Table of Contents:
- Introduction
- Choosing the Right CNC Precision Machining Parts Manufacturer
- CNC Precision Machining Parts Manufacturing Process
- Quality Control in CNC Precision Machining Parts Manufacturing
- Cost of CNC Precision Machining Parts Manufacturing
- Future Trends in CNC Precision Machining Parts Manufacturing
- Conclusion
-
1.Introduction
CNC precision machining parts are components that are produced using computer-controlled machining processes, such as turning, milling, and drilling. These processes are highly automated and use specialized machines to cut, shape, and form parts with high accuracy and precision. CNC precision machining parts are used in a wide range of industries, including aerospace, automotive, medical, electronics, and many others.
The importance of CNC precision machining parts lies in their ability to produce parts with a high degree of accuracy, consistency, and repeatability. This makes them ideal for manufacturing complex components that require tight tolerances and intricate shapes. CNC precision machining parts are also highly customizable and can be produced in large quantities, making them a cost-effective solution for many manufacturing applications. In this guide, we will explore the world of CNC precision machining parts manufacturers and provide valuable insights into the industry.
-
2.Choosing the Right CNC Precision Machining Parts Manufacturer
When choosing a CNC precision machining parts manufacturer, there are several factors to consider to ensure that you select the right one for your needs. Here are some key factors to keep in mind:
- Experience and Expertise: Look for a manufacturer with a proven track record of producing high-quality parts. Consider their experience in your specific industry and their expertise in machining the types of parts you need.
- Technology and Equipment: Ensure that the manufacturer uses the latest CNC machining technology and equipment to produce high-quality parts. Ask about their machines, software, and quality control processes.
- Materials and Capabilities: Consider the range of materials the manufacturer can work with, and their ability to handle complex designs, tight tolerances, and small production runs.
- Communication and Collaboration: Look for a manufacturer who values communication and collaboration with their clients. They should be responsive, transparent, and willing to work with you to achieve your goals.
When evaluating potential CNC precision machining parts manufacturers, here are some questions to ask:
- What industries do you specialize in, and what experience do you have working with my industry?
- What types of materials and designs can you work with?
- How do you ensure quality control during the manufacturing process?
- Can you provide references or case studies of similar projects you’ve completed?
- How do you handle communication and collaboration with your clients during the manufacturing process?
By considering these factors and asking the right questions, you can ensure that you choose a CNC precision machining parts manufacturer that meets your specific needs and delivers high-quality, reliable parts.
-
3.CNC Precision Machining Parts Manufacturing Process
CNC precision machining parts manufacturing involves several steps, each of which requires careful planning and execution. Here is a step-by-step guide to the CNC precision machining parts manufacturing process:
- Design and Engineering: The first step is to create a design for the part using computer-aided design (CAD) software. This design is then translated into a set of instructions for the CNC machine.
- Material Selection: The next step is to select the appropriate material for the part. Common materials used in CNC precision machining parts manufacturing include metals such as aluminum, stainless steel, and titanium, as well as plastics and composites.
- CNC Machining: The part is then produced using a CNC machine. The machine uses a set of instructions to cut, drill, or shape the part from the selected material. CNC machining is highly automated and requires minimal human intervention.
- Quality Control: Once the part is machined, it undergoes rigorous quality control measures to ensure that it meets the required specifications. This may include dimensional inspections, material analysis, and visual inspections.
- Finishing: The final step is to apply any necessary finishing processes, such as sandblasting, polishing, or coating, to the part. This helps to improve the part’s appearance and durability.
Common materials used in CNC precision machining parts manufacturing include metals such as aluminum, brass, copper, stainless steel, and titanium, as well as plastics such as ABS, nylon, and polycarbonate. The choice of material depends on the specific requirements of the part, including its strength, durability, and weight.
By following this step-by-step guide and using high-quality materials, CNC precision machining parts manufacturers can produce parts that meet the highest standards of accuracy, precision, and durability.
-
4.Quality Control in CNC Precision Machining Parts Manufacturing
Quality control is a critical aspect of CNC precision machining parts manufacturing. It ensures that the parts produced meet the required specifications and are free from defects. Here are some reasons why quality control is important in manufacturing:
- Ensures Product Consistency: Quality control measures help ensure that parts are manufactured consistently, meeting the required specifications every time. This is critical when producing parts for applications such as aerospace or medical devices, where consistency and reliability are essential.
- Reduces Scrap and Rework: By catching defects early in the production process, quality control measures can help reduce scrap and rework, saving time and money.
- Enhances Customer Satisfaction: High-quality parts that meet the required specifications are more likely to satisfy customers and improve their perception of the company.
Here are some common techniques used in quality control for CNC precision machining parts:
- Dimensional Inspections: Dimensional inspections involve measuring the part to ensure that it meets the required dimensions and tolerances. This can be done using specialized equipment such as coordinate measuring machines (CMMs) or optical scanners.
- Material Analysis: Material analysis involves testing the material used to manufacture the part to ensure that it meets the required specifications. This can involve testing the material’s strength, hardness, or other properties.
- Visual Inspections: Visual inspections involve examining the part for defects such as cracks, chips, or scratches. This can be done using specialized equipment such as microscopes or cameras.
- Statistical Process Control: Statistical process control involves monitoring the production process to detect and correct any variations that may affect the quality of the parts produced. This can involve analyzing data from sensors or other monitoring devices.
By using these techniques and implementing rigorous quality control measures, CNC precision machining parts manufacturers can ensure that their parts meet the highest standards of accuracy, precision, and reliability.
