Table of Contents:
- Introduction
- Types of Plastic Extruders
- Working Principles of Plastic Extruders
- Applications of Plastic Extruders
- Design Considerations for Plastic Extruders
- Maintenance and Repair of Plastic Extruders
- Conclusion
-
1.Introduction
Plastic extrusion is a manufacturing process used to produce continuous plastic profiles with a predefined cross-sectional shape. The plastic extrusion process involves melting plastic pellets and then pushing them through a die that creates a specific profile.
The development of modern plastic extrusion began in the early 20th century with the invention of Bakelite, the first synthetic plastic invented by Leo Baekeland in 1907. This breakthrough in plastic production led to the development of mass plastic extrusion during the 1930s.
Plastic extruders are essential in the manufacturing process for creating custom plastic parts in different shapes and sizes. The extruders are widely used in several industries, including construction, packaging, automotive, medical, and consumer goods.
By understanding the basics of plastic extrusion and the importance of plastic extruders in manufacturing, it’s possible to see why this manufacturing process is critical in producing different plastic components with unique features and characteristics.
-
2.Types of Plastic Extruders
There are three main types of plastic extruders used in the manufacturing process, each with unique characteristics and benefits. These types are:
- Single Screw Extruders: Single screw extruders are the most commonly used type of plastic extruders. The extruder consists of a rotating screw within a heated barrel that melts the plastic pellets and forces them through a die to create the desired profile. Single screw extruders are simple, reliable, and cost-effective, making them ideal for producing different types of plastic profiles.
- Twin Screw Extruders: Twin screw extruders are more complex and versatile compared to single screw extruders. The extruder consists of two intermeshing screws within a heated barrel that work together to mix, melt and shape the plastic. Twin screw extruders are commonly used in the production of high-quality plastics, including PVC, and can handle a more extensive range of materials, additives, and fillers.
- Co-Extruders: Co-extruders are a type of plastic extruder used to create multi-layered plastic profiles consisting of different materials and colors. Co-extruders work by feeding two or more extruders, melting and fusing them together before passing them through a die to create the final product.
Each type of plastic extruder has unique capabilities and advantages, making it suitable for different manufacturing applications. Understanding the types of plastic extruders available makes it easier to choose the appropriate one for specific manufacturing needs, enhancing the desired outcomes.
-
3.Working Principles of Plastic Extruders
The working principles of plastic extruders involve three basic processes, which include mixing and heating, melting and pressure generation, and shaping and cooling.
- Mixing and heating: The first process in plastic extrusion is mixing and heating. The plastic pellets are fed into the extruder’s hopper, where they move into the barrel. Inside the barrel, the rotating screw applies pressure to the pellets, mixing and compressing them as they move along the barrel’s length. The barrel is heated using heaters to melt and soften the plastic pellets as they move forward.
- Melting and pressure generation: As the plastic pellets move along the barrel, the heat generated by the heaters melts the plastic into a fluid mass. The screw continuously rotates and moves the molten plastic through the barrel, pushing it forward and generating high levels of pressure in the process, which helps to improve melting efficiency to change the polymer structure.
- Shaping and cooling: Once the hot, molten plastic reaches the die, it is constrained, forcing it to take on the shape of the die orifice. The hot plastic then passes through the sizing device and cooling zone, where it solidifies into the desired shape. The cooling can be by air or water, depending on the application or the desired outcome.
The quality of the final product depends on the quality of these three processes. Therefore, manufacturers often pay particular attention to the mixing and heating process, which plays an essential role in determining the quality and integrity of the product produced by plastic extruders.
-
4.Applications of Plastic Extruders
Plastic extruders have numerous applications across a wide range of industries due to their ability to produce customized plastic profiles with unique shapes, sizes, and characteristics. Here are some of the industries where plastic extruders are widely used:
- Packaging Industry: Plastic extruders are commonly used in the packaging industry to create different types of packaging materials like plastic bags, straws, and films.
- Construction Industry: The construction industry uses plastic extruders to produce various plastic components like pipes, tubes, profiles, and panels.
- Automotive Industry: Plastic extruders play a vital role in the automotive industry, where they are used to produce different plastic components such as weatherstripping, door panels, bumpers, and tires.
- Medical Industry: The medical industry uses plastic extruders to produce different medical products such as tubing, catheters, and surgical instruments.
- Consumer Goods Industry: In the consumer goods industry, plastic extruders are used to produce a wide range of products such as toys, electronic housings, sporting goods, and food packaging.
Plastic extruders provide high-quality and cost-effective manufacturing solutions for the above-mentioned industries, among others. These industries depend on plastic Extrusion for producing the desired properties and specific product attributes critical to their functioning.
If you want more about Plastic information ,You can click on the V1 Prototype website to find it.
-
5.Design Considerations for Plastic Extruders
Design considerations are vital for plastic extruder manufacturers to ensure that they produce high-quality products for their intended applications. These considerations typically fall into two categories: factors affecting extruder performance and the essential components of an extruder design.
1.Factors Affecting Extruder Performance: Several factors can impact the performance of a plastic extruder, including:
- Material properties: The physical and chemical properties of the plastic materials to be extruded can affect the extruder’s performance.
- Cross-sectional area and size: The cross-sectional area and size of the extruded product can affect material flow and pressure during the extrusion process.
- Screw design: Since screw design influences the mixing and transport of material, screw design can affect the extruder’s homogeneity, melting rate, and output.
- Barrel design: The barrel design influences the quality of the extruded product, affecting the pressure development, temperature profile, and melt mixing.
.
2.Essential Components of an Extruder Design: Key components that present in any extruder design include:
- Hopper: This is the part where the plastic pellets are fed into the extruder.
- Barrel: The barrel is a heated cylinder through which the molten plastic passes.
