Table of Contents:
- Introduction
- Overview of 3D Printing
- Overview of Injection Molding
- Cost Comparison
- Quality Comparison
- Production Comparison
- Environmental Factors
- Applications
- Future of Manufacturing
- Conclusion
-
1.Introduction:
The manufacturing industry has seen significant changes in recent years, with the introduction of new technologies like 3D printing and injection molding. These two manufacturing processes have revolutionized the way objects are designed, prototyped, and created in various industries, from healthcare to aerospace and automotive.
3D printing and injection molding are both used to produce objects of various shapes and sizes, but the processes involved are entirely different. While 3D printing involves building objects layer by layer using a digital model, injection molding involves creating objects using a mold in which molten material is injected to create the desired shape.
The purpose of this comparison is to explore the differences between 3D printing and injection molding in terms of their strengths, weaknesses, potential applications, and how they stack up against each other. This comparison will be helpful for manufacturers looking to decide between these two manufacturing processes depending on their specific needs and production requirements.
-
2. Overview of 3D Printing:
3D printing is a manufacturing process that involves building a three-dimensional object using a digital model as a guide. The process is also known as additive manufacturing because it adds layers of material to build an object, as opposed to traditional manufacturing methods that involve cutting or subtracting materials.
A. How 3D Printing Works:
The 3D printing process starts with a digital model, which can be created using 3D modeling software or obtained from a 3D scanner. The digital model is then sent to a 3D printer, which reads the data and uses it to produce an object layer by layer. The printer heats a material, such as plastic, metal, or resin, to a liquid or semi-liquid state and then deposits it layer by layer on a build platform. This process is repeated until the object is completed.
B. Materials Used:
3D printing can be done using a wide range of materials, each with its unique properties and applications. These materials include plastics, metals, ceramics, and resins. The type of material used in 3D printing depends on the application and the desired properties of the final product.
C. Pros and Cons:
Pros:
- 3D printing allows for high levels of customization and intricate designs that would be challenging or impossible to achieve using traditional manufacturing methods.
- It eliminates the need for tooling, which can be time-consuming and expensive.
- The process is fast and requires minimal labor compared to traditional methods.
- It has a lower environmental footprint due to the reduction in material waste.
.
Cons:
- It can be expensive to scale up to mass production levels.
- The quality and strength of the final product may not be comparable to those made through traditional manufacturing methods.
- There is limited material selection when compared to traditional manufacturing methods.
- Surface finish is not as smooth and requires post-processing to achieve desirable outcomes.
In general, 3D printing is best suited for small production runs, prototyping, and creating objects with intricate designs or features. It provides production freedom and design flexibility, but its cost-effectiveness and quality depend on the size of production, the materials used, and the desired final product outcomes.
-
3. Overview of Injection Molding:
Injection molding is a manufacturing process used to create objects by injecting molten material into a mold to create a desired shape. The process is commonly used to produce large quantities of identical objects, such as automotive parts, toys, and medical devices.
A. How Injection Molding Works:
The process of injection molding starts with melting a thermoplastic or thermosetting material into a liquid state, which is then injected into a steel mold under high pressure. The material takes the shape of the mold, and it is allowed to cool and solidify before removal from the mold. The cycle then repeats itself to create multiple identical parts.
B. Materials Used:
A broad range of materials can be used in injection molding, including plastics, metals, rubber, and glass. The selection of material depends on the application, cost, and desired physical properties of the final product.
C. Pros and Cons:
Pros:
- Injection molding allows for precise and accurate manufacturing of high-quality parts at high volumes.
- The finished product has a smooth surface finish and high dimensional accuracy.
- The process is cost-effective when producing high quantities of identical parts.
- The manufacturing process can be automated, reducing the need for labor.
.
Cons:
- The initial cost of tooling and machinery can be high, making it expensive for small production runs.
- Part design can be limited by the mold material and shape.
- The lead time for designing and producing the mold can be long.
- The process is not suitable for creating complex or intricate designs.
In general, injection molding is best suited for manufacturing large quantities of identical objects with high precision and smooth surface finish. It is used in the automotive industry, medical devices, toys, and consumer products. While it requires a high initial investment, it provides economies of scale, making it cost-effective for large production runs.
-
4. Cost Comparison:
When it comes to cost comparison between 3D printing and injection molding, several factors need to be considered.
A. Capital Investment Cost:
The initial capital investment for 3D printing is significantly lower than injection molding. 3D printers can range from hundreds to tens of thousands of dollars, depending on the size and functionality required, whereas injection molding machines and tooling can cost hundreds of thousands of dollars. However, as production increases, injection molding can be more cost-effective in the long run, making up for the initial investment.
