Stereolithography (SLA) 3D Printing
SLA Parts In As Soon As Next-Day; High-Quality Surface Finish for Aesthetic Models;Durable, Versatile Materials with Tight Tolerances.
Stereolithography (SLA) 3D Printing Parts
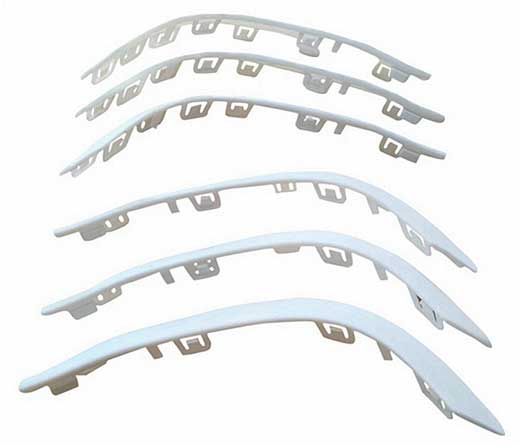
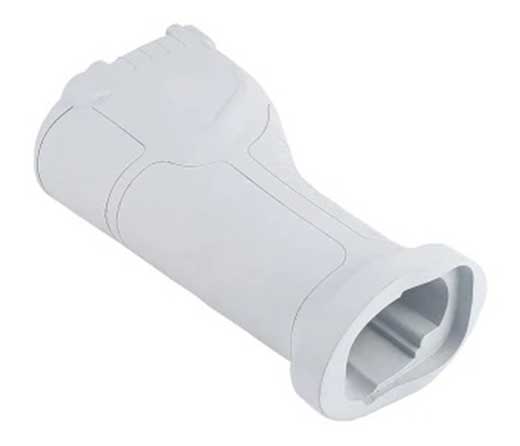
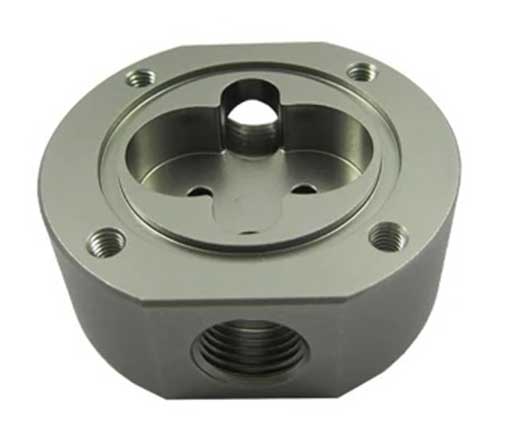
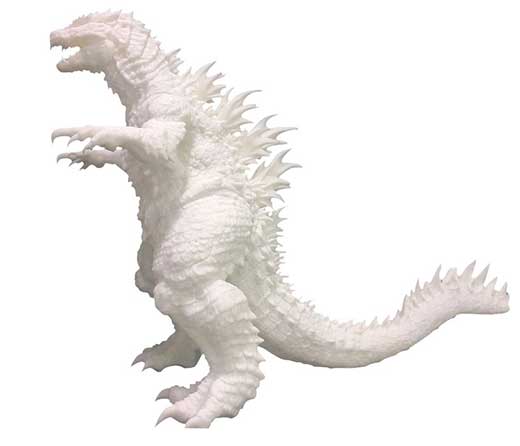
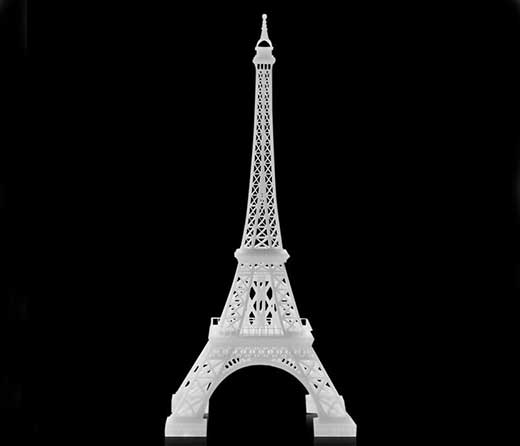
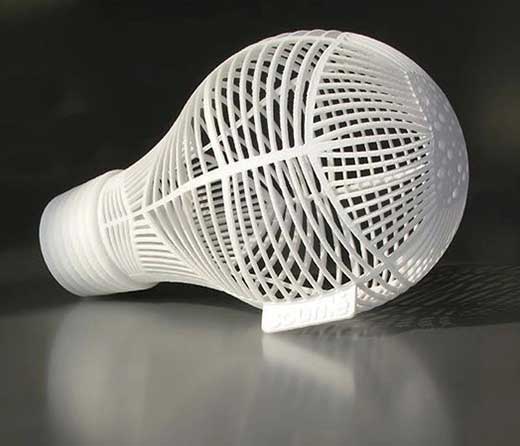
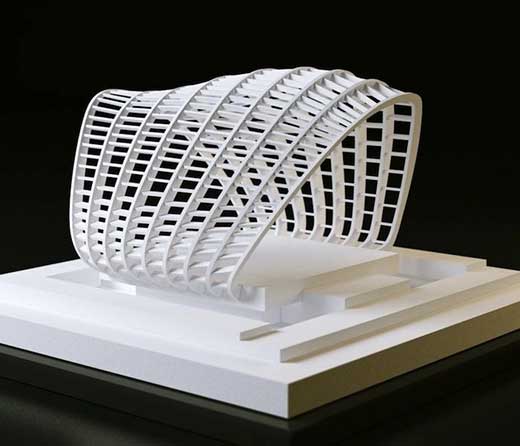
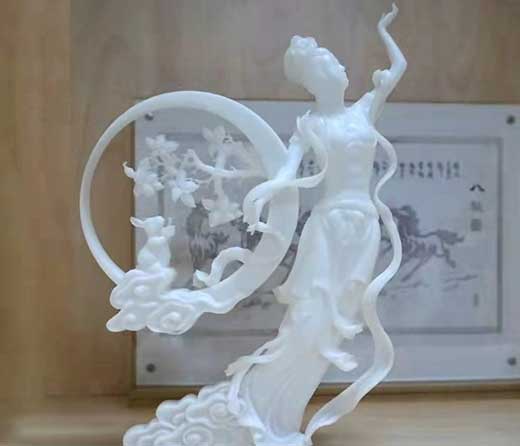
Stereolithography (SLA) 3D Printing Service
This technology is ideal for high-resolution finishes on medium- to large-sized parts. It is an extremely cost-effective solution for creating durable, aesthetically pleasing parts of considerable size on a tight deadline. Stereolithography (SLA) resins with extremely high heat deflection are available and are great candidates for molds or inserts.
How does the Stereolithography technology work? SLA cures photopolymer resin with an ultraviolet laser. The laser traces a shape dictated by the original file across the surface of the resin bath. The resin touched by the laser hardens, then the build platform descends in the resin bath and the process is repeated until the entire part is complete.
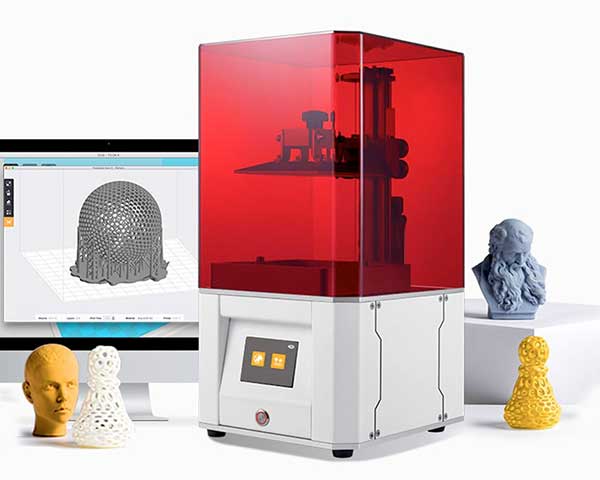
SLA 3D Printing Finishes
