Table of Contents:
- Introduction to Rapid Tooling
- Rapid Tooling Techniques
- Rapid Tooling Materials
- Applications of Rapid Tooling
- Factors to Consider for Successful Rapid Tooling
- Pros and Cons of Rapid Tooling
- Conclusion
-
1.Introduction to Rapid Tooling
Rapid tooling is a manufacturing technique used to quickly produce tooling for a manufacturing process. It eliminates the need for expensive and time-consuming traditional tooling methods such as injection molding, casting, or drilling. Rapid tooling includes a variety of techniques, materials, and applications, making it a versatile process suitable for different industries.
-
2.Rapid Tooling Techniques
Additive Manufacturing: Additive manufacturing, also known as 3D printing, is a popular technique for creating rapid tooling. It involves building layers upon layers of materials using CAD or digital blueprints. The process is cost-effective and fast, allowing manufacturers to produce complex and intricate parts with ease.
CNC Machined Tooling: This technique involves the use of computer numerical control (CNC) machines to produce rapid tooling. CNC machined tooling is a highly accurate method of tooling production that uses a variety of materials such as metals, plastics, and composites to create tooling.
Soft Tooling: Soft tooling involves using soft, silicone molds to produce parts. It involves casting or injection molding with the silicone molds. Soft tooling is ideal for short production runs when traditional tooling is not cost-effective.
If you need about Rapid Tooling service,You can click on the V1 Prototype website to find it.Rapid Tooling With More Flexibility, Low Cost, Volume Speed, Finishing For Your Upcoming Products.
-
3.Rapid Tooling Materials
Metal Materials: Rapid tooling can use different types of metal materials like aluminum, steel, copper, and nickel-based alloys. Metal rapid tooling is ideal for applications that require high accuracy, durability, and consistency.
Plastic Materials: Different types of plastics materials can be used in rapid tooling such as ABS, Polycarbonate, Nylon, and Polypropylene. Plastic rapid tooling is ideal for prototyping, small volume applications, and low-cost production.
Composite Materials: Composite rapid tooling combines different materials to improve performance and make ideal for applications that require lightweight parts. Carbon fiber reinforced plastic is an increasingly popular material for composite rapid tooling.
-
4.Applications of Rapid Tooling
Medical Devices: Rapid tooling is used to produce medical devices such as orthoses, prostheses, and hearing aids. It helps in producing complex geometries of the medical devices quickly with high precision and quality.
Automotive Engineering: Rapid tooling is widely used in automotive engineering to produce different automotive parts speedily and cost-effectively. The automotive sector relies heavily on rapid tooling techniques to improve vehicle performance, reduce costs, and speed up the production process.
Aerospace Industry: The aerospace industry demands a high level of precision and accuracy, and rapid tooling techniques can deliver this. Rapid tooling is used in the production of aerospace parts like engine components, turbines, sensors, and aircraft interiors.
Consumer Products: Rapid tooling is also used in consumer products for producing prototypes and small volume production runs. It helps meet the ever-changing consumer demands for new product designs, features, and quality.
-
5.Factors to Consider for Successful Rapid Tooling
Cost-effectiveness: Rapid tooling provides a cost-effective solution when compared to traditional tooling methods. It can help manufacturers save costs on materials, labor, and production time.
Time to Market: Rapid tooling significantly improves the time to market for a product. It enables manufacturers to release products sooner, thereby gaining an edge over the competition.
Quality Control: Rapid tooling delivers high precision and accuracy, reducing the chances of product defects. It leads to better quality control, higher yields, and lower costs.
-
6.Pros and Cons of Rapid Tooling
Pros: Rapid tooling is cost-effective, faster, versatile, and produces high-quality tools. It is ideal for prototyping and low-volume production runs.
Cons: Rapid tooling, when compared to traditional tooling, is not suited or cost-effective for high-volume production runs. It also has design limitations and requires skilled labor and equipment to operate the machines.
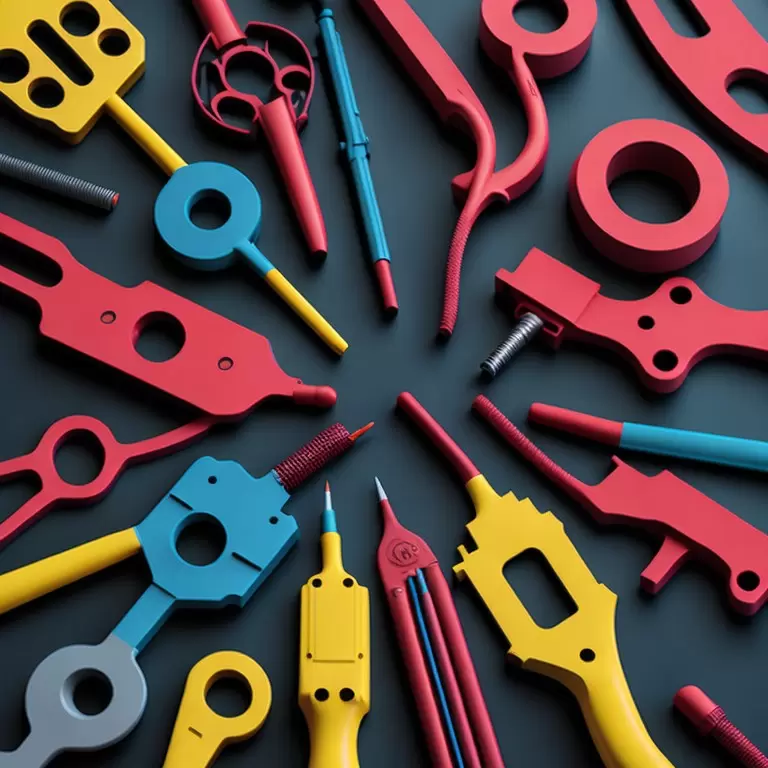
-
7.Conclusion
Rapid tooling provides a flexible solution for many different manufacturing applications. It offers a faster, cost-effective, and accurate way of producing tools and parts. The variety of techniques, materials, and applications make rapid tooling ideal for different industries like aerospace, automotive, and medical devices. With careful consideration of the factors involved, manufacturers can optimize rapid tooling to boost production efficiency and product quality while reducing production costs.