Table of Contents:
- Introduction
- Basics of CNC Programming
- CNC Programming Techniques
- Advanced CNC Programming Techniques
- CNC Programming for Specific Applications
- CNC Programming Best Practices
- Conclusion
-
1. Introduction
Computer Numerical Control (CNC) programming is a vital aspect of modern manufacturing. It involves using computer software to control automated machines, such as mills, lathes, and routers, to precisely cut, shape, and form raw materials into finished products. This article aims to provide a comprehensive guide to CNC programming, covering everything from the basics of G-code and M-code programming languages to advanced techniques for multi-axis machining, high-speed cutting, and 5-axis operations.
-
2. Basics of CNC Programming
To understand CNC programming, it is essential to first understand the basics of CNC machines and their components. CNC machines typically consist of a control unit, a motor, a spindle, and a tool. The control unit is where the CNC program is stored and executed, while the motor and spindle work together to move and rotate the tool. The tool is responsible for cutting, drilling, or shaping the material.
G-code and M-code are the two primary programming languages used in CNC programming. G-code is used to specify the tool’s movement and positioning, while M-code is used to control the machine’s auxiliary functions, such as coolant systems, tool changes, and spindle speed. CNC programs are typically structured in a specific format, with each command specifying a specific movement or function.
-
3. CNC Programming Techniques
CNC programming involves several techniques, including the use of CAD/CAM software, generating tool paths, and optimizing cutting parameters. CAD/CAM software allows programmers to create 3D models of the finished product, generate tool paths, and simulate the machining process. Tool path generation involves selecting the most efficient cutting paths to reduce machining time and minimize tool wear. Optimizing cutting parameters, such as feed rates and spindle speeds, can also help improve efficiency and reduce costs.
Macros are another important technique in CNC programming. Macros are pre-written pieces of code that can be reused for repetitive tasks, such as drilling holes or cutting slots. They help save time and reduce the risk of errors in programming.
Programming for multi-axis machining is also a critical technique in CNC programming. Multi-axis machines can move the tool in several directions simultaneously, allowing for more complex shapes and contours. However, programming for multi-axis machining requires more advanced knowledge of G-code and M-code.
-
4. Advanced CNC Programming Techniques
Advanced CNC programming techniques include implementing complex cutting strategies, using subroutines and loops for repetitive tasks, and applying advanced techniques for high-speed machining. Complex cutting strategies, such as adaptive milling and trochoidal milling, can help reduce machining time and improve surface finish quality. Subroutines and loops are used to repeat a series of commands, reducing the need for repetitive programming. Advanced techniques for high-speed machining involve optimizing cutting parameters and tool path strategies to achieve faster and more efficient machining.
Simulation software is another advanced technique in CNC programming. Simulation software allows programmers to simulate the machining process and identify potential errors or collisions before the program is executed on the actual machine. This helps reduce the risk of damage to the machine or the part being machined.
-
5. CNC Programming for Specific Applications
CNC programming can be tailored for specific applications, such as turning, milling, drilling, tapping, and surface finishing. Programming for turning operations involves specifying the tool’s movement along the axis of rotation, while milling operations involve specifying the tool’s movement in multiple directions. Drilling and tapping operations involve specifying the tool’s movement to create holes and threads, while surface finishing operations involve specifying the tool’s movement to achieve a specific surface finish.
Programming for 5-axis and 6-axis machining is another specialized application of CNC programming. 5-axis and 6-axis machines can move the tool in multiple directions simultaneously, allowing for more complex geometries and contours.
-
6. CNC Programming Best Practices
Efficient and effective CNC programming requires following best practices to ensure accuracy, consistency, and safety. Some best practices include properly documenting and organizing CNC programs, testing programs before running them on the machine, using the correct cutting tools and parameters, and regularly maintaining the machine to prevent breakdowns and ensure optimal performance.
It is also important to stay up to date with the latest developments and advancements in CNC programming, such as new software updates, cutting tools, and machining techniques. Continuing education and training can help improve skills and knowledge and lead to more efficient and effective CNC programming.
If you need more other the information ,You can click on the V1 Prototype website to find it.
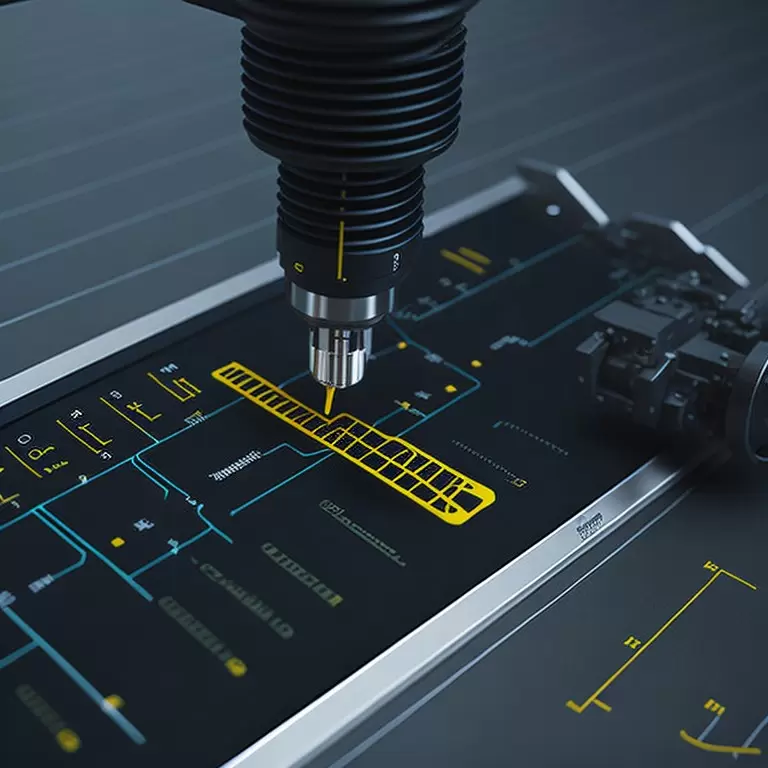
-
7. Conclusion
CNC programming is a critical aspect of modern manufacturing, allowing for precise and efficient machining of raw materials into finished products. From the basics of G-code and M-code programming languages to advanced techniques for multi-axis machining, high-speed cutting, and 5-axis operations, CNC programming requires a range of skills and knowledge. By following best practices and staying up to date with the latest advancements, CNC programmers can achieve optimal efficiency, accuracy, and safety in their work.