Supports are removed and minimally sanded in order to remove the support nubs left behind with some nubs remaining in hard-to-reach areas. Build lines are visually present and the parts have a granulated/gritty texture.
Supports are removed , parts are bead blasted and then sanded smooth. Build lines are somewhat present, but parts have a smooth texture. Bead blasted parts will make clear parts look frosty/cloudy.
Supports are removed and then the parts are sanded and bead blasted. Paint is applied directly to parts without a primer which means the build lines will be somewhat present through the paint.
Supports are removed and then the parts are sanded and bead blasted. A basic clear coat is applied to parts, but the build lines will still be somewhat present under the clear coat.
Supports are removed, parts are bead blasted and extensively sanded until all build lines are removed. Primer is applied before painting. Pantone color or color chip will need to be supplied to match color. Parts are smooth and build lines are completely removed. Parts look as close to production quality as possible.
Supports are removed, parts are bead blasted and extensively sanded until all build lines are removed. Multiple coats of clear are applied. Parts are smooth and build lines are completely removed. Parts are completely clear—almost glass-like.
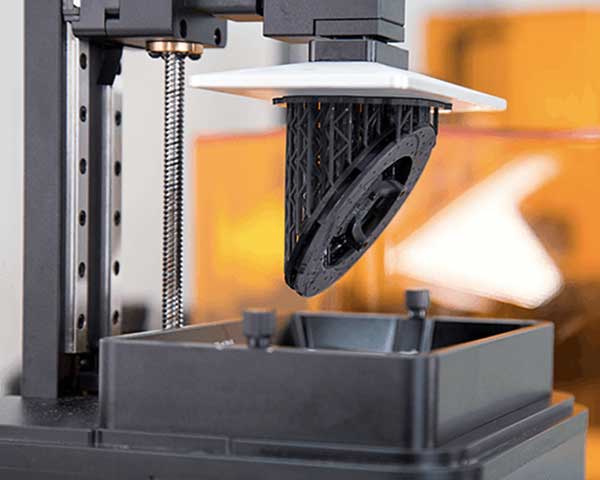
Why Choose SLA 3D Printing?