B. Cost of Materials:
The cost of materials varies between 3D printing and injection molding. While 3D printing can use a wide range of materials, the cost per unit can be higher due to the limited ability to purchase materials in bulk. Injection molding often requires more material per part, but the cost per unit can be lower due to economies of scale and the ability to purchase materials in bulk.
C. Cost of Labor:
The cost of labor for 3D printing is generally lower than that of injection molding. 3D printing requires less manual labor as the process is highly automated, whereas injection molding requires more manual labor to operate the machines, prepare and handle materials, monitor production, and perform quality control.
D. Cost of Equipment:
3D printing requires minimal equipment other than the printer itself, whereas injection molding requires sophisticated machinery, molds, and auxiliary equipment like robots, conveyors, and material handling systems. The equipment required for injection molding can drive up the cost of the manufacturing process.
Overall, 3D printing can be more cost-effective for small production runs or unique parts, while injection molding is better suited for mass production runs of identical parts. Careful consideration of the cost factors is essential when deciding between the two manufacturing processes.
-
5. Quality Comparison:
When it comes to quality comparison between 3D printing and injection molding, several factors need to be considered.
A. Tolerance:
Injection molding typically produces parts with higher accuracy and tighter tolerances, which means that the final parts have minimal deviation from the desired specifications. 3D printing, on the other hand, may have slightly lower tolerances due to the layer-by-layer printing process, which can result in small variations in surface finish and dimensional accuracy.
B. Surface Finish:
Injection molding produces parts with a smooth and uniform surface finish, requiring minimal post-processing to achieve the desired level of smoothness. 3D printing may produce parts with a rough surface finish, and in order to produce surfaces as smooth as those from injection molding, it may require additional post-processing, including sanding, painting, or coating.
C. Part Strength:
Injection molding generally results in parts with better strength and durability because the process uses high temperatures and high pressure to melt and form material into the mold. 3D printing parts may have lower strength due to the printed layer-by-layer manufacturing process, resulting in limited bonding between layers compared to injection molding.
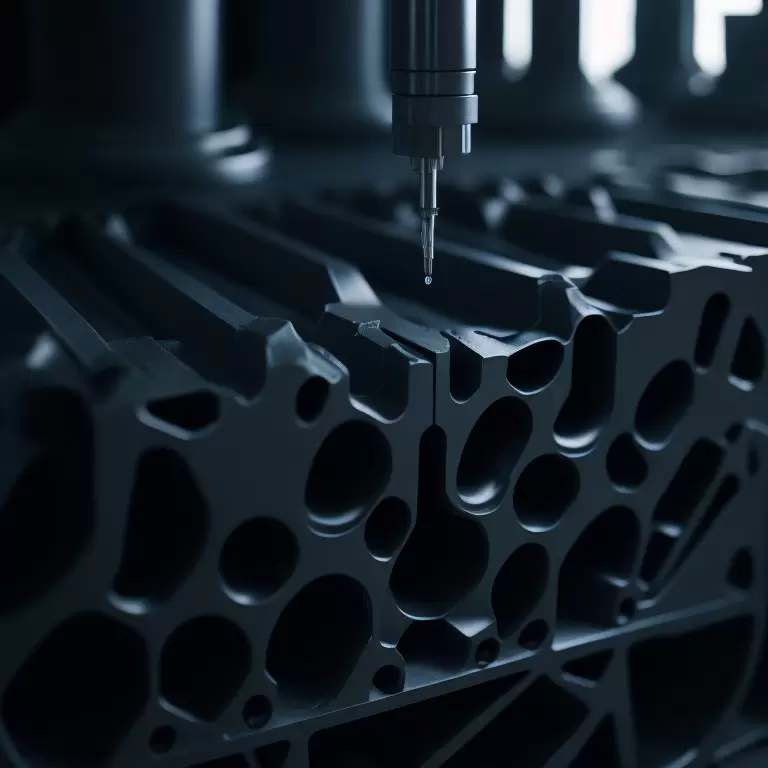
-
6. Production Comparison:
When it comes to production comparison between 3D printing and injection molding, several factors need to be considered.
A. Quantity:
Injection molding is well suited for high-volume production runs of identical parts, enabling manufacturers to produce hundreds of thousands or even millions of parts quickly and cost-effectively. 3D printing, on the other hand, is better suited for low to medium production runs, with limited economies of scale. While 3D printing can be cost-effective for unique or low volume production runs, it is less efficient for high volume mass production.
