength, tolerance, toughness, and other mechanical properties.
- Non-Destructive Testing (NDT): Non-destructive testing involves testing the parts for structural integrity, detecting possible flaws or cracks within the casting, without altering them in any way. It includes tests like Ultrasonic, Radiographic and Magnetic Particle inspection.
- Simulation Analysis: Advanced Simulation tools are capable of predicting the behavior of casting designs under specific process conditions. Simulations assist in identifying errors or areas of improvement, allowing for modifications to design or process parameters prior to mold-making.
Overall, the aluminum die casting inspection processes help detect defects, errors, or imperfections, that can lead to fatal consequences, product recalls, or warranty claims. Regular quality checks ensure that the finished product meets the desired specifications, establishing reliability, durability, and functionality.These procedures contribute towards producing an end product that is safe, high-quality, meets standards and specifications, and gaining the trust of the customers.
-
7. Maintenance and Care for Aluminium Die Casting Machines
Maintenance and care of aluminum die casting machines play a crucial role in ensuring the longevity of the equipment while ensuring the durability, accuracy, and quality of the casting components. Regular maintenance ensures reliable and efficient production, reducing downtime periods, and lowering costs incurred from repairing or replacing components. Here are some essential maintenance and care practices for aluminum die casting machines:
- Inspection: Regular inspection of die casting equipment and components is essential in detecting and rectifying minor issues before they become more significant practical problems. This involves checking the equipment for lubrication, deterioration, wear, and tear or signs of defect prior to casting operations.
- Lubrication: It is essential to lubricate the mold carefully, safeguarding it against damage from daily wear and tear. Consequently, the mold can last longer, perform better, and improve products’ quality. Lubrication should be performed daily after unimpeded mold removal.
- Cleaning: Consistent cleaning of die casting machines is critical to eliminating dirt, contaminants, and other foreign matter that can impede equipment functionality. Such detritus can hinder production quality, mold integrity, and lower machine longevity. Cleaning should not scratch the mold cavity surface as damages can affect the next production renders.
- Electrical and Hydraulic Systems: The preventative maintenance is instrumental in upholding the correct function of hydraulics and electronics. Checks on equipment regarding the interchanges of hydraulic fluids, replenishing of hydraulic oil, and circuit board malfunctions for electrical functions, among others, are essential.
- Cooling and Heating Systems: Consistent maintenance of the hot chamber creates an impact on the manufactured components through pressures and temperature controlled condition evenness. Fan filters and coolant filter replacement, together with component oil level checks, ensure smooth operation.
Overall, preventative maintenance practices extend the life of aluminium die casting machines, thereby bolstering productivity and boosting production quality. By following the care and safeguard guidelines of manufacturing components, companies can prevent expensive maintenance, downtime and ultimately gain a critical edge over their competitors.
-
8. Environmental Impact of Aluminium Die Casting
The environmental impact of aluminum die casting is a crucial concern as products are being manufactured everywhere across the globe. Nonetheless, thankfully, the industry has been continuously adopting sustainable approaches and environmentally-friendly practices to reduce the impact on the environment. Here are some ways aluminum die casting impacts the environment:
- Energy Consumption: Aluminum die casting requires a high level of energy consumption; the process requires intense heating of the aluminum alloys, demanding considerable energy. However, the exertion has advanced as machinery now incorporates high-efficiency energy-saving features to curb energy wastage during heating.
- Waste Generation: The production of aluminum casting generates waste- molten metal drops, burrs, and sprues, among others. However, recycling is a reliable strategy to minimize waste generation. By recycling the waste, the manufacturing process becomes sustainable reduces potential environmental hazards and minimizes energy consumption.
- Greenhouse Emissions: The die-casting calls for heat elevations, which if left unchecked, can escalate the emission of greenhouse gases into the atmosphere. Industries have adopted low-emission melting technologies that reduce CO2 discharges, promoting environmentally responsible production practices.
- Chemical Disposal and Environmental Contamination: Disposing of chemicals utilized in aluminum casting, cleaning and other processes can result in environmental pollution. However, in response, industries have implemented environmentally friendly disposal practices to minimize the risk of contamination.
Overall, the aluminum die casting industry has been working actively to bolster sustainable production processes and environmentally friendly practices through recycling, reduction of greenhouse-gas emissions, advanced energy management, waste reduction, and sustainable disposal of products. These modern practices showcase an industry that is not only committed to manufacturing high-quality products but also shows reference to environmental stewardship, and promotes corporate social responsibility.
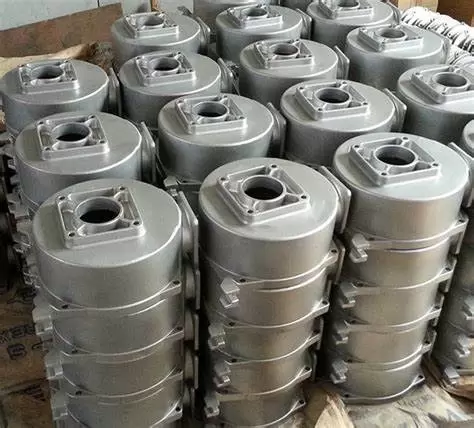
-
9. Conclusion
In conclusion, aluminum die casting is a versatile manufacturing process that produces high-quality, durable, and lightweight parts for various industries. The production of aluminum die casting requires the adoption of environmentally responsible and sustainable practices to minimize the emission of greenhouse gases, waste production, and the disposal of harmful chemicals. Some advancements in the aluminum die casting industry include the use of 3D printing, hybrid materials, and artificial intelligence, among others, leading to cost-effectiveness, versatility, and high-quality finished products. Quality control measures, such as visual inspection and non-destructive testing, ensure that the finished products meet the desired specifications, resulting in reliable and safe end products. Consistent maintenance and care practices help extend the life of the equipment, leading to increased production efficiency, reduced downtime periods, and lower costs incurred from repair or replacement of die casting equipment. The aluminum die casting industry is moving towards increased sustainability, promoting environmental stewardship, and social responsibility.