Brands use SLA for many reasons. SLA is an excellent choice if your project requires fine features, smooth surface finishing, part precision and accuracy, isotropy, mechanical attributes, water tightness or versatility of materials.
SLA offers a combination of high-quality resolution and surface finishes at large volumes. SLA is also very effective at faithfully capturing the intricacies of even the most complex parts. Clear SLA resins can achieve colorless clarity with additional post processing to mimic clear plastics. SLA specializes in creating parts that are highly cost-intensive to produce using any other method of manufacturing, being consistently used for trade show models, aesthetic parts and snap fits/functional assemblies.
SLA 3D Printing Manufacturing FAQs
SLA is a laser light curing technology, which uses ultraviolet laser beams to cure photosensitive resin layer by layer to form three-dimensional objects.
SLA 3D printing technology has the advantages of high precision, high speed, high-quality surface finish, and no need for support materials. This advanced manufacturing technology has been widely used in many fields, bringing revolutionary changes to all walks of life.
First, the high precision of SLA 3D printing technology makes it ideal for manufacturing complex parts. Compared with traditional processing methods, SLA 3D printing technology can accurately copy every detail on the design drawings, thereby ensuring the quality of the final product. This makes it have broad application prospects in aerospace, automobile manufacturing, medical equipment and other fields.
Secondly, SLA 3D printing technology is characterized by high speed. By using high-performance 3D printers and optimized printing parameters, SLA 3D printing technology can complete a large number of printing tasks in a short period of time. This greatly improves production efficiency and reduces production costs, allowing companies to bring new products to market faster.
In addition, SLA 3D printing technology offers a high-quality surface finish. Due to its unique light-curing principle, SLA 3D printing technology can achieve smooth and uniform surface quality, giving the final product a good appearance and feel. This is of great significance for parts that require high-quality surfaces, such as jewelry, toys, etc.
Finally, SLA 3D printing technology does not require support materials, which greatly simplifies the printing process. Traditional 3D printing technology usually requires the use of support materials to maintain complex geometric shapes, while SLA 3D printing technology can directly print support-free structures. This not only saves material costs, but also reduces post-processing workload and improves production efficiency.
In short, SLA 3D printing technology has brought great convenience to all walks of life with its advantages of high precision, high speed, high-quality surface finish and no need for support materials. As technology continues to develop and mature, we have reason to believe that SLA 3D printing technology will play an increasingly important role in future manufacturing.
Although SLA 3D printing technology is widely used in many fields, its cost is relatively high, which to a certain extent limits its application in some mass production or scenarios that require large amounts of use. In addition, SLA 3D printing technology also has some limitations in handling large parts and high-temperature applications.
First, let’s take a look at the cost of SLA 3D printing technology. The working principle of SLA 3D printing technology is to use a laser beam to solidify photosensitive resin layer by layer to create three-dimensional objects. This process requires a large amount of material and energy investment, so its cost is relatively high. For some companies or individuals who need to use 3D printing technology extensively, this may be a big burden.
Secondly, the limitations of SLA 3D printing technology in processing large parts cannot be ignored. Because of the way SLA 3D printing technology works, it is difficult to print large three-dimensional objects in one go. Instead, large objects need to be broken down into multiple small parts for printing, and then the parts are assembled together. This not only increases the workload, but may also affect the quality of the final product.
Finally, the limitations of SLA 3D printing technology in handling high-temperature applications is also an issue. Since SLA 3D printing technology uses photosensitive resin as the printing material, this material may be deformed or damaged in high-temperature environments, so SLA 3D printing technology is difficult to apply in high-temperature environments.
SLA 3D printing technology is ideal for manufacturing parts that require high precision and quality surface treatment, such as medical devices, jewelry, automotive and aerospace industries. This technology creates three-dimensional objects by stacking photosensitive resin layer by layer with exceptional precision and surface quality. In the medical field, SLA 3D printing technology can be used to manufacture complex medical devices such as prostheses, artificial joints and dental models. These parts require highly precise dimensions and surface smoothness to ensure patient safety and comfort.
In the jewelry industry, SLA 3D printing technology can be used to create exquisite jewelry and accessories. Due to its high precision and ability to express details, designers can use this technology to create complex geometric shapes and textures, making jewelry more unique and attractive. In addition, SLA 3D printing technology can also be used to manufacture customized jewelry, with personalized designs based on customer requirements.
