Table of Contents:
- Introduction to Injection Moulding
- Steps in Injection Moulding Process
- Injection Moulding Process Variables
- Quality Control Parameters
- Common Injection Moulding Issues and Their Solutions
- Advanced Injection Moulding Techniques
- Injection Moulding Applications
- Conclusion
-
1.Introduction to Injection Moulding
Injection moulding is a popular manufacturing process that is widely used in the production of a variety of products such as household appliances, consumer goods, aerospace parts, and automotive parts. This process relies on the use of specialized machinery to produce 3-dimensional parts by injecting molten material into a custom-made mold, then cooling and solidifying the material to complete the part.
Advantages of injection moulding include creating complex geometries, repeatable and is capable of high-volume production. Limitations are the high costs of setup and design limitation concerned with the mold construction.
-
2. Steps in Injection Moulding Process
The injection moulding process comprises six steps: mold design and preparation, material selection, material preparation, injection moulding machine set-up, injection moulding process detail, and post-processing finishing activities.
Step 1: Design and Preparing the Mold
Before the injection moulding process can begin, the injection mould needs to be designed and manufactured. This step involves identifying the required material and part shape, which are unique to each individual product. Mold preparation includes cleaning, checking the joints and their fit, and ensuring that the mold meets industry standards.
Step 2: Material Selection
Identifying the proper materials that are suitable for the product, end-use, and operating environment is essential for achieving the desired product performance. This step requires a comprehensive study of the material rights like stiffness, strength, and heat resistance, amongst others.
Step 3: Preparing the Material
In this stage, the raw material is prepared for injection into the mold. The material must be fed into the machine, sorted, and heated until it meets the required melting point specific to the material.
Step 4: Injection Moulding Machine Set-up
Mold and material are both complete, and the injection mold machine must be prepped. Referred to as “set-up,” this stage involves calibration of the machine such as temperature and pressure.
Step 5: Injection Moulding Process Detail
In this step, the actual injection moulding process happens. It involves clamping, injecting the material, solidifying or cooling the material, and finally, ejection of the final product.
Step 6: Post-processing Finishing Activities
Post-processing finishing activities are required to take care of any extra sprue, flash, or excess material that may be present on the finished product. Sanding, trimming, and quality control are also essential steps at this last stage of production.
-
3. Injection Moulding Process Variables
Injection moulding process variables are essential to the success of the overall manufacturing process. In this section, we will explore some of the critical process variables that require careful consideration.
Temperature:Temperature is a key factor in the injection moulding process, impacting the viscosity of the material, filling speed, cycle time, and material quality. Temperature can significantly impact the final product’s quality and lead to defects such as warping, deformation, and uneven surface texture.
Pressure:Pressure is vital for the proper filling of the material into the mould. Adequate pressure will ensure that the material fills the entire cavity uniformly, resulting in a high-quality product with consistent thickness. The pressure must also be carefully controlled to avoid overpacking that could cause cracking, or creating parts that may delaminate.
Fill rate:The rate at which material fills the mould cavity must be controlled with the greatest of care. If the fill rate is too slow, it will lead to defects such as burns and knit lines, compromising the material performance due to voids. Alternatively, if the fill rate is too fast, the parts could become weak and undersized.
Cooling time:Cooling time is the amount of time that a moulding takes to cool down to its initial temperature following injection. The cooling time causes the material to solidify into its final shape, curing into the designed shape. The length of cooling time should be appropriate and can vary depending on the material and the part size.
Mold temperature:The mold temperature is critical in the injection moulding process, and it must be precisely controlled. The mold’s temperature impacts the cycle time, warpage, sink marks, and surface finish. Generally, a higher mold temperature will make the moulding process faster while also providing a better surface finish. However, higher temperatures may cause the moulding to warp. The material’s specific heat capacity and thermal conductivity should be taken into consideration when setting mold temperature.
In conclusion, adequate control of product temperature, pressure, fill rate, cooling time, and mold temperature remains fundamental to the injection moulding process. Proper control and optimization of the specified process variables are essential for achieving high-quality products consistently. By understanding these critical variables, manufacturers can optimize the injection moulding process to produce high-quality parts that match the exact specifications of the application.
-
4. Quality Control Parameters
Maintaining high quality standards is crucial in the injection moulding process. In this section, we will discuss several quality control parameters that manufacturers must adhere to achieve a high-quality finished product.
Wall Thickness Control:Wall thickness control is essential in the injection moulding process to ensure the parts meet the required design specifications. Wall thickness should be consistent throughout the designed part. Deviating from the expected wall thickness can lead to structural defects such as warping or bowing, influencing the required physical properties.
Dimensional Accuracy & Tolerance:Dimensional accuracy and tolerance in injection moulding refer to ensuring that the final product meets the required specifications of the design. The measurements must be correct and within the tolerance range specified, with no deviations from the required specifications.