-
5.Cost of CNC Precision Machining Parts Manufacturing
The cost of CNC precision machining parts manufacturing depends on several factors, including:
- Material Costs: The cost of the raw material used to produce the part is a significant factor in the overall cost of manufacturing.
- Machine Time: The time required to machine the part is a critical factor in the overall cost of manufacturing. This is influenced by factors such as the complexity of the part and the machining processes required.
- Labor Costs: The cost of labor required to operate the CNC machine and perform quality control measures is a significant factor in the overall cost of manufacturing.
- Tooling Costs: The cost of tooling required to manufacture the part, such as cutting tools or fixtures, is also a significant factor in the overall cost of manufacturing.
There are several ways to reduce the cost of CNC precision machining parts manufacturing, including:
- Material Selection: Choosing lower-cost materials can help reduce the overall cost of manufacturing. However, this must be balanced against the requirements of the part, such as strength and durability.
- Design Optimization: Optimizing the design of the part to minimize machining time and reduce waste can help reduce the overall cost of manufacturing.
- Process Optimization: Optimizing the machining process to reduce cycle time and increase efficiency can help reduce the overall cost of manufacturing.
- Tooling Optimization: Optimizing the tooling used to manufacture the part can help reduce tooling costs and improve the efficiency of the machining process.
By implementing these strategies and working with a reputable CNC precision machining parts manufacturer, it is possible to reduce the overall cost of manufacturing while still producing high-quality parts that meet the required specifications.
-
6.Future Trends in CNC Precision Machining Parts Manufacturing
CNC precision machining parts manufacturing is a dynamic industry that is continually evolving. Here are some future trends to watch in the industry:
- Advancements in Technology: The industry is experiencing rapid advancements in technology, including the use of artificial intelligence (AI) and machine learning to optimize the machining process. Additionally, the use of additive manufacturing, such as 3D printing, is becoming increasingly common.
- Automation and Robotics: Automation and robotics are becoming increasingly prevalent in CNC precision machining parts manufacturing. This allows for increased efficiency and productivity while reducing labor costs.
- Green Manufacturing: The trend towards sustainable and environmentally-friendly manufacturing is also impacting the CNC precision machining parts manufacturing industry. This includes the use of green materials and processes that minimize waste and reduce energy consumption.
- Internet of Things (IoT): The IoT is beginning to play a more significant role in CNC precision machining parts manufacturing. By connecting machines and sensors, manufacturers can monitor and optimize the manufacturing process in real-time.
- Industry 4.0: Industry 4.0 is a term used to describe the integration of digital technologies into the manufacturing process. This includes the use of data analytics, cloud computing, and the IoT to improve efficiency and productivity.
By keeping up with these emerging trends and adopting new technologies and processes, CNC precision machining parts manufacturers can stay ahead of the curve and continue to provide high-quality parts to their customers.
Click on the V1 Prototype website to gain more Precision CNC Machining Services information.
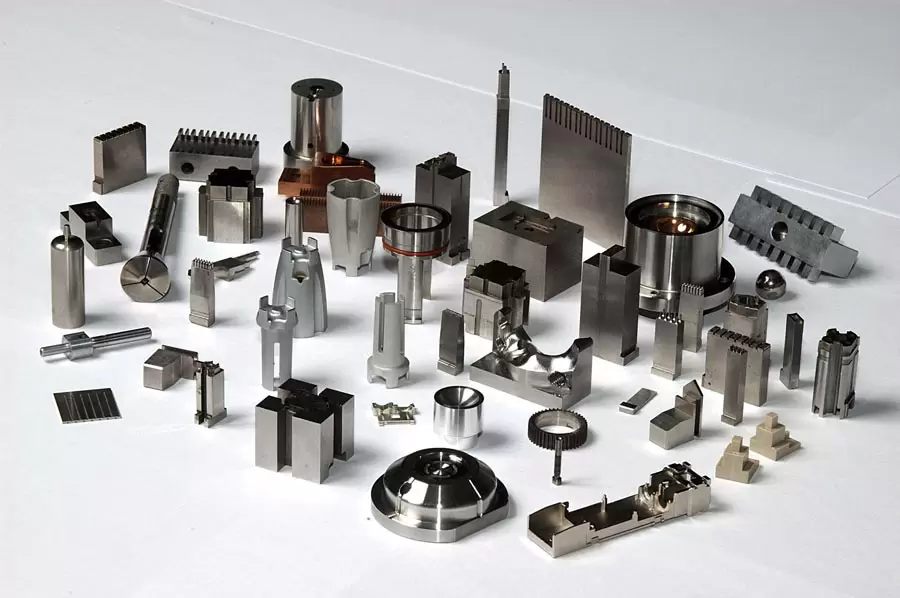
-
7.Conclusion
In conclusion, CNC precision machining parts play a critical role in various industries, and choosing the right manufacturer is essential to ensuring high-quality parts that meet the required specifications. When choosing a manufacturer, it is important to consider factors such as experience, capabilities, and quality control measures.
The top CNC precision machining parts manufacturers provide a range of services and features, including design and engineering support, prototyping, and high-volume production capabilities. Additionally, the manufacturing process for CNC precision machining parts involves several steps, including material selection, programming, and quality control.
To reduce the cost of CNC precision machining parts manufacturing, manufacturers can implement strategies such as material selection, design optimization, and process optimization. The industry is also experiencing several emerging trends, such as the use of AI and robotics, green manufacturing, and Industry 4.0.
Overall, CNC precision machining parts manufacturers play a crucial role in the manufacturing industry, and by staying up-to-date with the latest technologies and processes, they can continue to produce high-quality parts that meet the evolving needs of their customers.