In the automotive and aerospace industries, SLA 3D printing technology can be used to manufacture complex parts and assemblies. For example, automakers could use the technology to create lightweight vehicle parts to improve fuel efficiency and reduce emissions. The aerospace industry can use SLA 3D printing technology to manufacture high-performance aero-engine parts and improve engine efficiency and reliability.
In summary, SLA 3D printing technology has broad application prospects in industries that require high precision and high-quality surface treatment. It provides innovative solutions for industries such as medical, jewelry, automotive and aerospace, driving the development and progress of these industries.
In stereolithography (SLA) 3D printing technology, the materials used mainly include photosensitive resin, graphene, ceramics and metals. These materials play an important role in the 3D printing process and provide the basis for manufacturing high-quality three-dimensional objects.
First of all, photosensitive resin is one of the most commonly used materials in SLA 3D printing technology. It is a liquid material composed of polymers and photoinitiators that can be cured by irradiation with a laser beam. Photosensitive resin has excellent detail expression ability and smooth surface quality, and is suitable for manufacturing complex geometric shapes and fine structures. In addition, photosensitive resins can also achieve different hardness and durability requirements by adjusting their formula to meet the needs of different application fields.
Secondly, graphene is a two-dimensional material with excellent electrical and thermal conductivity. In SLA 3D printing technology, graphene can be used as a component of conductive lines or thermal management elements. By combining graphene with photosensitive resins, precise control of the electrical and thermal properties of printed objects can be achieved. This combination not only improves the functional performance of printed objects, but also enables more complex design and manufacturing requirements.
Third, ceramic materials are also widely used in SLA 3D printing technology. Ceramic materials have the characteristics of high hardness, wear resistance and high temperature resistance, and are suitable for manufacturing high-performance mechanical parts and tools. By mixing ceramic powder with photosensitive resin, precise control and processing of ceramic materials can be achieved. This combination not only improves the strength and durability of printed objects, but also enables more complex and sophisticated design requirements.
Finally, metal materials are also one of the important materials in SLA 3D printing technology. Metal materials have excellent electrical conductivity, thermal conductivity and mechanical properties, and are suitable for manufacturing parts with high strength and high electrical conductivity. By mixing metal powder with photosensitive resin, precise control and processing of metal materials can be achieved. This combination not only improves the strength and conductivity of printed objects, but also enables more complex and sophisticated design requirements.
To sum up, the material options for SLA 3D printing technology include photosensitive resin, graphene, ceramics and metals. These materials play different roles in the 3D printing process, providing diverse options for manufacturing high-quality, feature-rich three-dimensional objects. With the continuous development of technology, we can expect the emergence of more new materials to further expand the application fields and potential of SLA 3D printing technology.
The maximum size of SLA 3D printing technology varies between different devices, usually around tens of centimeters. This technology builds three-dimensional objects layer by layer by stacking photosensitive resin layer by layer and curing it using ultraviolet radiation. Due to its high precision and ability to express details, SLA 3D printing technology has wide applications in many fields.
First of all, SLA 3D printing technology plays an important role in the medical field. Doctors and engineers can use the technology to create accurate human models for surgical simulation and training. These models can accurately replicate human anatomy and organs, help doctors better understand diseases and surgical procedures, and improve the safety and success rate of surgeries.
Secondly, SLA 3D printing technology is also widely used in manufacturing. Manufacturers can use the technology to create complex parts and prototypes to speed up product development cycles and reduce costs. SLA 3D printing technology can produce parts with complex geometries faster and with less material waste than traditional machining methods.
In addition, SLA 3D printing technology is also widely used in the fields of art and design. Artists and designers can use this technology to create unique pieces of art and sculpture. Due to its ability to achieve a high degree of detail and precision, SLA 3D printing technology offers artists more creative possibilities, allowing them to transform their ideas into real works.
In short, although the maximum size of SLA 3D printing technology is limited, its application potential in medical, manufacturing and art fields is huge. As technology continues to develop and improve, we can expect SLA 3D printing technology to achieve larger sizes and higher precision in the future, bringing more innovation and development opportunities to all walks of life.
SLA 3D printing technology requires the use of 3D modeling software that supports the STL file format.
SLA (Stereolithography) is a common 3D printing technology that creates objects by curing photosensitive resin layer by layer. In order to print on an SLA 3D printer, the designed object first needs to be converted into a 3D model. This requires the use of a 3D modeling software that supports the STL file format.
STL (Standard Tessellation Language) is a file format used to describe three-dimensional geometric shapes. It is one of the most commonly used file formats in the 3D printing industry. The STL file consists of a series of triangular patches, and each patch contains information such as the normal vector and vertex coordinates of the patch. This information can be read by the 3D printer and converted into actual printing paths.
Therefore, to use SLA 3D printing technology, you first need to choose a 3D modeling software that supports the STL file format. Such software can help users create, edit and optimize 3D models and export them as STL files for printing on SLA 3D printers. There are many 3D modeling software to choose from on the market, such as Blender, AutoCAD, SolidWorks, etc. They all support the STL file format and provide a wealth of functions and tools to meet the needs of different users.
