Table of Contents:
- Introduction
- Materials Used for High Precision Parts
- Techniques for High Precision Manufacturing
- Applications of High Precision Parts
- Quality Control and Inspection
- Challenges and Solutions
- Conclusion
-
1.Introduction
High precision manufacturing is becoming increasingly important in today’s world. With advancements in technology and the growing demand for high-quality products, precision parts and components are required for various applications in industries such as aerospace, medical, automotive, consumer goods, and electronics. This article will provide an overview of high precision manufacturing, including materials used, techniques for production, applications, quality control, and challenges and solutions.
-
2. Materials Used for High Precision Parts
A. Types of Metals Used
Stainless steel, aluminum alloys, titanium alloys, and other high-strength metals are preferred for high precision manufacturing applications, as they offer high strength, corrosion resistance, and durability.
B. Specialty Plastics
Specialty plastics such as PEEK, polycarbonate, and acetal are also commonly used in high precision manufacturing due to their chemical resistance, wear resistance, and light weight properties.
C. Ceramics
Ceramic materials such as zirconia, alumina, and silicon carbide are used for high precision parts due to their high mechanical strength, low thermal expansion, and high wear resistance.
-
3. Techniques for High Precision Manufacturing
A. Machining Processes
Machining processes such as CNC milling, turning, and grinding are commonly used for the production of high precision components. These techniques require a high level of accuracy and control.
B. Additive Manufacturing
Additive manufacturing techniques such as 3D printing and rapid prototyping enable the production of complex and high-precision components with minimal material waste.
C. Laser Cutting and Welding Techniques
Laser cutting and welding techniques are commonly used for the production of high precision components in industries such as automotive, aerospace, and medical.
D. Surface Treatment Processes
Surface treatment processes such as electroplating, anodizing, and chemical etching are used to enhance the properties of components for high precision applications, such as wear resistance and corrosion resistance.
If you want more about high precision parts information ,You can click on the V1 Prototype website to find it.
-
4. Applications of High Precision Parts
A. Aerospace Manufacturing
Aerospace manufacturers rely on precision components for aircraft parts such as turbine blades, landing gear, and aerospace actuators. These components must be made to specific tolerances and high standards to ensure safety and performance.
B. Medical Device Manufacturing
The medical device manufacturing industry requires high-precision components for applications such as surgical tools, implants, and diagnostic equipment. Cleanliness, biocompatibility, and precision are critical factors in these applications.
C. Electronics Manufacturing
Electronic components such as microchips and integrated circuits require high precision manufacturing for optimal performance. The manufacturing process must be clean and free from contamination, and the components must be precisely fabricated to ensure optimal performance.
D. Automotive Manufacturing
The automotive industry requires high precision components for applications such as engines, transmission systems, and steering systems. High precision manufacturing is critical in ensuring safety, reliability, and performance.
E. Consumer Goods Manufacturing
Consumer goods such as electronics, appliances, and tools require high precision components for optimal functionality and durability. High precision manufacturing techniques are used to ensure quality, consistency, and optimal performance.
-
5. Quality Control and Inspection
A. Metrology and Measuring Techniques
Metrology techniques such as coordinate measuring machines (CMMs) and optical measurement systems are used to measure components and ensure that they meet the required tolerances.
B. Statistical Process Control
Statistical Process Control (SPC) is used to monitor the manufacturing process and ensure that it is within the required specifications. SPC data is used to adjust the production process and maintain consistent quality.
C. Quality Management Process
A quality management process is an essential aspect of high precision manufacturing. This process ensures that quality is maintained throughout the manufacturing process, from design to final inspection.
-
6. Challenges and Solutions
A. Challenges in High Precision Manufacturing
Challenges in high precision manufacturing include complex geometries, tight tolerances, difficult materials, and strict quality control requirements.
B. Innovative Solutions
Innovative solutions such as automation, machine learning, and digital twins are being used to address challenges in high precision manufacturing. These solutions enable manufacturers to achieve higher precision and efficiency in the production process.
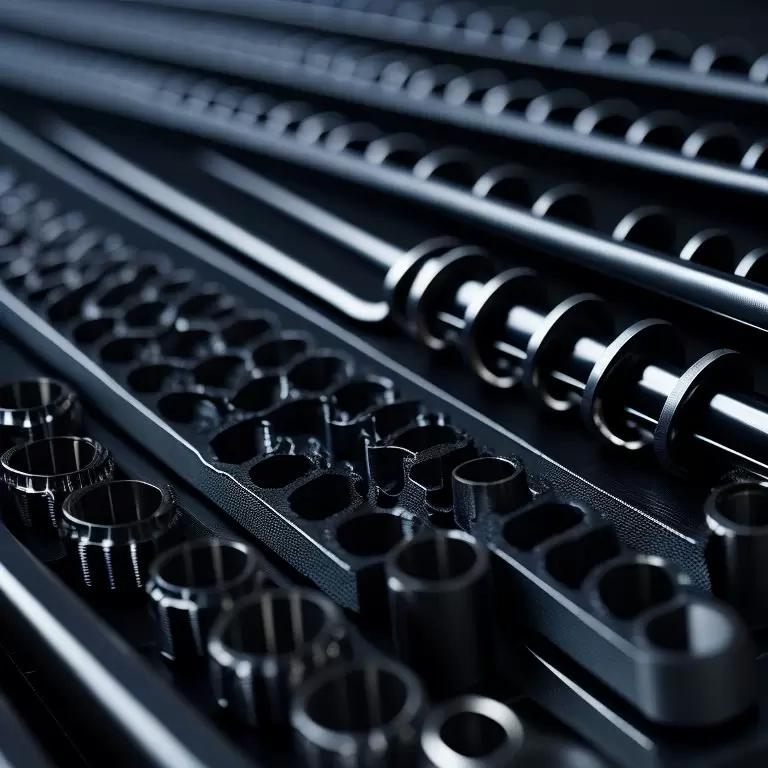
-
6. Conclusion
High precision manufacturing has become essential in today’s world, with industries such as aerospace, medical, automotive, consumer goods, and electronics relying on high-precision components for optimal performance. By using advanced materials and techniques, and ensuring strict quality control, manufacturers can produce high-quality, consistent, and durable components. As technology continues to advance, high precision manufacturing is expected to continue to play a significant role in various industries, driving innovation and progress in manufacturing.