- Screw: The screw is an essential part of an extruder that moves the plastic through the barrel.
- Die: The die is the part that shapes the plastic as it exits the extruder.
- Control system: An extruder system is responsible for controlling different factors within the process, like temperature, pressure, and speed.
Understanding these design considerations helps manufacturers to develop their custom-made extruders or select ones from existing designs. The design considerations defined the performance and capabilities of the plastic extruder to ensure optimal results and efficiency.
-
6.Maintenance and Repair of Plastic Extruders
Maintenance and repair are crucial to ensure the long-term viability and productivity of plastic extruders. Below are some best practices for preventative maintenance and common repairs and techniques for plastic extruders:
1.Best Practices for Preventative Maintenance:
- Regular cleaning: Thorough cleaning of the extruder components is essential in preventing or reducing contamination issues to improve the products’ quality.
- Lubrication: Regular lubrication of the components improves their efficiency and residual longevity.
- Inspection: Regular inspection of the extruder components helps identify any hidden defects, cracks, or irregularities that may affect the operation.
- Record keeping: While undertaking maintenance, it is vital to record the maintenance data to analyze and adjust scheduled maintenance accordingly.
.
2.Common Repairs and Techniques:
- Screw and Barrel Replacement: Wear and tear are inevitable in extruder use, and the screw and barrel is the extruder’s essential components. Replacing these components is necessary when wear and tear are deemed excessive.
- Heater Replacement: Heaters may wear out and lose efficiency over time, requiring replacement.
- Calibration: It is necessary to check the machine calibration to ensure that its output meets product specification and customer satisfaction.
- Welding and Machining: Welding and machining can be used in repair work to seal cracks or imperfections in the extruder components.
In conclusion, preventative maintenance and timely repair of plastic extruders can avoid significant damage or accidents, prolong their useful life while ensuring high-quality products. Regular maintenance and immediate repairs minimize downtime, reduce costs, and enhance efficiency, ensuring business growth and customer satisfaction.
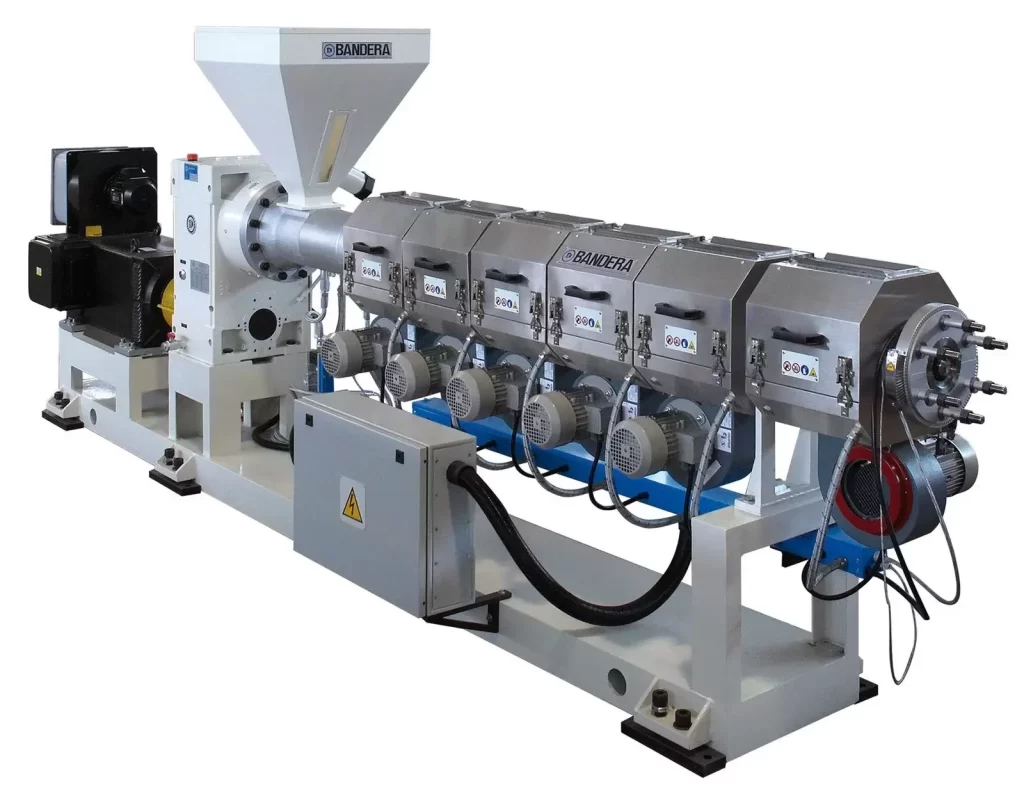
-
7.Conclusion
Plastic extruders are essential manufacturing components that allow for the creation of customized plastic profiles, tubes, and components used across various industries, including packaging, construction, automotive, medical, and consumer goods. Understanding the working principles and the types of extruders and their essential components, manufacturers can select the best-suited equipment for their requirements.
Design considerations affect the extruder’s performance and output, which can influence the quality of the final product, indicating how crucial they are to manufacturers. To maintain optimum productivity and efficiency, preventative maintenance practices ensure equipment lasts longer and works optimally. Common repairs are also essential in avoiding long downtimes and high repair costs.
In the future, plastic extruders are expected to become more advanced, with improvements in the processing capabilities, production speeds and efficiency, and energy-saving features. The integration of artificial intelligence and machine learning is expected to improve the extruder’s capability and precision to meet the ever-increasing customer needs.
In conclusion, plastic extruders are crucial manufacturing components globally and will continue to play an essential role in various industries’ growth and expansion. As technology continues to enhance the manufacturing processes, the use of plastic extruders will remain critical to precision, speed, and cost-effectiveness in production.