When using SLA 3D printing technology, you also need to pay attention to some other factors, such as selecting appropriate photosensitive resin materials, setting appropriate printing parameters, etc. These factors will all have an impact on the quality of the final print result. Therefore, in addition to selecting 3D modeling software that supports the STL file format, other factors need to be considered to ensure satisfactory printing results.
The accuracy of SLA 3D printing technology typically ranges from 50 microns to 200 microns, depending on the equipment and materials used. This technology uses light-curing resin to build objects layer by layer. The resin is cured by irradiation with laser beams to form the desired three-dimensional structure.
The accuracy of SLA 3D printing technology is affected by multiple factors. First, the performance of the device itself plays an important role in accuracy. Advanced SLA printers are usually equipped with high-precision optical systems, stable workbenches, and precise control systems, all of which can improve printing accuracy.
Secondly, the material used will also affect the accuracy of printing. Different types of photocurable resins have different viscosities and rheological properties, which will directly affect layer thickness control and surface smoothness during the printing process. Therefore, choosing the right material for a specific application is critical to achieving high-precision printing results.
In addition, the settings of printing parameters will also affect the accuracy. For example, the selection of parameters such as laser power, scanning speed, and layer thickness will directly affect the size and surface quality of the printed object. Reasonable parameter settings can improve printing accuracy and detail expression capabilities.
It should be noted that although the accuracy of SLA 3D printing technology can reach a high level, there is still a certain error range. This is because there are certain uncertainties in the curing of the resin and the scanning of the laser beam during the printing process. Therefore, in application scenarios with high precision requirements, post-processing or other technical means may be required to further improve the accuracy of the printing results.
In general, the accuracy of SLA 3D printing technology ranges from 50 microns to 200 microns, but the specific accuracy depends on the performance of the equipment, the selected materials, and the settings of the printing parameters. By rationally selecting equipment and materials, and optimizing printing parameters, printing accuracy and detail expression capabilities can be improved to a certain extent.
The speed of SLA 3D printing technology will vary depending on different equipment and materials. Typically, its printing speed ranges from a few millimeters to tens of millimeters per hour. The printing speed of this technology is affected by several factors, including the model of the printer, the performance of the print head, the type of light source used and the materials selected.
First, different models of SLA 3D printers have different printing speeds. Some high-end SLA printers usually have high printing speeds, which can reach tens of millimeters per hour or even higher. Some entry-level SLA printers may only have a printing speed of a few millimeters per hour. Therefore, when choosing an SLA 3D printer, you need to choose the appropriate model based on actual needs and budget.
Secondly, the performance of the print head is also one of the important factors affecting the speed of SLA 3D printing. High-performance printheads are typically able to move and eject photosensitive resin faster, resulting in faster printing. In addition, the resolution and accuracy of the print head will also have an impact on the printing speed. Higher resolutions and accuracy may take longer to print each layer, reducing overall print speed.
The type of light source is also one of the factors that affects the speed of SLA 3D printing. Currently common light source types include laser light sources and LED light sources. Laser light sources usually have higher energy density and stability, which can cure photosensitive resin faster, thereby increasing printing speed. LED light sources are relatively slow, but their cost is lower and their service life is longer.
Finally, the material chosen will also affect SLA 3D printing speed. Different photosensitive resin materials have different curing speeds and fluidities, which will have an impact on printing speed. Some high-performance photosensitive resin materials usually have faster curing speeds, which can increase printing speeds. However, these materials tend to be more expensive and have a certain impact on the environment.
To sum up, the speed of SLA 3D printing technology is affected by many factors, including printer model, print head performance, light source type and selected materials. When choosing an SLA 3D printer, you need to consider these factors comprehensively and choose the appropriate equipment and materials based on actual needs and budget to obtain the best printing speed and quality.
Yes, SLA 3D printing technology requires pre-treatment during the printing process to ensure that the photosensitive resin can be cured correctly.
First, before 3D printing, the photosensitive resin needs to be pretreated. The purpose of this step is to ensure that the resin can react chemically under specific lighting conditions to form the desired three-dimensional structure. The preprocessing process usually includes the following steps:
1. Cleaning and preparation: First, the 3D printer and related equipment need to be thoroughly cleaned to ensure that no impurities or contaminants are present. In addition, the required photosensitive resin and other necessary materials need to be prepared.
2. Mixing and stirring: Next, mix and stir the photosensitive resin with the corresponding photoinitiator. This process is very important because it ensures that the photoinitiator in the photosensitive resin is evenly distributed, thereby improving the curing effect.
3. Filtration and degassing: After mixing and stirring, the photosensitive resin needs to be filtered and degassed. The purpose of this step is to remove possible air bubbles and particles to ensure that the surface of the printed model is smooth and defect-free.