B. Time to Market:
3D printing allows for faster time to market because it eliminates the need for tooling, which can take weeks or months to develop. 3D printing can produce parts rapidly, and printing iterations can be made quickly and economically, resulting in a shorter lead time to products being on the market. Injection molding requires more significant upfront investment for tooling and setup, leading to longer lead times, making it less flexible than 3D printing, which can adjust designs and quickly make product changes for easier testing and iterating.
C. Complexity:
3D printing is better suited for complex designs and shapes, including geometries with undercuts, overhangs, or irregular shapes that may not be possible with injection molding. Injection molding can be more limited in terms of the shapes and designs that can be created due to the requirement for mold shapes.
Overall, each manufacturing process has its strengths and weaknesses in production, with 3D printing being a more flexible and speedy manufacturing process that can produce complex designs in smaller quantities, while injection molding is a more specialized, high-volume production process that can produce parts with better tolerances and strength.
-
7. Environmental Factors:
When it comes to environmental factors, both 3D printing and injection molding have their strengths and limitations.
A. Sustainability:
3D printing can be more sustainable than injection molding in certain situations. 3D printing allows for on-demand production, reducing the need for inventory and stocking of parts. It also produces less waste material compared to injection molding, where excess materials and trimmings are typical. The relatively small footprint of 3D printing also makes it a more sustainable option in terms of resource conservation, especially for companies that require close-to-marketplace production.
B. Waste Management:
Injection molding generates a more significant amount of waste than 3D printing, such as waste material and trimming or excess material. However, injection molding’s waste materials can be recycled and reused, whereas improper disposal of 3D-printed waste materials presents a problem as they may also be non-biodegradable. Careful consideration should be taken to ensure that the printed material is recyclable or is disposed of responsibly.
C. Carbon Footprint:
Both 3D printing and injection molding can have a high carbon footprint, mostly due to the manufacturing process and associated energy use. However, 3D printing has the potential to have a lower carbon footprint because it can reduce the transportation of inventory and reduce waste, leading to lower energy consumption overall. It is said that locally 3D printing, for example, city blocks or nearby industrial parks, can significantly reduce transportation costs and thus reduce carbon footprint.
While both 3D printing and injection molding have environmental implications, 3D printing’s on-demand production, minimal waste, reduced dependence on inventory, and localized manufacturing capability may make it a more sustainable option. Still, both methods must be considered holistically to assess their environmental impact properly.
-
8. Applications:
Both 3D printing and injection molding have their specific applications across different industries. Here are some examples of the industries where 3D printing and injection molding are applied the most.
A. Industries where 3D Printing is Most Commonly Used:
- Product design & prototyping: 3D printing is heavily used for designing and prototyping products in a range of industries, including consumer goods, aerospace, automotive, architecture, medical devices, and electronics.
- Dental and medical: 3D printing has become an essential tool in the dental and medical fields, allowing dentists and surgeons to create customized implants, prosthetics, and surgical guides.
- Jewellery and fashion - 3D printing enables unique and customizable jewelry designs with increased detail and intricacy.
- Artistry and film: 3D printing is used in movie and theatre productions to create one-of-a-kind props, costumes, and sets.
.
B. Industries where Injection Molding is Most Commonly Used:
- Automotive: Injection molding is heavily used in manufacturing automotive components such as engine housings, oil pans, dashboards, and bumpers.
- Consumer goods: Injection molding has widespread use in manufacturing everyday consumer goods such as toys, storage containers, and kitchenware.
- Medical: Injection molding is utilized in mass production of hearing aids, syringe barrels, and caps, and tubing leading to medical equipment assembly.
- Packaging: Injection molding plays a vital role in packaging production, with a wide range of materials used including plastic, metal and gum.
Overall, both 3D printing and injection molding offer distinctive benefits to different industries, leading to increased advancements in design, production, and cost control in different applications.
-
9. Future of Manufacturing:
Both 3D printing and injection molding are continuously evolving, with emerging technologies leading to exciting future possibilities. Here are some of the emerging technologies and possible future trends in 3D printing and injection molding.
A. Emerging Technologies in 3D Printing:
- Multi-material printing: 3D printing technology is now advancing to allow for printing with multiple materials, increasing design flexibility and enabling a range of new products to be manufactured.
- Continuous 3D printing: Advances in 3D printing have led to the development of continuous printing technology, including “infinite build” technology, allowing for uninterrupted production.
- Large-scale printing: Promising advancements in 3D printing are being explored for large-scale manufacturing applications, such as creating building components or manufacturing aircraft components.
.