Surface Finish:The surface finish of the final product needs to match the specified requirements. Common surface finish requirements may include textured, matte, or glossy finishes. Surface defects such as flashes or burrs must also be avoided or eliminated during the post-processing activities, which can negatively impact the surface finish.
Defects:Various defects can occur in the injection moulding process, such as gate blush, sink marks, or flash formation. These can alter the mechanical properties, such as stiffness or durability, and could influence the final part’s structural integrity. Correcting for these common injection moulding defects can be achieved through optimizing the process variables or re-defining the design specifications.
To address these quality control parameters, proper monitoring of every step in the injection moulding process is essential. Manufacturers must have an established quality control process that ensures each part is produced with the critical parameters noted above. Utilizing advanced measurement techniques such as precision measuring tools or inspection machines can help to prevent deviations and ensure accurate results.
By adhering to strict quality control procedures, manufacturers can consistently produce high-quality injection moulded parts that meet the desired product performance requirements. The importance of quality control may not be immediately visible, but it is crucial to ensuring reliable product performance and to ensure the customer’s satisfaction is met.
-
5. Common Injection Moulding Issues and Their Solutions
Though injection moulding is a reliable and efficient manufacturing process, it is not without its challenges. In this section, we will explore some of the most common injection moulding issues that manufacturers face, and their likely solutions.
Flash:Flash happens when material escapes from the mould cavity during the injection process, leading to material surfaces that go beyond the part design. The resultant material overhang can lead to part deformation and make the finishing more challenging.
Solution: Increasing clamping force, assigning gate location, and reducing fill speed can help reduce the occurrence of flash.
Short Shot:A short shot occurs when insufficient material is injected into the mould, causing the resultant part to be undersized or inadequately filled.
Solution: Checking material condition, increasing the injection speed, or increasing fill pressure to allow for complete filling will address this issue.
Sink Marks:Sink marks occur when the outer surface of the part’s thicker areas take longer to cool down, leading to an uneven transition effect.
Solution: Increasing fill pressure, cooling time, or avoiding uneven wall thickness can help prevent this problem.
Warping:Warping occurs when injection-moulded parts deform and no longer meet the required dimensional accuracy, caused by uneven cooling or thermal stress.
Solution: Reducing the mold temperature slowly, ensuring even distribution of cooling channels, and reducing injection speed can reduce the likelihood of warping.
In conclusion, injection molding issues such as flash, short shots, sink marks, and warping can be challenging to resolve. Thankfully, output problems can often be rectified by altering the machine settings, optimizing the temperature profile, and fine-tuning the mold design. Manufacturers will need to take a proactive approach by screening and investigating these problems daily to maintain high-quality standards. By addressing these common injection moulding issues promptly, manufacturers can minimize the cost of rejections and material waste, and ultimately produce a high-quality product that satisfies the customer’s expectations.
-
6. Advanced Injection Moulding Techniques
Advanced injection moulding techniques have revolutionized the manufacturing industry, offering more design freedom and better performance for the final product. In this section, we will discuss some of the advanced injection moulding techniques in use and their benefits.
Overmolding:Overmolding is a technique that involves using two different materials to mould a single product. The two different materials are injected subsequently or simultaneously in two different cavities to create a finished product with unique properties.
This technique is well-suited for manufacturing products that require different material properties on various parts in one assembly. Overmolding allows for a better ergonomic fit of the final product, adding durability, and reducing vibration noise.
Gas-Assisted Injection Moulding:Gas assisted injection moulding (GAIM) involves using gas to supplement the injection of molten plastic to form specific parts during the molding process. The gas is injected into the mould cavity during the fill process, preventing material injection filling inadequately, while providing additional benefits such as lower product weight, reduced cycle time, and an improved surface finish.
GAIM is suitable for making large parts with thick and thin-walled sections, corrugated tubes or sheets, and automotive components with anti-shrink properties.
Insert Moulding:
Insert moulding meshes traditional plastic injection moulding with metal, both being melted simultaneously in one cavity of the mould.
This technique is ideal for the manufacture of parts that require more robust support structures, such as electrical connectors, threaded connectors or handles.
Co-Injection Moulding:
Co-injection moulding is a technique where a core of the molded component is formed with a combination of multiple materials, simultaneously or in sequence.
The technique allows for improved bonding strength by aligning materials with unique features, and enhanced product performance. Among these materials could be reinforcing fibers, metals or biodegradable polymers. Co-injection moulding strengthens the quality of the finished product, enabling greater durability, thermal stability, and more advanced aesthetic properties.
In conclusion, advanced injection moulding techniques offer manufacturers the ability to create complex and durable products with improved product quality and longevity. Overmolding is flexible in accommodating various material properties, GAIM reducing weight and cost, Insert moulding providing robust support structures, and Co-injection moulding allows for bonding strength in two or more materials. Successful specialists use advanced injection moulding techniques to manufacture products that meet exact requirements and offer products suitable for diverse applications.
If you want more about Injection Moulding information ,You can click on the V1 Prototype website to find it.