4. Adjust the viscosity: Depending on the specific printing needs, the viscosity of the photosensitive resin may need to be adjusted. By adding an appropriate amount of diluent or thickener, the fluidity of the photosensitive resin can be controlled to adapt to different printing requirements.
5. Coating and exposure: Finally, the pre-treated photosensitive resin is applied to the printing platform and exposed using a specific light source. The length and intensity of exposure will vary depending on the properties of the photosensitive resin used to ensure that the resin is fully cured.
Through these pre-processing steps, SLA 3D printing technology ensures that the photosensitive resin can be cured correctly to obtain high-quality printing results. These steps are important to increase print speed, reduce defects, and extend the life of the printhead. Therefore, before SLA 3D printing, these pre-processing steps must be carefully performed to ensure a smooth printing process.
In stereolithography (SLA) 3D printing technology, the commonly used light sources are usually ultraviolet lasers or light-emitting diodes (LEDs). This advanced 3D printing technology uses these light sources to solidify photosensitive resin to build the desired three-dimensional object layer by layer.
Ultraviolet laser is a high-energy light source that can produce a high-intensity ultraviolet beam in a short time. When an ultraviolet beam shines on a photosensitive resin, the photosensitizer in the resin absorbs the ultraviolet energy, causing a chemical reaction that changes the resin from liquid to solid. By controlling the movement and scanning speed of the laser beam, specific areas of the photosensitive resin can be precisely cured, enabling layer-by-layer construction of three-dimensional objects.
Another common light source is a light-emitting diode (LED). LED is a semiconductor device that emits light of a specific wavelength. In SLA 3D printing technology, LEDs are often used to produce blue or violet light. These light wavelengths can effectively excite the photosensitizer in the photosensitive resin. Compared with UV lasers, LEDs have higher energy efficiency and longer service life, so they are more popular in some application scenarios.
Whether using ultraviolet laser or LED as the light source, SLA 3D printing technology can achieve high-precision and high-quality three-dimensional object manufacturing. This technology is widely used in aerospace, automobile manufacturing, medical and health and other fields, providing innovative solutions for various industries. As technology continues to develop and improve, SLA 3D printing technology will continue to play an important role in promoting the advancement of digital manufacturing.
Common question in SLA 3D Printing Production
SLA 3D printed parts need to be cleaned with alcohol or other chemicals to remove uncured resin, and then exposed to UV light for curing and surface finish improvement.
Yes, stereolithography (SLA) 3D printing technology needs to be performed in an indoor environment, and the light needs to be kept low to prevent the photosensitive resin from being accidentally cured. This is because the photosensitive resin used in the SLA 3D printing process is very sensitive to light. Once exposed to strong light, it will solidify quickly, causing printing failure or poor printing results.
To ensure the stability and accuracy of the SLA 3D printing process, here are some suggestions:
1. Choose a suitable printing environment: Choose a relatively closed, dark room or studio for printing. Curtains, shade cloth, or other blackout materials can be used to reduce the entry of outside light.
2. Use a dedicated printing box: Purchase a printing box specifically for SLA 3D printing. These boxes usually have good light-shielding properties and can effectively block light from entering the printing area.
3. Use low-power LED lights: If you cannot completely prevent light from entering the printing area, you can consider using low-power LED lights to provide the necessary lighting. Make sure the light does not shine directly on the photosensitive resin to avoid unnecessary curing.
4. Control the printing speed: In a dark environment, the printing speed can be appropriately reduced to reduce the impact of light on the photosensitive resin. But be careful not to reduce it too fast, so as not to affect the printing quality and efficiency.
5. Check the printing quality regularly: During the printing process, check the printing quality regularly, especially the curing condition of the photosensitive resin. If any abnormalities are found, adjust the printing parameters or replace the light source in time.
In short, in order to ensure the stability and accuracy of the SLA 3D printing process, it needs to be carried out in an indoor environment, and appropriate measures should be taken to prevent the photosensitive resin from being accidentally cured. This ensures high-quality 3D models and products are printed.
Yes, SLA 3D printing technology can indeed be used to produce commercial products. However, to achieve this goal, it must meet certain production requirements and quality control standards. First, we need to ensure that the 3D printer used has sufficient accuracy and stability to produce high-quality finished products during the production process. In addition, we also need to select suitable 3D printing materials to meet the performance and durability requirements of the product.
During the production process, we need to pay close attention to the working status of the 3D printer to ensure its normal operation. At the same time, we also need to monitor the printing process in order to detect and solve possible problems in time. In order to ensure product quality, we also need to conduct regular quality inspections and maintenance, including cleaning, calibration and replacement of worn parts of the 3D printer.
In addition, we also need to develop appropriate post-processing processes based on the specific needs of the product to improve the appearance and performance of the product. This may include steps such as surface preparation, heat treatment, spraying, etc. Throughout the entire production process, we need to continuously optimize the production process, improve production efficiency, and reduce costs.