B. Emerging Technologies in Injection Molding:
- High-speed injection molding: Injection molding technology advances that allow for faster cycles, high-pressure capabilities, automation, and intelligence-based quality control.
- Innovative material options: Development of alternative sustainable and biodegradable materials for complex injection molding designs.
- Smart & intelligent injection molding parts: Connecting data control sensors and artificial intelligence (AI) to optimize injection molding.
.
C. Possible Future Trends in Manufacturing:
- Integrated integration of 3D printing and injection molding: The combination of 3D printing and injection molding can enable rapid prototyping, customization, and mass production within the same manufacturing process chain.
- Hybrid manufacturing: The fusion of 3D printing and conventional manufacturing techniques, such as welding, cutting, or other assembly processes, will lead to increasing use of advanced manufacturing processes for complex designs.
- Digitization: Increasing use of data and related technologies such as Cloud Computing, Artificial Intelligence (AI) and the Internet of Things (IoT) to improve the manufacturing capacity and flexibility through customisation while reducing production costs.
Overall, the future of manufacturing holds endless possibilities for innovation and advancements, with 3D printing and injection molding poised to play a central role in future product development across industries. Achieving these advancements in manufacturing requires a continued focus on evolving new and existing technologies to meet the specific needs of manufacturers and their customers.
If you need about 3D Printing or Injection Molding Services,You can click on the V1 Prototype website to find it.
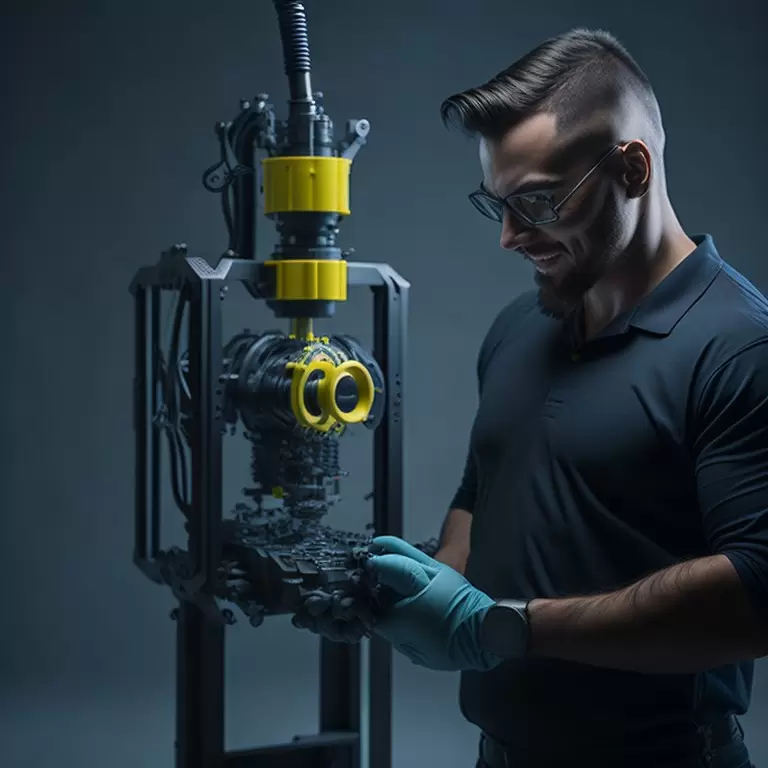
-
10. Conclusion:
In conclusion, 3D printing and injection molding are two popular manufacturing processes with their distinctive strengths and limitations. Both play a significant role in different industries, and it’s important to consider their unique features to make an informed decision when selecting the ideal manufacturing process.
3D printing’s benefits include mass customization and reduced tooling costs, making it a valuable tool for product design and prototyping. Injection molding, on the other hand, is ideal for high-volume mass production of identical parts in industries such as automotive, consumer goods manufacturing, and medical devices due to its low unit cost and highly refined manufacturing process.
Environmental and sustainability factors have also become increasingly important in manufacturing, and both 3D printing and injection molding have the potential to reduce waste, lower energy consumption, and lead to more sustainable manufacturing processes in the future.
Advancements in both 3D printing and injection molding technology continue to improve, with advancements such as multi-material printing, high-speed injection molding, and smart intelligent injection molding that will increase precision and lower production costs, as well as provide opportunities for customisation and digitization.
In conclusion, manufacturers need to weigh the trade-offs between 3D printing and injection molding based on their specifications, design requirements, sustainability goals, costs, and production volumes. With careful consideration and a clear understanding of these processes and their applications, manufacturers can adopt the best-fit manufacturing process for their business needs.