-
7. Injection Moulding Applications
Injection moulding is a versatile manufacturing process that can be applied in the production of various products for different industries. In this section, we will discuss some of the most common applications of injection moulding.
Packaging:Injection moulding is commonly used in the packaging industry to produce a wide range of products like caps, closures, bottles, jars, and tubes. The process of injection moulding provides the necessary structural integrity for packaging products, especially those that will have to bear force, such as those for the food and beverage industry.
Automotive:The automotive industry widely utilizes injection moulding in the manufacture of various parts, from small components such as door handles to large parts such as bumpers. Injection moulding for the car parts enables the production of highly precise parts with excellent durability features, such as vibration resistance.
Medical:The medical industry benefits from injection moulding for producing check valves, valves, syringes, and various other medical devices. The plastic parts produced that meet bio-compatibility standards are non-invasive, and offer the necessary strength and durability for long-term use.
Consumer Goods:The consumer goods industry typically relies on injection moulding to produce products such as electronic parts, electrical connectors, sports equipment, toys, office supplies, and cosmetic containers. The process of injection moulding enables these products to be produced with high accuracy, consistency, and quality, improving the overall aesthetic appeal and functionality.
Aerospace:Injection moulding is increasingly valuable to the aerospace industry, especially due to the need to reduce weight in the manufacturing processes. Current applications of injection moulding in the aerospace industry include manufacturing complex components like brackets, housings, and control knobs.
In conclusion, injection moulding has enabled a wide variety of products to be produced in different sectors such as packaging, automotive, medical, consumer goods, and aerospace. The technology allows for the production of strong, durable, and highly accurate components, making it possible for manufacturers to design parts with high quality and value, and providing customizable solutions for different applications in different sectors.
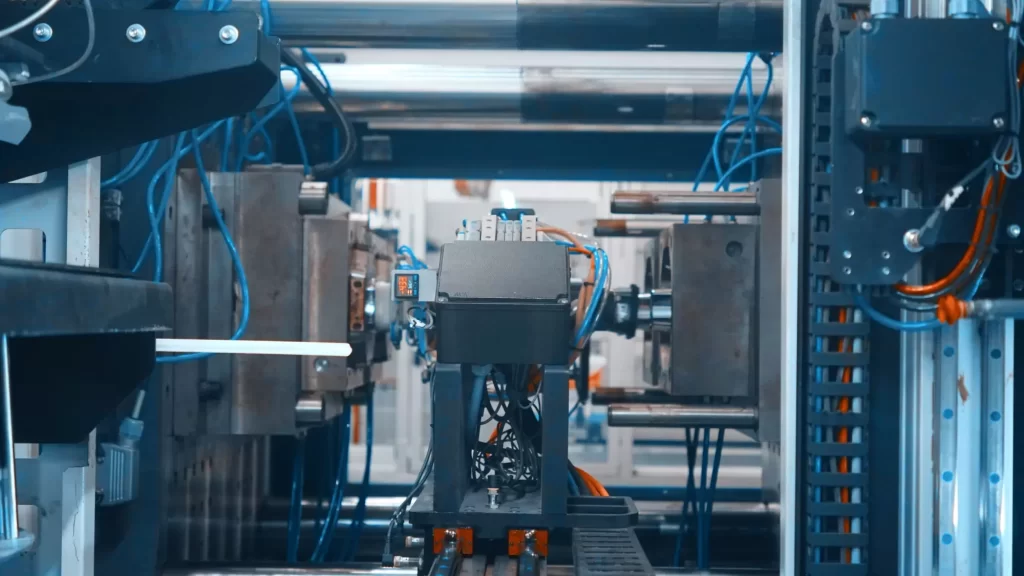
-
8. Conclusion
In conclusion, injection moulding is a versatile and efficient manufacturing process that has revolutionized the production of various products in different sectors. Here are some key takeaways from our discussion:
- Injection moulding requires careful consideration of process variables such as temperature, pressure, fill rate, cooling time, and mold temperature for high quality parts.
- Quality control parameters such as wall thickness control, dimensional accuracy and tolerance, surface finish, and defects are essential for consistent product quality.
- Advanced injection moulding techniques such as overmoulding, gas-assisted injection moulding, insert moulding, and co-injection moulding offer manufacturers added flexibility and product performance.
- Injection moulding has widespread applications in industries like packaging, automotive, medical, consumer goods, and aerospace.
.
Practical tips for injection moulding success include:
- Regular maintenance of the machine and tools.
- Optimizing the process variables to achieve the desired properties.
- Constant monitoring of the process to ensure quality.
- Proper documentation of the process and material parameters.
- Selecting the right materials for input to the process.
Overall, injection moulding remains an essential manufacturing process, as it enables manufacturers to produce high-quality products that meet specific applications’ unique requirements. By understanding the process’ critical parameters and considering advanced techniques, manufacturers can optimize their injection moulding processes and remain competitive in the market.