In short, although SLA 3D printing technology has great potential, to apply it to the production of commercial products, we must strictly follow the relevant production requirements and quality control standards. Through continuous improvement and optimization, we can give full play to the advantages of 3D printing technology and provide the market with high-quality, high-performance commercial products.
Yes, SLA 3D printing technology does allow the use of multiple materials on the same part. However, this requires changing the photosensitive resin or using mixed materials to achieve it.
First, let’s take a look at SLA 3D printing technology. SLA (Stereolithography) is a stereolithography technology that uses a laser beam to solidify photosensitive resin layer by layer to create three-dimensional objects. This technology is capable of high precision and complex structures, and therefore has wide applications in many fields.
To use multiple materials on the same part, SLA 3D printing technology requires some special measures. First, one way is to replace the photosensitive resin. Different photosensitive resins have different characteristics and performance, such as strength, hardness, transparency, etc. By changing the photosensitive resin, it is possible to print with different materials on the same part. This method can be used to manufacture products with special functional or performance requirements.
Another approach is to use mixed materials. Hybrid materials are when two or more different materials are mixed together to obtain desired properties and characteristics. In SLA 3D printing, hybrid materials can be used to achieve the combination of multiple materials on the same part. For example, a material with high strength can be mixed with a substance with good electrical or thermal conductivity to create a product with a specific function.
However, working with mixed materials also comes with some challenges. First, the compatibility of different materials is a key issue. Certain materials may not mix well together, causing problems during the printing process or reduced performance in the final product. Therefore, when selecting and using mixed materials, adequate research and testing is required to ensure their compatibility and stability.
Additionally, using mixed materials also requires consideration of process parameters and conditions during the printing process. Different materials may require different parameter settings such as laser power, scanning speed and layer thickness to achieve the best printing results. Therefore, when using mixed materials for SLA 3D printing, it needs to be adjusted and optimized according to the specific situation.
In short, SLA 3D printing technology can achieve the use of multiple materials on the same part by changing the photosensitive resin or using mixed materials. This approach allows for greater flexibility and creativity in manufacturing products with special functionality or performance requirements. However, using mixed materials also requires attention to compatibility and selection of process parameters to ensure the stability of the printing process and the quality of the final product.
The production cost of SLA 3D printing technology varies depending on the equipment and materials, but overall it is more expensive than traditional manufacturing technology.
First of all, the equipment cost required by SLA 3D printing technology is relatively high. SLA 3D printers typically require higher investment costs compared to traditional manufacturing technologies. This is mainly because SLA 3D printers use advanced laser curing technology to achieve high-precision and high-quality printing effects. In addition, SLA 3D printers also need to be equipped with professional software and control systems to ensure the stability and reliability of the printing process. The purchase and maintenance costs of these devices are relatively high, thus increasing the production cost of SLA 3D printing technology.
Secondly, the materials used in SLA 3D printing technology also have an impact on costs. SLA 3D printing usually uses photosensitive resin as the printing material. This material has high precision and durability and is suitable for making complex parts and models. However, photosensitive resins are relatively expensive and require special handling and drying steps during the printing process, which also increases production costs. In addition, if you need to print multiple colors or materials with special properties, the cost will increase accordingly.
In addition, the production process of SLA 3D printing technology also requires certain labor costs. Compared with traditional manufacturing technologies, SLA 3D printing requires more operators for monitoring and management. Operators need to have relevant skills and experience to ensure the accuracy and stability of the printing process. In addition, due to the particularity of SLA 3D printing technology, some special post-processing work may be required, such as removing support structures, sanding and painting, etc., which will also increase labor costs.
In summary, although SLA 3D printing technology has unique advantages in manufacturing complex parts and models, its production cost is relatively high. The cost of equipment and materials as well as labor costs are important factors affecting the cost of SLA 3D printing technology. However, as the technology continues to develop and mature, it is expected that the cost of SLA 3D printing technology will gradually decrease, making it more competitive and widely used in various fields.
SLA 3D printing technology is an advanced manufacturing process that creates three-dimensional objects by stacking photosensitive resin materials layer by layer. To ensure the normal operation of the device, optical components and photosensitive resin need to be cleaned and replaced regularly.
First, optical components play a vital role in the SLA 3D printing process. These components include lasers, lenses and mirrors, which are responsible for focusing the laser beam onto the photosensitive resin to form the desired shape. However, due to prolonged use and the impact of the working environment, optical components may accumulate dust, dirt, and other impurities. These contaminants can interfere with the transmission and focus of the laser beam, causing poor print quality or errors. Therefore, regular cleaning of optical components is one of the key steps to keep your equipment functioning properly.
Secondly, photosensitive resin is another important component in the SLA 3D printing process. Photosensitive resin is a special material that undergoes a chemical reaction when exposed to a laser beam, solidifying and forming the desired shape. However, over time, photosensitive resin may gradually thicken or deteriorate, affecting its performance and print quality. In addition, the photosensitive resin may contain bubbles or other impurities, which will also affect the printing results. Therefore, regular replacement of photosensitive resin is another critical step to ensure the normal operation of the equipment.
In short, SLA 3D printing technology requires regular cleaning and replacement of optical components and photosensitive resin to ensure the normal operation of the equipment and print quality. This not only extends the service life of the equipment, but also improves production efficiency and product quality.
Yes, SLA 3D printing technology can indeed print transparent parts. However, in order to achieve this goal, we need to choose a transparent photosensitive resin and perform appropriate post-processing.
First, let's take a look at photosensitive resin. Photosensitive resin is a special type of resin that can be cured by exposure to ultraviolet or visible light. During the 3D printing process, this resin is sprayed onto a printing platform and then cured by a UV light source. Since photosensitive resin has transparent properties, it can be used to print transparent parts.
However, simply using a clear photosensitive resin is not enough to ensure that printed parts are completely transparent. Before 3D printing, we also need to make some settings and adjustments to the printer. This includes selecting appropriate printing parameters such as layer thickness, print speed and infill density. The selection of these parameters will directly affect the transparency and quality of the printed parts.
In addition, after 3D printing is completed, we need to perform some post-processing steps to further improve the transparency of the part. This may include removal of support structures, cleaning of the surface, and further polishing and sanding. These post-processing steps help us remove any impurities or imperfections that may affect the transparency of the part.
In short, SLA 3D printing technology can indeed print transparent parts, but it requires the selection of transparent photosensitive resin and appropriate post-processing. By setting up and adjusting printer parameters correctly, as well as performing the necessary post-processing steps, we can obtain high-quality transparent parts.
SLA 3D printing technology has strong production capacity and can complete a large number of orders in a short time. However, when deciding to use this technology for production, we also need to consider some important factors, such as production time and cost.
First, what we need to focus on is production time. Although SLA 3D printing technology can quickly complete large quantities of orders, the production time of each order is still affected by many factors. For example, if the order quantity is very large, then the production time may increase accordingly. Additionally, if the item being printed is very complex, production time may also be affected. Therefore, when using SLA 3D printing technology for production, we need to reasonably arrange the production time according to the specific circumstances of the order.
Secondly, we also need to consider production costs. Although SLA 3D printing technology can save a lot of manpower and material resources, the cost of its equipment and materials is still relatively high. Therefore, when using this technology for production, we need to carefully calculate the production costs to ensure that our production activities can obtain sufficient profits.
Overall, SLA 3D printing technology is a very effective production tool, but when using it for production, we also need to consider factors such as production time and cost. Only in this way can we ensure that our production activities are both efficient and economical.
During the modeling process of SLA 3D printing technology, there are many factors that need to be considered. First, part geometry is an important consideration. Different geometries may require different modeling methods and techniques to ensure that the printed part meets the design requirements.
Secondly, the support structure is also one of the key factors to consider during the modeling process. Because SLA 3D printing technology builds parts by stacking materials layer by layer, in some complex geometries, it may be necessary to add support structures to maintain the stability and integrity of the part. Therefore, during the modeling process, the support structure needs to be designed and arranged rationally to reduce the impact on part quality and accuracy.
In addition, shrinkage and thermal deformation are also factors that need to be considered during the modeling process of SLA 3D printing technology. Because 3D printing materials are subject to heat during the printing process, it may cause shrinkage or deformation of the material. Therefore, during the modeling process, these factors need to be taken into consideration and corresponding adjustments and compensations made to ensure that the printed parts can meet the design requirements.
To sum up, the modeling process of SLA 3D printing technology needs to comprehensively consider factors such as part geometry, support structure, shrinkage and thermal deformation. Only by fully considering and processing these factors can high-quality 3D printed parts be obtained.
Yes, SLA 3D printing technology can indeed print parts with internal structures. However, in actual operation, we need to consider the support structure and post-processing process.
First, support structures are temporary structures set up to maintain the shape of the part during the 3D printing process. These support structures are often made from a different material than the printing material, such as water-soluble polymers or degradable materials. After printing is complete, the support structure needs to be removed in order to obtain the final part. Therefore, when designing a 3D model, you need to consider how to properly set up the support structure to reduce the impact on the surface and internal structure of the part.
Secondly, the post-processing process refers to a series of processing and processing steps performed on the parts after 3D printing is completed to improve their surface quality, dimensional accuracy and performance. Common post-processing techniques include grinding, polishing, painting, heat treatment, etc. Depending on the specific requirements and application of the part, appropriate post-processing methods can be selected to improve the overall quality and performance of the part.
In short, although SLA 3D printing technology can print parts with internal structures, in practical applications, we need to pay attention to the support structure and post-processing process to ensure that the quality and performance of the parts meet the requirements.